Introduction
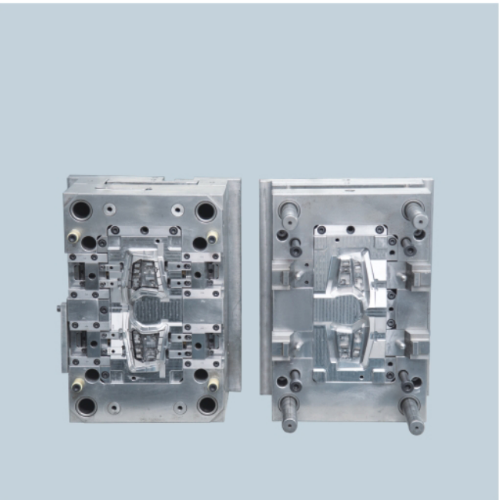
When it comes to manufacturing, understanding the differences between die casting and injection molding is crucial. Baoyuan has established itself as a leader in plastic injection molding, offering expertise in producing high-quality products. By comparing die casting and injection molding, we can make informed decisions about which process best suits our production needs.
Understanding Die Casting and Injection Molding
Die casting involves forcing molten metal into a mold cavity under high pressure, while injection molding uses molten material injected into a mold cavity. Both processes have their unique advantages and applications, making it essential to understand their differences for efficient production.
Die casting is known for producing parts with excellent dimensional accuracy and smooth surface finishes, making it ideal for manufacturing complex shapes and thin-walled parts. On the other hand, injection molding is preferred for its ability to produce large quantities of parts with consistent quality and high precision. Understanding the specific advantages of each process allows manufacturers to choose the most suitable method for their production needs, ultimately leading to cost savings and improved product quality.
Baoyuan's Expertise in Injection Molding
Baoyuan's proficiency in using advanced software for mold design ensures precision and accuracy in every product manufactured through injection molding. The company's commitment to quality and reliability sets it apart as an industry leader in plastic injection molding. Additionally, Baoyuan's expertise in material selection and process optimization allows for the production of high-quality, durable plastic components. This attention to detail results in products that meet or exceed industry standards, making Baoyuan a trusted partner for businesses seeking top-notch injection molding solutions.
Comparing Die Casting and Injection Molding
When comparing die casting vs injection molding cost, it becomes evident that each process has its own set of benefits and challenges. By weighing the pros and cons of metal injection molding materials versus die casting materials, we can make informed decisions about which method best suits our production requirements. Die casting offers high strength and durability, making it ideal for producing complex shapes with thin walls. On the other hand, injection molding provides more design flexibility and allows for the use of a wider range of materials, including plastics and metals. Understanding these differences is crucial in determining which process will result in the most cost-effective solution for your specific project.
Baoyuan's Expertise in Injection Molding
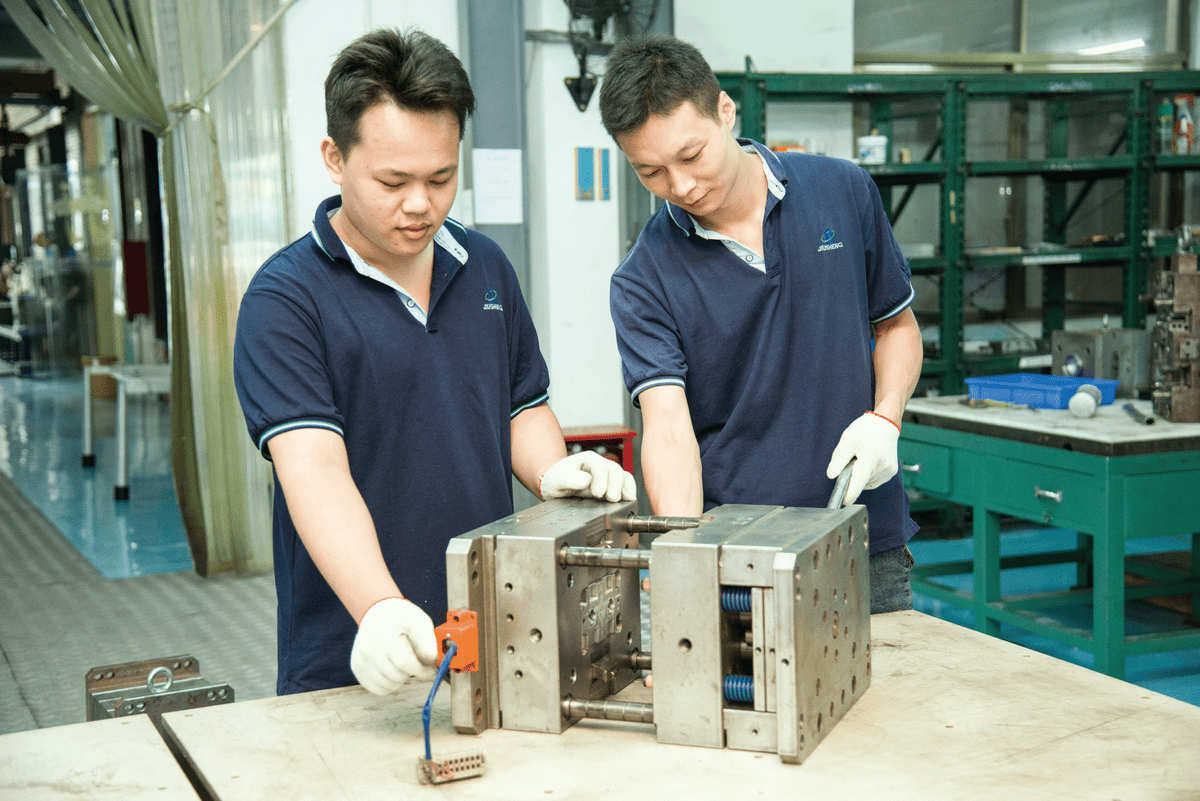
