Introduction
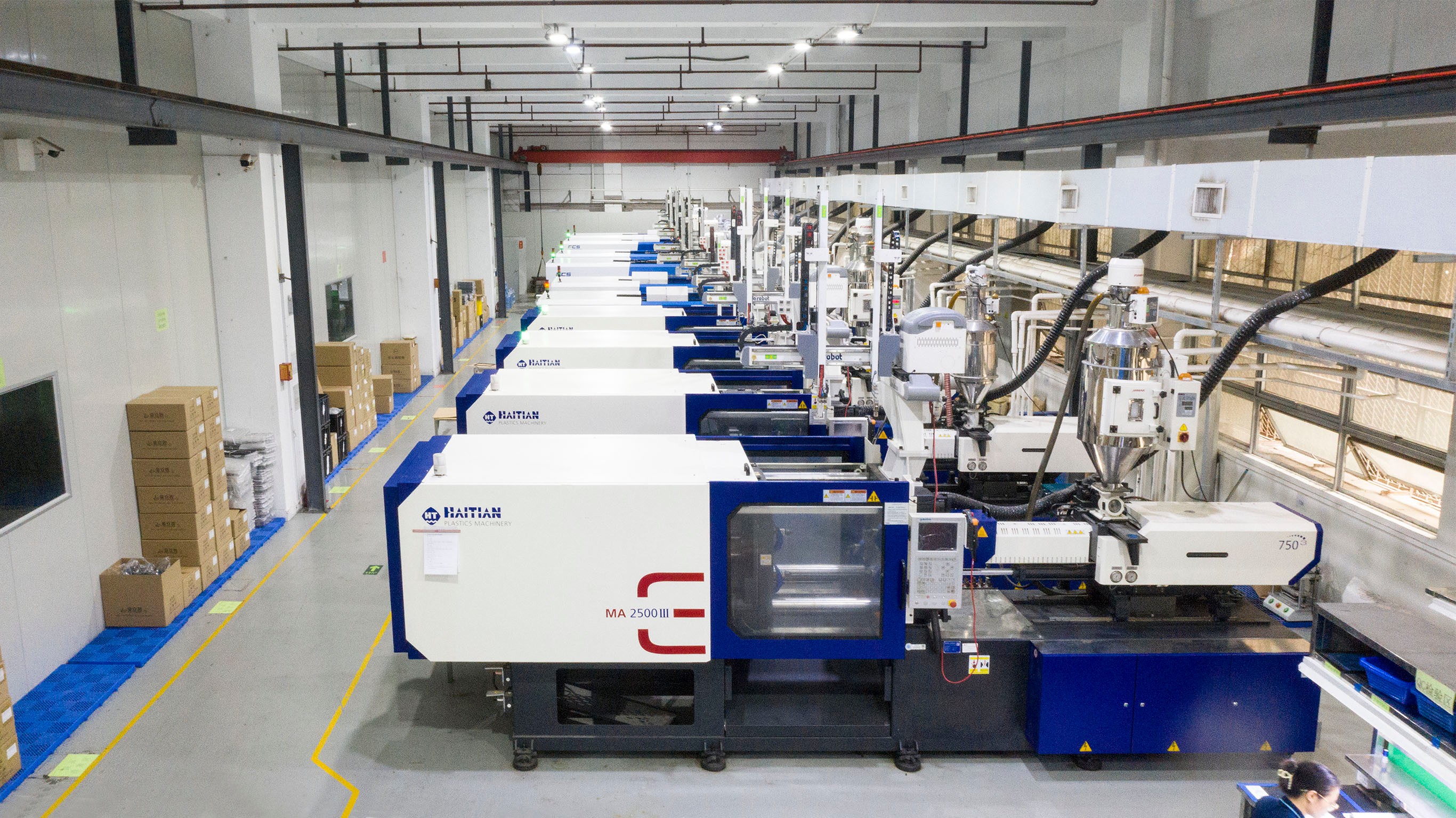
When it comes to plastic manufacturing, understanding the various processes involved is crucial for achieving the desired end product. Selecting the ideal plastic manufacturing process can significantly impact the quality, cost, and efficiency of production. Key considerations for plastics manufacturing include material selection, production volume, and desired product specifications.
