Introduction
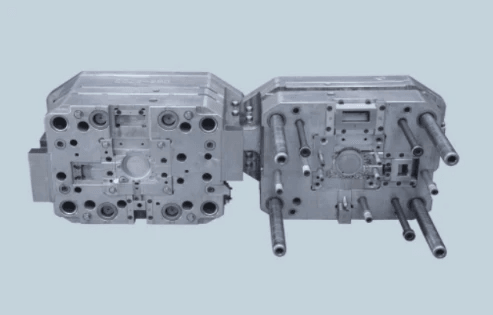
Injection molding is a fascinating process, and at the heart of it lies the often-overlooked component known as injection molding gates. These gates play a crucial role in directing molten plastic into the mold cavity, influencing both the quality of the final product and the efficiency of production. Understanding injection molding gates is not just about knowing their function; it's about recognizing how their design impacts everything from material flow to overall manufacturing costs.
Understanding Injection Molding Gates
At its core, an injection molding gate serves as the entry point for molten plastic into a mold. There are various types of gates for injection molding, each with unique characteristics that affect how materials flow into molds and solidify. From pin gate injection molding to valve gates, understanding these different types is essential for choosing the right solution for your project.
Common Issues with Injection Molding Gates
Despite their importance, many manufacturers encounter common issues with injection molding gates that can lead to defects or inefficiencies in production. Problems such as incomplete filling, gate marks on finished products, or excessive cycle times can all stem from poorly designed or improperly placed gates. Addressing these challenges early on can save time and resources while enhancing product quality.
Importance of Proper Gate Design
The design of injection molding gates cannot be overstated; it directly influences production efficiency and part quality. A well-designed gate ensures optimal flow characteristics while minimizing defects like sink marks or warping in molded parts. By investing time in understanding what is runner and gate in injection molding, manufacturers can significantly improve their processes and outcomes.
Types of Gates for Injection Molding
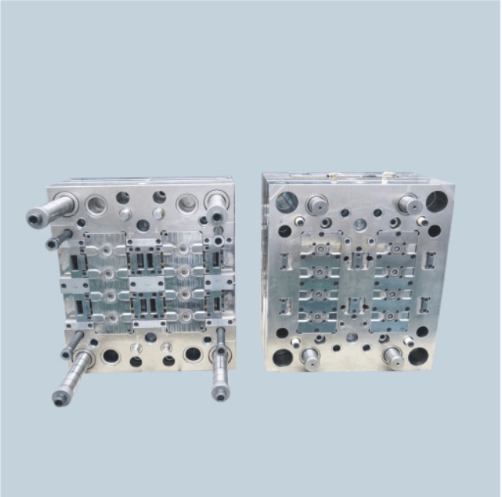
When it comes to injection molding gates, understanding the various types is crucial for optimizing your production process. Different gate designs can significantly affect the quality of your final product, as well as the efficiency of the manufacturing process itself. In this section, we will explore the different types of gates used in injection molding and how they can impact your project.
Overview of Different Gate Types
There are several types of gates for injection molding, each with its unique characteristics and applications. Common gate types include edge gates, fan gates, tab gates, and pin gate injection molding systems. Each type serves a specific purpose and can influence factors such as material flow, cooling time, and surface finish on the molded part.
Edge gates are often used for large parts where aesthetics are less critical, while fan gates provide a wider entry point to distribute material evenly across a mold cavity. Pin gate injection molding is particularly advantageous when precision is required or when dealing with complex geometries that need careful filling without compromising quality.
Benefits of Pin Gate Injection Molding
Pin gate injection molding offers several benefits that make it an attractive choice for many projects. One key advantage is its ability to create smaller, more precise gate openings that minimize visible marks on the finished product—ideal for high-quality consumer goods where aesthetics matter. Additionally, pin gates help control material flow more effectively than some other designs.
Another benefit lies in their versatility; pin gates can be used in both single-cavity and multi-cavity molds without sacrificing performance or quality. This flexibility makes them suitable for a wide range of applications across various industries—from automotive components to intricate medical devices—where precision matters.