Baoyuan's proficiency in injection molding is evident in their adept use of cutting-edge software for mold design. By harnessing the power of advanced technology, they are able to create precise and intricate molds that meet the highest standards of quality and efficiency.
Baoyuan's proficient use of software for mold design
The skilled team at Baoyuan leverages sophisticated software to meticulously craft molds that are tailored to the unique specifications of each project. This attention to detail ensures that every product produced through injection molding is of superior quality, meeting or exceeding client expectations.
In addition to ensuring superior quality, the use of advanced software for mold design at Baoyuan also allows for greater precision and accuracy in the production process. This means that each mold is meticulously crafted to exact specifications, reducing the margin for error and minimizing material waste. As a result, clients can benefit from cost savings and a more efficient production process, ultimately leading to a competitive edge in the market.
Benefits of injection molding in mass production
Injection molding offers significant advantages in mass production, allowing for the rapid creation of large quantities of products with consistent quality and minimal waste. Baoyuan's expertise in this area enables them to deliver cost-effective solutions for high-volume manufacturing needs.
In addition to the advantages of rapid production and consistent quality, injection molding also allows for the use of a wide range of materials, including thermoplastics, metals, and elastomers. This versatility enables manufacturers to create products with varying properties and characteristics, meeting diverse customer needs without compromising on quality or efficiency. Baoyuan's understanding of material selection in injection molding further enhances their ability to deliver tailored solutions for mass production.
Challenges of injection molding in material selection
While injection molding offers a wide range of material options, selecting the most suitable material for a specific project can be a complex task. Baoyuan's experienced team navigates these challenges with precision, ensuring that the chosen materials align with the desired characteristics and performance requirements.
Selecting the right material for injection molding involves considering factors such as strength, flexibility, heat resistance, and durability. Baoyuan's team of experts evaluates these characteristics to ensure that the chosen material will meet the specific requirements of the project. This attention to detail helps to avoid potential issues such as warping, cracking, or poor surface finish that can result from using an unsuitable material.
