Introduction
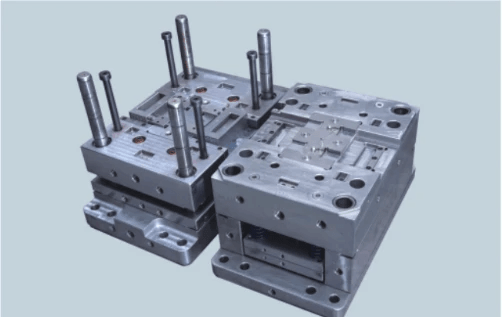
Injection molding is a widely used manufacturing process, but it’s not without its quirks. One of the most perplexing issues that can arise is known as jetting injection molding. Understanding jetting injection molding issues is crucial for manufacturers looking to produce high-quality products efficiently.
Understanding Jetting Injection Molding Issues
So, what is the cause of jetting? At its core, jetting occurs when molten plastic flows too quickly into a mold cavity, leading to uneven filling and surface defects. This phenomenon can compromise the integrity and appearance of the final product, making it essential to grasp the underlying mechanics behind this issue.
Importance of Recognizing Common Mistakes
Recognizing common mistakes in the injection molding process is vital for avoiding costly errors down the line. Many manufacturers overlook factors such as injection speed and temperature control, which can significantly contribute to jetting problems. By being aware of these pitfalls, you can proactively address them and improve your overall production quality.
Overview of Solutions to Jetting Problems
How to avoid jetting in injection molding? The good news is that there are several effective strategies available! From optimizing injection speeds to selecting suitable materials and maintaining temperature control, understanding how to fix flow lines in injection molding can help mitigate these issues and lead you toward flawless production outcomes.
What Causes Jetting in Injection Molding
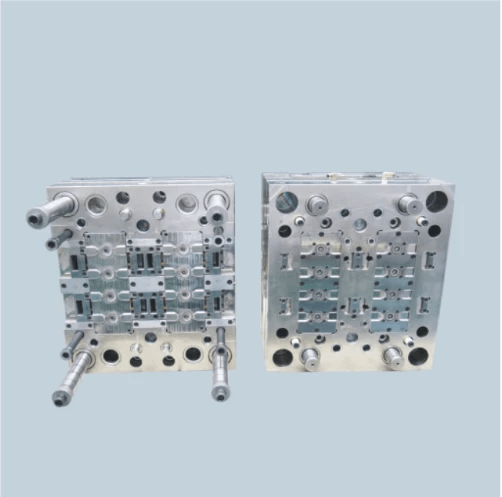
Understanding what causes jetting in injection molding is crucial for manufacturers looking to enhance product quality and minimize defects. Jetting occurs when molten plastic flows unevenly into the mold, leading to unsightly flow lines and compromised structural integrity. By delving into the science behind jetting, common scenarios where it occurs, and key factors influencing its formation, we can better grasp how to avoid jetting in injection molding.
The Science Behind Jetting
At its core, the jetting effect is a phenomenon caused by rapid injection of molten plastic into a cold mold cavity. When the speed of injection exceeds a certain threshold, the material can form a jet that penetrates ahead of the surrounding flow front. This creates turbulence and results in inconsistent filling patterns, which are often manifested as visible flow lines on finished products—an unsightly reminder of what happens when things go awry.
Common Scenarios for Jetting Occurrence
Jetting tends to rear its ugly head in specific situations during the injection molding process. For instance, it frequently occurs when injecting low-viscosity materials at high speeds or when using molds with intricate geometries that impede smooth flow paths. Additionally, environmental factors such as ambient temperature and humidity can exacerbate jetting issues—making it essential for manufacturers to be vigilant about their conditions while producing parts.
Key Factors in Jetting Formation
Several key factors contribute to the formation of jetting during injection molding processes. One major contributor is inadequate temperature control; if the mold is too cold or if the melt temperature is too low, it can lead to premature solidification of material before it fills all areas of the cavity effectively. Other factors include improper gate design or placement that disrupts material flow and insufficient packing pressure that fails to ensure complete cavity fill—each element playing a critical role in whether or not you’ll encounter those pesky flow lines.
