Introduction
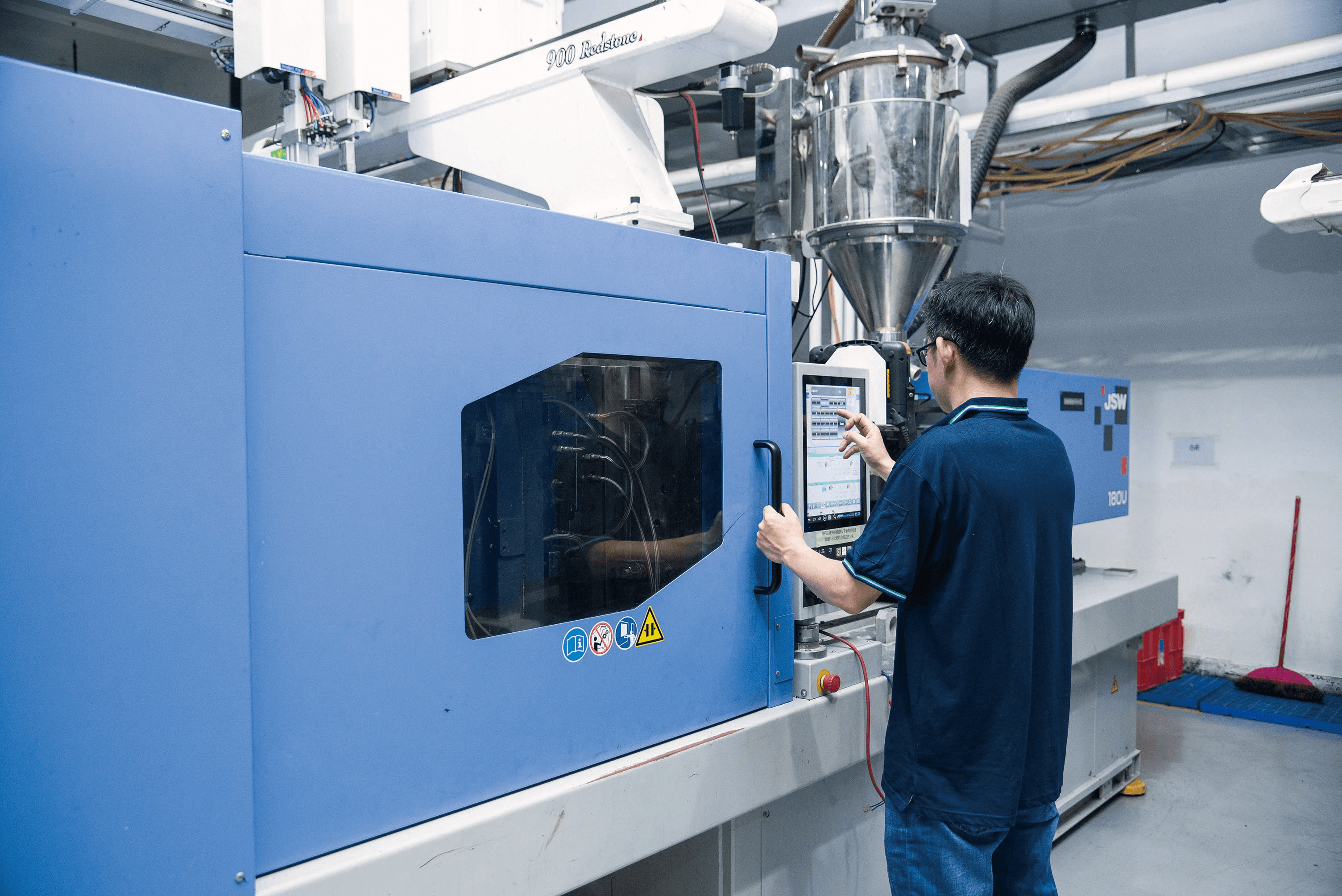
In the world of manufacturing, the injection molding hopper plays a crucial role in shaping the final product. Understanding what a hopper in injection molding is can significantly enhance your grasp of the entire process. This introduction will explore key components of injection molding and highlight common challenges faced with hoppers.