Pros of Die Casting

Die casting offers high strength and durability, making it ideal for producing sturdy and long-lasting products. The metal components created through die casting are able to withstand heavy loads and harsh environments, ensuring reliable performance in various applications.
High strength and durability of die cast products
With die casting, manufacturers can achieve a smooth surface finish and intricate details on the final products. This allows for the creation of aesthetically pleasing components with fine details that meet the desired specifications. In addition to the visual appeal, die cast products also offer high strength and durability, making them ideal for applications where reliability is essential. Whether it's automotive parts, electronic components, or household fixtures, die cast products can withstand the rigors of daily use without compromising on quality.
Smooth surface finish and intricate details
When it comes to large production runs, die casting is a cost-effective option due to its ability to produce a high volume of parts in a shorter amount of time. This efficiency results in lower overall production costs, making die casting an economical choice for mass manufacturing.
In addition to its cost-effectiveness for large production runs, die casting also offers a smooth surface finish and intricate details. This is particularly advantageous for parts that require a high level of precision and aesthetic appeal. The process of die casting allows for the creation of complex shapes and thin walls, resulting in finished products with a refined and polished appearance. This makes die casting an ideal choice for industries such as automotive, consumer electronics, and home appliances where the visual appeal of the final product is crucial.
Cost-effective for large production runs
Baoyuan's expertise in die casting enables us to deliver high-quality parts that meet the most demanding requirements. With our advanced technology and skilled team, we ensure that our die cast products exhibit exceptional strength, precision, and cost-effectiveness.
By leveraging the benefits of die casting such as superior strength, detailed finishes, and cost efficiency for large-scale production runs, Baoyuan is committed to providing top-notch solutions for our clients' manufacturing needs.
Making informed decisions about manufacturing processes is crucial for achieving optimal results. When comparing metal injection molding vs. die casting, it's essential to consider factors such as material options, part complexity, production volume, and overall cost-effectiveness.
