Introduction

When it comes to injection molding, short shots are a common issue that can impact product quality and production efficiency. Understanding the causes and solutions for short shots is crucial for any plastic production operation. Detecting and correcting short shots is essential to ensure the highest quality of plastic products.
Understanding Short Shots in Injection Molding
Short shots in injection molding occur when the mold cavity is not completely filled during the injection process, resulting in incomplete or undersized parts. This defect can lead to product rejections and increased production costs. One common cause of short shots is inadequate injection pressure, which may not be sufficient to fill the mold cavity completely. Another cause could be a lack of proper venting in the mold, leading to air traps that prevent the material from flowing freely and filling the cavity. Additionally, improper temperature control of the molten material can also result in short shots, as variations in temperature can affect flow consistency and lead to incomplete filling of the mold cavity. These factors must be carefully monitored and adjusted to prevent short shots and ensure high-quality production outcomes.
Common Causes of Short Shots
Several factors can contribute to short shots in injection molding, including improper mold design, inadequate material flow, and temperature variations. Identifying these root causes is essential for effectively addressing short shot defects.
In addition to mold design, material flow, and temperature variations, other factors such as inadequate injection pressure and insufficient cooling time can also contribute to short shots in injection molding. Insufficient injection pressure can result in incomplete filling of the mold cavity, leading to short shots. Similarly, inadequate cooling time can cause premature ejection of the part before it is fully formed, resulting in a short shot defect. Therefore, thorough analysis of all potential factors is crucial for identifying and addressing the root causes of short shots in injection molding processes.
Importance of Detecting and Correcting Short Shots
Detecting and correcting short shots is vital for maintaining product quality and meeting customer requirements. Implementing effective problem-solving strategies can help prevent the occurrence of short shots and optimize production processes. Short shots in injection molding occur when the mold does not completely fill with molten plastic, resulting in incomplete or undersized parts. This can lead to product defects, increased scrap rates, and ultimately higher production costs if not addressed promptly. By detecting short shots early and implementing corrective measures, manufacturers can minimize waste and ensure consistent product quality, ultimately enhancing customer satisfaction.
What are Short Shots in Injection Molding?
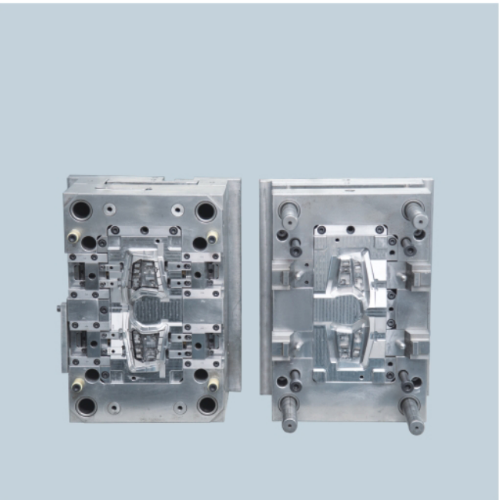
Definition and Impact of Short Shots
Short shots in injection molding occur when the mold cavity is not completely filled during the injection process, resulting in incomplete parts. This defect can lead to product malfunction and increased production costs due to rework or scrap. Baoyuan's expertise in short shot analysis allows for quick identification and resolution of this issue.
Short shots can result from a variety of factors, including inadequate injection pressure, poor mold design, or incorrect material temperature. Baoyuan's team of experienced engineers and technicians are well-versed in identifying these root causes and implementing effective solutions to prevent short shots from occurring in the future. By addressing the underlying issues, Baoyuan helps clients avoid the costly consequences of short shots and ensures the production of high-quality parts.
Baoyuan's Expertise in Short Shot Analysis
With a team of senior management and technical personnel experienced in mold design, mold opening, and injection molding, Baoyuan is well-equipped to analyze short shots in plastic injection molding. Their proficiency in identifying root causes and implementing problem-solving strategies ensures efficient resolution of short shot defects.
How Short Shots Affect Product Quality
Short shots can significantly impact product quality by causing defects such as voids, sinks, or warpage. Baoyuan's extensive experience in production and quality assurance of single-color and double-color plastic products enables them to understand the detrimental effects of short shots on product performance and appearance.
