Introduction
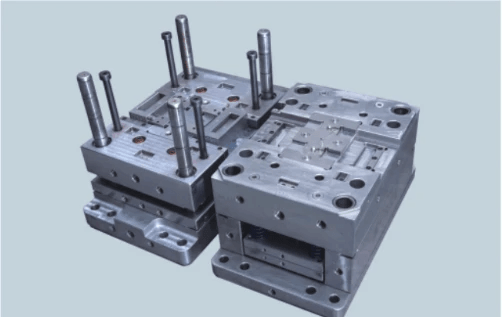
In the world of plastic injection molding, understanding injection molding tolerances is crucial for ensuring that the final product meets design specifications and performance requirements. Tolerances dictate how much variation is acceptable in the dimensions of molded parts, which can significantly affect functionality and quality. As we delve deeper into this topic, we will uncover the importance of these tolerances in design, common misconceptions surrounding them, and their implications in various industries.
Understanding Injection Molding Tolerances
Injection molding tolerances refer to the allowable limits of variation in a part's dimensions during the manufacturing process. These tolerances are not arbitrary; they are influenced by several factors including material properties, mold design, and manufacturing techniques. A solid grasp of these tolerances helps designers create more effective mold injection designs that optimize both performance and cost-efficiency.
Importance of Tolerance in Design
The significance of tolerance in design cannot be overstated; it directly impacts product quality and manufacturability. When designers specify precise injection molding tolerance standards, they ensure that each component fits together seamlessly within an assembly, reducing the risk of failure during operation. Moreover, well-defined tolerances can lead to lower production costs by minimizing waste and rework due to poorly fitting parts.
Common Myths about Injection Molding
Despite its widespread use, there are several myths about plastic injection molding that can lead to misunderstandings about its capabilities and limitations. One common misconception is that tighter tolerances always equate to better quality; however, this isn't necessarily true as overly stringent tolerances can increase production costs without significant benefits. Another myth is that all plastic molding materials behave uniformly under similar conditions—each material has its unique characteristics affecting how it responds to mold design and processing parameters.
What Are Injection Molding Tolerances?
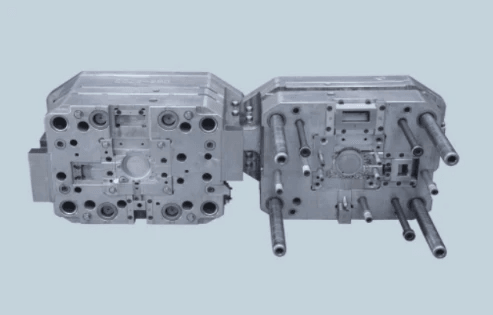
Injection molding tolerances are the allowable limits of variation in the dimensions of molded parts during the plastic injection molding process. These tolerances are critical for ensuring that components fit together correctly and function as intended, especially in industries where precision is paramount. Understanding injection molding tolerances can mean the difference between a successful product launch and costly redesigns.
Definition and Overview
At its core, injection molding tolerances refer to the specific measurements that dictate how much a part can deviate from its intended dimensions. This includes factors like length, width, height, and even angles that must be maintained within specified limits to ensure functionality and interoperability with other components. The importance of these tolerances cannot be overstated; they directly influence both the performance of mold plastic injection parts and their overall quality.
In practical terms, injection molding tolerances are set based on both industry standards and specific project requirements. Manufacturers often consult established tolerance guidelines to determine acceptable ranges for their products, which helps streamline production processes while minimizing waste. By adhering to these standards, companies can produce high-quality plastic injection parts that meet customer expectations consistently.
Factors Affecting Tolerances
Several factors come into play when determining injection molding tolerances for any given project. First among these is the type of plastic molding material used; different materials have unique properties that affect shrinkage rates during cooling and solidification processes. For example, some plastics may expand or contract more than others when subjected to temperature changes, which can lead to variations in final dimensions.
Another significant factor is mold design itself; a well-executed mold injection design will account for thermal expansion properties as well as flow characteristics of the chosen material. Additionally, machine settings during the actual plastic injection process—such as pressure and temperature—can also impact how closely parts adhere to specified tolerances. Understanding these variables allows designers to better predict outcomes and make necessary adjustments throughout production.