Understanding the Plastic Manufacturing Process
The manufacturing processes for plastics encompass a wide range of techniques such as injection molding, extrusion, blow molding, thermoforming, compression molding, rotational molding, transfer molding, and reaction injection molding (RIM). Each process has its unique advantages and limitations that must be carefully evaluated based on the specific requirements of the project.
Importance of Selecting the Right Process
Selecting the ideal plastic manufacturing process is crucial for ensuring that the final product meets performance standards while maintaining cost-effectiveness. The wrong process can lead to subpar quality or excessive production costs. Therefore, thorough analysis and understanding of each process are essential to make an informed decision.
Key Considerations for Plastics Manufacturing
In addition to choosing the right manufacturing process, other key considerations in plastics and rubber manufacturing include sustainability practices, regulatory compliance, material sourcing, and technological advancements. These factors play a vital role in shaping industry trends and driving innovation in plastic forming and manufacturing processes.
Injection Molding
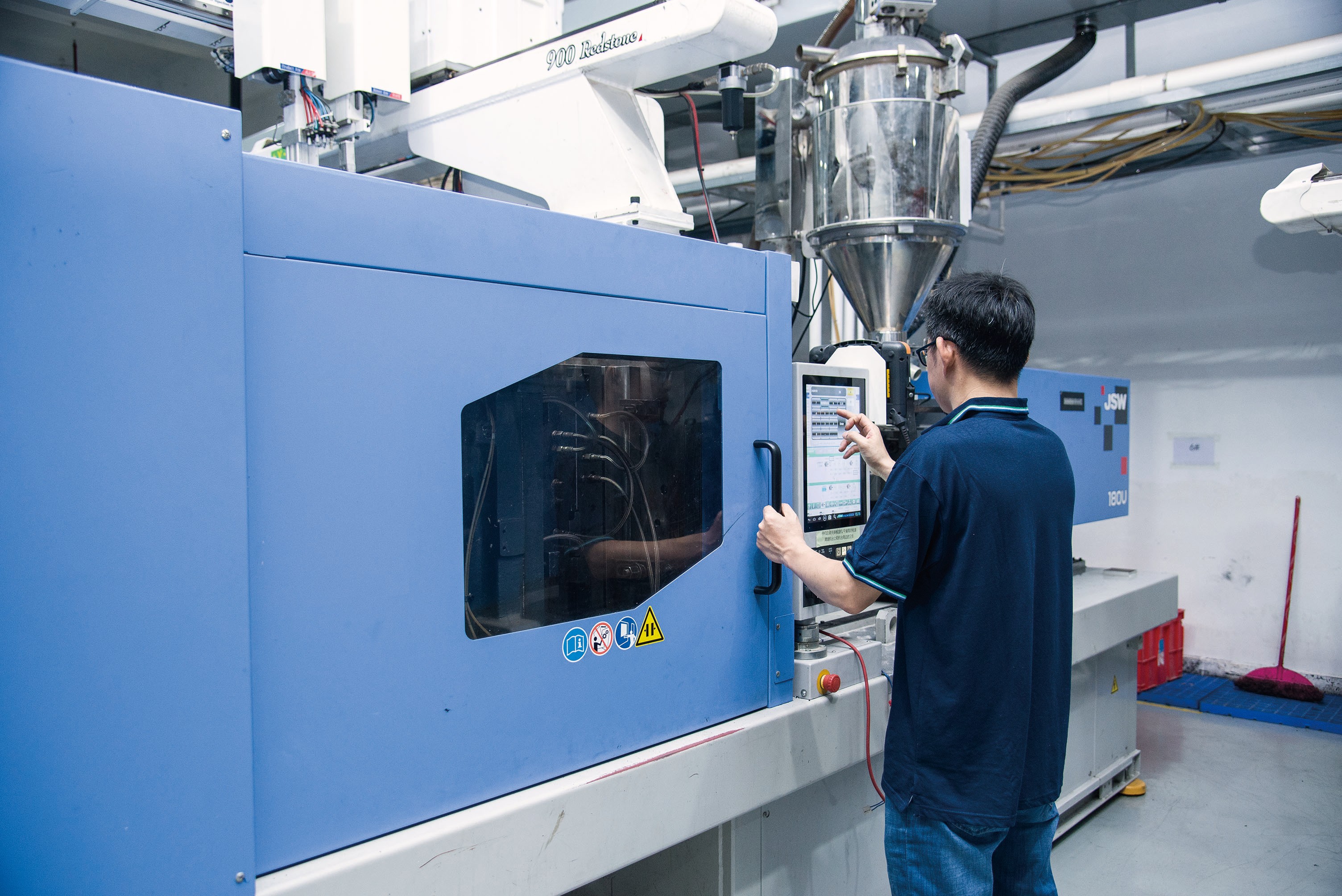
When it comes to plastic manufacturing processes, injection molding is a key player. Baoyuan's expertise in injection molding ensures precision and efficiency in producing high-quality plastic parts. The advantages of injection molding include fast production cycles, high efficiency, and the ability to create complex shapes. However, limitations such as initial tooling costs and material restrictions should be carefully considered when selecting this process.