How to Avoid Jetting in Injection Molding
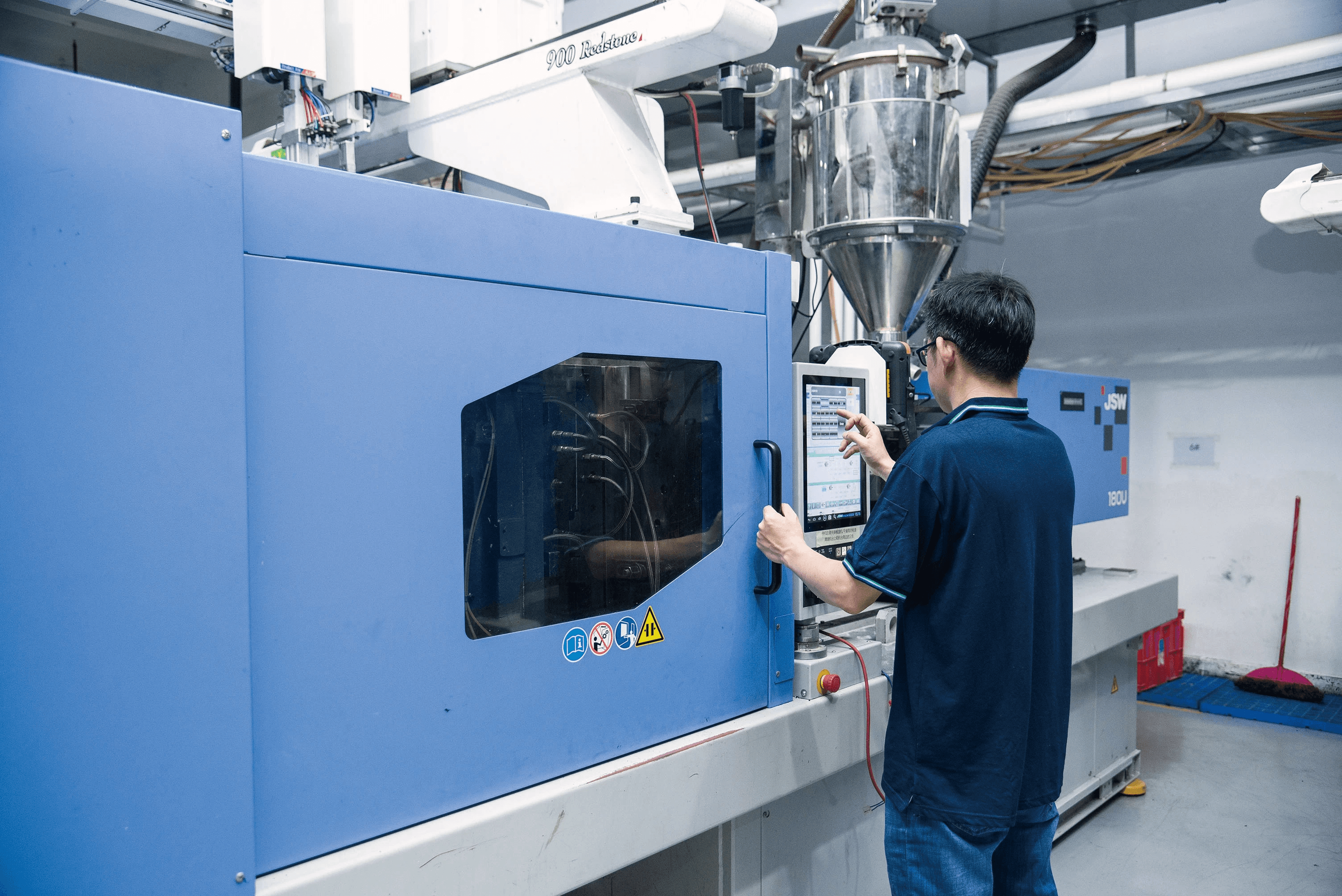
When it comes to jetting injection molding, prevention is key. By understanding the factors that contribute to this issue, manufacturers can take proactive steps to minimize its occurrence. In this section, we’ll explore strategies for optimizing injection speed, controlling temperature, and selecting the right materials—all aimed at answering the question: How to avoid jetting?