Choosing the Right Gate for Your Project
Selecting the right type of gate for your project involves considering multiple factors that impact both production efficiency and final product quality. Begin by assessing your design requirements: how complex is your part geometry? What level of surface finish do you need? Understanding these criteria will guide you toward choosing between options like pin gate injection molding or other alternatives.
Another important consideration is material type; some materials flow better with specific gate designs due to viscosity differences during processing. Finally, don't forget about cost implications—while some advanced gating systems may offer superior performance or aesthetic benefits, they could also increase production costs significantly.
Ultimately, balancing these elements will help ensure you select an appropriate design that meets both functional needs and budget constraints while achieving optimal results with your chosen injection molding gates.
What Are Gates in Injection Molding?
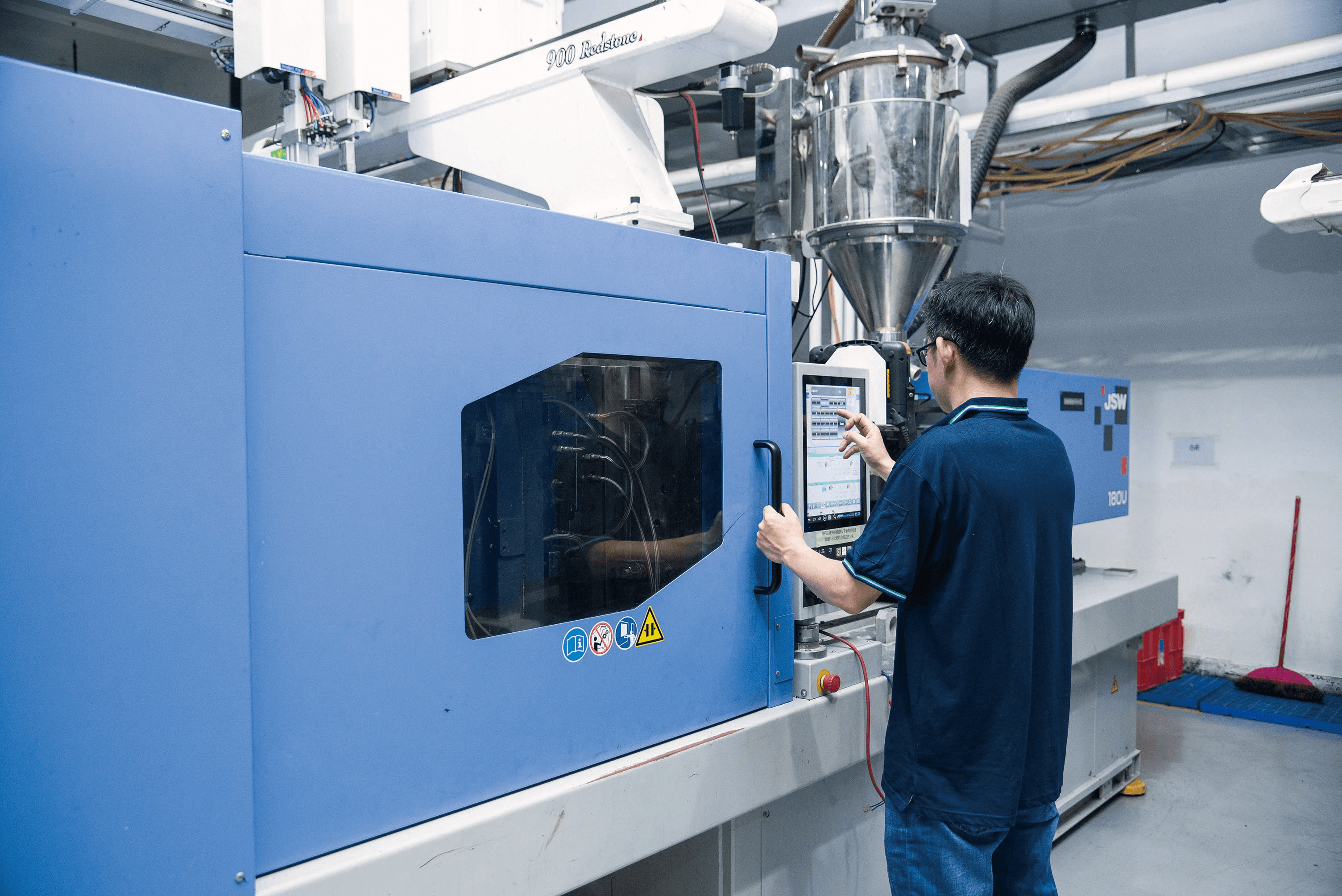
When diving into the world of injection molding, understanding what gates are is crucial. These small but mighty components play a vital role in the process, acting as the entry point for molten plastic into the mold cavity. Without proper design and function of injection molding gates, production can suffer significantly.
