Introduction
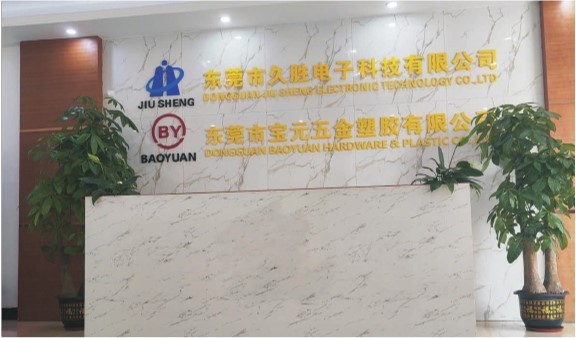
When it comes to the plastic manufacturing process, understanding the intricate methods and techniques involved is crucial for producing high-quality products. From the manufacturing process of plastic bottles to the production of plastic tubes, each step requires precision and expertise. Efficient production is key in meeting demand without compromising on quality, making it essential for companies like Baoyuan to excel in this field.
Understanding Plastic Manufacturing Process
The manufacturing process of plastic involves a series of steps, from creating plastic raw materials and granules to molding them into various forms. Whether it's injection molding, blow molding, or extrusion molding, each method plays a vital role in shaping the final product.
Importance of Efficient Production
Efficient production in the plastic manufacturing industry is essential for meeting market demands while maintaining high standards of quality. With an increasing need for products like plastic bottles and tubes, companies must optimize their processes to ensure timely delivery without compromising on durability and functionality.
Baoyuan: Expertise in Plastic Manufacturing
As a leader in the industry, Baoyuan brings extensive expertise to the table when it comes to plastic manufacturing. With a focus on innovation and efficiency, they have mastered various types of plastic manufacturing processes and are committed to delivering exceptional products that meet stringent quality standards.
Types of Plastic Manufacturing Process
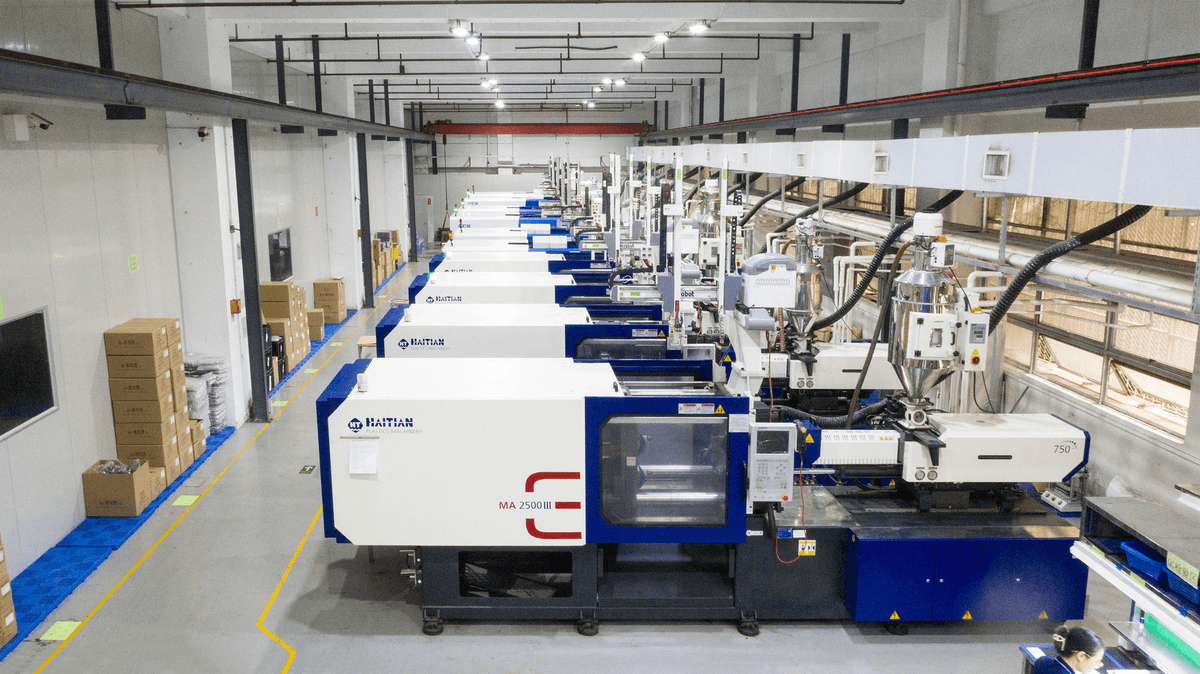
When it comes to plastic manufacturing process, there are several key methods used in the industry. Injection molding is a popular technique that involves injecting molten plastic into a mold to create various products such as toys, automotive parts, and household items. Blow molding, on the other hand, is commonly used for producing hollow objects like plastic bottles and containers by inflating a hot tube of plastic until it takes the shape of the desired mold. Lastly, extrusion molding is utilized for creating continuous lengths of plastic products such as pipes, tubing, and sheets by forcing melted raw material through a die.