Optimizing Injection Speed
One of the primary culprits behind jetting is improper injection speed. If the speed is too high, it can lead to turbulent flow and result in air entrapment—what we often refer to as jetting. Therefore, finding that sweet spot in injection speed is crucial; not too fast and not too slow—just right for a smooth fill without causing chaos inside the mold.
Adjusting your machine settings based on trial runs can help establish an optimal injection speed tailored for your specific material and part design. Regularly monitoring flow rates during production will also aid in identifying any deviations that could lead to jetting issues down the line. Ultimately, by carefully calibrating injection speeds, you’re one step closer to preventing those pesky flow lines.
Temperature Control Strategies
Temperature plays a vital role in determining how materials behave during the injection molding process, making it essential for avoiding jetting problems. The question What causes jetting in injection molding? often leads back to inadequate temperature control—especially when resin temperatures are either too low or too high. Maintaining consistent melt temperatures ensures that materials flow smoothly into molds without creating voids or air pockets.
Implementing effective temperature control strategies involves careful monitoring of both barrel and mold temperatures throughout production runs. Using thermal imaging tools can provide real-time insights into temperature fluctuations that could contribute to jetting effects. Remember: a well-regulated temperature not only helps avoid jetting but also enhances overall product quality.
Material Selection Considerations
The choice of material significantly influences whether you’ll encounter issues like jetting during production runs; thus, selecting suitable materials is paramount when considering how to avoid jetting in injection molding processes. Some resins are inherently more prone to creating air pockets due to their viscosity or molecular structure—making them less ideal for specific applications where precision is key.
Conducting thorough research on various materials’ properties before starting a project can save time and resources later on by reducing potential complications associated with poor material choices. Additionally, consulting with suppliers about alternative formulations designed specifically for low-jetting scenarios could yield beneficial results as well! Ultimately, making informed decisions about material selection will pave the way toward smoother operations and higher-quality outputs.
The Jetting Effect and Its Implications
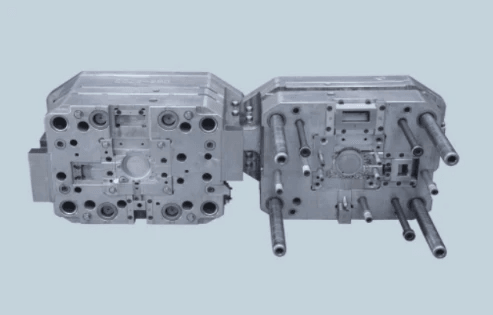
Jetting in injection molding can significantly affect the overall quality of the final product, leading to defects that may compromise functionality and aesthetics. Understanding how jetting injection molding manifests can help manufacturers take proactive measures to mitigate its impact. By recognizing the implications of jetting, businesses can prioritize quality assurance and maintain their reputation in the competitive market.
How Jetting Impacts Product Quality
The jetting effect often results in flow lines and surface imperfections that detract from product quality. When jetting occurs, it creates uneven material distribution, which can weaken structural integrity and lead to premature failure during use. Moreover, products with noticeable jetting issues may not meet customer expectations, resulting in increased returns and diminished brand loyalty.
Visual Indicators of Jetting Issues
Identifying visual indicators of jetting issues is crucial for timely intervention in injection molding processes. Common signs include streaks or lines on the surface of molded parts that are indicative of improper material flow during production. If you notice these imperfections consistently across a batch, it’s time to ask yourself: what is the cause of jetting? Addressing these visual cues early can prevent further complications down the line.
Long-term Consequences of Ignoring Jetting
Ignoring jetting problems can lead to severe long-term consequences for manufacturers. Over time, continued production without addressing these issues may result in a tarnished reputation as customers receive subpar products that fail to perform as expected. Additionally, persistent jetting could lead to increased production costs due to waste and rework—definitely not a recipe for success when considering how to avoid jetting in injection molding.
