Introduction
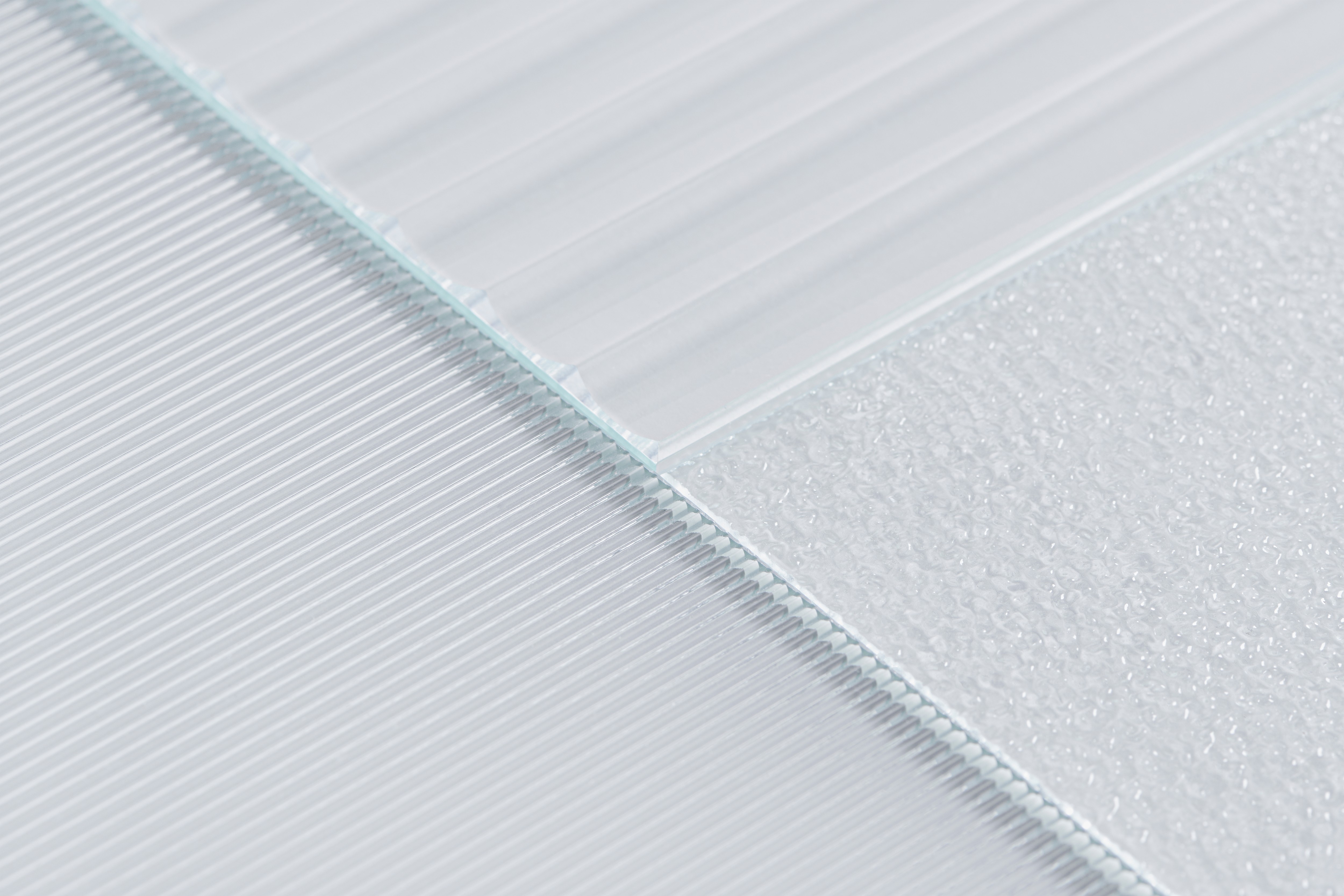
When it comes to choosing the right material for precision plastic components, the debate between ABS and polycarbonate has been ongoing. Understanding the differences and key factors to consider is crucial in making an informed decision that aligns with your project's requirements.
Understanding the Differences
ABS and polycarbonate are both popular choices for injection molded products due to their unique properties and performance in various applications. While ABS offers good impact resistance and machinability, polycarbonate boasts high transparency and heat resistance, making it a preferred choice for certain projects.