Causes of Short Shots in Injection Molding
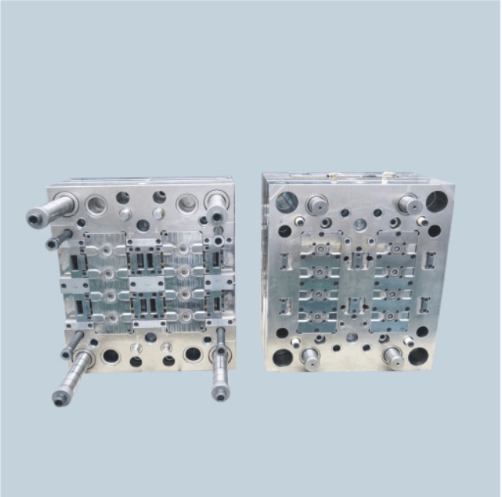
Factors Contributing to Short Shots
Short shots in injection molding can be caused by various factors such as inadequate injection pressure, improper material temperature, or insufficient mold filling. These issues can lead to incomplete part formation and affect the overall product quality.
In addition to injection pressure, material temperature, and mold filling, other factors that can contribute to short shots in injection molding include the quality of the raw materials used, the design of the mold, and the speed at which the injection process is carried out. The raw materials must be free from contaminants and properly mixed to ensure uniformity in the final product. Furthermore, a well-designed mold with proper venting and cooling channels is essential for achieving complete part formation. Additionally, controlling the speed of injection is crucial to prevent premature cooling and ensure that the material fills all areas of the mold before solidifying.
Baoyuan's Insights on Identifying Root Causes
The Baoyuan team's expertise lies in identifying the root causes of short shots in injection molding. With years of experience and technical knowledge, they can pinpoint the specific factors contributing to short shots and develop effective solutions for their clients. One key area that the team focuses on is the impact of mold design on short shot occurrence. The intricacies of mold design can have a significant influence on the quality and consistency of injection molded products. Factors such as gate placement, venting, and cooling channels all play a role in determining whether short shots occur.
Effects of Mold Design on Short Shot Occurrence
Mold design plays a critical role in the occurrence of short shots in injection molding. Poorly designed molds can result in uneven material distribution and air traps, leading to short shot defects. Baoyuan's skilled technical personnel are proficient in mold design and can address these issues effectively.