Lastly, environmental conditions such as humidity or temperature fluctuations in the manufacturing facility can also play a role in achieving desired tolerances. Companies need to maintain consistent conditions during production runs to ensure repeatability in their processes while minimizing defects caused by external influences.
Industry Applications
Injection molding tolerances find application across various industries where precision engineering is essential—from automotive components to medical devices and consumer electronics. In automotive manufacturing, for instance, even minor deviations in part dimensions can lead to assembly issues or performance failures that compromise safety standards or operational efficiency. Therefore, strict adherence to tolerance guidelines is crucial for maintaining quality control in this sector.
Similarly, in medical device manufacturing where safety is non-negotiable, precise injection molding tolerances are vital for ensuring compatibility between different components within complex assemblies like surgical instruments or diagnostic equipment. Any deviation could potentially lead not only to product failure but also serious health risks for end-users.
Consumer electronics also rely heavily on tight injection molding tolerance standards due to intricate designs requiring precise fits among multiple parts—think smartphones or laptops where every millimeter counts! As technology advances further into miniaturization trends with ever-smaller components being developed daily, understanding how these tolerances work becomes increasingly important across all sectors involved in plastic injection molding processes.
Key Injection Molding Tolerance Standards
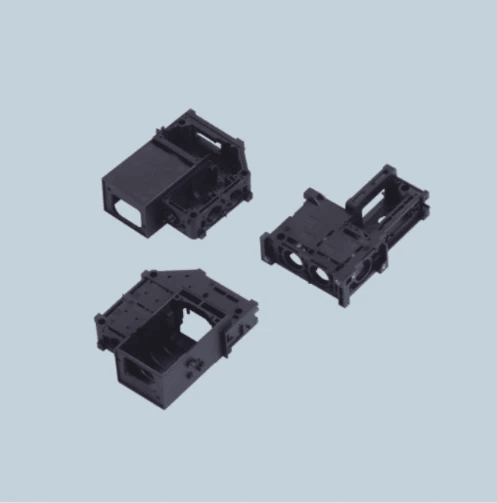
In the world of injection molding, adhering to tolerance standards is crucial for ensuring product quality and consistency. These standards provide a framework for manufacturers to follow, which helps in minimizing defects and maximizing efficiency in plastic injection molding processes. Understanding key injection molding tolerance standards can significantly enhance mold injection design and overall production outcomes.
ISO 2768 and Its Relevance
ISO 2768 is an international standard that provides general tolerances for linear dimensions, angular dimensions, and geometrical tolerances in mechanical engineering. This standard is particularly relevant in the context of injection molding tolerances, as it offers guidelines that can be applied across various industries, including automotive and consumer goods. By following ISO 2768, manufacturers can ensure that their mold plastic injection processes meet consistent quality benchmarks while reducing the risk of errors due to dimensional discrepancies.
ISO 2768 breaks down into two categories: ISO 2768-1 for linear dimensions and ISO 2768-2 for angular dimensions. These classifications help designers select appropriate tolerances based on their specific application needs, making it easier to communicate requirements clearly throughout the production process. In addition, adhering to this standard can streamline compliance with other industry-specific regulations, further enhancing product reliability.
ASME Y14.5 and Geometric Dimensioning
ASME Y14.5 is another critical standard that focuses on geometric dimensioning and tolerancing (GD&T), providing a comprehensive set of symbols and rules for defining part features accurately. This standard plays a vital role in plastic injection molding by helping engineers specify allowable variations in shape and form during the manufacturing process. By utilizing ASME Y14.5 guidelines within mold injection design, companies can improve communication between design teams and manufacturing personnel while ensuring that products meet stringent quality requirements.
The application of GD&T principles allows engineers to convey complex design intent clearly without ambiguity, thus reducing misunderstandings during production phases. Furthermore, incorporating these geometric tolerancing principles into plastic molding material selection ensures compatibility with desired performance characteristics—ultimately leading to better-fitting components with fewer defects. By understanding ASME Y14.5's intricacies, manufacturers can harness its power to achieve tighter control over their injection molding tolerances.