Injection Molding
Injection molding is a versatile process that allows for the production of complex and intricate shapes with high precision and consistency. The method begins with feeding plastic granules into a hopper which then feeds into a heated barrel where it is mixed and melted before being injected into a mold cavity under high pressure. Once cooled and solidified, the finished product is ejected from the mold ready for further processing or use. Additionally, injection molding is ideal for creating products with thin walls and complex geometries, making it a cost-effective option for mass production. The ability to use multiple materials simultaneously also adds to its versatility, allowing for the creation of composite parts with varying characteristics.
Blow Molding
In the manufacturing process of plastic bottles, blow molding plays an essential role in creating various types of containers including water bottles, soda bottles, and shampoo bottles among others. The process starts by melting down plastic granules and then forming them into a parison (hollow tube) which is then clamped into a mold where compressed air inflates it to take on the shape of the cavity before cooling down.
Blow molding is a versatile process that allows for the creation of containers in various shapes and sizes, making it a popular choice for manufacturers. The use of compressed air to inflate the parison ensures that the plastic takes on the exact shape of the mold, resulting in consistent and high-quality bottles. Additionally, the cooling down process solidifies the plastic, ensuring that the bottles are durable and ready for use.
Extrusion Molding
For producing items like plastic tubes or pipes, extrusion molding is employed to create continuous lengths of these products with uniform cross-sections. The method involves feeding raw material in the form of pellets or granules through an extruder where it is melted before being forced through a die to produce long shapes that can be cut to specific lengths as needed.
After the plastic shapes are cut to specific lengths, they can undergo additional processing such as cooling, shaping, or finishing to meet the desired specifications. This may involve using water baths or air cooling systems to solidify the plastic material and ensure it retains its shape. Additionally, the extruded plastic products can be further treated with additives or coatings to enhance their properties, such as adding UV stabilizers for outdoor use or colorants for aesthetic appeal.
Key Stages in Plastic Manufacturing
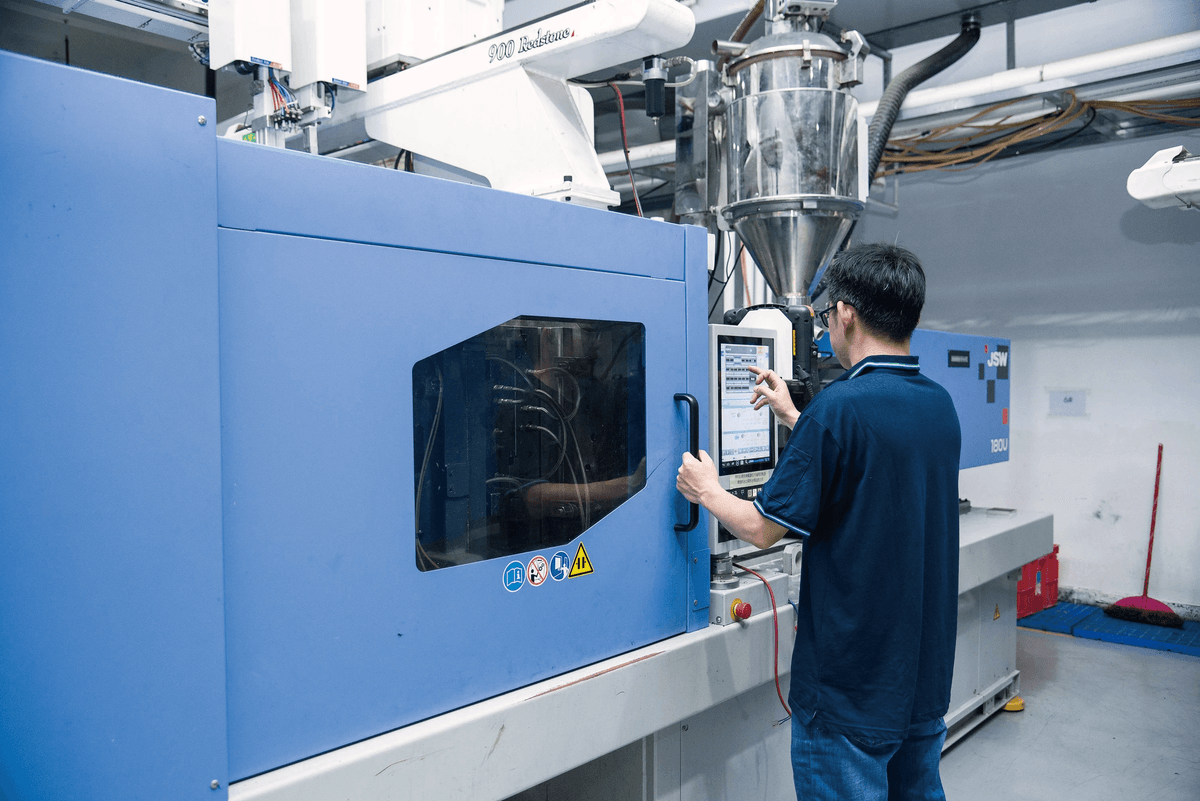
When it comes to the plastic manufacturing process, there are several key stages that play a crucial role in ensuring the production of high-quality plastic products. One of the initial stages is mold design, where the specifications for the plastic product are carefully crafted into a mold. This stage requires precision and attention to detail to ensure that the final product meets all required specifications.
