Introduction
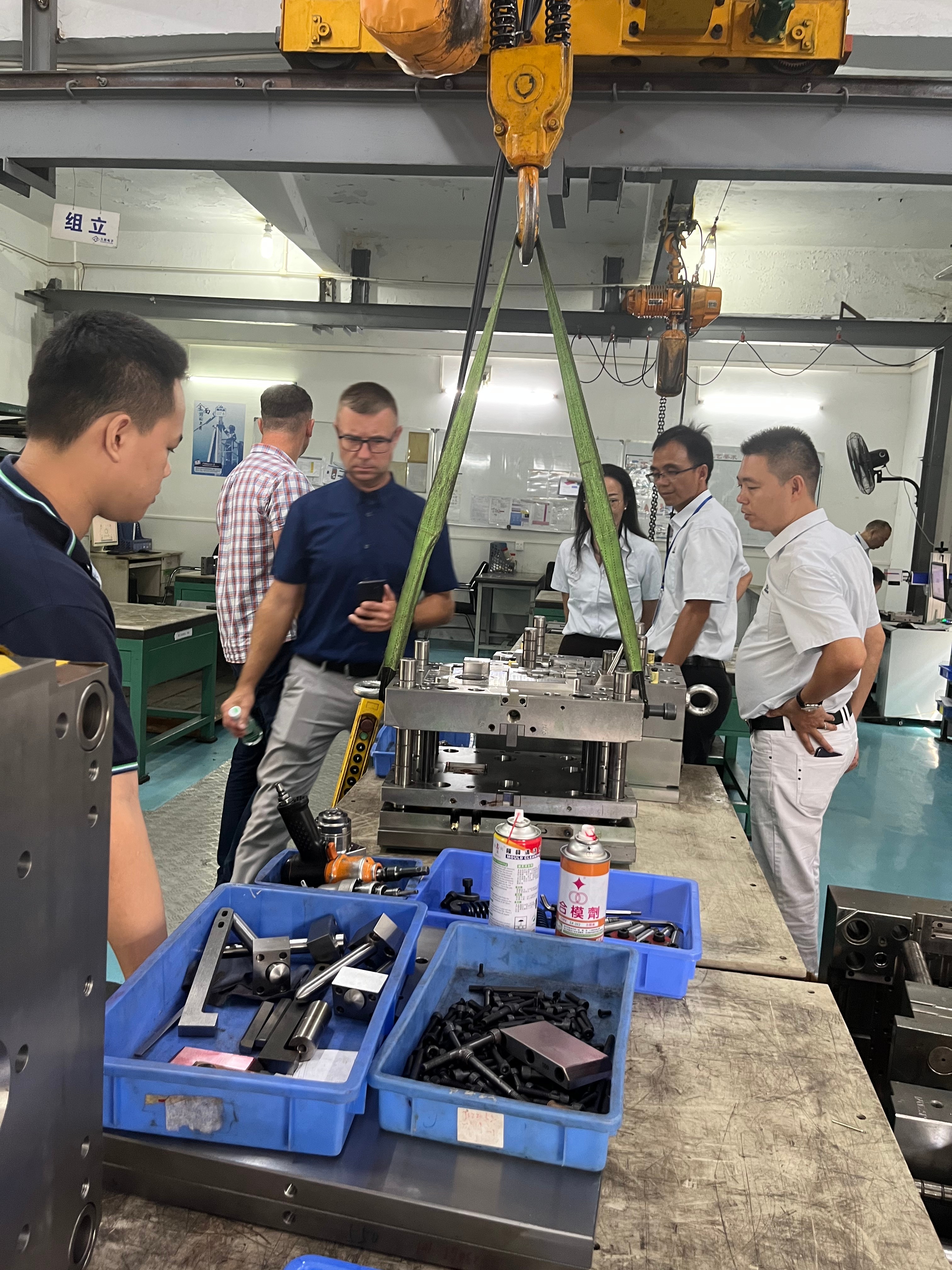
Injection molding is a widely used manufacturing process that allows for the mass production of complex plastic parts. However, like any intricate system, it is not immune to injection molding defects and causes that can significantly impact product quality and production efficiency. Understanding these defects is crucial for manufacturers striving to maintain high standards and meet consumer expectations.