Key Factors to Consider
In selecting the right material for your project, factors such as durability, cost-effectiveness, and compatibility with different product designs play a pivotal role. It's essential to weigh these factors against your specific project needs to ensure optimal results.
Making an Informed Decision
The decision between ABS plastic molding and polycarbonate injection molding is not one-size-fits-all. Long-term durability, cost analysis, and impact on the manufacturing process must be carefully considered to make an informed choice that aligns with your project goals.
By understanding the differences between ABS and polycarbonate materials and considering key factors such as durability and cost-effectiveness, you can make an informed decision that aligns with your project's specific requirements.
ABS vs Polycarbonate: A Material Overview
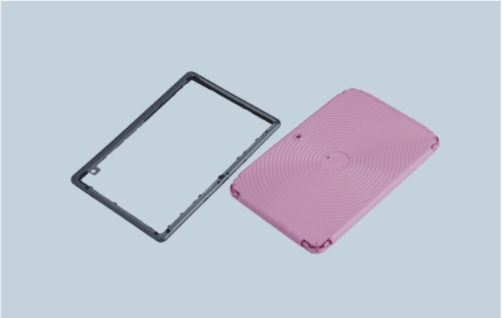
When comparing ABS vs polycarbonate, it's essential to understand the unique properties of each material. ABS plastic is known for its toughness, impact resistance, and heat resistance, making it ideal for a wide range of applications. On the other hand, polycarbonate offers exceptional transparency, high impact strength, and excellent dimensional stability, making it suitable for products that require optical clarity and durability.
Properties of ABS Plastic
ABS plastic is a thermoplastic polymer known for its outstanding mechanical properties. It exhibits excellent impact resistance and toughness, making it suitable for products that require durability and strength. Additionally, ABS is resistant to heat and chemicals, making it an ideal choice for a variety of applications.
ABS plastic is also known for its ease of processing, allowing it to be molded into a wide range of shapes and sizes. This versatility makes it a popular choice for manufacturers looking to create intricate and complex designs. Additionally, ABS plastic can be easily painted or coated, further expanding its potential applications in industries such as automotive, electronics, and consumer goods.
Properties of Polycarbonate
Polycarbonate is a transparent thermoplastic known for its exceptional impact resistance and optical clarity. It offers high heat resistance and dimensional stability, making it suitable for products that require transparency and durability. Polycarbonate also has excellent electrical insulation properties.
Polycarbonate's exceptional impact resistance and optical clarity make it a popular choice for a wide range of applications. Whether it's used in automotive parts, safety goggles, or electronic display screens, polycarbonate's durability and transparency provide an ideal solution for products that require both strength and visibility. Its high heat resistance and dimensional stability further enhance its versatility, allowing manufacturers to create long-lasting, reliable products across various industries.
Performance in Various Applications
When considering ABS vs polycarbonate performance in various applications, it's important to note that ABS is commonly used in automotive parts, electronic housings, consumer goods, and toys due to its toughness and impact resistance. On the other hand, polycarbonate is often used in medical devices, safety goggles, electronic components, and LED light covers due to its optical clarity and high impact strength.
In addition to their specific applications, ABS and polycarbonate also differ in their chemical resistance. ABS is more resistant to a wide range of chemicals, making it suitable for use in automotive parts and consumer goods that may come into contact with various substances. On the other hand, polycarbonate offers better resistance to oils and greases, making it a preferred choice for medical devices and electronic components that need to withstand exposure to these substances without degrading.
Choosing the Right Material for Your Project
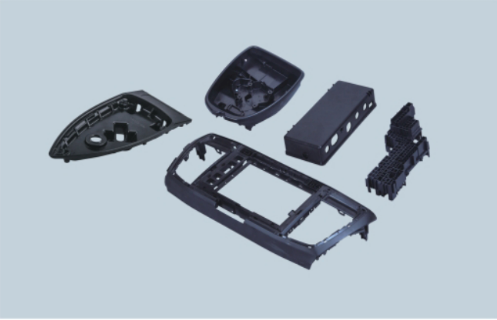
When it comes to selecting the right material for your project, several factors must be considered. The properties of ABS and polycarbonate, such as strength, impact resistance, and temperature stability, should be carefully evaluated to ensure they meet the specific requirements of your application.