Understanding the Injection Molding Hopper
The injection molding hopper is essentially the gateway for raw materials into the molding machine, serving as a storage unit that feeds plastic pellets or granules into the barrel for processing. It’s important to recognize that this component not only holds materials but also influences how efficiently they are processed. With various designs tailored for different applications, understanding what is a hopper in injection molding can help streamline production and improve overall efficiency.
Key Components of Injection Molding
Injection molding involves several key components working together harmoniously, among which the hopper stands out due to its foundational role. The barrel, screw, and nozzle are equally essential, each contributing to transforming raw plastic into finished products. By comprehending these components' functions—especially what is the function of the barrel in injection molding—you can better appreciate how they interact to produce high-quality items.
Common Challenges with Hoppers
Despite their importance, hoppers often face challenges that can disrupt production lines and lead to inefficiencies. Common issues include jamming and blockages that hinder material flow or temperature regulation problems affecting processing conditions. Knowing these challenges helps manufacturers devise strategies for improvement while also raising questions like what is the difference between hopper dryer and dehumidifier?, which can further impact material quality during processing.
What is a Hopper in Injection Molding?
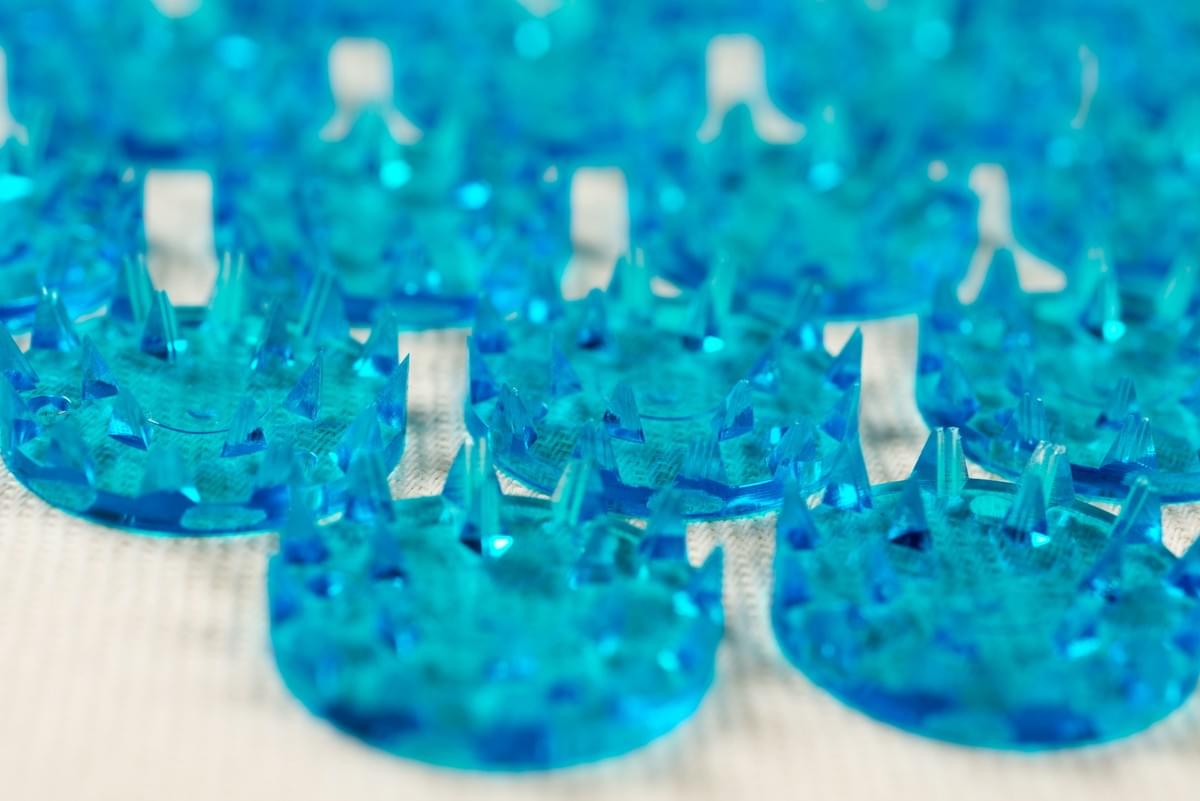
In the world of injection molding, the hopper plays a crucial role in ensuring that raw materials are efficiently fed into the system. This component serves as a storage unit for plastic pellets or granules before they enter the barrel for processing. Understanding what a hopper is in injection molding is essential for anyone involved in manufacturing processes that rely on this technology.