Baoyuan's Expertise in Injection Molding
Baoyuan's extensive experience in injection molding sets them apart as a reliable partner for all plastic manufacturing needs. Their state-of-the-art facilities and skilled workforce enable them to handle projects of any scale with utmost precision and quality. Whether it's prototyping or mass production, Baoyuan's expertise in injection molding guarantees top-notch results.
Advantages and Limitations of Injection Molding
The advantages of injection molding are evident in its ability to produce large volumes of identical parts with minimal waste, making it a cost-effective solution for many industries. However, the initial investment in tooling can be substantial, especially for small-scale production runs. Material selection is also crucial as certain plastics may not be suitable for the injection molding process.
Innovations in Injection Molding Technology
Innovations in injection molding technology have revolutionized the industry by enhancing efficiency and reducing environmental impact. From advanced mold design software to energy-efficient machinery, these innovations have paved the way for sustainable manufacturing practices while maintaining high productivity levels. Baoyuan stays at the forefront of these technological advancements to deliver cutting-edge solutions to their clients.
Remember that selecting the ideal plastic manufacturing process is crucial for achieving optimal results while considering factors such as cost-effectiveness, production volume, and material requirements. With Baoyuan’s expertise across various plastic forming techniques like extrusion, blow molding, thermoforming, compression molding, rotational molding, transfer molding and reaction injection molding (RIM), they offer comprehensive solutions tailored to specific project needs within the plastics and rubber manufacturing industry trends.
Extrusion
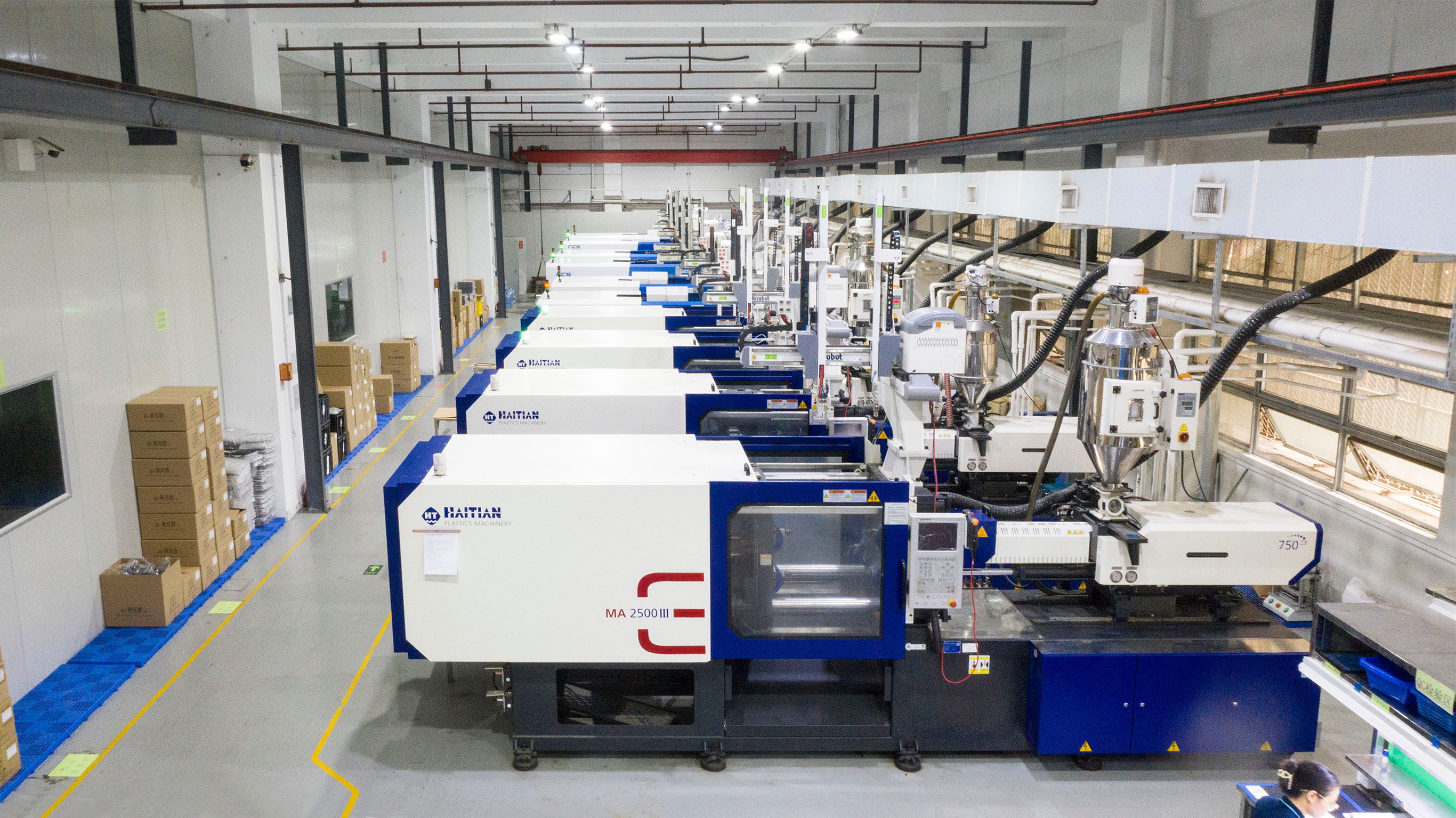
When it comes to plastic manufacturing processes, extrusion is a key method used by Baoyuan due to their proficiency in this area. The extrusion process involves pushing raw plastic material through a die to create a specific shape, making it ideal for producing continuous lengths of plastic with a consistent cross-section.