How to Fix Flow Lines in Injection Molding
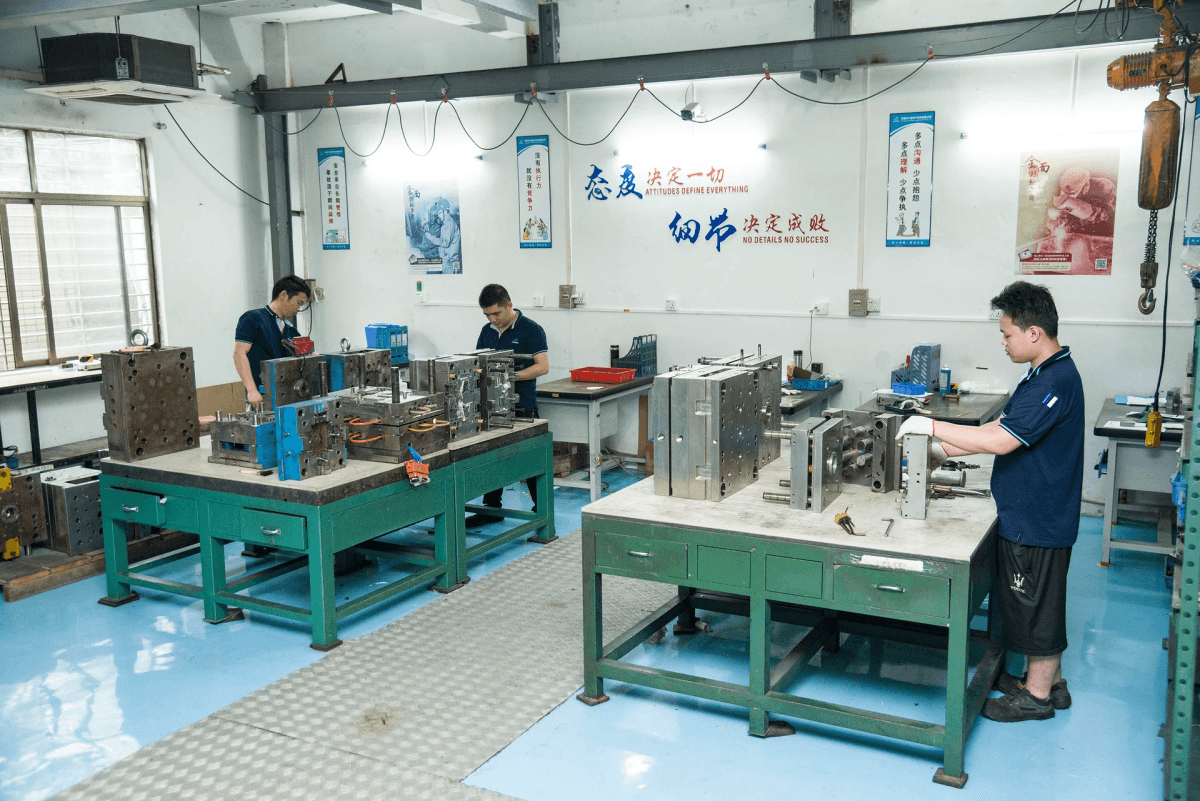
Flow lines can be a pesky problem in jetting injection molding, and addressing them effectively is crucial for maintaining product quality. Identifying these imperfections early on can save time, resources, and frustration down the line. So, let’s dive into how to fix flow lines in injection molding and ensure your products are up to snuff.
Identifying Flow Lines in Your Products
The first step in fixing flow lines is recognizing what they look like on your products. Flow lines typically present as streaks or patterns that run along the surface of molded parts, often caused by inconsistent material flow during injection molding. To spot these flaws, conduct a thorough visual inspection under good lighting; this will help you determine the extent of the jetting effect and how it impacts your final product.
To make identification even easier, consider using a light source at different angles to highlight any imperfections that may not be immediately visible. Pay attention to areas where materials converge or where there might be changes in thickness—these are prime spots for jetting issues. Once you’ve pinpointed flow lines, you’ll be better equipped to tackle them effectively.
Techniques for Remedial Action
Once you've identified the flow lines, it’s time for some remedial action! One effective technique is adjusting the injection speed; reducing it can help ensure a more uniform material flow and minimize instances of jetting injection molding. Additionally, tweaking the temperature settings of both the mold and material can also yield positive results—higher temperatures often improve fluidity but may exacerbate other issues if not managed carefully.