Definition and Overview
An injection molding hopper is essentially a funnel-shaped container that holds the raw material used in the molding process. It feeds these materials into the barrel, where they are heated and melted before being injected into molds to form various products. The design of the hopper allows for gravity-assisted flow, ensuring a steady supply of material to maintain consistent production rates.
Importance in the Molding Process
The importance of an injection molding hopper cannot be overstated; it acts as the gateway for materials entering the system. A well-functioning hopper ensures that there are no interruptions during production, which can lead to defects or inconsistencies in product quality. Moreover, it helps maintain optimal material temperatures, which is crucial for achieving desired physical properties in molded parts.
Different Types of Hoppers
There are several types of hoppers used in injection molding, each designed with specific applications and materials in mind. For instance, some hoppers come equipped with heating elements to keep moisture-sensitive materials dry—this leads us to consider what is the work of a hopper dryer? Other hoppers may feature agitators or vibrators to ensure uniform material flow and prevent clumping or jamming issues during operation. Understanding these variations can help manufacturers choose the right type of hopper based on their unique production requirements.
What is the Function of the Barrel in Injection Molding?
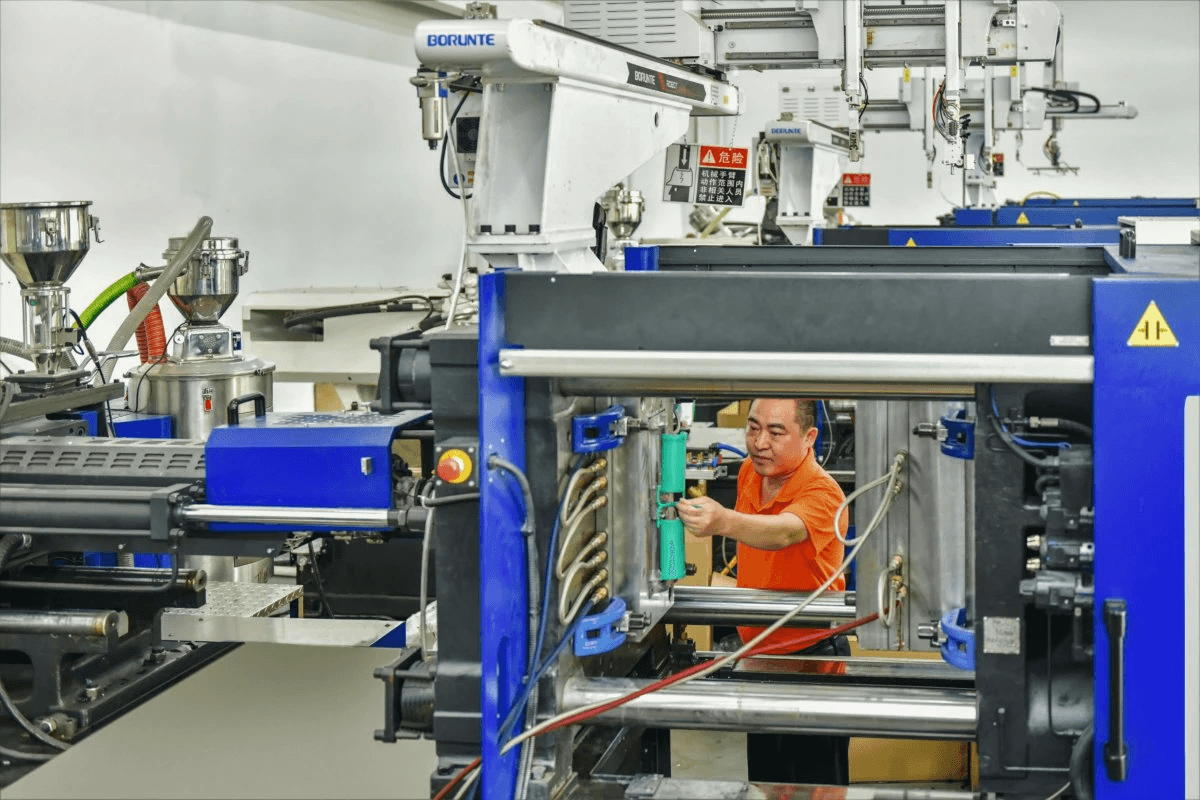
The barrel is a critical component in the injection molding process, serving as a conduit for material transformation and delivery. It works hand-in-hand with the injection molding hopper to ensure that raw materials are efficiently melted and injected into molds. Understanding what is the function of the barrel in injection molding can illuminate its vital role in producing high-quality plastic parts.
Role of the Barrel in Processing
The barrel's primary role is to provide a controlled environment where plastic pellets are heated, melted, and mixed thoroughly before being injected into molds. This heating process ensures that materials reach their optimal viscosity for smooth flow during injection. Without an efficient barrel, even the best-designed injection molding hopper would struggle to deliver consistent results.