Pros of Injection Molding
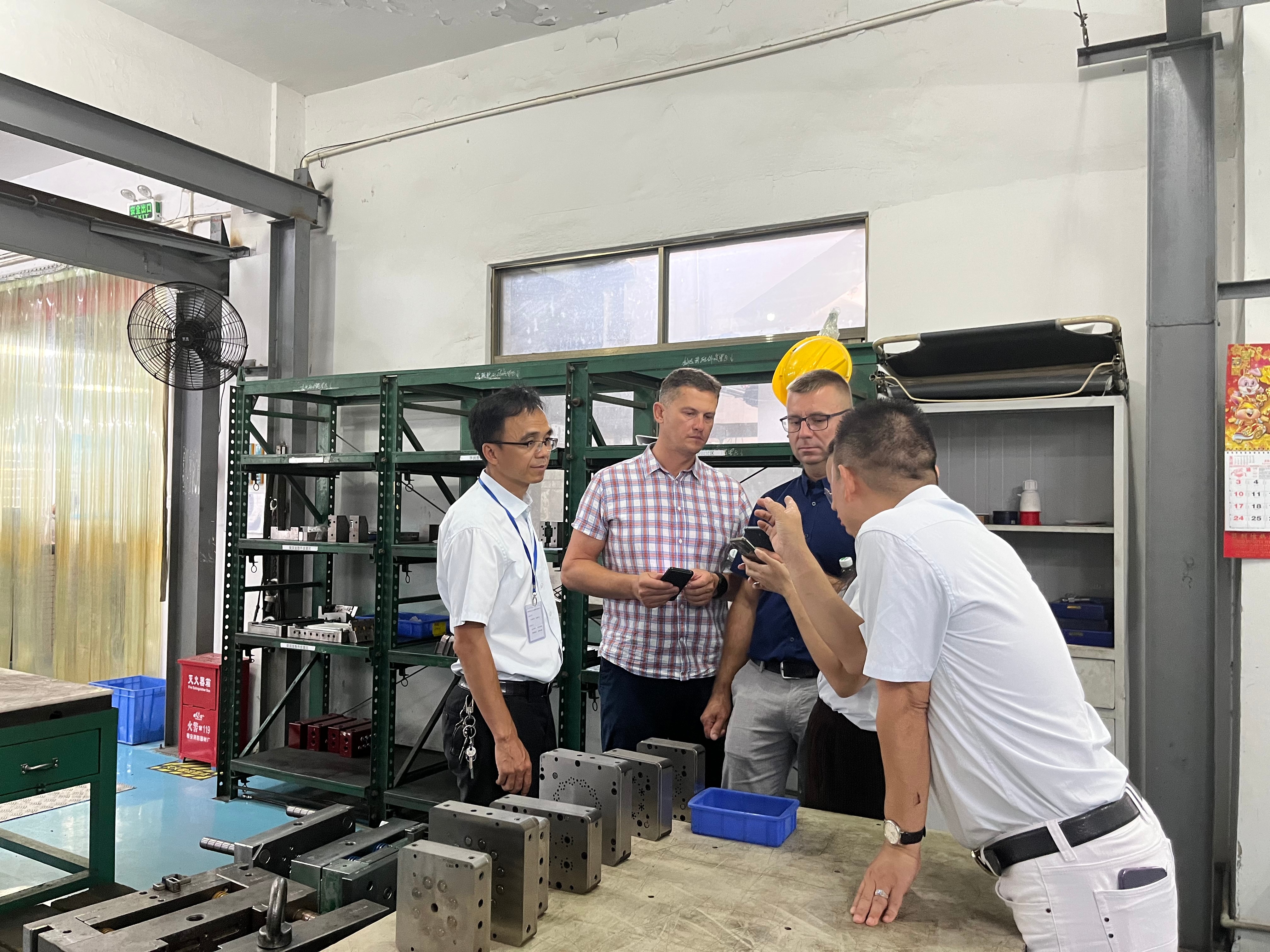
When comparing die casting vs injection molding, one of the significant advantages of injection molding is the wide range of material options it offers, providing manufacturers with flexibility in choosing the best material for their specific product requirements. From traditional plastics to advanced composites and even metal injection molding materials, the versatility of injection molding allows for endless possibilities in material selection.
Wide range of material options for flexibility
Plastic injection molding allows for the use of various thermoplastics and thermosetting polymers, offering different properties such as strength, flexibility, and heat resistance. On the other hand, metal injection molding enables the production of parts using a wide range of metal alloys, including stainless steel, aluminum, and titanium. This flexibility in material choice makes injection molding suitable for diverse applications across industries.
Complex shapes and detailed features achievable
Injection molding excels in producing intricate and complex shapes with detailed features that may be challenging or impossible to achieve through other manufacturing processes. The ability to create precise geometries and intricate designs makes it a preferred method for manufacturing products with unique shapes or complex internal structures.
Reduced waste and material usage
Another advantage of injection molding is its capability to minimize waste and optimize material usage during production. With proper design considerations and efficient mold filling techniques, manufacturers can reduce scrap materials and achieve higher production yields, ultimately leading to cost savings and environmental benefits.
With its wide range of material options, ability to produce complex shapes with detailed features, and reduced waste and material usage benefits, it's clear that injection molding offers numerous advantages over die casting when it comes to manufacturing precision parts efficiently
Cons of Die Casting
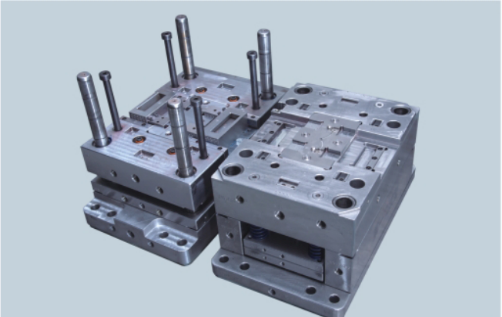
When considering die casting vs injection molding, one of the drawbacks of die casting is the high initial tooling and setup costs. The creation of molds for die casting can be quite expensive, especially for complex parts with intricate details. This can make die casting less cost-effective for smaller production runs or prototypes.
