Introduction
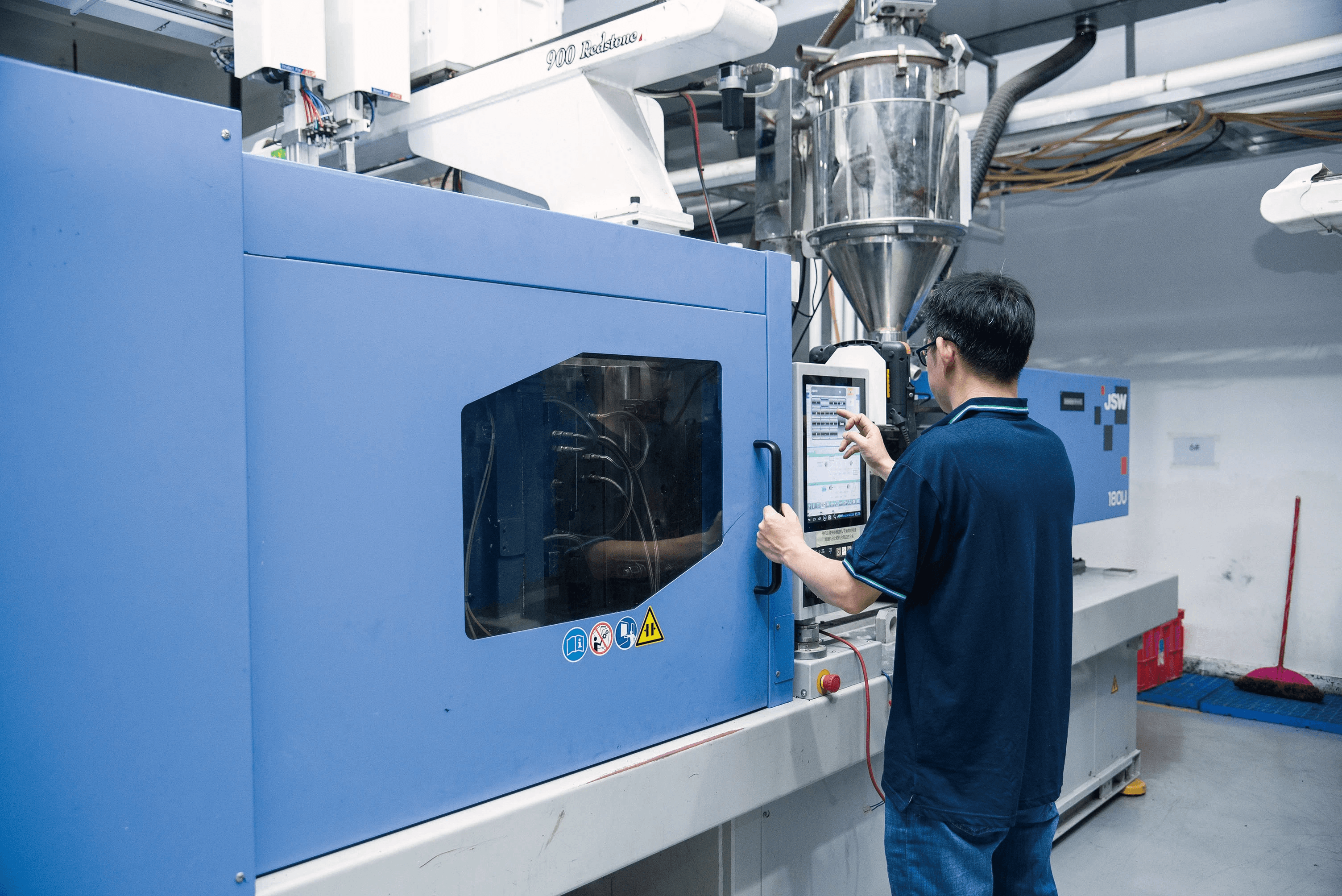
In the world of large-scale manufacturing, efficiency and precision are paramount. As industries strive to meet growing consumer demands, understanding the intricacies of production processes becomes crucial. One such process that has revolutionized appliance production is injection molding, a method that combines speed with accuracy to create high-quality components.
Understanding Large-Scale Manufacturing
Large-scale manufacturing refers to the mass production of goods using advanced technologies and streamlined processes. It enables companies to produce vast quantities while maintaining consistent quality and reducing costs. By leveraging techniques like injection molding, manufacturers can ensure that their output meets both market demand and stringent quality standards.