Moreover, temperature control within the barrel is crucial; it helps maintain uniform melting while preventing degradation of sensitive materials. The design of the barrel often incorporates various heating zones that allow for precise temperature management tailored to specific material requirements. Thus, understanding what is a hopper in injection molding becomes easier when you see how it feeds into this essential processing unit.
Interaction with the Hopper
The interaction between the barrel and the injection molding hopper is fundamental to effective production cycles. The hopper serves as a storage unit for raw plastic pellets before they are fed into the barrel for melting and processing. When evaluating what is the difference between a hopper dryer and dehumidifier, it’s important to note that while both devices manage moisture levels, their roles differ significantly in relation to both hoppers and barrels.
A well-functioning injection molding hopper ensures a steady flow of materials into the barrel without jamming or blockages—issues that can severely disrupt production efficiency. Additionally, if temperatures fluctuate within either component due to poor interaction or maintenance issues, product quality may be compromised as well. Therefore, recognizing how these two parts work together can help troubleshoot common problems encountered during manufacturing.
Impact on Product Quality
The quality of products produced through injection molding heavily relies on both consistent material feed from hoppers and effective processing within barrels. Any inconsistency at this stage can lead to defects such as warping or incomplete filling of molds—issues no manufacturer wants on their record! Understanding what is a hopper in injection molding provides context for how critical it is for feeding high-quality materials into barrels.
Furthermore, proper functioning of both components directly influences cycle times; faster melting translates into quicker production rates without sacrificing quality standards. If you consider what is the work of a hopper dryer alongside these elements, it becomes clear that maintaining ideal moisture levels enhances both flow characteristics and melting efficiency—ultimately impacting end-product durability and aesthetics.
In conclusion, recognizing how integral each element—the injector mold itself along with its associated components like hoppers and barrels—is essential for achieving optimal manufacturing outcomes cannot be overstated!