Definition and Function
Gates in injection molding are essentially openings that allow the molten material to flow from the runner system into the mold cavity. They serve as a controlled passage for material entry, ensuring that parts fill uniformly and efficiently. The type of gate used can influence not only the filling process but also aspects like surface finish and overall part quality.
Impact on Production Efficiency
The design of injection molding gates has a direct impact on production efficiency and cycle times. Well-designed gates facilitate faster filling, reducing cycle times and leading to higher output rates. Conversely, poorly designed gates may cause issues such as incomplete fills or excessive scrap rates, which ultimately hinder productivity.
Common Misconceptions
One common misconception is that all injection molding gates are created equal; this couldn't be further from the truth! Different types of gates serve various purposes depending on project requirements—some may be optimal for thin-walled parts while others excel in thicker applications. Additionally, many believe that gate size is negligible; however, it plays a significant role in controlling flow rate and ensuring consistent quality throughout production.
The Runner and Gate Relationship
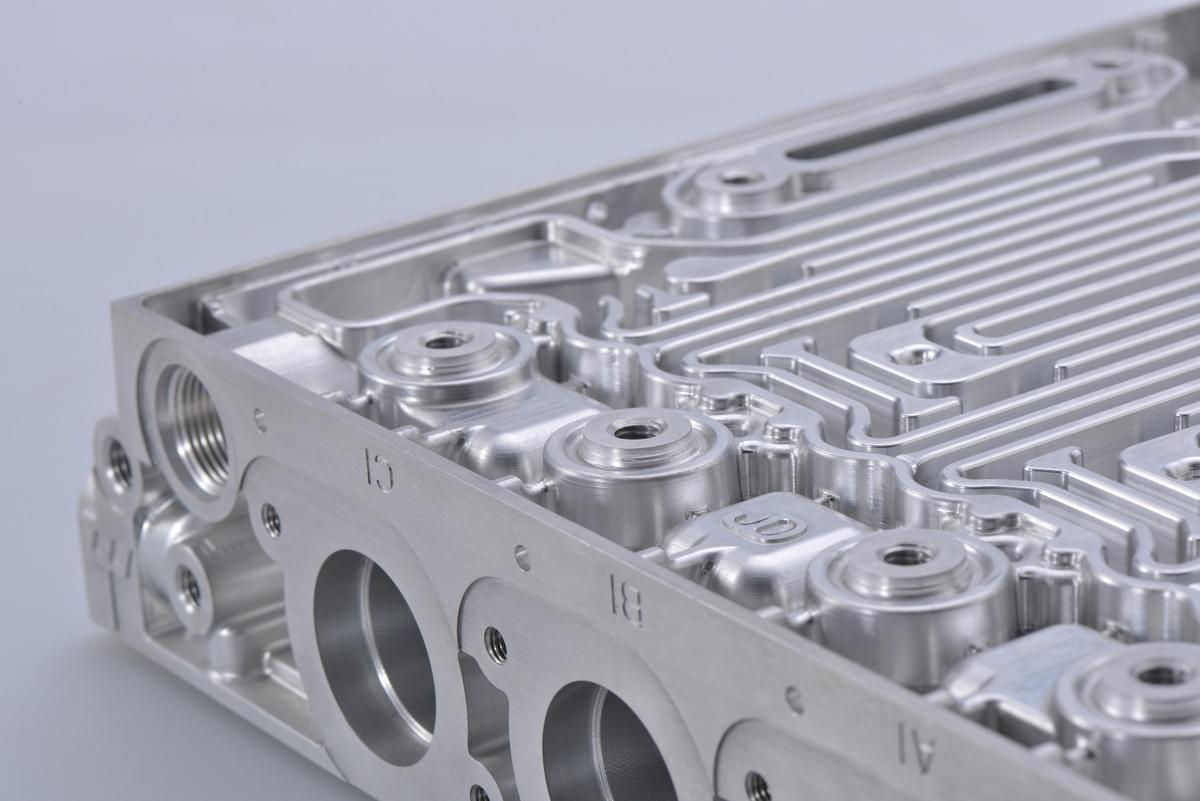
Understanding the relationship between the runner and gate in injection molding is crucial for achieving optimal production outcomes. The runner system serves as the pathway that directs molten plastic to various injection molding gates, which then deliver it into the mold cavities. This intricate interplay affects not only flow efficiency but also the overall quality of the final product.