Understanding Injection Molding Defects
Injection molding defects can manifest in various forms, from surface blemishes to structural weaknesses, each with its own set of implications. What are the common defects in injection molding? Some of the most frequent issues include sink marks, warping, flash, and gate vestiges—each presenting unique challenges during production. By identifying these defects early on, manufacturers can take appropriate measures to rectify them before they escalate into larger problems.
The Importance of Identifying Causes
Identifying the root causes of injection molding defects is essential for effective quality assurance and continuous improvement in manufacturing processes. Without understanding what leads to these issues—such as improper temperature settings or inadequate material selection—it becomes nearly impossible to implement effective solutions. This knowledge empowers teams to create strategies that not only address current problems but also prevent future occurrences.
Common Injection Molding Issues
Common injection molding issues often stem from both human error and equipment malfunctions during production runs. For instance, what is the problem with the injection molding process? Problems like inconsistent material flow or incorrect cooling times can lead to various defects that affect product integrity and aesthetics. Moreover, understanding what are moulding material defects helps manufacturers select higher-quality materials that minimize risk and enhance overall product performance.
Overview of Injection Molding Defects
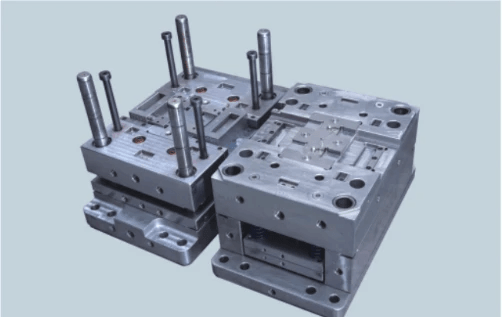
Injection molding is a widely used manufacturing process, but it’s not without its pitfalls. Understanding injection molding defects and causes is essential for anyone involved in production, as these issues can lead to significant financial losses and compromised product quality. Let’s dive into the types of defects that commonly occur, their consequences in production, and some real-world examples that highlight the importance of vigilance.
Types of Injection Molding Defects
What are the common defects in injection molding? There are several prominent types that manufacturers often encounter, including short shots, sink marks, warping, and gate vestiges. Each defect has its own unique characteristics; for instance, short shots occur when the mold isn't completely filled with material, while sink marks appear due to uneven cooling or insufficient packing pressure.
Gate vestiges are another common issue—what is the cause of gate vestiges? They result from leftover material at the gate location after ejection from the mold and can detract from a product's aesthetic appeal. Other defects like flash (excess material around mold edges) and discoloration can also arise from improper settings or poor-quality materials.
Consequences of Defects in Production
The consequences of defects in production can be dire for manufacturers. First and foremost, defective products lead to increased costs due to waste and rework; this not only affects profit margins but also impacts delivery timelines. Additionally, persistent injection molding defects can damage a company's reputation if customers receive subpar products.
Furthermore, what is the problem with the injection molding process itself? The complexity of this process means that even minor deviations in temperature or pressure can result in significant flaws. Ultimately, these issues may lead to higher rates of customer complaints and returns—an outcome no manufacturer desires.
Industry Examples of Real-World Defects
Industry examples serve as cautionary tales about injection molding defects and causes that should not be overlooked. For instance, consider a large automotive manufacturer that faced a recall due to defective dashboard components caused by inadequate cooling during production—this resulted in warping over time. Similarly, a consumer electronics company discovered its smartphone casings had visible gate vestiges after launch; this not only affected sales but also customer trust.
These real-world cases highlight how crucial it is for companies to understand what are moulding material defects as well as how they relate to overall production quality. By learning from these examples and implementing better practices for detection and prevention—like rigorous testing protocols—manufacturers can enhance their processes significantly.