Additionally, the use of proper cooling channels and vents in mold design is crucial for preventing short shots. Inadequate cooling can lead to premature solidification of the material, resulting in incomplete filling of the mold cavity. Baoyuan's technical team understands the importance of optimizing cooling systems within the mold to ensure uniform material flow and minimize the risk of short shot defects.
Detecting Short Shots in Injection Molding
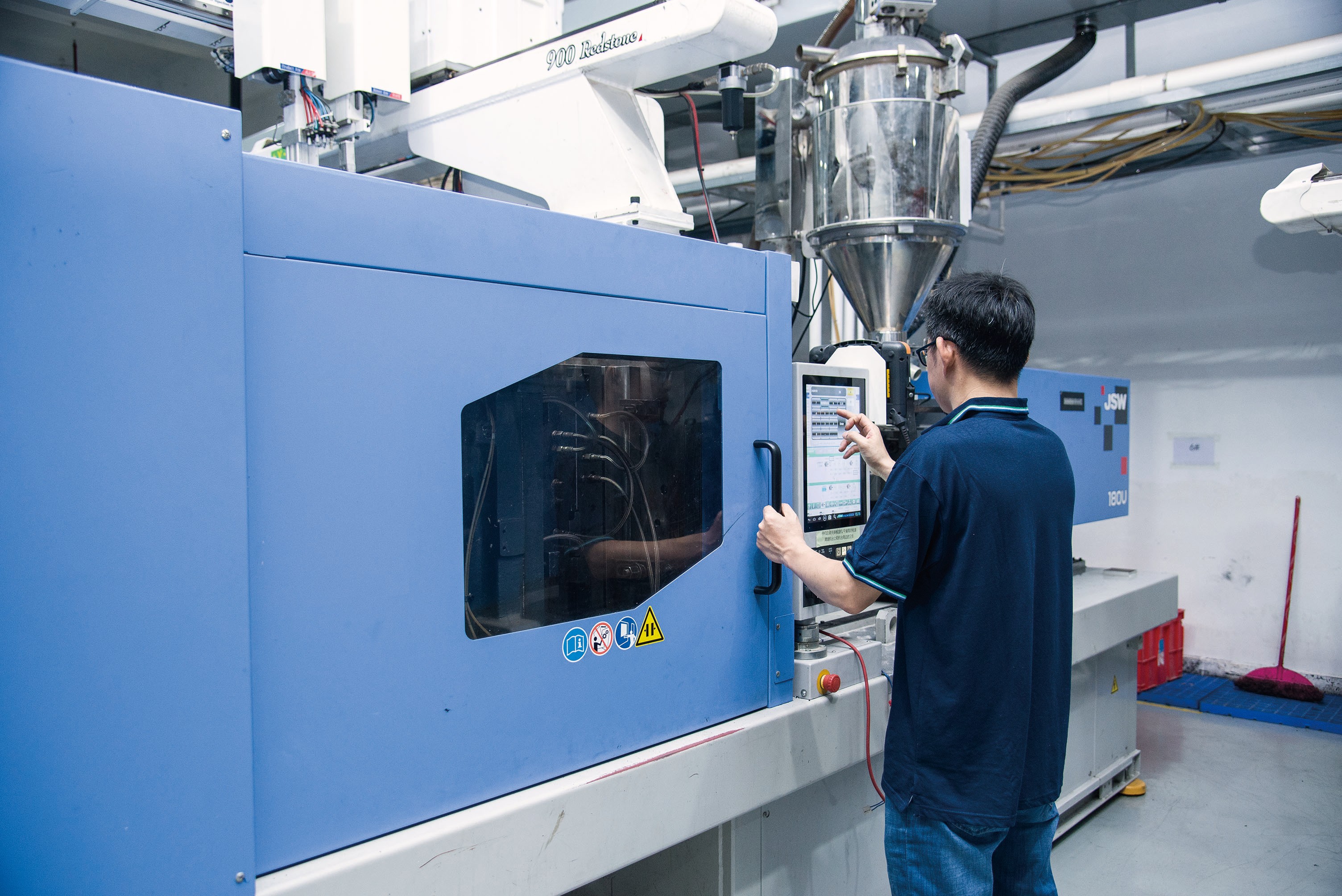
When it comes to detecting short shots in injection molding, Baoyuan utilizes advanced detection methods to ensure quality control. By employing state-of-the-art technology and inspection processes, the Baoyuan team is able to identify potential short shot defects with precision and accuracy.
Baoyuan's Advanced Detection Methods
Baoyuan's advanced detection methods include real-time monitoring of the injection molding process, utilizing high-tech sensors and monitoring equipment to detect any signs of short shots as they occur. This proactive approach allows for immediate intervention and correction, minimizing the impact of short shot defects on product quality. Real-time monitoring also enables Baoyuan to gather valuable data on the injection molding process, which can be used for continuous improvement and optimization. By staying ahead of potential issues through real-time monitoring, Baoyuan can ensure consistent quality and efficiency in their production processes.
Importance of Real-time Monitoring
Real-time monitoring is crucial in detecting short shots in injection molding, as it enables quick response to any issues that may arise during the production process. By continuously monitoring key parameters such as pressure, temperature, and fill rate, Baoyuan ensures that any potential short shot defects are promptly identified and addressed.
Real-time monitoring also allows Baoyuan to make immediate adjustments to the injection molding process, ensuring that the production of short shots is minimized. This proactive approach helps to maintain high product quality and reduces the need for rework or scrap, ultimately saving time and resources. By staying vigilant through real-time monitoring, Baoyuan can uphold its reputation for delivering exceptional products to its customers.