What is Runner and Gate in Injection Molding?
In injection molding, runners are channels that transport molten material from the injection unit to the gates of a mold. Gates are openings through which this material enters the mold cavity, determining how well and evenly it fills each section. Together, these components form a critical connection in ensuring that injection molding gates function effectively.
The design of both runners and gates can significantly impact production efficiency and part quality. For instance, poorly designed runners may lead to uneven filling or air traps, while inadequate gate sizing can cause flow issues or defects in molded parts. Understanding what is runner and gate in injection molding helps manufacturers optimize their designs for better results.
How Design Affects Flow and Quality
The design choices made for runners and gates directly influence how molten plastic flows through them during the injection process. Factors such as cross-sectional area, length, and geometry all play a role in determining how quickly and uniformly material reaches each gate. An efficient design minimizes pressure loss while maximizing filling speed, which ultimately enhances part quality.
Moreover, different types of gates for injection molding—such as pin gate injection molding or valve gates—offer unique advantages depending on specific project requirements. For example, a well-placed valve gate can help control flow more precisely than traditional options, reducing waste and improving surface finish quality. Therefore, understanding how design affects flow is essential for optimizing both efficiency and product integrity.
Best Practices for Runner System Design
When designing a runner system for your project, several best practices can help ensure effective performance of your injection molding gates. First off, consider minimizing the length of runners while maintaining adequate cross-sectional area; shorter runners reduce cycle time but must be large enough to avoid excessive pressure drops during filling.
Additionally, incorporating features like rounded corners within your runner design can facilitate smoother flow transitions compared to sharp angles which may create turbulence—an enemy of efficient filling! Lastly, always account for thermal considerations; maintaining consistent temperatures throughout your runner system helps ensure uniform melting characteristics across all injected materials.
Exploring Valve Gates in Injection Molding
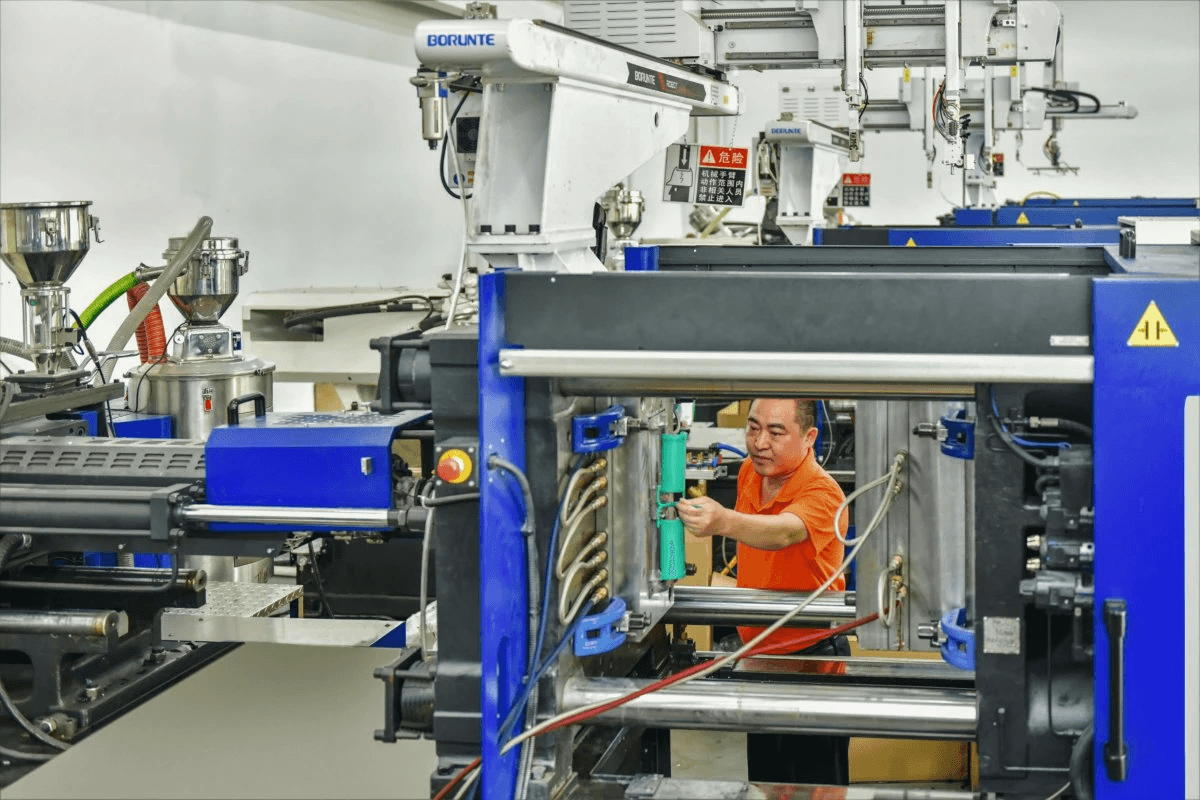