Exploring Common Defects in Injection Molding
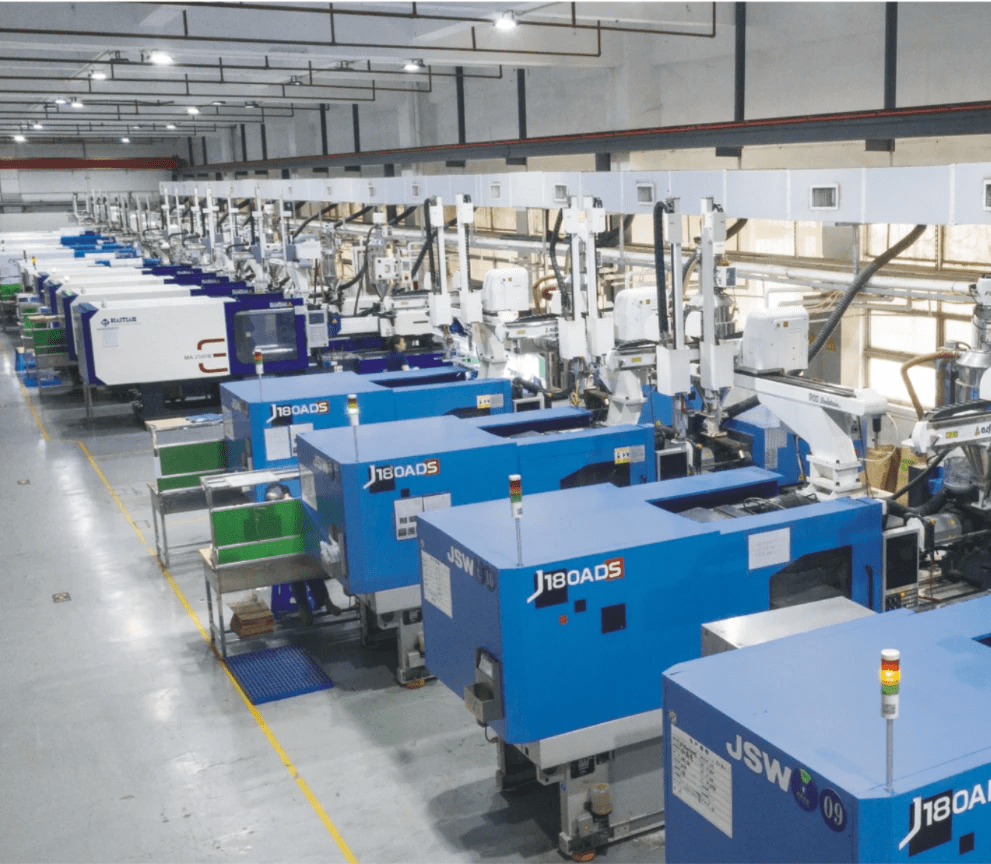
Injection molding is a widely used manufacturing process, but it’s not without its pitfalls. Understanding the common injection molding defects and their causes is crucial for ensuring quality production. This section will delve into prevalent defects, analyze real-world examples, and explore methods to detect and prevent these issues.
What are the common defects in injection molding?
What are the common defects in injection molding? The most frequently encountered issues include short shots, flash, sink marks, warping, and gate vestiges. Short shots occur when the mold cavity isn't completely filled with material, often due to insufficient pressure or inadequate material flow. Flash refers to excess plastic that seeps out of the mold during injection, which can lead to additional trimming costs and aesthetic concerns. Sink marks are depressions that appear on the surface of a molded part as it cools unevenly, while warping happens when parts distort due to temperature fluctuations or improper cooling rates.
These defects not only compromise product integrity but also affect overall production efficiency. For instance, gate vestiges—those pesky remnants left at the gates where plastic enters molds—can be both an eyesore and a functional issue if not managed properly. Understanding these common injection molding defects and their causes allows manufacturers to implement corrective measures early on.