Factors to Consider in Material Selection
The choice between ABS and polycarbonate will depend on various factors such as mechanical properties, chemical resistance, and surface finish. ABS is known for its excellent impact resistance and toughness, making it suitable for products that require durability. On the other hand, polycarbonate offers superior heat resistance and optical clarity, making it ideal for applications that require transparency.
When considering material selection, it's important to also think about the cost of production. ABS is generally more cost-effective than polycarbonate, making it a preferred choice for products with budget constraints. However, polycarbonate may be the better option for applications that require long-term durability and resistance to environmental factors, as it tends to have a longer lifespan and requires less maintenance. Therefore, weighing the initial cost against long-term benefits is crucial in making the right material selection decision.
Impact on Manufacturing Process
The material you choose can significantly impact the manufacturing process. ABS plastic molding is well-suited for injection molding due to its flowability and ease of processing. Polycarbonate injection molding requires higher temperatures and pressures but offers exceptional dimensional stability and precision in producing complex components.
The choice of material also impacts the long-term durability and cost analysis of the manufacturing process. ABS plastic, with its excellent impact resistance and low cost, provides a durable solution for various applications. On the other hand, polycarbonate, while requiring higher initial investment, offers superior long-term durability and can result in cost savings due to reduced maintenance and replacement costs over time. Careful consideration of these factors is crucial in determining the most suitable material for your manufacturing needs.
Long-Term Durability and Cost Analysis
Long-term durability and cost analysis are crucial considerations when selecting a material for your project. While ABS is cost-effective and offers good mechanical properties, polycarbonate's higher initial cost may be justified by its superior heat resistance and optical clarity, resulting in long-term savings.
By carefully evaluating the factors mentioned above, you can make an informed decision about whether ABS or polycarbonate is the right choice for your project. The next section will delve into the benefits and limitations of ABS plastic molding versus polycarbonate injection molding.
ABS Plastic Molding vs Polycarbonate Injection Molding
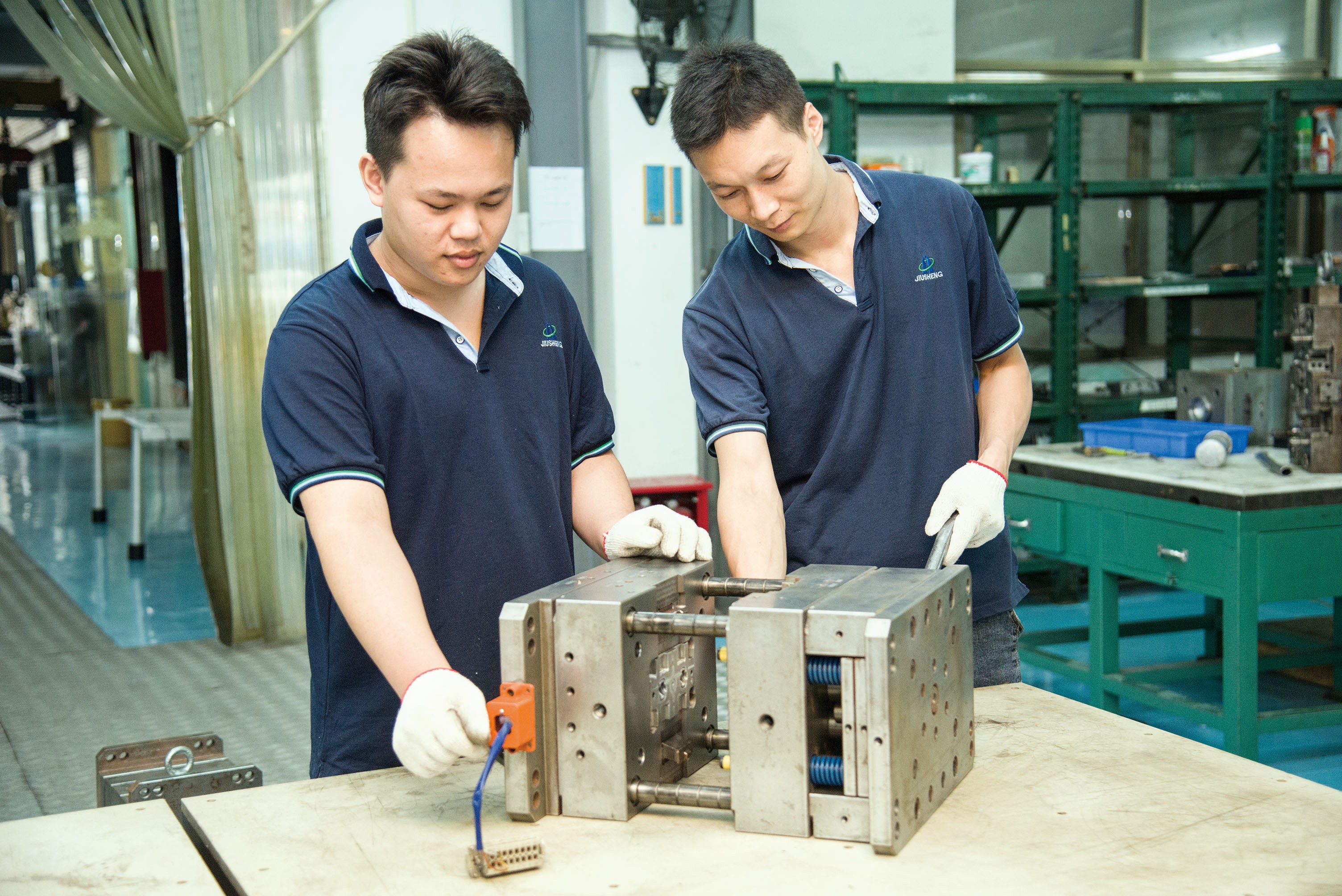
When it comes to ABS plastic molding and polycarbonate injection molding, each process has its own set of benefits and limitations. ABS plastic molding offers excellent impact resistance and is ideal for producing precision plastic components with intricate details. On the other hand, polycarbonate injection molding provides superior optical clarity and high heat resistance, making it suitable for a wide range of injection molded products.
