Introduction
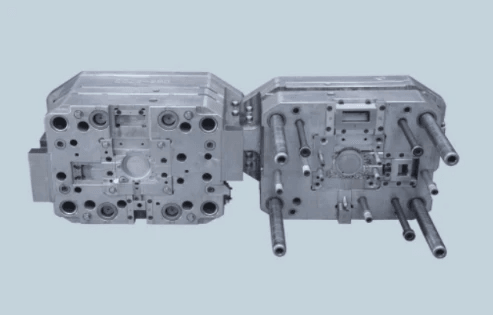
Understanding Die Casting and Injection Molding
Die casting involves forcing molten metal into a mold under high pressure, creating precise shapes with excellent surface finishes. On the other hand, injection molding typically refers to injecting molten plastic into molds, which allows for intricate designs and high-volume production runs. So what is the difference between die cutting and injection molding? While both processes aim to create components efficiently, they differ significantly in materials used and applications.
The Importance of Choosing the Right Method
Choosing the right manufacturing method can make or break your project’s budget and timeline. For instance, if you opt for die casting when injection molding would suffice (or vice versa), you might end up with excess costs or delays in production. Thus, understanding why you would use die casting—or when it’s better to choose metal injection molding vs. die casting—is essential for making informed decisions.
Overview of Key Differences
At first glance, die cast vs injection molding might seem interchangeable; however, they cater to different needs within the manufacturing spectrum. Die casting is typically used for metals like aluminum or zinc and excels in producing durable parts with tight tolerances; whereas injection molding shines in creating complex plastic components at rapid speeds. Additionally, it’s important to consider factors like cost efficiency and precision when evaluating these methods—especially when discussing what is the disadvantage of die casting compared to its plastic counterpart.
What is Die Casting?
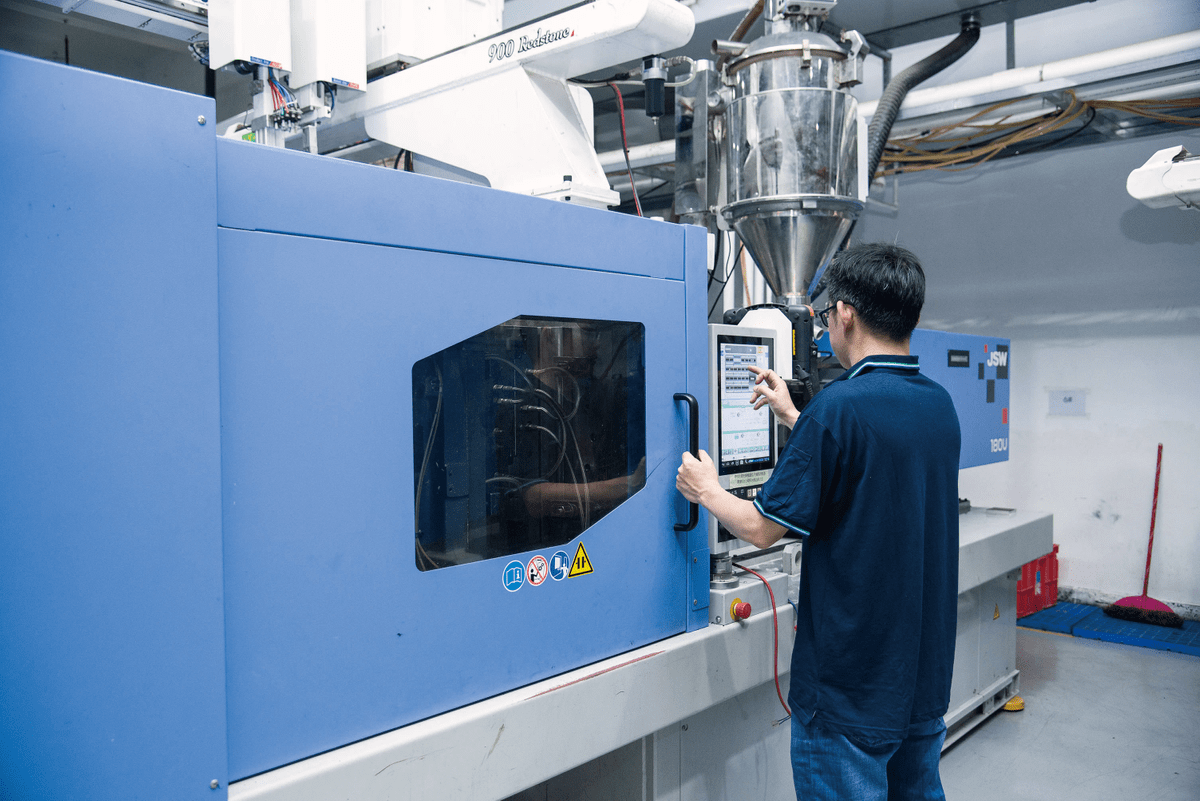
Die casting is a manufacturing process that involves forcing molten metal into a mold cavity under high pressure. This technique allows for the creation of intricate shapes and fine details, making it a favored method in various industries. But what exactly sets die casting apart from other methods like injection molding?