Case Studies on Defective Products
To illustrate the impact of injection molding defects in real-world scenarios, consider two case studies involving defective products from well-known companies. In one instance, a major automotive manufacturer faced significant recalls due to short shots in critical components like dashboards. These short shots led to structural weaknesses that could jeopardize passenger safety—definitely not ideal!
In another case study involving consumer electronics, a popular smartphone brand encountered problems with flash on their casing components. The excess material not only marred the sleek design but also increased production costs due to additional finishing processes required for quality assurance. These examples highlight how understanding what are moulding material defects can save companies from costly errors down the line.
Methods for Detection and Prevention
Prevention is always better than cure—especially when tackling injection molding defects! Implementing effective detection methods can significantly reduce occurrences of these issues in production lines. Techniques such as visual inspections during various stages of manufacturing help identify potential problems early on.
Moreover, utilizing advanced technologies like infrared thermography can provide insights into temperature variations during cooling cycles—a key factor influencing many types of defects including warping and sink marks. Quality control measures should also include regular audits of moulding materials; understanding what are moulding material defects ensures that only high-quality materials enter your processes.
By fostering a culture of proactive problem-solving within teams—like Baoyuan’s dedicated approach—you can bolster your defenses against common injection molding defects and causes effectively!
Analyzing Gate Vestiges
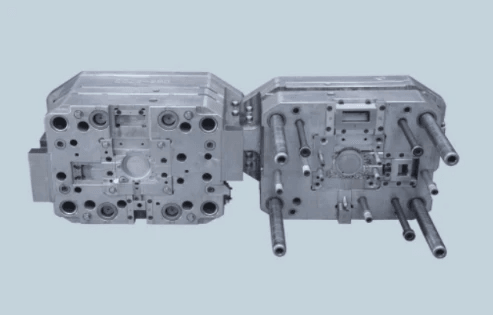
Gate vestiges are a common issue in the world of injection molding defects, often leading to unsightly marks on molded products. These remnants occur when the material used to fill the mold does not completely detach from the gate, leaving behind small bumps or scars. Understanding what causes gate vestiges is crucial for manufacturers aiming to deliver high-quality products without imperfections.
What is the cause of gate vestiges?
The primary cause of gate vestiges stems from improper cooling and solidification of the injected material at the point where it enters the mold. If the injection speed is too high or if there’s insufficient cooling time, excess material can remain attached at the gate, resulting in visible defects. Additionally, poor mold design or incorrect placement of gates can exacerbate this issue, making it essential to analyze these factors carefully during production.
Impact on Product Aesthetics and Functionality
Gate vestiges significantly impact both aesthetics and functionality, creating an undesirable appearance that can deter customers. For many products, especially those intended for consumer markets, visual appeal plays a crucial role in purchasing decisions; thus, any visible defect can lead to decreased sales and customer dissatisfaction. Furthermore, these imperfections may affect how well parts fit together or function in their intended applications, potentially leading to mechanical failures or operational issues down the line.
Strategies to Minimize Gate Vestige Issues
To minimize gate vestige issues effectively, manufacturers should focus on optimizing their injection molding processes by adjusting parameters like injection speed and cooling time. Implementing advanced mold designs that promote better flow distribution can also help reduce residual material at gates. Regularly reviewing and refining production techniques alongside employee training ensures that teams are well-equipped to identify potential injection molding defects and causes before they impact product quality.