Mold Design
The mold design stage in the plastic manufacturing process involves creating a blueprint for the plastic product. This includes determining the shape, size, and dimensions of the final product, as well as any specific features or details that need to be incorporated. The use of advanced CAD software allows for intricate designs to be translated into precise molds, ensuring that each product is manufactured with accuracy and consistency.
Mold Opening
Once the mold design is finalized, the next stage in the process is mold opening. This involves separating the two halves of the mold to reveal a cavity into which molten plastic will be injected. The opening and closing of molds must be executed with precision to avoid any defects or imperfections in the final product.
Injection Molding Process
The injection molding process is a critical stage in plastic manufacturing, where molten plastic material is injected into a pre-designed mold cavity at high pressure and temperature. This allows for complex shapes and structures to be formed with accuracy and efficiency, making it one of the most widely used methods for producing plastic products such as bottles, tubes, and various other items.
By paying close attention to these key stages in plastic manufacturing - from mold design to injection molding - Baoyuan ensures that every product meets stringent quality standards while also optimizing production efficiency.
Factors Affecting Efficiency
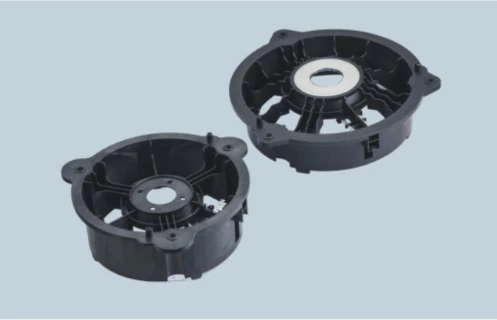
When it comes to the plastic manufacturing process, quality assurance plays a crucial role in ensuring efficiency. By implementing stringent quality control measures at every stage of production, manufacturers can minimize defects and wastage, ultimately streamlining the entire process.
Quality Assurance
Quality assurance in the plastic manufacturing process involves thorough inspection of raw materials, strict adherence to production standards, and rigorous testing of finished products. By maintaining high-quality standards, manufacturers can reduce the likelihood of rework and recalls, thus enhancing overall efficiency.
Single-color and Double-color Products
Another factor that affects efficiency in plastic manufacturing is the production of single-color versus double-color products. While single-color products may require less time and resources to produce, double-color items often involve more complex processes and longer cycle times, impacting overall production efficiency.
Skillful Use of Software
In today's digital age, skillful use of software has become increasingly important in optimizing the plastic manufacturing process. From CAD/CAM design software to advanced production planning tools, leveraging technology can significantly enhance operational efficiency and minimize errors.