Hopper Dryer vs. Dehumidifier
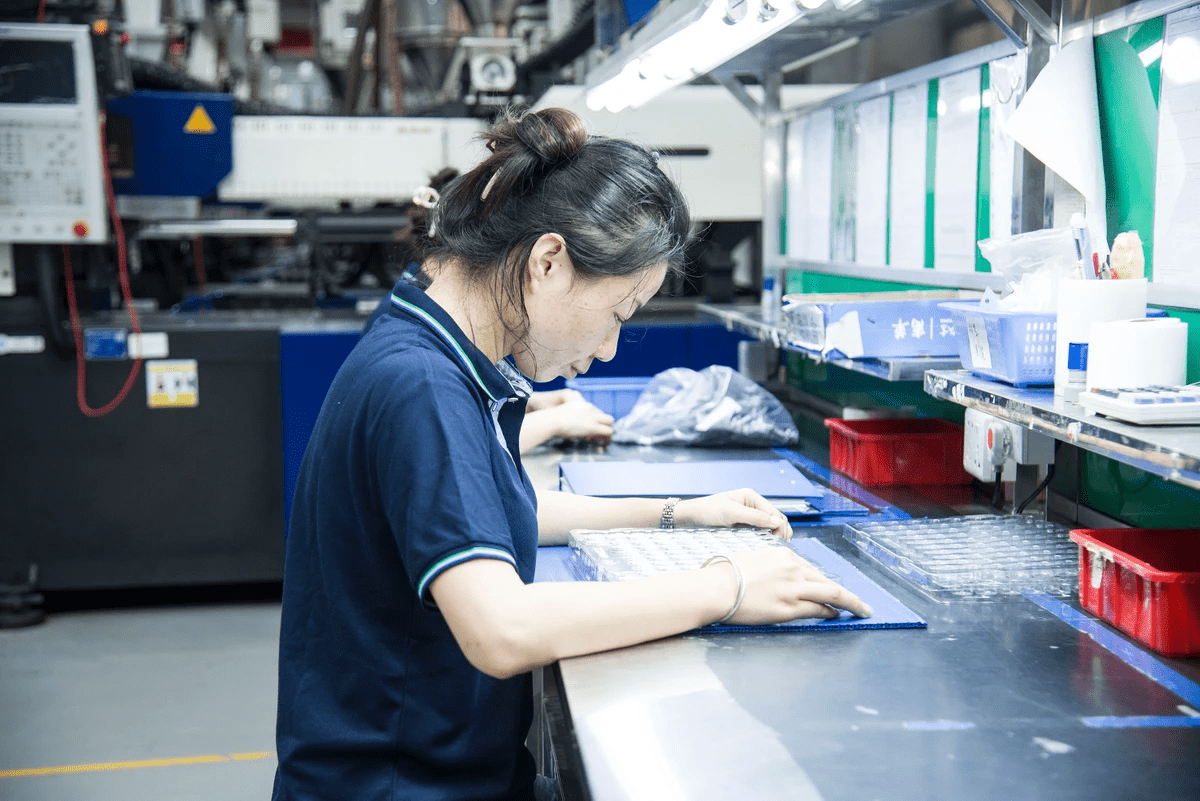
What is the Difference?
A hopper dryer is designed specifically to reduce moisture content in plastic resins before they are processed in an injection molding hopper. It uses heated air to dry materials, ensuring that moisture levels are kept at a minimum for optimal processing conditions. On the other hand, a dehumidifier works by removing humidity from the air surrounding the material, which can also help in maintaining low moisture levels but does so through a different mechanism.
In essence, while both devices aim to address moisture issues that can affect injection molding, their methods differ significantly. The hopper dryer directly heats materials within the injection molding process environment, allowing for faster drying times and more immediate results. Conversely, dehumidifiers create a controlled atmosphere around storage areas or processing environments without directly interacting with materials.
Efficiency and Cost Considerations
When evaluating efficiency and cost considerations for these two systems, it's essential to understand their operational costs versus their benefits in preventing defects during injection molding processes. Hopper dryers typically have higher upfront costs due to their heating elements and more complex designs; however, they often provide quicker drying times which can lead to increased production rates down the line.