Investigating the Injection Molding Process
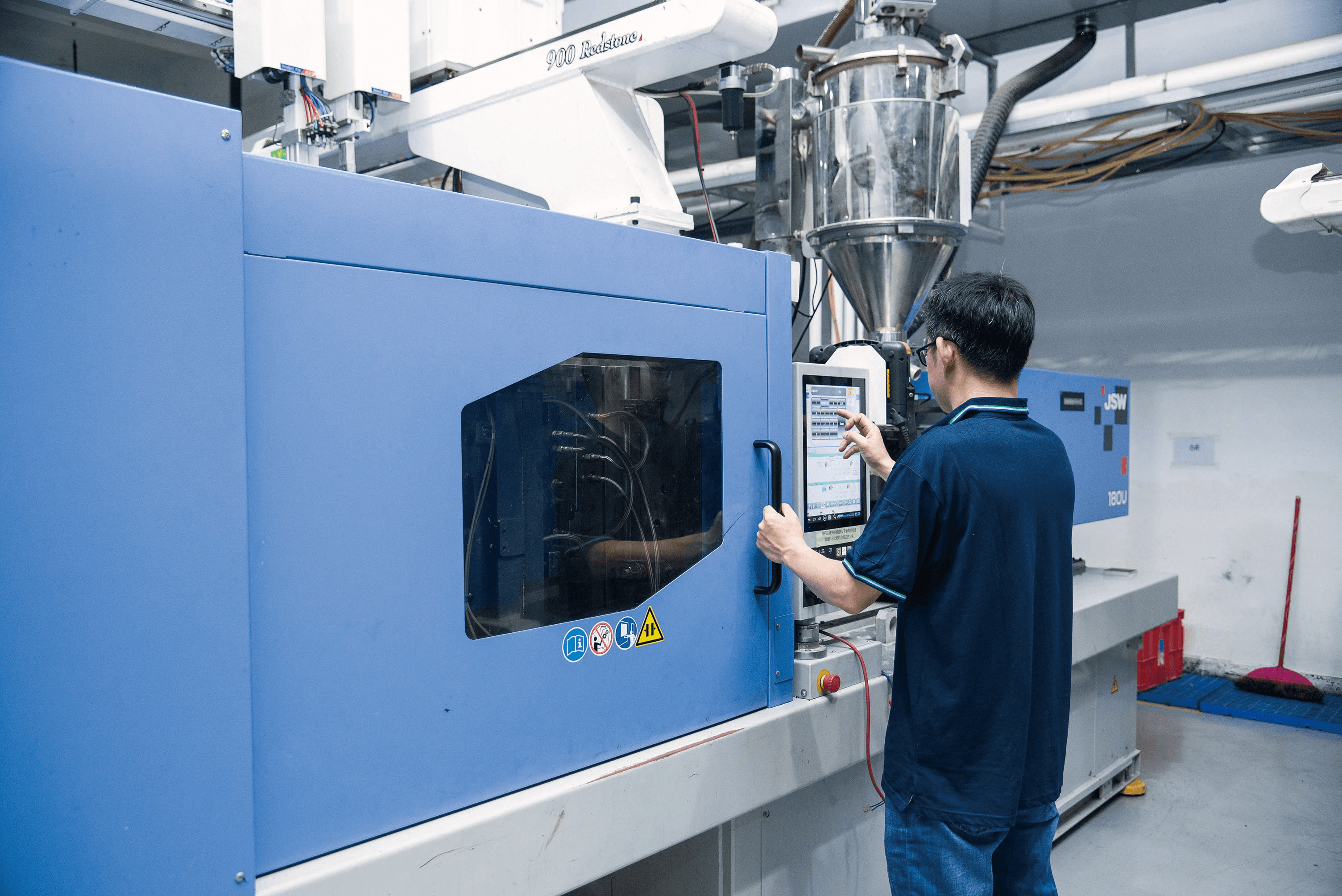
The injection molding process is a sophisticated technique that, while efficient, can present several challenges. Problems often arise due to various factors, such as machine settings, material quality, or operator error. Understanding what is the problem with the injection molding process is crucial for manufacturers aiming to minimize defects and enhance product quality.
What is the problem with the injection molding process?
One of the primary issues in the injection molding process is inconsistency in product quality, which can lead to significant injection molding defects and causes. Variations in temperature, pressure, and cooling times can result in products that do not meet specifications or exhibit visible defects. Additionally, if the mold design is flawed or not maintained properly, it can exacerbate these issues and lead to further complications.