Best Practices for Compliance
Achieving compliance with key injection molding tolerance standards requires diligence at every stage of the production process—from initial design through final inspection. One best practice involves conducting thorough training sessions for all team members involved in mold plastic injection operations; this ensures everyone understands how these standards affect their work responsibilities directly related to maintaining high-quality output levels.
Additionally, implementing advanced software solutions designed specifically for managing tolerance specifications can streamline compliance efforts significantly by automating calculations related to dimensional variations throughout the lifecycle of a project—minimizing human error along the way! Regular audits should also be conducted on both equipment used during production as well as finished products themselves; this proactive approach helps identify any deviations from established guidelines before they escalate into larger issues affecting overall quality or performance metrics.
By integrating these best practices into daily operations while staying informed about evolving industry trends surrounding injection molding tolerance standards will ultimately lead organizations toward enhanced efficiency gains alongside improved customer satisfaction levels—a win-win scenario!
How Tolerance Affects Mold Design
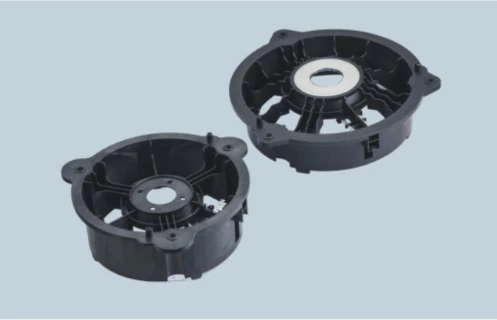
When it comes to mold design, understanding injection molding tolerances is crucial for achieving the desired quality and functionality of plastic parts. Tolerances dictate how precise the dimensions of molded components must be, directly influencing everything from part fit to overall performance. Therefore, designers must carefully consider these tolerances during the initial stages of mold plastic injection design.
Critical Design Considerations
One of the most critical design considerations in injection molding is ensuring that the mold can accommodate specified tolerances without compromising functionality. This includes evaluating factors such as draft angles, wall thickness, and rib designs that can affect how well a part will release from the mold. Additionally, selecting appropriate plastic molding materials that align with tolerance requirements can make or break a project; materials with high shrinkage rates may necessitate tighter controls on dimensions.
Another aspect to consider is how temperature fluctuations during production can impact injection molding tolerances. For instance, if a material expands or contracts more than anticipated due to thermal variations, it could lead to parts falling outside acceptable tolerance ranges. Thus, engineers must integrate thermal management strategies into their mold injection design process to mitigate these risks effectively.
Lastly, understanding how features like undercuts or complex geometries interact with tolerances is vital for successful plastic injection molding outcomes. Each unique element in a design should be scrutinized for its potential impact on dimensional accuracy and consistency throughout production runs. By prioritizing these considerations early in the design phase, manufacturers can minimize costly revisions later on.
Influence on Mold Plastic Injection
The influence of injection molding tolerances extends beyond mere measurements; they significantly affect the entire mold plastic injection process itself. If tolerances are too tight for a given material or machine capability, it may lead to frequent defects and increased cycle times as operators struggle to meet specifications consistently. Conversely, overly relaxed tolerances might result in poorly fitting components that fail under stress or don't meet customer expectations.
Moreover, achieving precise tolerances requires meticulous attention during every step of the manufacturing process—from initial setup through cooling and ejection phases—to ensure that each part meets established standards. This includes calibrating equipment accurately and performing regular maintenance checks to avoid deviations caused by wear over time. Thus, organizations committed to maintaining high-quality standards must invest in both technology and training tailored toward managing these challenges efficiently.
In addition to operational impacts, compliance with recognized injection molding tolerance standards—like ISO 2768—can enhance credibility within competitive markets by demonstrating reliability and commitment to quality assurance processes. Adhering strictly not only helps streamline production but also fosters trust among clients who rely on consistent performance across multiple batches of products.
Role of Mold Injection Design in Quality
Mold injection design plays an indispensable role in ensuring that products adhere closely to defined injection molding tolerances while meeting quality benchmarks set by industry standards. The precision with which molds are engineered directly influences whether parts will withstand functional tests without issue or fail catastrophically under load conditions due solely to poor dimensional accuracy.