Quality Control Measures for Short Shot Identification
In addition to real-time monitoring, Baoyuan implements stringent quality control measures specifically designed for short shot identification. Through meticulous inspection protocols and rigorous testing procedures, the team is able to pinpoint the root causes of short shots and take corrective action to prevent their occurrence.
Furthermore, Baoyuan's quality control measures include regular equipment maintenance and calibration to ensure optimal performance and accuracy in identifying short shots. By investing in state-of-the-art technology and training their staff on the latest industry standards, Baoyuan stays ahead of the curve in detecting and resolving short shot issues. This proactive approach not only minimizes production downtime but also enhances overall product quality, giving clients peace of mind.
With Baoyuan's expertise in advanced detection methods and real-time monitoring capabilities, you can rest assured that your plastic production will be free from the detrimental effects of short shot defects.
Correcting Short Shots in Injection Molding
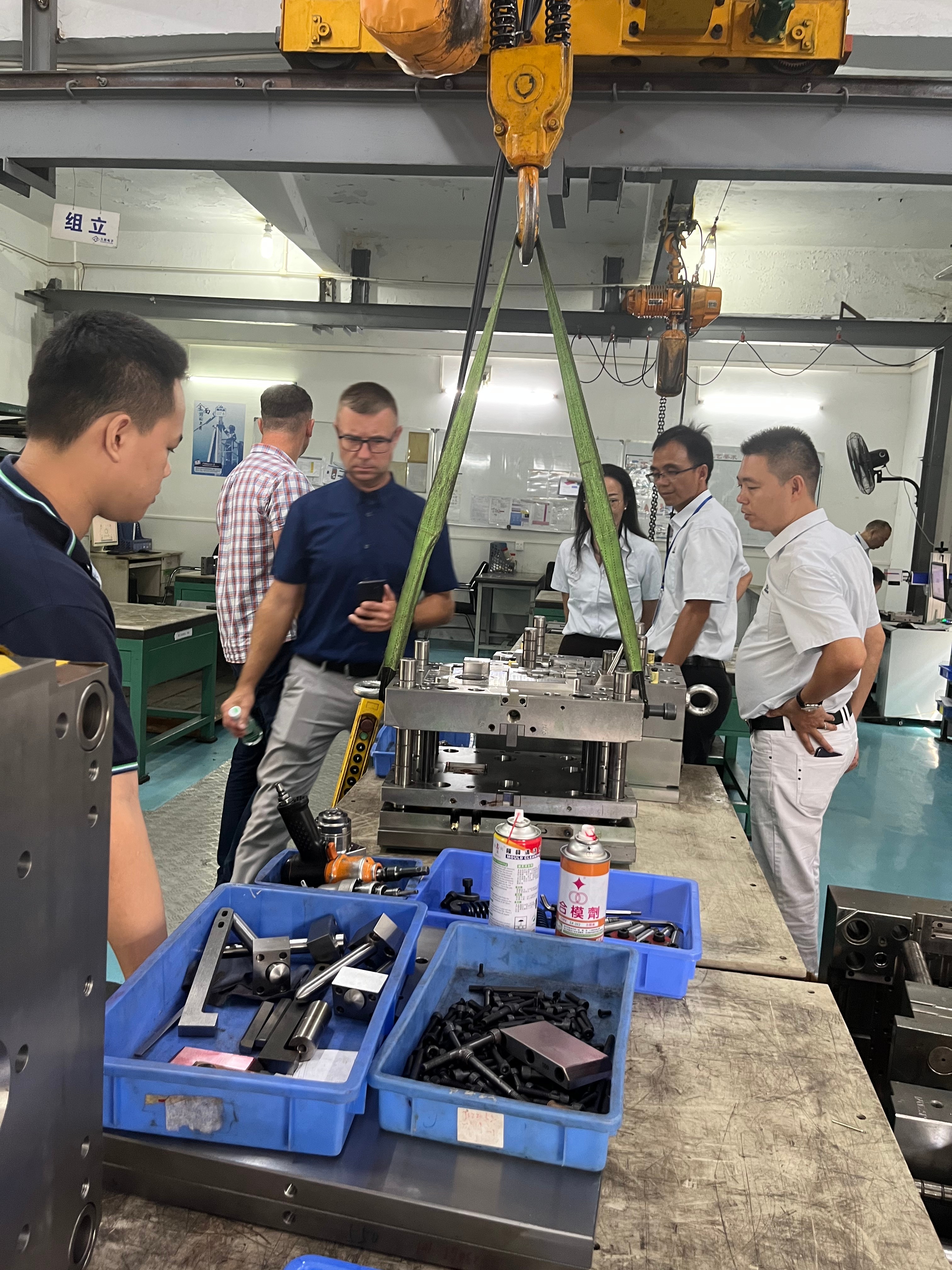
As a leading expert in injection molding, Baoyuan has developed problem-solving strategies to address short shot defects. By utilizing advanced software for mold design and injection molding, the Baoyuan team can effectively identify and resolve the root causes of short shots in plastic production. Their extensive experience in troubleshooting short shots enables them to provide efficient and practical solutions for improving product quality.