Valve gates have become a significant topic in the realm of injection molding gates, offering unique advantages and applications. Understanding what a valve gate is can help manufacturers make informed decisions about their molding processes. In this section, we will delve into the definition, benefits, and limitations of valve gates in injection molding.
What is a Valve Gate in Injection Molding?
A valve gate in injection molding is a specialized type of gate that utilizes a mechanism to control the flow of molten plastic into the mold cavity. Unlike traditional gates that remain open during filling, valve gates close off the flow at strategic points, allowing for better control over the injection process. This precise gating method minimizes issues such as flash or unwanted material flow, ultimately enhancing part quality.
Advantages Over Traditional Gates
One of the main advantages of using valve gates over traditional types of gates for injection molding is their ability to reduce cosmetic defects on molded parts. Since they can be closed at specific times during filling, they help prevent surface imperfections caused by excess material or turbulence. Additionally, valve gates contribute to more efficient production by reducing cycle times and waste material—making them an appealing choice for high-quality applications.
Another perk? The flexibility offered by valve gate systems allows for better design options when creating complex geometries or multi-cavity molds. With improved control over fill patterns and pressures, manufacturers can achieve higher precision and consistency across multiple parts produced from a single mold cycle. This adaptability makes them ideal for industries where aesthetics and performance are paramount.
Applications and Limitations
While valve gates offer numerous benefits, they do come with certain limitations that should be considered when selecting injection molding gates for your project. For instance, these systems can be more complex than traditional pin gate injection molding setups; thus requiring additional maintenance and calibration to ensure optimal performance over time. Furthermore, their initial investment costs may be higher due to the need for specialized equipment.
Despite these challenges, valve gates find applications across various industries including automotive components, consumer electronics housings, and medical device manufacturing—where quality and precision are non-negotiable factors. By understanding both their advantages and limitations within different contexts of what are gates in injection molding processes, manufacturers can make informed choices that align with their production goals.