Dehumidifiers may be less expensive initially but could require additional equipment or modifications for optimal performance when dealing with certain plastics used in your injection molding hopper setup. Ultimately, choosing between these two options will depend on your specific production needs—whether you prioritize speed or cost-effectiveness.
Best Applications for Each
Determining which system is best suited for your operation involves considering various factors such as material type and processing requirements within your injection molding process. Hopper dryers are ideal for hygroscopic materials like nylon or PET that tend to absorb moisture quickly; therefore, using them can prevent potential defects related to moisture during processing through an injection molding hopper.
On the other hand, if you’re dealing with less sensitive materials or working in an environment where humidity control is necessary but not critical—like some thermoplastics—a dehumidifier might be sufficient to maintain acceptable moisture levels without incurring higher energy costs associated with heating elements found in hopper dryers.
In conclusion, understanding what is a hopper in injection molding—and how its components function together—is vital when deciding between these two options for managing material moisture effectively.
Common Issues with Injection Molding Hoppers
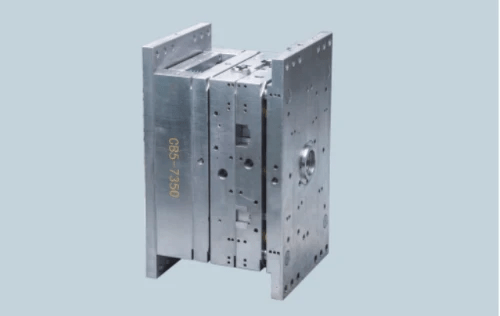
Injection molding hoppers are essential components in the molding process, but they can encounter several common issues that disrupt operations. Understanding these challenges is crucial for maintaining efficiency and product quality. In this section, we will explore jamming and blockages, temperature regulation problems, and material flow challenges associated with injection molding hoppers.
Jamming and Blockages
Jamming and blockages are perhaps the most frustrating issues that can occur with an injection molding hopper. These problems often arise when materials clump together or get stuck due to improper loading or moisture absorption, leading to production delays. Regular maintenance and proper material handling are vital to prevent these issues from becoming a recurring nightmare.
To address jamming in an injection molding hopper, operators should first inspect the hopper for any obstructions or foreign materials causing the blockage. Additionally, ensuring that the materials used are suitable for the specific type of hopper can greatly reduce the likelihood of jams occurring in the first place. Remember, a well-functioning hopper is key to smooth operations; after all, nobody wants to play tug-of-war with their machinery!
Temperature Regulation Problems
Temperature regulation is another critical aspect when discussing what is a hopper in injection molding? If temperatures fluctuate too much within the hopper, it can lead to inconsistent material properties and ultimately affect product quality. Maintaining optimal temperatures ensures that materials flow smoothly from the hopper into the barrel without degradation.
When dealing with temperature regulation problems in an injection molding hopper, it’s essential to monitor both ambient conditions and heater functionality closely. Any malfunctioning heating elements could lead to uneven temperatures that compromise your production process. Hence, regular checks on temperature sensors will help keep everything running like a well-oiled machine!
Material Flow Challenges
Material flow challenges can be particularly vexing when considering what is the function of the barrel in injection molding? If materials do not flow correctly from the hopper into the barrel due to poor design or incorrect settings, it can result in incomplete melts or inconsistent fill patterns during production runs. This inconsistency can lead directly to defects in finished products—an outcome no one wants!
To mitigate material flow challenges within an injection molding hopper, operators should evaluate both feed rates and material characteristics regularly. Adjustments may need to be made based on varying humidity levels or different types of resins being used—especially when considering what is the difference between a hopper dryer and dehumidifier? Ensuring proper airflow through your setup will also help maintain consistent material delivery throughout your processes.