Optimization Techniques
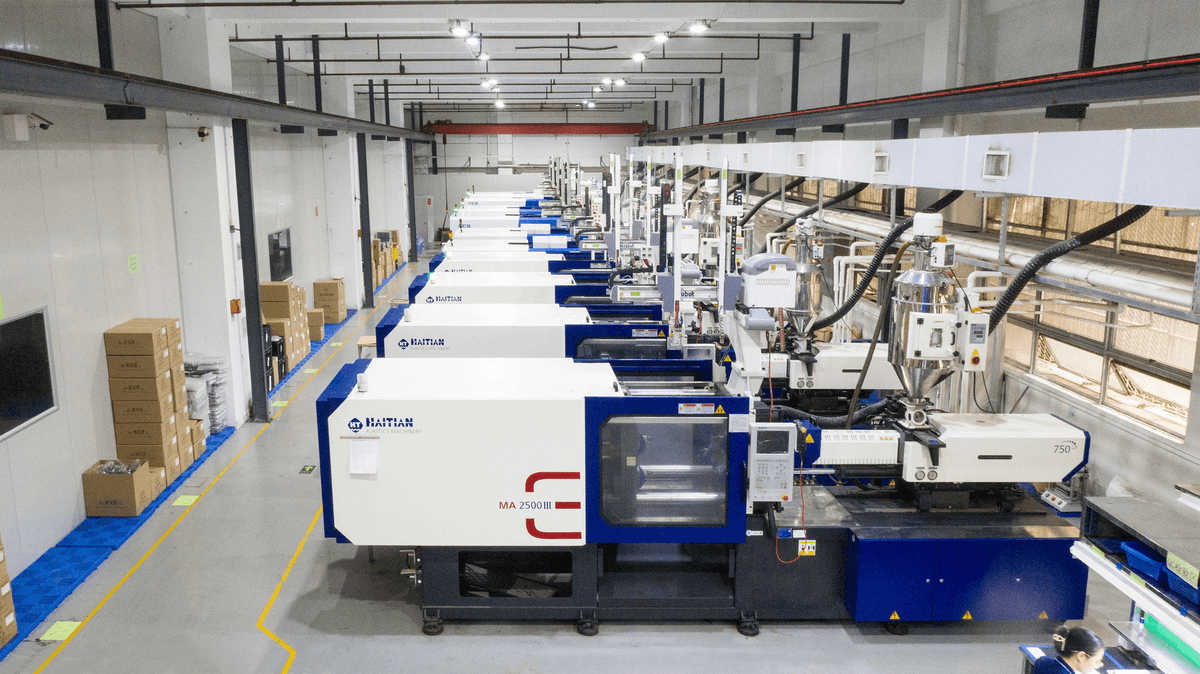
In the realm of plastic manufacturing process, optimization is key to achieving efficiency and cost-effectiveness. Streamlining the production line involves identifying and eliminating bottlenecks, reducing unnecessary steps, and maximizing output. Baoyuan excels in this area, ensuring that every stage of the plastic manufacturing process is seamlessly integrated for optimal productivity.
Streamlining Production Line
Baoyuan employs cutting-edge technology to streamline the production line, minimizing downtime and enhancing overall throughput. By leveraging automated systems and robotics, they are able to significantly reduce lead times and increase output capacity. This ensures that the plastic bottle manufacturing process or plastic tube manufacturing process is carried out with precision and speed.
Implementing Lean Manufacturing Principles
With a commitment to lean manufacturing principles, Baoyuan focuses on eliminating waste and maximizing value for their clients. By continuously analyzing their processes and making incremental improvements, they are able to optimize resource utilization while maintaining top-notch quality in the manufacturing process of plastic products.
Continuous Improvement Strategies
Baoyuan's dedication to continuous improvement is evident in their proactive approach to refining their operations. They regularly gather feedback from their team members and clients, using this input to drive innovation in their plastic raw material manufacturing process or plastic granules manufacturing process. This ensures that they stay ahead of industry trends while delivering exceptional results.