Another limitation of die casting is that it is primarily limited to certain metals and alloys, such as aluminum, zinc, and magnesium. While these materials offer high strength and durability, they may not always be the best choice for every application. This restricts the versatility of die casting compared to plastic injection molding, which offers a wider range of material options.
Furthermore, die casting typically has longer production lead times compared to injection molding. The process of creating and refining molds for die casting can be time-consuming, leading to delays in production timelines. This can be a significant drawback when quick turnaround times are essential for meeting market demands.
Cons of Injection Molding
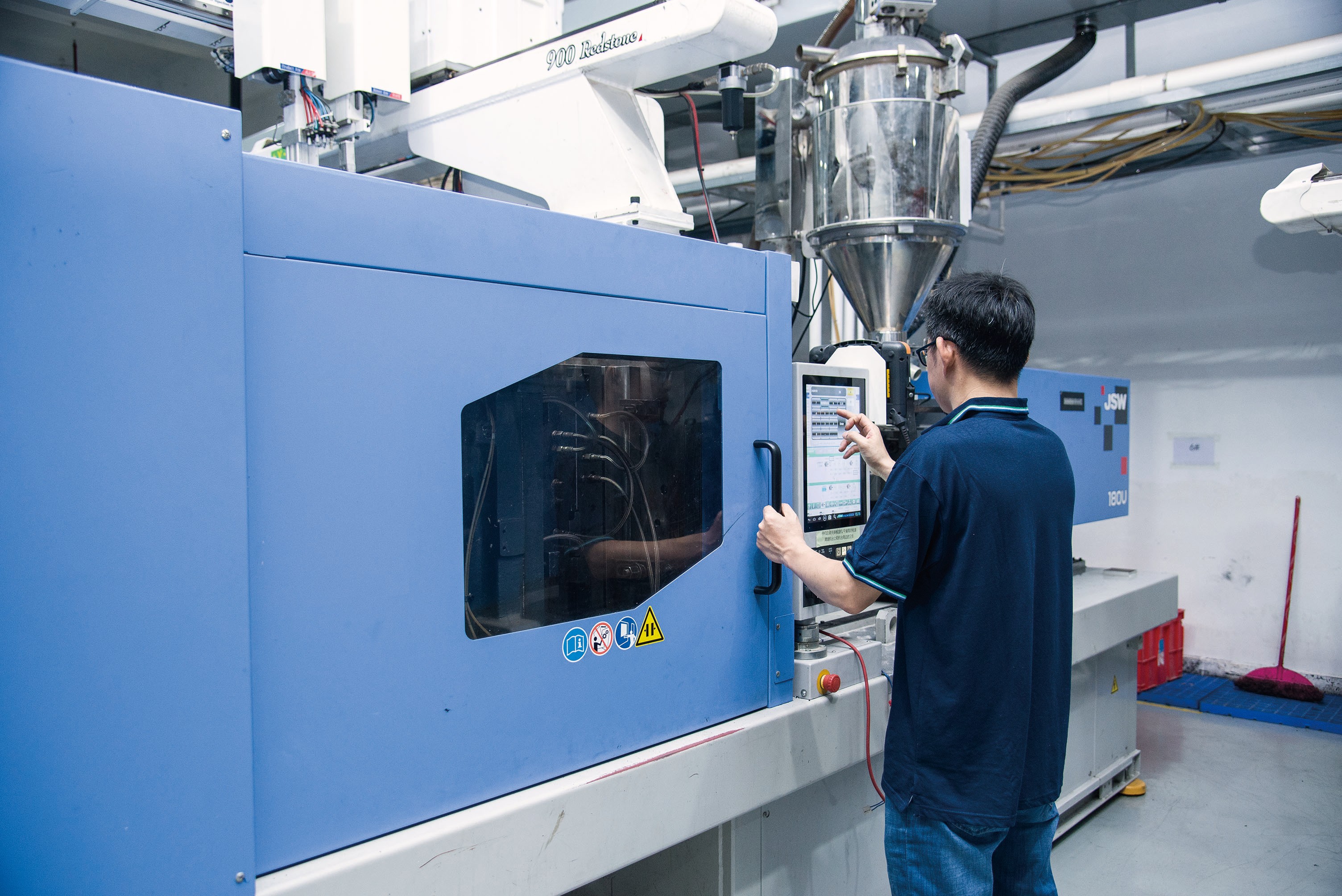
Complexity in mold design and maintenance
Injection molding requires intricate mold designs, adding complexity to the manufacturing process. The maintenance of these molds also demands attention to detail and expertise to ensure the quality of the final products. Furthermore, the cost of equipment and energy for high-volume runs can be significant, adding another layer of complexity to the overall production process. This requires careful budgeting and planning to ensure that the manufacturing operation remains profitable while meeting production demands.