A well-designed mold incorporates features such as cooling channels strategically placed near high-heat areas—allowing for even temperature distribution—which helps maintain consistent shrinkage rates across all parts produced from it over time. Furthermore, incorporating advanced technologies like simulation software allows designers to visualize potential issues before physical prototypes are built; this proactive approach often results in significant cost savings down the line when adjustments can be made digitally rather than through trial-and-error methods post-production launch.
Ultimately, investing time into optimizing mold injection designs not only enhances product quality but also improves overall efficiency throughout manufacturing operations—a win-win scenario! As companies strive toward greater innovation within their respective fields while adhering closely established tolerance guidelines becomes increasingly paramount for maintaining competitiveness amidst evolving consumer demands.
Materials and Their Impact on Tolerances
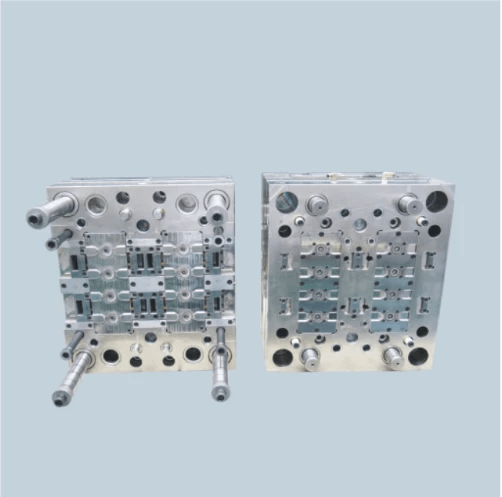
When it comes to injection molding tolerances, the choice of plastic molding material is a pivotal factor that can significantly influence the final product's quality and precision. Each type of plastic has its own unique properties that affect how it behaves during the plastic injection molding process. Therefore, selecting the right material is not just about aesthetics or cost; it's crucial for achieving optimal injection molding tolerance standards.
Choosing the Right Plastic Molding Material
Choosing the right plastic molding material involves balancing performance characteristics with production requirements. Different plastics offer varying levels of strength, flexibility, and thermal resistance, which directly impact mold injection design and tolerances. For instance, materials like ABS are popular for their toughness and ease of processing, while engineering-grade plastics like nylon provide enhanced mechanical properties but may require more precise mold designs to meet stringent injection molding tolerances.
Moreover, understanding the end-use application is essential in this selection process. If a product will be subjected to high temperatures or stress, using a high-performance polymer can help maintain dimensional stability and prevent distortion during cooling. Ultimately, making an informed choice about plastic materials ensures that your mold plastic injection process yields parts that meet or exceed expected tolerances.
Thermal Expansion and Its Effects
Thermal expansion is another critical consideration when discussing injection molding tolerances. As plastics heat up during processing and cool down after being injected into molds, they expand and contract at different rates depending on their composition. This behavior can lead to variations in dimensions if not adequately accounted for in mold design.
For instance, if a material expands too much during heating but does not contract uniformly upon cooling, it may result in warping or misalignment of features in the final part. Therefore, understanding how specific materials respond to temperature changes is vital for maintaining tight tolerances throughout production cycles. Designers must incorporate these thermal characteristics into their mold designs to mitigate issues related to dimensional accuracy.
Material-Specific Tolerance Guidelines
Each type of plastic has its own set of tolerance guidelines tailored to its unique properties and applications within injection molding processes. These material-specific tolerance guidelines provide manufacturers with benchmarks that help ensure consistent quality across batches while adhering to industry standards for precision parts manufacturing.
For example, some thermoplastics may allow tighter tolerances than others due to their inherent stability under varying conditions; however, this often comes at a higher cost or complexity in processing techniques such as mold design adjustments or cooling strategies tailored specifically for those materials. Understanding these nuances allows engineers to optimize both design and manufacturing processes effectively.
In conclusion, appreciating how different plastic molding materials impact injection molding tolerances is essential for achieving high-quality results in any project involving mold plastic injection techniques. By carefully considering factors like thermal expansion effects and adhering closely to material-specific tolerance guidelines throughout each stage—from selecting raw materials through final inspection—manufacturers can enhance overall product integrity while minimizing waste associated with rework or rejects.