Baoyuan's Proficiency in Extrusion
Baoyuan has honed their expertise in extrusion, allowing them to efficiently produce a wide range of plastic products with precision and quality. Their skilled team ensures that the extruded products meet the exact specifications and requirements of their clients, making them a reliable partner in the plastics manufacturing industry.
Types of Extrusion Processes
There are various types of extrusion processes utilized by Baoyuan, including hot extrusion, cold extrusion, and hydrostatic extrusion. Each method has its own unique advantages and applications, catering to different industry needs and product requirements.
Applications and Benefits of Extrusion in Plastic Manufacturing
Extrusion plays a crucial role in the plastic manufacturing industry, as it is commonly used for creating pipes, tubing, seals, and even food packaging materials. The process offers benefits such as cost-effectiveness, versatility in design, and the ability to work with a wide range of thermoplastic materials.
Now that we have explored Baoyuan's proficiency in extrusion and its various applications and benefits within the plastics manufacturing process, let's delve into other essential molding techniques offered by this industry leader.
Blow Molding
Blow molding is a versatile plastic manufacturing process that Baoyuan has perfected over the years. With expertise in both extrusion blow molding and injection blow molding, our team ensures high-quality production for a wide range of industries.
Baoyuan's Experience in Blow Molding
Baoyuan's extensive experience in blow molding allows us to cater to diverse client needs, from custom packaging solutions to automotive components and consumer goods. Our state-of-the-art facilities and skilled technicians guarantee precise and efficient production.
Variations of Blow Molding Techniques
The variations in blow molding techniques include extrusion blow molding, injection blow molding, and stretch blow molding, each with its unique advantages and applications. Baoyuan understands the intricacies of these techniques to deliver optimal results for our clients.