Equipment and energy costs for high-volume runs
High-volume injection molding runs can lead to significant equipment and energy costs, impacting the overall production expenses. The need for specialized machinery and continuous energy supply adds to the operational costs.
Furthermore, the complexity of intricate designs in high-volume runs can pose quality control challenges. Ensuring that each molded piece meets the required specifications and standards can be time-consuming and labor-intensive, adding to the overall production expenses. This meticulous attention to detail is necessary to maintain the integrity of the final products and meet customer expectations.
Quality control challenges for intricate designs
Intricate designs in injection molding can pose quality control challenges, as ensuring consistency in detailed features becomes a critical aspect of the production process.
In addition to consistency in detailed features, intricate designs also present challenges in terms of material flow and fill. The complexity of the design can lead to uneven distribution of the molten material, resulting in defects such as warping, sink marks, or voids. This requires careful analysis and adjustment of the injection molding process parameters to achieve uniform filling and minimize defects, adding another layer of complexity to quality control for intricate designs.
Conclusion
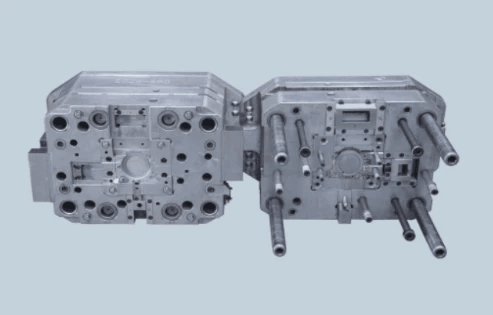
Choosing the Right Manufacturing Process
When deciding between die casting vs injection molding, it's essential to consider factors such as material, production volume, and cost. While die casting offers high strength and durability for metal parts, plastic injection molding provides flexibility and intricate designs for large-scale production runs. Understanding the specific needs of your project will help in choosing the right manufacturing process.
Baoyuan's Commitment to Quality Injection Molding
With Baoyuan's expertise in plastic injection molding and metal injection molding materials, clients can be assured of high-quality products that meet their specifications. Baoyuan's proficient use of software for mold design ensures precision and efficiency in the manufacturing process, resulting in cost-effective solutions for mass production needs.
Making Informed Decisions: Die Casting vs Injection Molding
In making informed decisions about die casting vs injection molding, it's crucial to weigh the pros and cons of each process. While die casting offers smooth surface finish and cost-effectiveness for large production runs, plastic injection molding provides a wide range of material options and reduced waste. By understanding these differences, clients can make informed choices based on their specific requirements.
Overall, both die casting and injection molding have their strengths and limitations. With Baoyuan's expertise in injection molding and commitment to quality manufacturing processes, clients can trust that their project needs will be met with precision and efficiency. By understanding the unique advantages of each method, clients can make informed decisions that align with their project goals.