Another common problem involves contamination of materials during processing. When foreign substances are introduced into the material feed or mixing stages, they can create unwanted moulding material defects that compromise both aesthetics and functionality. Identifying these problems early on helps ensure a smoother production cycle and higher-quality output.
Common Process Failures and Their Causes
Several types of failures commonly occur within the injection molding process that contribute to defects. For instance, insufficient filling of molds often results from low injection speed or inadequate pressure settings—both critical aspects when discussing what are common defects in injection molding? If not addressed promptly, these failures may lead to incomplete parts or even scrap production.
In addition to filling issues, another prevalent failure type includes short shots where material does not fill all areas of a mold cavity due to various reasons like poor venting or incorrect temperature settings. These conditions can also lead directly back to understanding what is the cause of gate vestiges? Inadequate venting allows air pockets that disrupt flow patterns resulting in surface imperfections.
Finally, wear and tear on machinery components can introduce variability into processes as well; worn screws or damaged nozzles may affect melt flow rates leading again toward increased chances for defects like warping or flash formation during cooling stages.
Solutions to Improve Process Reliability
To enhance reliability within the injection molding process requires a multifaceted approach focused on both technology upgrades and staff training initiatives aimed at defect prevention strategies. Regular maintenance schedules for machinery should be implemented alongside real-time monitoring systems that track performance metrics—this ensures any deviations from standard operations are quickly identified before they escalate into larger problems associated with injection molding defects and causes.
Moreover, optimizing mold design through simulations allows engineers to anticipate potential issues before production runs begin; this proactive measure significantly reduces risks related to short shots or gate vestiges by ensuring proper flow paths are established from day one! Staff training programs focusing on best practices will further equip operators with knowledge about recognizing common signs of failure early on—leading them toward effective interventions before major disruptions occur.
Lastly—and perhaps most importantly—investing in high-quality raw materials will reduce occurrences related specifically back toward moulding material defects; selecting reliable suppliers who adhere strictly to industry standards guarantees a more consistent end product every time!
Understanding Moulding Material Defects
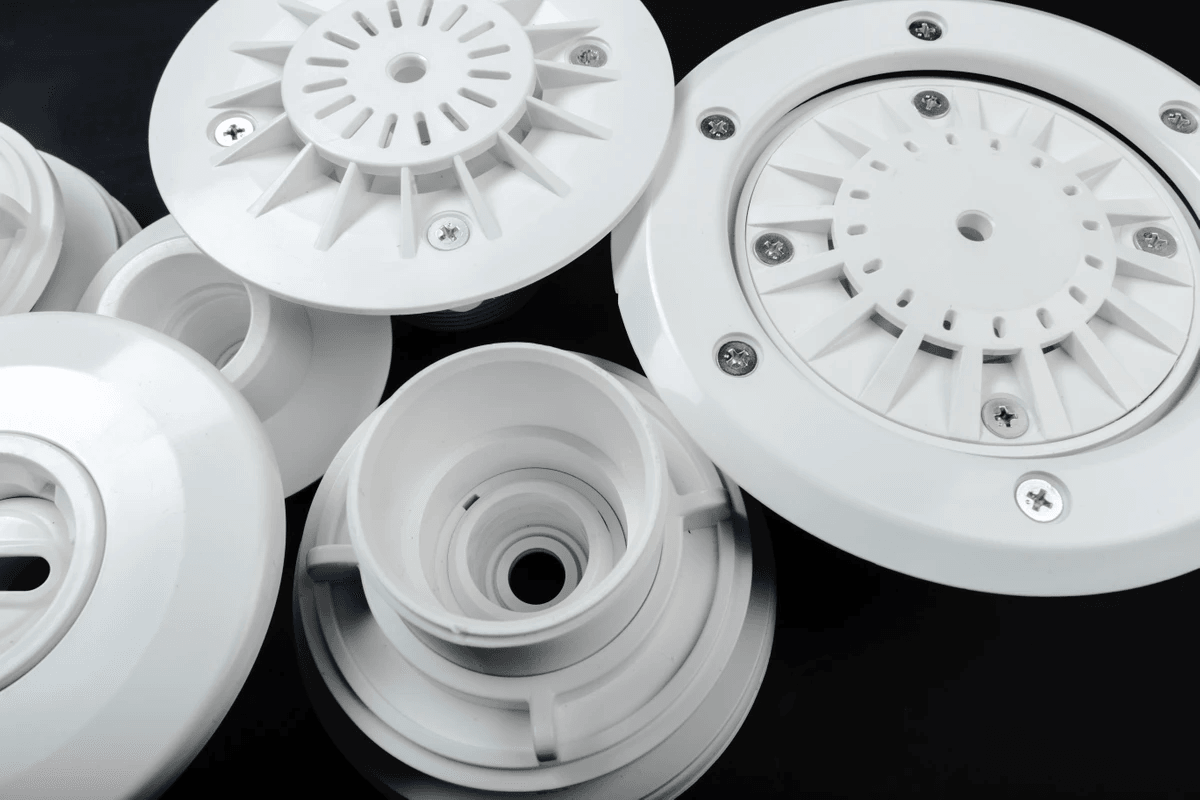
Moulding material defects can significantly impact the quality and functionality of injection-molded products. These defects arise from issues related to the raw materials used, such as impurities, inconsistencies in composition, or improper handling during the manufacturing process. Recognizing what are moulding material defects is crucial for maintaining production efficiency and ensuring that end products meet industry standards.