Advancements in Blow Molding Technology
As technology continues to evolve, so does the blow molding process. Baoyuan stays at the forefront of these advancements, incorporating innovations such as multi-layer coextrusion and sustainable materials to meet the ever-changing demands of the plastics industry.
Plastics and Rubber Manufacturing Industry Trends are constantly evolving with new technologies and processes being developed regularly. It's crucial for businesses to stay updated on these trends to remain competitive in the market. By understanding the various manufacturing processes for plastics and selecting the ideal one for specific products, companies can ensure efficiency and cost-effectiveness while maintaining high-quality standards throughout their production operations.
Thermoforming

Thermoforming is a plastic manufacturing process that involves heating a sheet of plastic until it becomes pliable, then forming it into a specific shape using a mold. Baoyuan has honed its expertise in thermoforming, ensuring precision and quality in every product. This process is versatile and cost-effective, making it an ideal choice for various industries.
Baoyuan's Expertise in Thermoforming
Baoyuan's extensive experience in thermoforming sets them apart as leaders in the industry. Their skilled team and state-of-the-art equipment enable them to produce high-quality thermoformed products with intricate designs and precise specifications, meeting the diverse needs of their clients.
Understanding the Thermoforming Process
Thermoforming begins with heating a thermoplastic sheet until it becomes pliable, then placing it over a mold where vacuum or pressure forms the material into the desired shape. Once cooled, the formed plastic retains its new shape, ready for trimming and finishing touches.
Key Applications of Thermoforming in Plastics Industry
Thermoforming is widely used in packaging, automotive parts, electronic enclosures, and even medical equipment due to its ability to produce complex shapes with relatively low tooling costs. Its versatility makes it an attractive option for manufacturers looking to create custom-designed plastic products efficiently.
Remember that understanding the different plastic manufacturing processes is crucial when selecting the ideal method for your specific product needs. The Plastic Forming & Manufacturing Process requires careful consideration of factors such as material properties, design complexity, production volume, and cost-effectiveness to ensure success in your manufacturing endeavors within the Plastics and Rubber Manufacturing industry.
Compression Molding
Baoyuan's expertise in compression molding is unmatched, with a proven track record of delivering high-quality plastic products. Our state-of-the-art facilities and skilled technicians ensure precise and efficient compression molding processes that meet the highest industry standards.
Baoyuan's Competence in Compression Molding
With years of experience, Baoyuan has perfected the art of compression molding, offering custom solutions for various industries. Our team's extensive knowledge and hands-on approach enable us to tackle complex projects with ease, delivering exceptional results every time.
Advantages and Limitations of Compression Molding
Compression molding offers several advantages, including cost-effectiveness, high production output, and the ability to mold intricate shapes. However, it may not be suitable for large-scale production or products requiring thin walls due to longer cycle times and material limitations.
Recent Developments in Compression Molding
Recent advancements in compression molding technology have focused on improving cycle times, enhancing material compatibility, and reducing energy consumption. Baoyuan stays at the forefront of these developments to ensure our clients benefit from the latest innovations in compression molding.
Rotational Molding
Rotational molding, also known as rotomolding, is a manufacturing process where a hollow plastic part is formed by rotating a mold while the material melts and coats the inside. Baoyuan's skill in rotational molding ensures high-quality and durable products for various industries.
Baoyuan's Skill in Rotational Molding
With years of experience, Baoyuan has honed its expertise in rotational molding, delivering precise and consistent results for clients across different sectors. The company's proficiency in this process allows them to create complex shapes and large parts with ease, meeting the unique requirements of their customers.
Process and Equipment Used in Rotational Molding
The rotational molding process involves loading a measured amount of polymer powder into a mold, which is then heated and rotated bi-axially to evenly distribute the material. This method offers flexibility in design and production, as well as cost-effectiveness due to minimal waste. Specialized equipment such as ovens, molds, and cooling chambers are used to ensure the quality of the final product.
Unique Characteristics and Applications of Rotational Molding
One of the unique characteristics of rotational molding is its ability to produce seamless parts with uniform wall thickness, making it ideal for creating large containers, tanks, playground equipment, and even medical devices. The versatility of this method allows for customization without sacrificing structural integrity or durability.