Troubleshooting Injection Molding Hopper Problems
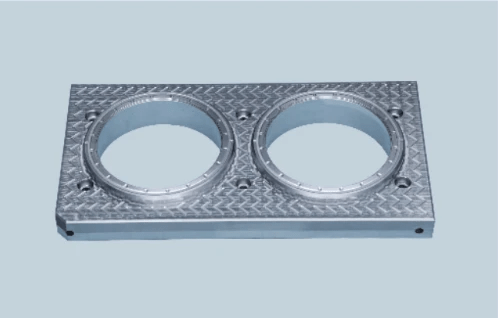
Troubleshooting injection molding hopper problems is crucial for maintaining efficiency and product quality in the molding process. Identifying issues early on can save time, resources, and headaches down the line. By understanding common symptoms of failures, solutions can be implemented effectively to keep your operation running smoothly.
Identifying Symptoms of Failures
When it comes to the injection molding hopper, several symptoms may indicate that something is amiss. For instance, if you notice inconsistent material flow or frequent jamming, it could suggest a blockage or improper settings in your hopper. Additionally, unusual noises or overheating during operation may signal temperature regulation problems that need immediate attention.
Recognizing these signs early can prevent larger issues from developing within the system. Also, pay attention to any changes in product quality; defects may arise from improper feeding or melting processes linked to the hopper's performance. Understanding what is a hopper in injection molding helps operators pinpoint these issues more effectively.
Solutions for Common Issues
Once you've identified the symptoms of failures in your injection molding hopper, it's time to explore some solutions. For jamming and blockages, ensure that materials are properly sized and free from contaminants before entering the hopper—this simple step can make a world of difference! If you're facing temperature regulation problems, check if your heating elements are functioning correctly and adjust settings as needed.
For material flow challenges, consider adjusting the angle of the hopper or using a different feeder design to improve gravity feed characteristics. Furthermore, understanding what is the function of the barrel in injection molding will help you recognize how it interacts with your hopper; ensuring both components work harmoniously can enhance overall performance significantly. Remember that preventive maintenance is key; regular checks can help avoid many common issues.
When to Consult Experts like the Baoyuan Team
While many troubleshooting tasks can be handled internally, sometimes it's best to call in professionals like Baoyuan Team when things get tricky. If you've tried various adjustments without success or if you're unsure about specific technical aspects such as what is the difference between a hopper dryer and dehumidifier regarding their impact on moisture control within your system—don't hesitate to reach out for expert advice.
Expert teams not only provide insights into complex problems but also offer tailored solutions based on their extensive experience with injection molding hoppers and related systems. They can also assist with training staff on proper maintenance practices and operational guidelines for optimal performance of equipment like your hopper dryer—ensuring everyone knows what is the work of a hopper dryer in relation to preventing moisture-related defects.
In conclusion, effective troubleshooting involves recognizing symptoms early on and implementing appropriate solutions while knowing when it's time to seek expert assistance for more intricate challenges related to your injection molding processes.
Conclusion
In the world of injection molding, understanding the role of the injection molding hopper is essential for achieving optimal production outcomes. A hopper serves as the first step in the material feeding process, ensuring that plastic pellets are delivered efficiently to the barrel for melting and shaping. Without a properly functioning hopper, even the best machinery can falter, leading to delays and quality issues.
Recap of Hopper Functionality
So, what is a hopper in injection molding? It's more than just a container; it's a crucial component that regulates material flow into the barrel. The interaction between the hopper and barrel directly influences processing efficiency and product quality, making it vital to grasp their functionalities together.
Importance of Proper Maintenance
Maintaining your injection molding hopper is not just good practice; it’s essential for consistent production runs. Regular checks can prevent common issues such as jamming or temperature regulation problems that could disrupt operations. Remember, an ounce of prevention is worth a pound of cure—keeping your hopper in top shape will save time and costs down the line.
Seeking Expert Help for Complex Issues
When faced with persistent challenges like material flow issues or when trying to determine what is the difference between a hopper dryer and dehumidifier, consulting experts can be invaluable. The Baoyuan Team specializes in troubleshooting complex problems related to hoppers and barrels alike. If you find yourself scratching your head over what is the function of the barrel in injection molding or how to optimize your processes further, don’t hesitate to seek professional guidance.