Another approach involves modifying gate locations or sizes; strategically placing gates can help direct material flow more evenly throughout the mold cavity. If you're still seeing those pesky flow lines after making adjustments, consider switching materials altogether; some resins are less prone to jetting than others due to their viscosity characteristics. Remember: experimentation is key when figuring out how to avoid jetting in injection molding!
Best Practices for Prevention
Prevention is always better than cure! To keep those annoying flow lines at bay from the get-go, start with proper mold design—ensure that your molds facilitate smooth material entry without abrupt changes that could disrupt flow patterns. Regular maintenance checks on your equipment also play a vital role; worn-out components can lead to inconsistencies that contribute to jetting problems.
Educate your team about what causes jetting in injection molding so they’re aware of potential pitfalls during production runs. Consider implementing simulation software during design phases; this allows you to visualize potential issues before they happen and devise strategies accordingly! By adopting these best practices early on, you'll create an environment conducive to flawless production while minimizing any risk associated with unwanted defects.
Lessons from the Baoyuan Team
When it comes to tackling jetting injection molding issues, the Baoyuan team stands out for their innovative approach and deep understanding of mold design principles. Their expertise has allowed them to identify and rectify common pitfalls in the injection molding process, ensuring that manufacturers can produce high-quality products without the dreaded jetting effect. By sharing their knowledge and experiences, they provide invaluable insights into how to avoid jetting in injection molding.
Baoyuan’s Expertise in Mold Design
Baoyuan's mold design expertise is rooted in a thorough understanding of what causes jetting in injection molding. They focus on creating molds that optimize flow rates and minimize turbulence, which are critical factors in preventing jetting. With years of experience under their belt, they have developed techniques that not only address existing problems but also proactively prevent future occurrences.
Their team utilizes advanced simulation software to predict potential jetting issues before production begins. This forward-thinking approach allows them to make necessary adjustments during the design phase, ensuring a smoother manufacturing process down the line. Ultimately, Baoyuan’s commitment to excellence means fewer headaches for manufacturers dealing with flow lines or other defects related to jetting.
Case Studies of Successful Fixes
The Baoyuan team's portfolio includes numerous case studies where they successfully tackled jetting problems head-on. For instance, one notable project involved a client facing significant quality control issues due to persistent flow lines caused by improper injection speed settings. By implementing tailored adjustments and optimizing parameters based on specific material characteristics, Baoyuan was able to eliminate these defects entirely.
Another case study highlights how Baoyuan collaborated with a client struggling with temperature inconsistencies that contributed to the formation of jetting effects during production runs. Through meticulous analysis and strategic modifications in both mold design and processing conditions, they achieved remarkable improvements in product quality while reducing waste significantly. These examples illustrate not just what is the cause of jetting but also how targeted interventions can lead to tangible results.
Collaborating for Quality Assurance
Collaboration is at the heart of Baoyuan's strategy for combating challenges like flow lines and other issues associated with jetting injection molding. They believe that open communication with clients fosters an environment where innovative solutions can thrive—after all, who knows your products better than you? By working closely together throughout the entire production process, from initial design through final testing stages, both parties can ensure that every aspect aligns perfectly.
Baoyuan also emphasizes ongoing training for their team members as part of their commitment to quality assurance practices. This continuous learning helps them stay ahead of emerging trends and technologies within the industry related to how to fix flow lines in injection molding effectively. The result? A more robust partnership dedicated not only to solving existing problems but also preventing new ones from arising.
In summary, lessons learned from the Baoyuan team underscore the importance of expertise in mold design and collaborative efforts aimed at achieving quality assurance within injection molding processes plagued by challenges like jetting effects or flow lines.