Benefits and Limitations of Each Process
ABS plastic molding is known for its cost-effectiveness, ease of processing, and the ability to be easily colored or finished. However, it may not be suitable for applications that require high heat resistance or optical clarity. Polycarbonate injection molding, on the other hand, offers exceptional impact strength and can withstand high temperatures without deformation. However, it may be more expensive than ABS plastic molding and can be prone to scratching.
Compatibility with Different Product Designs
When considering compatibility with different product designs, ABS plastic molding is well-suited for products that require intricate details or complex geometries. Its ability to be easily colored also makes it a popular choice for products with specific aesthetic requirements. Polycarbonate injection molding is ideal for products that demand optical clarity or need to withstand harsh environmental conditions due to its superior heat resistance and durability.
Quality and Precision of Molded Plastics
Both ABS plastic molding and polycarbonate injection molding processes are capable of producing high-quality molded plastics with precision and accuracy. However, the choice between the two will depend on the specific requirements of your project. While ABS plastic offers excellent dimensional stability and surface finish, polycarbonate provides exceptional optical clarity and impact resistance.
Now that we've explored the benefits and limitations of both ABS plastic molding and polycarbonate injection molding processes, it's important to carefully consider which material best suits your project's needs before making a decision.
Two Shot Injection Molding: A Comparative Analysis
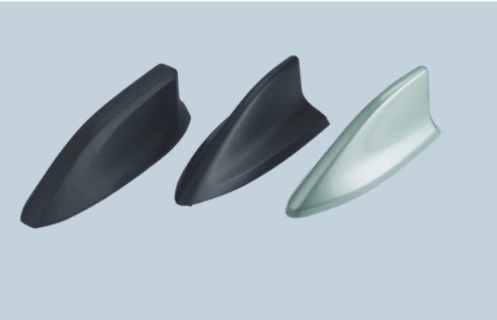
Two shot injection molding offers numerous advantages, including reduced production time, lower labor costs, and improved product quality. However, it also comes with challenges such as increased tooling complexity and higher initial investment. When it comes to ABS and polycarbonate, two shot molding is suitable for both materials, offering versatile options for creating precision plastic components.
Advantages and Challenges of Two Shot Molding
The main advantage of two shot injection molding is the ability to produce complex, multi-material products in a single operation, reducing assembly time and costs. On the other hand, the process requires precise control over material compatibility and adhesion, as well as specialized equipment and expertise.
The ability to produce complex, multi-material products in a single operation is a game-changer for manufacturers looking to streamline their production processes. This not only reduces assembly time and costs but also allows for the creation of innovative designs that were previously difficult to achieve. However, achieving the desired results requires precise control over material compatibility and adhesion, which can be challenging without the right expertise and equipment.