Transfer Molding
Baoyuan has honed its proficiency in transfer molding, a versatile plastic manufacturing process that involves transferring a measured amount of uncured molding material into a heated mold cavity. This method allows for complex shapes and intricate details to be achieved with high precision.
Baoyuan's Proficiency in Transfer Molding
Our team at Baoyuan is well-versed in the intricacies of transfer molding, ensuring that each product meets the highest standards of quality and precision. With our expertise, we can cater to a wide range of industries and produce custom solutions tailored to specific requirements.
Comparison with Other Molding Techniques
In comparison to other molding techniques, transfer molding offers distinct advantages such as reduced material waste, shorter production cycles, and the ability to mold intricate parts with minimal flash or excess material. It also provides better control over the molding process and allows for the use of various materials.
Benefits of Transfer Molding in Plastic Manufacturing
The benefits of transfer molding in plastic manufacturing are manifold. It enables cost-effective production of complex geometries, reduces post-molding operations, and ensures consistent part quality. Additionally, it offers excellent dimensional stability and is well-suited for high-volume production runs.
Reaction Injection Molding (RIM)
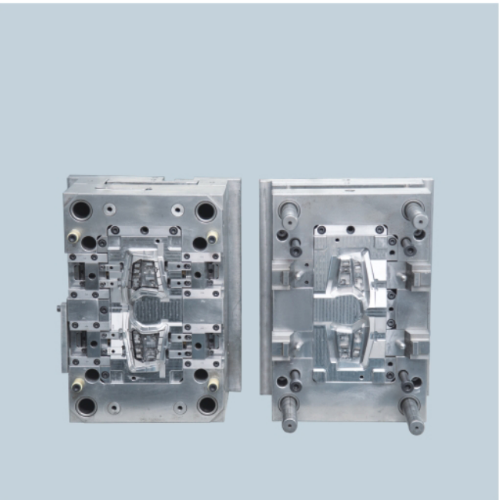
Baoyuan's expertise in reaction injection molding (RIM) sets us apart in the plastics manufacturing industry. With our state-of-the-art facilities and skilled technicians, we have successfully produced high-quality RIM products for various applications.
Baoyuan's Expertise in Reaction Injection Molding
Our team at Baoyuan has extensive experience and knowledge in reaction injection molding, allowing us to deliver superior quality products to our clients. From automotive components to medical equipment, we have the expertise to meet diverse RIM manufacturing needs.
Understanding the RIM Process
Reaction injection molding (RIM) involves mixing two liquid components under high pressure and injecting them into a mold where they chemically react and solidify into the desired shape. This process allows for the production of large, complex parts with excellent surface finishes.
Key Industries and Products Utilizing RIM Technology
Industries such as automotive, aerospace, and electronics rely on RIM technology for producing lightweight yet durable components. From bumpers and body panels to enclosures and housings, RIM offers versatility and cost-effectiveness for a wide range of products.