The Process Explained
The die casting process begins with the melting of metal, often aluminum or zinc, which is then injected into a steel mold at high speed and pressure. Once the metal cools and solidifies, the mold opens, releasing the finished part. This method enables rapid production of complex geometries with excellent surface finishes, but it’s essential to understand what is the difference between die cutting and injection molding to choose the right approach for your project.
Common Materials Used
Die casting typically employs non-ferrous metals such as aluminum, zinc, magnesium, and copper alloys due to their favorable properties like low melting points and excellent fluidity when molten. These materials are chosen not only for their strength but also for their ability to be cast into thin-walled sections without compromising structural integrity. However, when comparing Metal Injection Molding vs. Die Casting, it's crucial to consider how material choices can affect performance in specific applications.
Typical Applications
You’ll find die casting used extensively in industries ranging from automotive to consumer electronics due to its ability to produce lightweight yet durable components efficiently. Common applications include engine blocks, transmission housings, and various electronic enclosures—proof that die casting is indeed a powerhouse in manufacturing! So why would you use die casting over other methods? Its unique combination of cost-effectiveness and precision makes it an attractive choice for mass production runs.
What is Injection Molding?
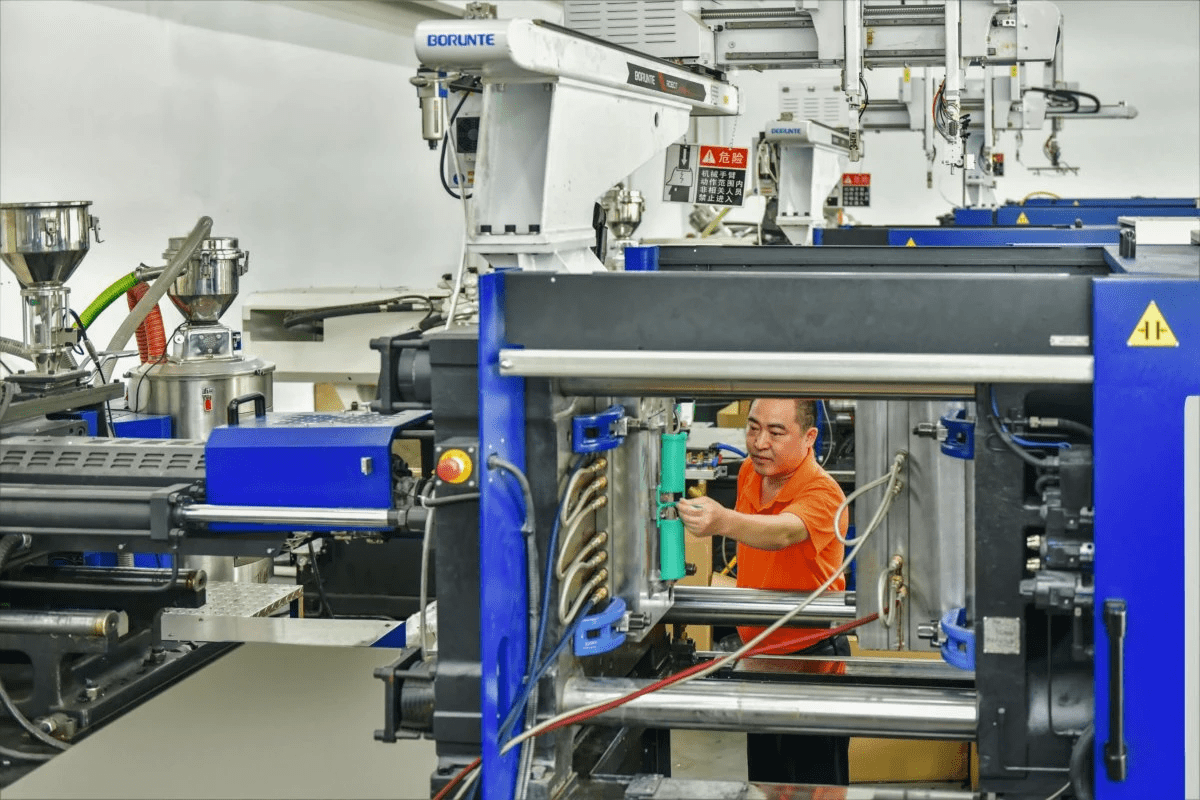
Injection molding is a manufacturing process that involves injecting molten material into a mold to create precise and complex shapes. This method is widely used due to its ability to produce large quantities of parts with high consistency and minimal waste. It’s particularly popular in industries where speed and precision are paramount, making it a strong contender when discussing die cast vs injection molding.
The Process Explained
The injection molding process begins with the heating of plastic pellets until they melt into a viscous liquid. This molten plastic is then injected into a pre-designed mold under high pressure, allowing it to fill every cavity and detail of the mold before cooling and solidifying. Once cooled, the mold opens, and the finished product is ejected—ready for use or further processing—making it an efficient choice compared to traditional methods like die casting.