What are moulding material defects?
Moulding material defects refer to a range of flaws that occur due to problems with the materials utilized in the injection molding process. These can include issues like contamination, moisture absorption, or inadequate thermal stability of the materials. When asking, What are the common defects in injection molding? it’s important to consider that many of these originate from poor-quality raw materials or improper storage conditions.
Effects of Material Quality on Production
The quality of moulding materials directly influences production outcomes and product integrity. Low-quality materials can lead to various injection molding defects and causes such as warping, cracking, or surface blemishes on finished products. Furthermore, compromised material quality may result in increased scrap rates and rework costs, ultimately affecting a company's bottom line and reputation.
Best Practices for Material Selection
To minimize the risk of moulding material defects, implementing best practices for material selection is essential. Start by sourcing high-quality raw materials from reputable suppliers who adhere to strict quality control measures; this is a vital step in avoiding potential pitfalls associated with poor material choices. Additionally, conducting thorough testing before full-scale production can help identify any issues early on—ensuring that your team is not left asking What is the problem with the injection molding process? down the line.
Conclusion
In summary, understanding injection molding defects and their causes is crucial for maintaining high-quality production standards. By identifying what are the common defects in injection molding, manufacturers can take proactive measures to enhance their processes. Acknowledging issues like gate vestiges, process failures, and moulding material defects allows for better product outcomes and customer satisfaction.
Key Takeaways on Injection Molding Defects
Injection molding defects can arise from various sources, including material quality, process parameters, and design flaws. Recognizing what are the common defects in injection molding—such as short shots, warping, and sink marks—enables teams to address them efficiently. Furthermore, understanding what is the cause of gate vestiges helps manufacturers improve product aesthetics while maintaining functionality.
Effective Strategies to Mitigate Causes
To effectively mitigate the causes of injection molding defects, implementing rigorous quality control measures is essential. This includes regular monitoring of the injection molding process to identify what is the problem with the injection molding process early on. Additionally, selecting high-quality materials and adhering to best practices can significantly reduce occurrences of moulding material defects.
The Role of the Baoyuan Team in Quality Assurance
The Baoyuan team plays a pivotal role in ensuring that production meets industry standards by focusing on reducing injection molding defects and causes at every stage of manufacturing. Their expertise allows them to pinpoint specific issues such as gate vestiges or other common problems effectively. By fostering a culture of continuous improvement and utilizing advanced detection methods, Baoyuan enhances overall product quality while minimizing waste.