Sustainable Practices in Plastic Manufacturing
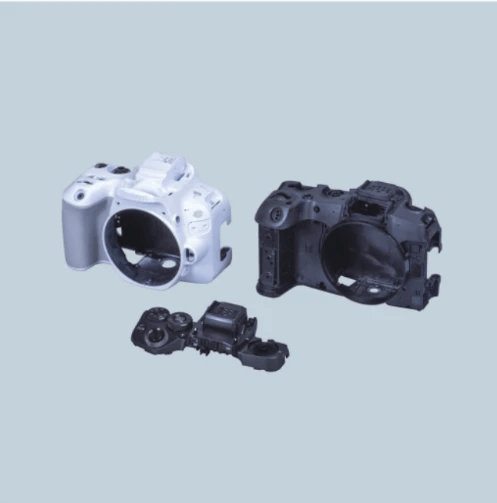
Recycling and Reusability
In the plastic manufacturing process, recycling and reusability play a crucial role in reducing environmental impact. By incorporating recycled materials into production, companies can minimize waste and promote a circular economy. Baoyuan is committed to utilizing recycled plastics to create sustainable products that align with eco-friendly initiatives.
By using recycled plastics, Baoyuan is not only reducing the amount of waste in production but also contributing to the conservation of natural resources. This approach helps to lessen the demand for new raw materials, which in turn reduces the environmental impact associated with extracting and processing virgin materials. Additionally, incorporating recycled plastics into production processes can also lead to cost savings for companies, making it a financially sustainable choice as well.
Reducing Waste in Production
Efficient management of plastic waste during the manufacturing process is essential for minimizing environmental harm. Implementing lean manufacturing principles and optimizing production lines can significantly reduce material wastage and enhance overall efficiency. Baoyuan's dedication to waste reduction ensures responsible and sustainable practices in plastic production.
Eco-friendly Raw Material Selection
Selecting environmentally friendly raw materials is essential for promoting sustainability in the plastic manufacturing process. By prioritizing biodegradable or renewable resources, manufacturers can minimize their ecological footprint and contribute to a greener future. Baoyuan's commitment to eco-friendly raw material selection underscores its dedication to sustainable production practices.
By sourcing raw materials from sustainable suppliers, Baoyuan ensures that its production process aligns with its eco-friendly values. This commitment to responsible sourcing not only benefits the environment but also supports ethical and fair labor practices. Through careful selection of raw materials, Baoyuan sets a positive example for the industry, inspiring other manufacturers to prioritize sustainability in their supply chain.
Conclusion
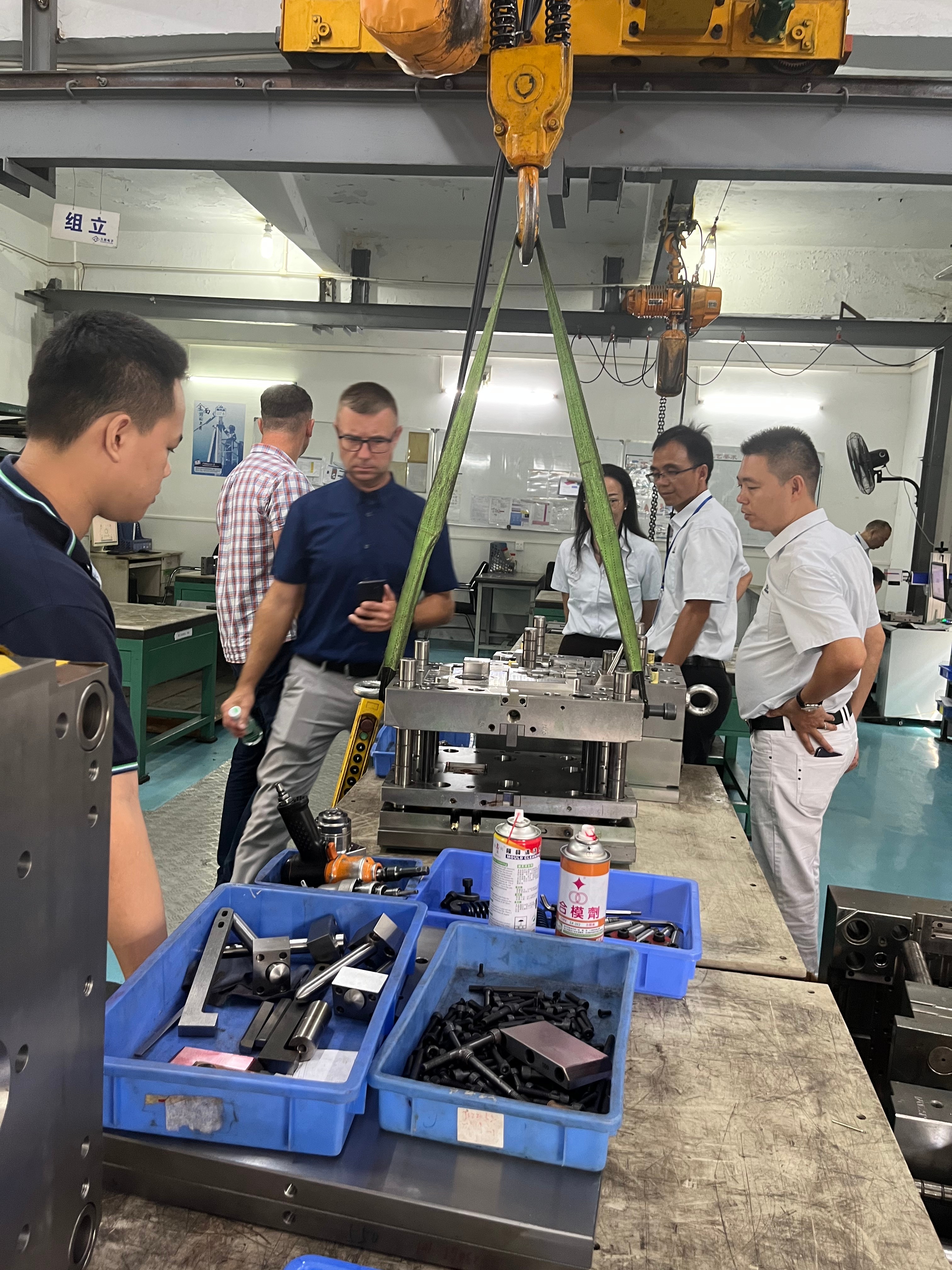
As we wrap up our discussion on the plastic manufacturing process, it's clear that achieving efficiency is crucial for the industry's success. Baoyuan has established itself as an industry-leading expert in this field, with a deep understanding of the various types of plastic manufacturing processes. Their commitment to advancing towards sustainable production sets them apart from their competitors.