Common Materials Used
Injection molding primarily utilizes thermoplastics such as ABS (Acrylonitrile Butadiene Styrene), polycarbonate, and nylon due to their flexibility and durability. Additionally, thermosetting plastics can also be employed for applications requiring heat resistance or rigidity. Understanding what materials work best helps clarify what is the difference between die cutting and injection molding, as each method has its preferred materials based on desired properties.
Typical Applications
This versatile process finds applications across various industries including automotive parts, consumer electronics, medical devices, and packaging solutions. For example, most modern car interiors feature components made through injection molding for their intricate designs and lightweight properties. With such widespread use, it's essential to weigh the advantages of metal injection molding vs die casting depending on specific project requirements; each method serves unique needs in manufacturing.
Die Cast vs Injection Molding: Key Differences
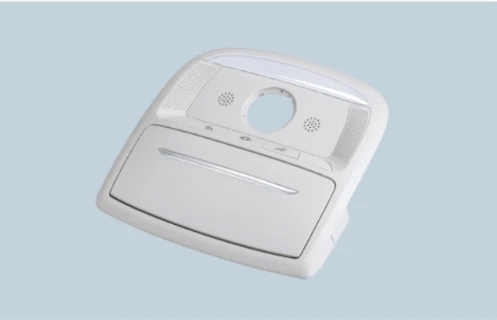
Cost Considerations
Cost is often a primary factor in deciding between die casting and injection molding. Generally, die casting involves higher initial tooling costs due to the need for durable molds that can withstand high pressures and temperatures. However, if you're producing large volumes of parts, the per-unit cost can decrease significantly with die casting compared to injection molding—making it a cost-effective choice in such scenarios.
On the flip side, while injection molding may have lower upfront costs for tooling, especially for smaller production runs, the materials used can also impact overall expenses. For instance, thermoplastics are generally less expensive than metals used in die casting. Therefore, understanding what is the disadvantage of die casting in terms of initial investment versus long-term production costs is essential when weighing your options.
Production Speed and Efficiency
When comparing metal injection molding vs. die casting regarding speed and efficiency, both processes have their advantages depending on specific project requirements. Die casting typically offers faster cycle times due to its ability to produce parts at high speeds with minimal cooling time required after each cycle. This makes it ideal for high-volume production where time-to-market is critical.