Conclusion
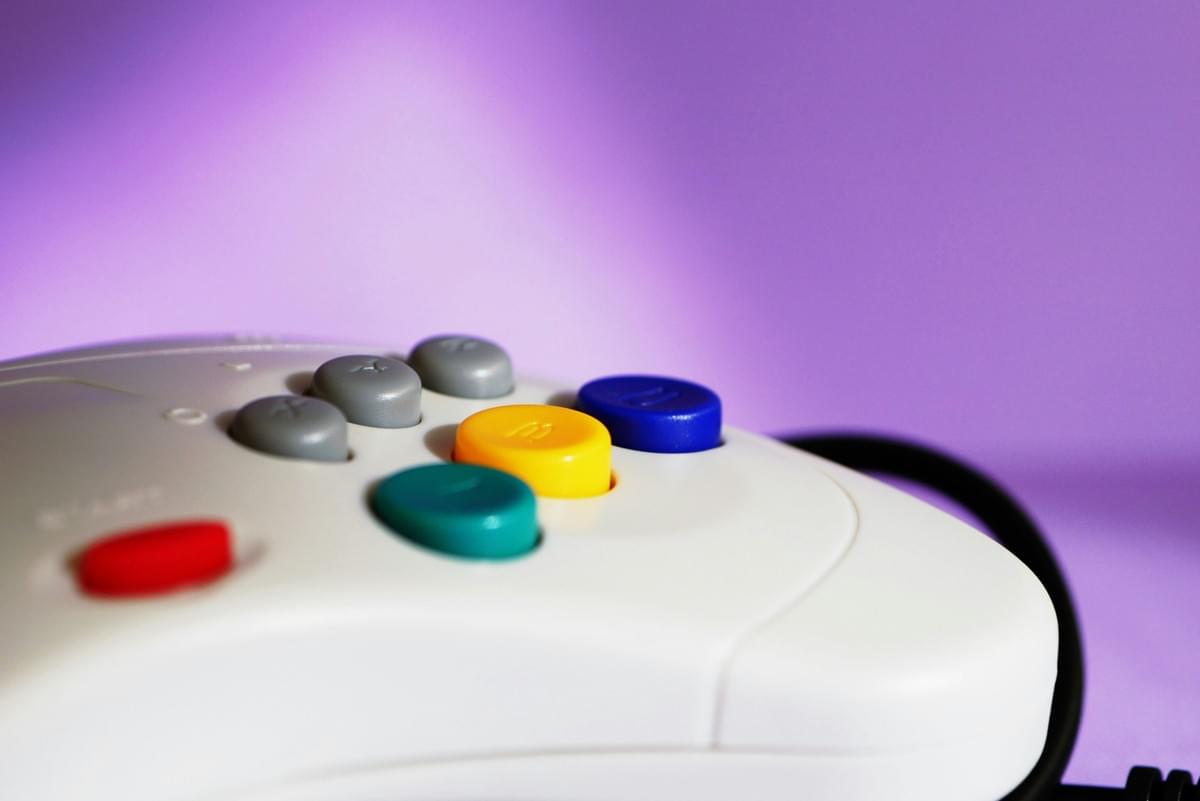
In the world of injection molding, jetting is a challenge that can’t be ignored. Understanding what causes jetting in injection molding is essential for manufacturers who strive for high-quality products. By recognizing the implications of this phenomenon, industry professionals can take proactive steps to avoid pitfalls and enhance production efficiency.
Recap of Jetting Injection Molding Challenges
Jetting occurs when molten plastic moves too quickly, leading to air entrapment and unsightly flow lines. What is the cause of jetting? It often stems from factors like rapid injection speeds, improper temperature settings, and material choices that don’t align with specific project requirements. Ignoring these challenges can result in compromised product quality and increased costs due to rework or waste.
Future Steps for Effective Solutions
To tackle jetting effectively, manufacturers must focus on how to avoid jetting in injection molding processes through careful planning and execution. Future steps include optimizing parameters such as injection speed, temperature control strategies, and selecting appropriate materials tailored to each application’s needs. Additionally, investing in training for staff about what causes jetting in injection molding will empower teams to identify issues early on.
The Path to Flawless Injection Molding Products
Achieving flawless products requires a commitment to understanding the jetting effect and its implications on quality control. Manufacturers should also implement best practices for how to fix flow lines in injection molding when they do occur—promptly addressing issues minimizes long-term consequences that could harm reputation or profitability. With a collaborative approach among teams like Baoyuan’s expertise in mold design, companies can pave their way toward producing top-notch injection molded products that meet customer expectations.