Understanding Gate Seal in Injection Molding
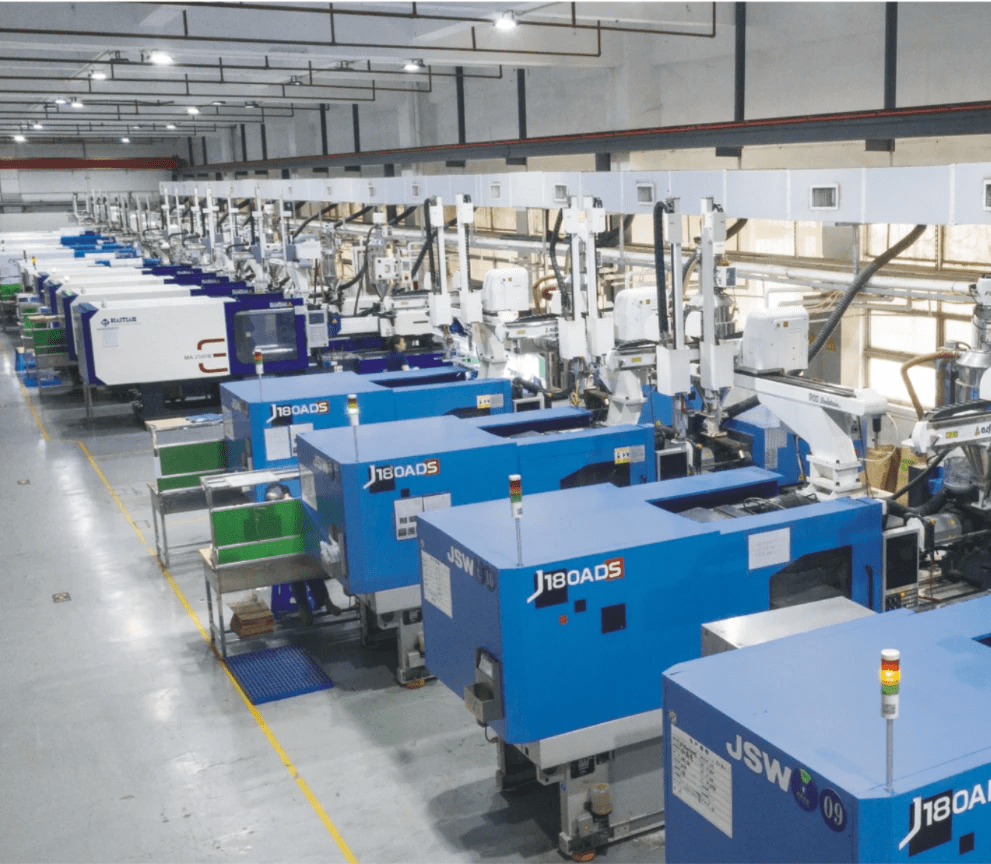
In the world of injection molding, gate seals play a pivotal role in ensuring that the final product meets quality standards. A proper gate seal prevents material leakage during the injection process, which can lead to defects and increased production costs. Understanding what a gate seal is and how it functions is essential for anyone involved in injection molding gates.
What is Gate Seal in Injection Molding?
Gate seal refers to the mechanism that ensures a tight closure at the gate area during the injection molding process. This seal prevents molten plastic from escaping before it solidifies, maintaining control over material flow and ensuring that each part is filled correctly. Without an effective gate seal, manufacturers could face issues like flash or incomplete parts, which can compromise product integrity.
Importance for Quality Control
The quality of gate seals directly impacts overall production efficiency and product reliability. An inadequate seal can lead to defects such as short shots or surface imperfections, ultimately affecting customer satisfaction and increasing waste rates. By focusing on proper gate design and sealing techniques, manufacturers can significantly reduce these risks while enhancing their reputation for quality.
Techniques for Achieving Proper Seals
Achieving a reliable gate seal involves several techniques that hinge on understanding various types of gates for injection molding. First, selecting the right type of gate—such as pin gate injection molding—can facilitate better sealing performance due to its design characteristics. Additionally, employing precise temperature control during processing helps ensure that materials remain at optimal viscosity for effective sealing when they reach the gates.