Suitability for ABS and Polycarbonate
Two shot molding is well-suited for both ABS and polycarbonate due to their compatibility with other materials such as thermoplastic elastomers (TPE) or thermoplastic polyurethane (TPU). This opens up a wide range of design possibilities for injection molded products, allowing for the creation of innovative and functional components.
Two shot molding offers the advantage of combining different materials in a single injection molded product, which can greatly enhance its functionality and aesthetics. By using ABS or polycarbonate as the base material and incorporating TPE or TPU for overmolding, manufacturers can create products with improved grip, cushioning, or flexibility. This versatility allows for the production of ergonomic designs that are not only comfortable to use but also visually appealing, giving them a competitive edge in the market.
Impact on Product Functionality and Aesthetics
The use of two shot injection molding can greatly enhance product functionality by incorporating different materials with varying properties into a single part. This can improve performance, durability, and aesthetics while reducing overall production costs. The process allows for greater design flexibility in creating visually appealing products that meet specific performance requirements.
The ability to combine different materials in a single part through two shot injection molding also allows for the integration of multiple functions within a single component. This means that products can be designed to perform multiple tasks or have added features without the need for additional parts or assembly. This not only streamlines production and reduces potential points of failure but also enhances the overall functionality and user experience of the end product.
Baoyuan: Your Partner in Manufacturing Excellence
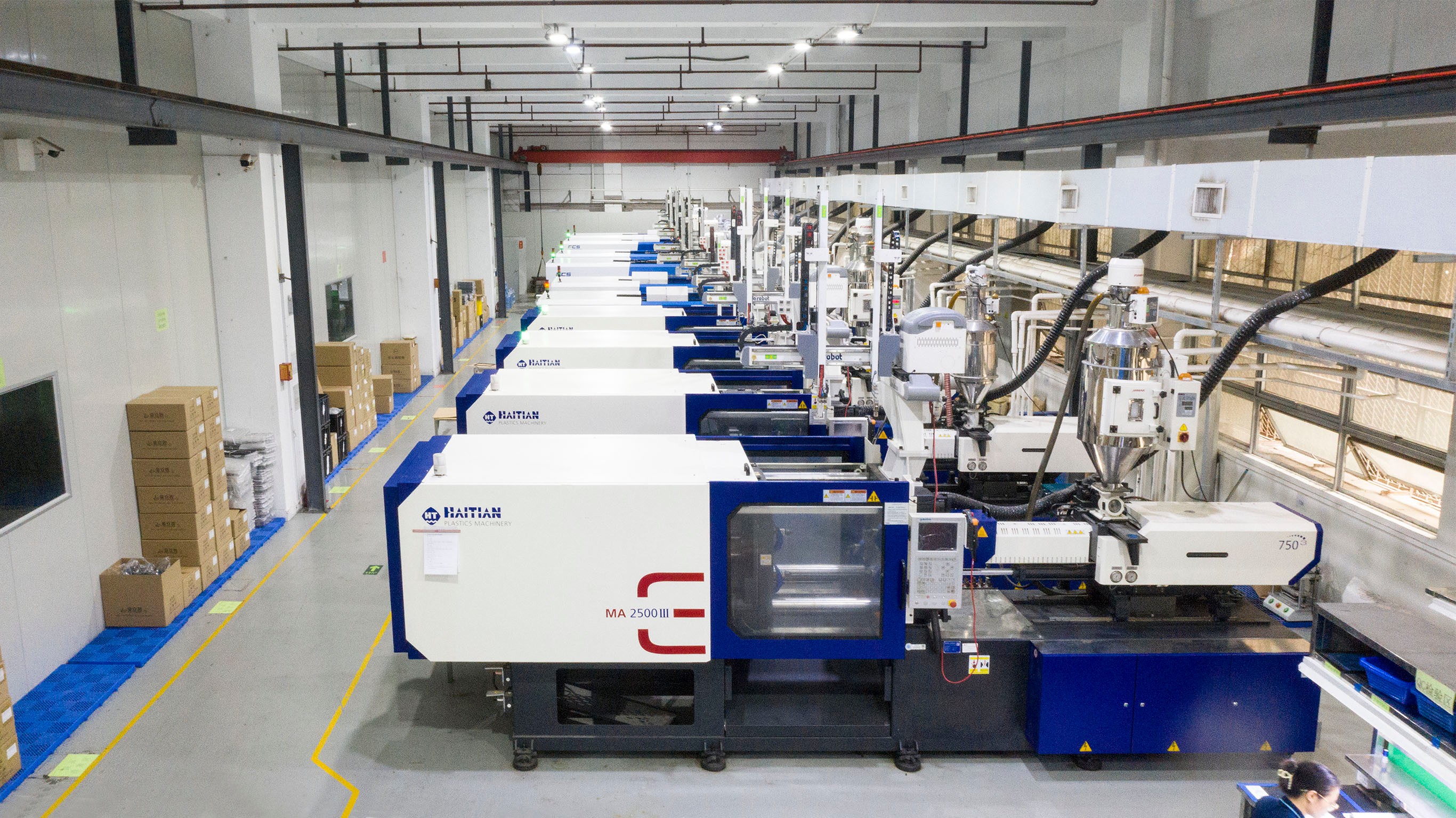
Baoyuan is a trusted leader in precision plastic components, specializing in injection molded products made from ABS and polycarbonate. With decades of experience, Baoyuan offers unmatched expertise in manufacturing high-quality plastics for various industries.