Baoyuan's Problem-solving Strategies
Baoyuan's problem-solving strategies for short shot defects involve a comprehensive analysis of the injection molding process, including mold design, material selection, and machine settings. By leveraging their technical expertise and industry experience, the Baoyuan team can quickly identify the underlying issues causing short shots and develop targeted solutions to rectify the defects. Their proactive approach ensures that production downtime is minimized while achieving optimal product quality.
Furthermore, Baoyuan's problem-solving strategies involve conducting thorough testing and analysis to validate the effectiveness of their solutions. By utilizing advanced simulation software and real-world testing, the team can ensure that the implemented changes will effectively address the short shot defects. This commitment to validation and verification guarantees that the solutions are not only quick but also reliable, leading to long-term improvements in production efficiency and product quality.
Techniques for Resolving Short Shot Defects
In addressing short shot defects, Baoyuan employs a range of techniques tailored to the specific requirements of each injection molding project. These techniques may include adjusting injection parameters, optimizing cooling processes, or modifying mold designs to improve material flow and distribution. By implementing these proven techniques, Baoyuan can effectively resolve short shot defects and enhance overall production efficiency.
In addition to the aforementioned techniques, Baoyuan also leverages advanced simulation software to analyze and optimize the filling and packing phases of the injection molding process. This allows for precise adjustments to be made in order to prevent short shot defects from occurring. Furthermore, Baoyuan's team of experienced engineers continuously monitors and evaluates production processes to identify potential areas for improvement, ensuring that short shot defects are proactively addressed before they impact production.
Baoyuan's Experience in Troubleshooting Short Shots
With years of experience in plastic production and quality assurance, the Baoyuan team has amassed invaluable insights into troubleshooting short shots in injection molding. Their hands-on experience with single-color and double-color plastic products enables them to anticipate potential issues and implement preventive measures to avoid short shot defects altogether. By leveraging their expertise, Baoyuan consistently delivers high-quality solutions for common injection molding defects.
Furthermore, Baoyuan's team is adept at identifying the root causes of short shots, whether it be due to material issues, mold design flaws, or machine malfunctions. Their thorough understanding of the injection molding process allows them to pinpoint potential areas of concern and take proactive steps to address them before they escalate into production delays or defective products. This proactive approach not only saves time and resources but also ensures that clients receive consistently high-quality plastic products.
Remember that it's essential to address both the causes & solutions for common injection molding defects like short shots to ensure smooth production processes and superior product quality.