The Role of Technology in Achieving Tolerances

In the rapidly evolving world of injection molding, technology plays a pivotal role in meeting and exceeding injection molding tolerances. From advanced software solutions that streamline mold design to innovative processes that enhance precision, technology is transforming how we approach plastic injection molding. As manufacturers strive for tighter tolerances and higher quality, leveraging these technological advancements becomes essential.
Software Solutions in Mold Design
The days of manual calculations and guesswork in mold plastic injection design are long gone, thanks to sophisticated software solutions. These tools allow engineers to simulate the entire injection molding process, predicting how various factors will affect the final product's tolerances. By using computer-aided design (CAD) and computer-aided engineering (CAE) software, designers can optimize mold designs before they even hit production, ensuring compliance with injection molding tolerance standards.
Moreover, these software solutions enable real-time adjustments during the design phase, which can significantly reduce errors related to mold injection design. With features like 3D modeling and stress analysis, engineers can visualize potential issues early on and address them proactively. This not only enhances the accuracy of plastic injection but also cuts down on costly revisions later in the manufacturing process.
Innovations in Injection Molding Processes
The landscape of injection molding is continuously evolving with new innovations designed to improve efficiency and precision. Techniques such as multi-material injection molding allow for complex designs while maintaining strict tolerances across different materials. This versatility opens up a world of possibilities for product designers who want to push the boundaries of what’s achievable in plastic molding material combinations.
Additionally, advancements like real-time monitoring systems help track key parameters during production runs, ensuring that any deviations from established tolerances are caught immediately. These systems provide feedback loops that allow operators to make instant adjustments—minimizing waste and maximizing quality control throughout the entire manufacturing process. The integration of automation further enhances consistency by reducing human error associated with traditional methods.
Baoyuan’s Approach to Precision
At Baoyuan, achieving exceptional precision in plastic injection is more than just a goal; it's a commitment rooted in cutting-edge technology and best practices for compliance with industry standards. Their state-of-the-art facilities utilize advanced mold design software alongside innovative techniques tailored specifically for high-precision applications within the realm of injection molding tolerances. This approach ensures that every component produced meets or exceeds customer expectations while adhering strictly to established tolerance guidelines.
Baoyuan also emphasizes continuous improvement through research into new materials and processes that can better withstand thermal expansion effects—one of the key factors affecting tolerances during production runs. By focusing on both technological advancement and meticulous attention to detail within their mold injection design processes, Baoyuan sets itself apart as a leader in delivering high-quality products consistently aligned with rigorous industry standards.
As we look towards future developments in this field, it’s clear that technology will continue shaping how we achieve tighter tolerance levels across various applications within plastic injection molding.
Conclusion
In the ever-evolving landscape of manufacturing, understanding injection molding tolerances is crucial for achieving high-quality products. As technology advances and market demands shift, the future of injection molding will likely see even tighter tolerances and innovative approaches to mold design. Staying informed about these trends can empower designers and engineers to create more precise and efficient plastic injection molding solutions.
The Future of Injection Molding Tolerances
The future of injection molding tolerances promises to be exciting, with increasing emphasis on precision and sustainability. As industries push for higher quality outputs, adherence to stringent injection molding tolerance standards will become even more critical. Innovations in materials and processes will likely lead to breakthroughs that further enhance the accuracy of mold plastic injection techniques.
Enhancing Quality through Better Tolerances
Enhancing quality through better tolerances isn't just a goal; it's a necessity in today’s competitive market. By focusing on precise mold injection design, manufacturers can significantly reduce waste and improve product reliability. Improved tolerance levels not only lead to better fitting components but also enhance overall customer satisfaction, thereby creating a win-win situation for businesses.
Practical Tips for Successful Molding
To achieve successful plastic injection molding outcomes, consider these practical tips: first, always select the right plastic molding material tailored to your specific application needs; different materials behave differently under varying conditions, impacting tolerances significantly. Secondly, invest in advanced software solutions that aid in mold design—these tools can help predict potential issues before they arise during production. Lastly, continuous education on industry standards related to injection molding tolerance standards will keep your team sharp and your processes optimized.