Injection molding also boasts impressive efficiency but may require longer cycle times depending on part complexity and material cooling rates. However, modern advancements in technology have improved both methods' speeds significantly over recent years. Ultimately, whether you prioritize quick turnaround or flexibility will influence your choice between these two methods.
Precision and Detail
Precision is another area where die cast vs injection molding diverges notably; both methods excel but cater to different needs based on application requirements. Die casting typically produces parts with excellent dimensional accuracy and surface finish due to its high-pressure process—ideal for intricate designs that demand tight tolerances without extensive post-processing work.
Conversely, while injection molding can achieve great detail as well—especially when utilizing advanced techniques like multi-material or overmolding—it may not always reach the same level of precision as die cast components made from metals like aluminum or zinc alloys. Thus, if your project requires exceptionally fine details or specific mechanical properties found only in certain metals, asking yourself why would you use die casting might lead you toward that method as a more suitable option.
Advantages and Disadvantages
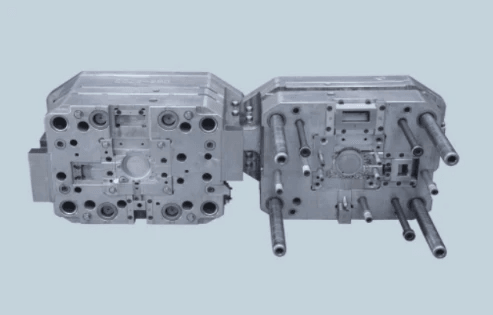
Why Would You Use Die Casting?
Die casting is often favored for its ability to produce high volumes of parts with exceptional precision and surface finish. One of the main reasons to choose die casting is its efficiency in mass production; once the mold is created, each cycle can yield numerous identical parts quickly. Additionally, die cast components are typically stronger than those produced through other methods due to the dense nature of metals used in the process.
In terms of material versatility, why would you use die casting? It accommodates a variety of alloys such as aluminum, zinc, and magnesium that offer different properties suitable for various applications. Moreover, the process allows for intricate designs that can include undercuts and thin walls without compromising strength — a significant advantage when compared to other methods like injection molding.
What is the Disadvantage of Die Casting?
Despite its many advantages, what is the disadvantage of die casting? One notable drawback lies in the high initial costs associated with creating molds; they can be expensive and time-consuming to develop. This means that if you're producing small quantities or if your design changes frequently, those upfront costs may not justify using this method.
Additionally, while die cast components are strong, they are not always suitable for every application; certain materials may limit flexibility or impact resistance compared to alternatives like injection molded plastics. Furthermore, there are concerns about porosity in some metal castings which could affect performance in critical applications — definitely something to consider when weighing your options.
Metal Injection Molding vs. Die Casting: Pros and Cons
When comparing metal injection molding vs. die casting, it’s essential to recognize that each method has distinct pros and cons tailored for specific needs. Metal injection molding excels at producing complex shapes with fine details at lower volumes than traditional die casting but often struggles with larger parts where strength is paramount — making it less ideal for heavy-duty applications.
On the flip side, while die casting offers superior strength and durability for high-volume production runs — particularly in industries like automotive or aerospace — it falls short on flexibility regarding design changes after mold creation compared to metal injection molding’s adaptability during development phases. Ultimately deciding between these two processes requires a thorough understanding of your project requirements: volume needed, material specifications, cost constraints — all crucial factors when pondering what is the difference between casting and die casting?
Real-World Applications of Each Method
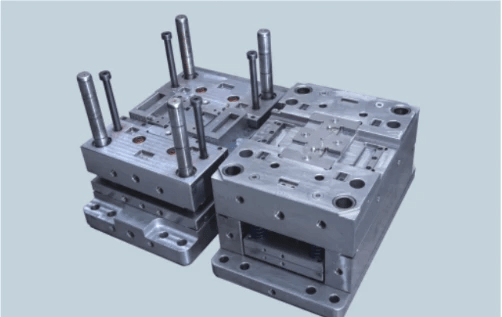
Industries That Rely on Die Casting
Die casting is predominantly favored in industries that require high-volume production of intricate metal parts. The automotive sector is a prime example, utilizing die casting for engine components, transmission cases, and other critical parts due to its ability to produce lightweight yet durable products. Additionally, the electronics industry often employs die cast components for housings and heat sinks, benefiting from the precision this method offers.