Leveraging Baoyuan's Expertise
When it comes to choosing the right material for your project, Baoyuan's team of experts can provide valuable insights on the advantages of ABS vs polycarbonate. Their deep understanding of the properties and performance of these materials ensures that you make an informed decision that aligns with your project requirements.
Furthermore, Baoyuan's team can also offer guidance on the best manufacturing processes for each material, ensuring that your project is produced with the highest quality and precision. Whether it's injection molding for ABS or thermoforming for polycarbonate, their expertise can help you navigate the complexities of production to achieve the best results. By leveraging their knowledge, you can avoid costly mistakes and delays, ultimately saving time and resources in the long run.
Ensuring Quality and Precision in Production
Baoyuan's commitment to quality extends to every stage of production, from material selection to final inspection. Their state-of-the-art facilities and rigorous quality control processes guarantee that each product meets the highest standards for durability, functionality, and aesthetics. Moreover, Baoyuan is constantly researching and optimizing the use of ABS and polycarbonate materials in their production processes. By staying at the forefront of material innovation, they are able to ensure that their products not only meet industry standards but also exceed customer expectations.
Optimizing the Use of ABS and Polycarbonate Materials
With Baoyuan as your manufacturing partner, you can optimize the use of ABS and polycarbonate materials to achieve superior results. Their expertise in ABS plastic molding and polycarbonate injection molding allows for innovative solutions that enhance product performance while minimizing costs. Furthermore, Baoyuan's commitment to sustainability means that their manufacturing processes prioritize eco-friendly practices, ensuring that your products are not only high-performing but also environmentally responsible. In addition, Baoyuan's dedication to quality control guarantees that the ABS and polycarbonate materials used in your products meet the highest standards, providing peace of mind for both you and your customers.
Conclusion

When it comes to choosing the right material for your project, the decision between ABS and polycarbonate can make a significant impact on the performance and durability of your product. By understanding the differences and key factors to consider, you can make an informed decision that aligns with your project's requirements. Whether it's ABS plastic molding or precision plastic components, the choice between these materials will have a lasting impact on your manufacturing process.
Making the Right Choice for Your Project
The properties of ABS plastic and polycarbonate play a crucial role in determining which material is best suited for your project. With ABS offering excellent impact resistance and polycarbonate providing high transparency and heat resistance, it's essential to carefully evaluate which material aligns with your specific application needs. By considering factors such as long-term durability and cost analysis, you can ensure that you make the right choice for your project.
Leveraging Expertise for Successful Manufacturing
When it comes to injection molded products, precision and quality are paramount in achieving superior results. The benefits and limitations of ABS plastic molding versus polycarbonate injection molding should be carefully evaluated to determine which process is best suited for your product designs. By leveraging expertise in manufacturing processes, you can ensure that your products meet the highest standards of quality and precision.
Achieving Superior Results with Baoyuan
As a trusted partner in manufacturing excellence, Baoyuan offers expertise in optimizing the use of ABS and polycarbonate materials for various applications. Whether it's two shot injection molding or molded plastics, Baoyuan's commitment to quality ensures that your products achieve superior functionality and aesthetics. With Baoyuan as your manufacturing partner, you can rest assured that every aspect of production is meticulously executed to achieve exceptional results.