Achieving Efficiency in Plastic Manufacturing
Efficiency in the plastic manufacturing process is essential for meeting consumer demand and reducing production costs. By optimizing key stages and implementing lean manufacturing principles, companies can streamline their operations and improve overall efficiency. Baoyuan's expertise in this area makes them a valuable partner for businesses looking to enhance their plastic manufacturing processes.
Efficiency in the plastic manufacturing process not only leads to cost savings but also allows companies to meet consumer demand in a timely manner. By optimizing key stages such as material sourcing, production, and distribution, businesses can reduce lead times and improve their ability to respond to market trends. Baoyuan's expertise in implementing lean manufacturing principles ensures that their partners can stay ahead of the competition by continuously improving their plastic manufacturing processes.
Baoyuan: Industry-Leading Expertise
Baoyuan's extensive knowledge of the plastic manufacturing process, including the manufacturing process of plastic bottles and plastic tube manufacturing process, positions them as a trusted leader in the industry. Their ability to adapt to new technologies and optimize production lines ensures that they remain at the forefront of innovation and efficiency.
Baoyuan's commitment to sustainable production sets them apart as an industry leader. By investing in eco-friendly materials and energy-efficient technologies, Baoyuan is dedicated to reducing their environmental impact while maintaining high-quality production standards. Their forward-thinking approach not only benefits the planet but also positions them as a preferred partner for businesses seeking sustainable packaging solutions.
Advancing Towards Sustainable Production
As environmental concerns continue to grow, sustainable practices in plastic manufacturing are becoming increasingly important. Baoyuan's commitment to recycling and reusability, reducing waste in production, and selecting eco-friendly raw materials demonstrates their dedication to advancing towards sustainable production. By partnering with Baoyuan, businesses can align themselves with these eco-conscious practices.
In addition to their commitment to recycling and reusability, Baoyuan also prioritizes energy efficiency in their production processes. By investing in state-of-the-art technology and implementing energy-saving measures, they are able to minimize their environmental impact while maintaining high-quality output. This dedication to sustainable energy practices sets them apart as a leader in eco-friendly plastic manufacturing.