In sectors like aerospace and defense, die casting is equally valuable for creating complex geometries with tight tolerances—ensuring safety and reliability in critical applications. The question often arises: What is the difference between die cutting and injection molding? While both methods are used for shaping materials, die casting specifically refers to metal shaping under high pressure, unlike injection molding which typically involves plastics.
Industries That Rely on Injection Molding
Injection molding has carved out its niche in various sectors by providing flexibility and efficiency with plastic materials. The consumer goods industry heavily relies on this method for producing everything from toys to household items—benefiting from quick turnaround times and lower costs per unit when producing large quantities. Additionally, medical device manufacturers frequently use injection molding due to its capability of creating precise components that meet stringent regulatory standards.
Moreover, packaging companies utilize injection molding for creating containers and closures that are both functional and aesthetically appealing. A common inquiry among manufacturers is: What is the disadvantage of die casting? While it excels at precision metal parts, it may not be as cost-effective or versatile as injection molding when working with diverse materials or low-volume runs.
Case Study: Baoyuan’s Innovative Solutions
Baoyuan has emerged as a leader in providing innovative solutions through both die casting and injection molding techniques across multiple industries. By leveraging their expertise in Metal Injection Molding vs. Die Casting processes, they have successfully developed customized components tailored to client specifications while maintaining efficiency at scale.
For instance, Baoyuan's collaboration with an automotive manufacturer resulted in a series of lightweight yet robust engine parts produced via advanced die casting techniques—reducing weight without compromising strength or performance significantly. Their ability to adapt methodologies based on project requirements showcases why some companies might choose die casting over other methods; it's not just about what you produce but how effectively you can do so while meeting industry demands.
Conclusion
In the world of manufacturing, understanding the nuances of different methods is crucial for making informed decisions. In our exploration of die cast vs injection molding, we've uncovered their unique processes, materials, and applications. Ultimately, the choice between these two techniques can significantly impact both product quality and production efficiency.
Summary of Die Casting Advantages
Die casting offers several compelling advantages that make it a preferred choice in various industries. For starters, it provides exceptional dimensional accuracy and surface finish, which are essential for high-quality components. Additionally, die casting is ideal for producing complex shapes with thin walls and intricate details—something that sets it apart from traditional casting methods.
When considering what is the difference between casting and die casting, it's clear that die casting utilizes high-pressure techniques to create precise parts quickly. This method also allows for faster production rates compared to other manufacturing processes, making it an efficient option for large-scale production runs. However, one must also ponder what is the disadvantage of die casting; while it excels in precision and speed, initial tooling costs can be high.
Insights on Injection Molding Benefits
This method can accommodate a wide range of thermoplastics and thermosetting polymers, allowing manufacturers to tailor products to specific requirements easily. Moreover, injection molding tends to have lower per-unit costs for larger production runs due to its efficiency in mass-producing identical parts.
When discussing metal injection molding vs. die casting, it's important to note that while metal injection molding allows for intricate designs in metal parts at lower volumes than die casting typically offers—each process has its specialized applications where they excel best. Injection molding also provides excellent repeatability in production quality over time—a significant advantage when consistency is key in manufacturing environments.
Making the Right Choice for Your Project
Choosing between die cast vs injection molding ultimately depends on your project's specific needs—including material properties required and design complexity desired. If you prioritize precision with metals or need robust components capable of withstanding significant stress or wear-and-tear conditions, then die casting might be your go-to method. Conversely, if you're looking at plastic components that require flexibility in design or rapid prototyping capabilities without breaking the bank on tooling costs—then injection molding could be your best bet.
Before deciding which technique aligns best with your project goals—consider factors like cost implications over time (not just upfront), required tolerances, material availability—and don’t forget about potential future scalability! By weighing these elements carefully against each other while keeping an eye on industry trends—you'll find yourself well-equipped to navigate this intricate landscape successfully.