Conclusion
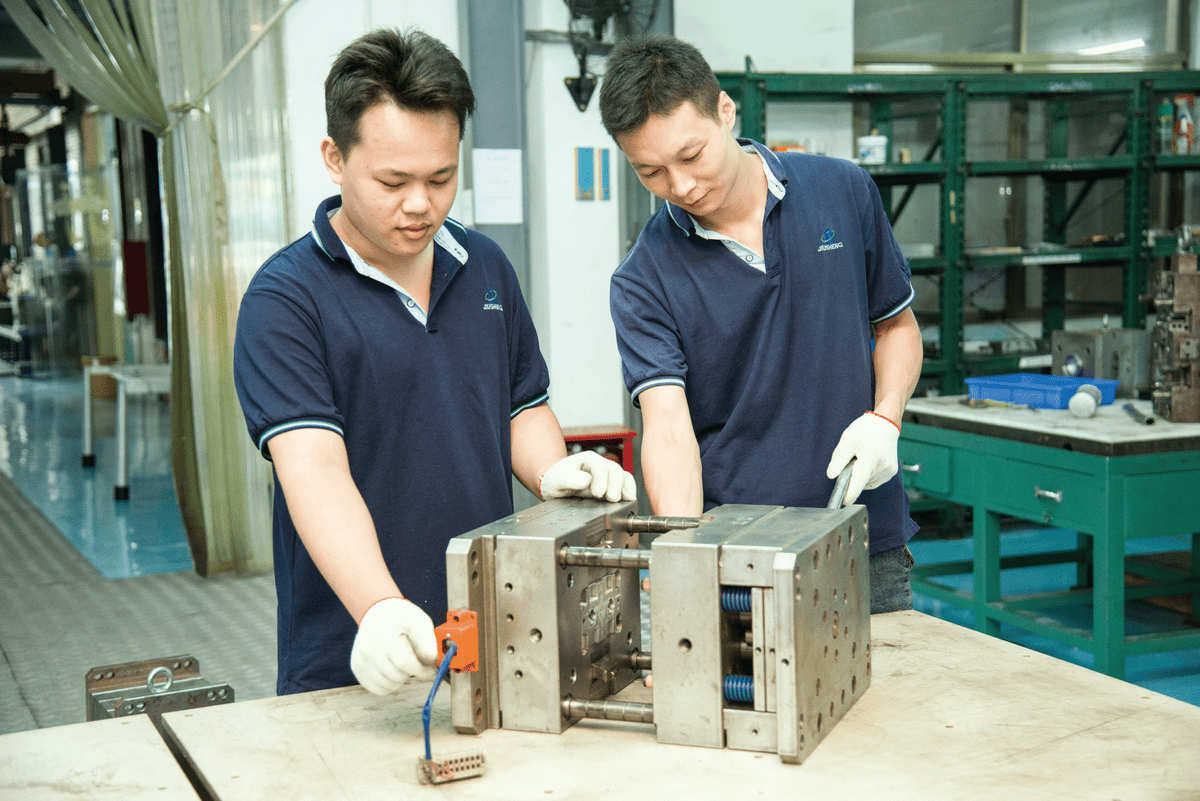
In the world of injection molding, understanding injection molding gates is crucial for achieving high-quality products efficiently. The design and type of gate used can significantly affect production efficiency, part quality, and overall project success. By exploring various aspects of gates, including their types, functions, and the relationship with runners, we can make informed decisions that enhance our manufacturing processes.
Key Takeaways on Injection Molding Gates
Injection molding gates come in various types, each with its unique advantages and applications. From pin gate injection molding to valve gates, knowing what are gates in injection molding helps manufacturers select the best option for their specific needs. Additionally, understanding what is runner and gate in injection molding allows for optimized flow and quality control throughout the production process.
Tackling Common Gate Issues Effectively
Common issues with injection molding gates can lead to defects and inefficiencies if not addressed properly. Techniques such as ensuring proper gate seal in injection molding can prevent material leakage and improve product integrity. By being proactive about these challenges and implementing best practices for runner system design, manufacturers can mitigate risks associated with different types of gates for injection molding.
Expert Insights from the Baoyuan Team
The Baoyuan team emphasizes that selecting the right type of gate is essential for successful injection molding projects. Their expertise highlights how a well-designed valve gate in injection molding can offer significant advantages over traditional methods while also acknowledging potential limitations. With continuous advancements in technology and materials, staying informed about innovations related to injection molding gates will empower manufacturers to achieve optimal results.