Conclusion
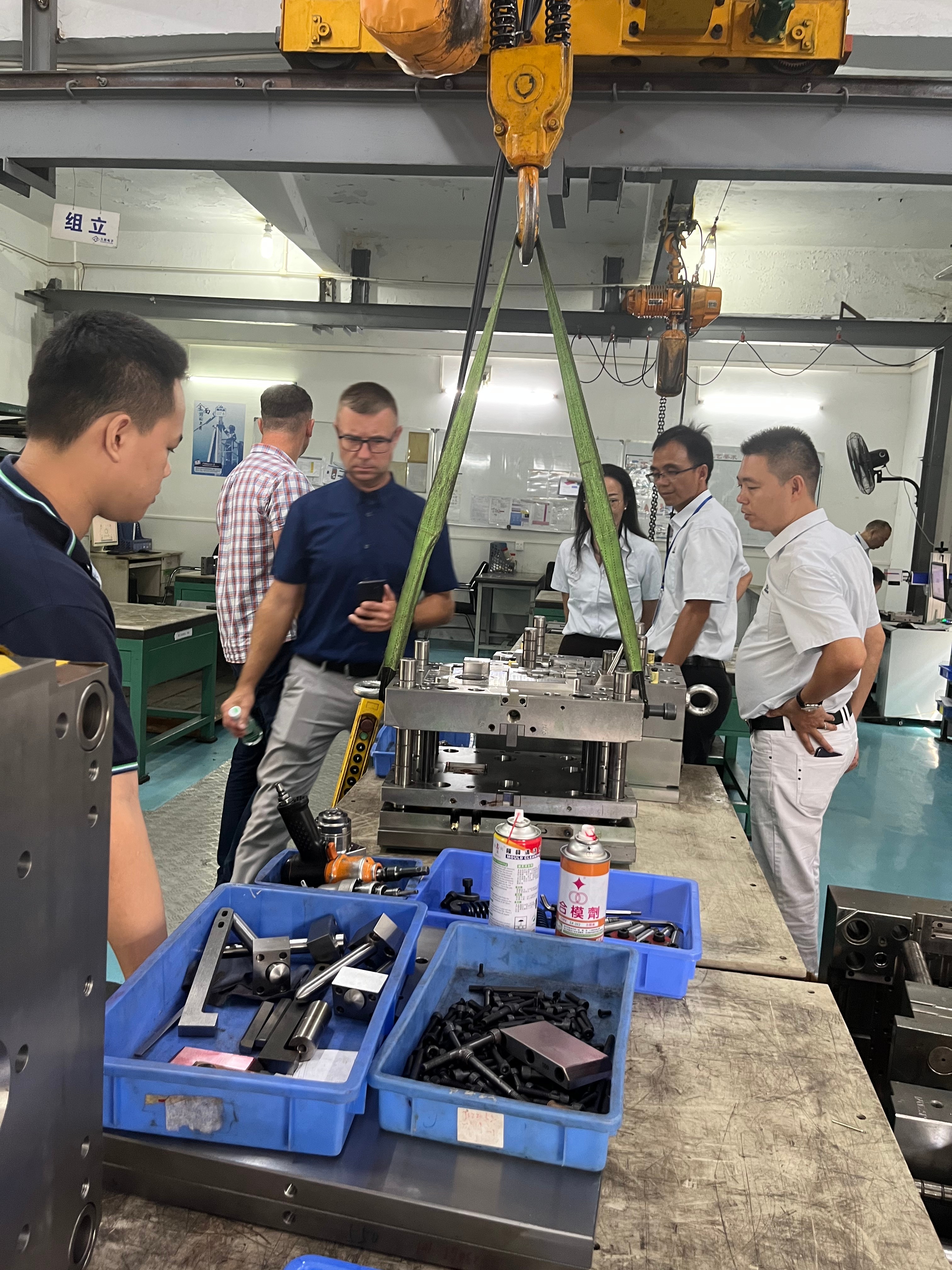
When it comes to plastic manufacturing, the selection of the ideal process is crucial for achieving the desired results. Understanding the various processes such as injection molding, extrusion, blow molding, thermoforming, compression molding, rotational molding, transfer molding, and reaction injection molding allows manufacturers to make informed decisions based on their specific needs and requirements.
Selecting the Ideal Plastic Manufacturing Process
Selecting the ideal plastic manufacturing process involves considering factors such as production volume, material properties, design complexity, and cost-effectiveness. By evaluating these factors and understanding the advantages and limitations of each process, manufacturers can choose the most suitable method for their specific application.
The Plastic Forming & Manufacturing Process
The plastic forming and manufacturing process encompasses a wide range of techniques that enable the creation of diverse products across various industries. From simple to complex shapes, plastic forming processes offer versatility and efficiency in producing high-quality components for consumer goods, automotive parts, medical devices, packaging materials, and more.
Plastics and Rubber Manufacturing Industry Trends
As technology continues to evolve, the plastics and rubber manufacturing industry is witnessing several trends that are shaping its future. These trends include advancements in sustainable materials, digitalization of production processes through Industry 4.0 technologies, increased focus on recycling and circular economy principles to reduce environmental impact.
With a deep understanding of these trends and an emphasis on innovation and sustainability practices within the industry will lead to continued growth and development in plastic manufacturing processes.