Conclusion
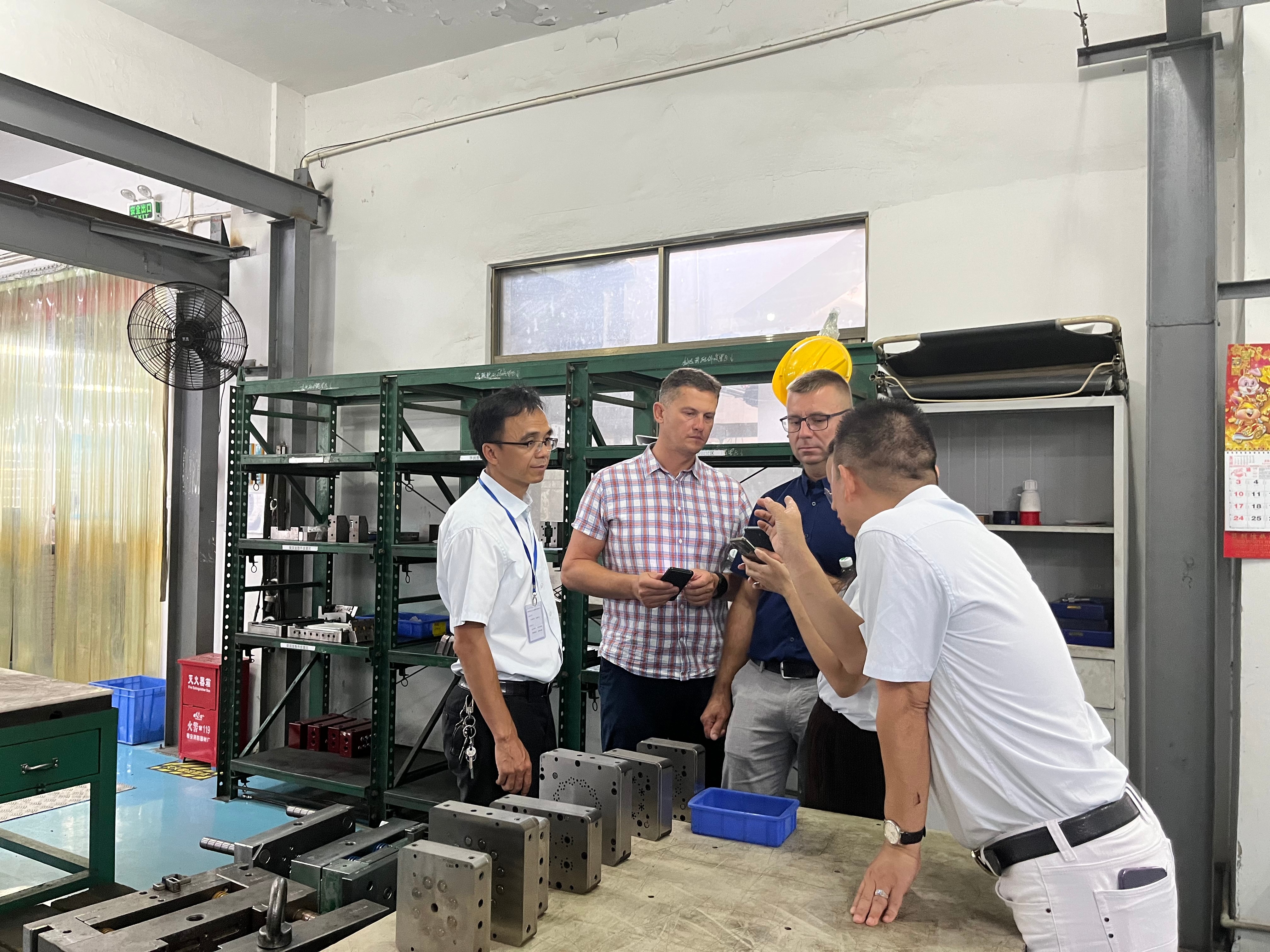
Baoyuan's Proven Solutions for Short Shots
Baoyuan's team of seasoned professionals brings years of industry experience to the table, offering expert solutions for short shots in injection molding. With their proficiency in mold design and injection molding, they have successfully tackled short shot issues, ensuring high-quality plastic products for their clients.
How to Avoid Short Shots in Your Production
To prevent short shots in your plastic production, it is essential to address common causes such as mold design flaws and inadequate monitoring. Baoyuan recommends implementing real-time monitoring and quality control measures to catch potential short shot defects early on, saving time and resources in the long run.
Quality Assurance in Injection Molding
Quality assurance is paramount in injection molding to ensure that short shot defects are minimized. Baoyuan's expertise lies not only in troubleshooting short shots but also in implementing quality control measures to guarantee the production of flawless plastic products. By prioritizing quality assurance, manufacturers can avoid costly rework and maintain customer satisfaction.