The Role of Injection Molding in Appliance Production
Injection molding plays a pivotal role in the production of appliances by allowing for rapid creation of complex parts with tight tolerances. This method utilizes an injection molding hopper to feed molten plastic into molds, shaping components with remarkable precision. As a result, manufacturers can produce everything from knobs to casings efficiently, making it an indispensable process in modern appliance manufacturing.
Benefits of Injection Molding for Appliance Manufacturing
The benefits of injection molding extend beyond mere speed; they encompass cost-effectiveness and versatility as well. Understanding plastic injection molding price structures helps businesses make informed decisions about production investments while factoring in long-term savings from reduced waste and labor costs. Furthermore, addressing low volume injection molding cost allows smaller manufacturers to compete effectively without sacrificing quality or performance in their products.
Overview of Injection Molding
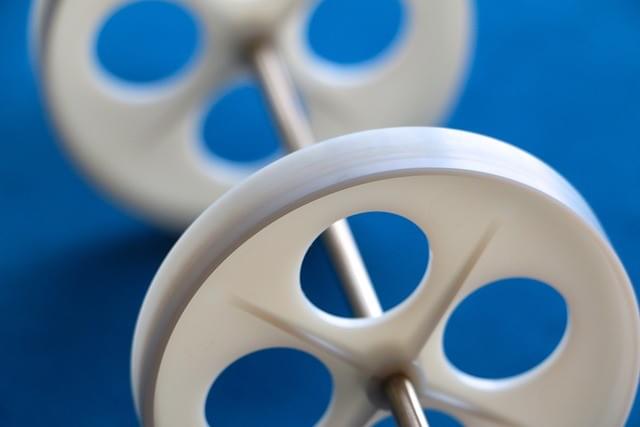
Injection molding is a transformative process in large-scale manufacturing, enabling the production of intricate plastic parts with remarkable efficiency and precision. This technique involves injecting molten plastic into a mold to create components that meet specific design requirements. The beauty of injection molding lies in its ability to produce high volumes of identical parts, making it indispensable in industries such as appliance manufacturing.
What is Injection Molding?
At its core, injection molding is a manufacturing process where thermoplastic or thermosetting materials are heated until they become pliable and then injected into a mold cavity under pressure. Once cooled, the material solidifies, taking on the shape of the mold. This method not only allows for complex designs but also ensures that each part adheres to strict injection molding tolerances, which are crucial for maintaining quality in large-scale production.
The versatility of injection molding means it can be used for everything from small appliance components to larger industrial parts. It’s particularly favored for its speed; once the initial setup is complete, producing thousands or even millions of parts becomes feasible without significant downtime. As such, when evaluating plastic injection molding price, businesses often find it cost-effective compared to other manufacturing methods.
Key Components of an Injection Molding System
An efficient injection molding system consists of several key components that work together seamlessly to produce high-quality products. The most critical element is the injection molding hopper, where raw plastic pellets are fed into the machine before being melted and injected into molds. Additionally, there are heating elements that ensure consistent melting temperatures and clamping units that hold molds securely during the injection process.
Other essential components include the screw mechanism responsible for mixing and conveying the melted plastic as well as temperature control systems that maintain optimal processing conditions. Each component plays a vital role in ensuring that products meet stringent quality standards while adhering to specific injection molding tolerances necessary for effective appliance functionality. Understanding these components helps manufacturers optimize their processes and reduce costs associated with low volume injection molding.
Types of Injection Molding Processes
There are various types of injection molding processes tailored to different production needs within large-scale manufacturing environments. The most common method is conventional injection molding, ideal for high-volume production runs where uniformity is critical; however, alternatives like gas-assisted and foam-injection molding offer unique advantages depending on design requirements and material properties.
Gas-assisted injection molding uses gas pressure during part formation to create hollow sections or reduce material usage while maintaining structural integrity—an excellent choice for lightweight appliance components. On the other hand, low volume injection molding provides flexibility for small batch productions at a lower cost per unit than traditional methods but may require higher initial investment due to mold fabrication expenses.
In summary, understanding these different types allows manufacturers to select the best approach based on their specific needs while keeping an eye on factors like plastic injection molding price and overall efficiency in production cycles.
The Importance of Precision
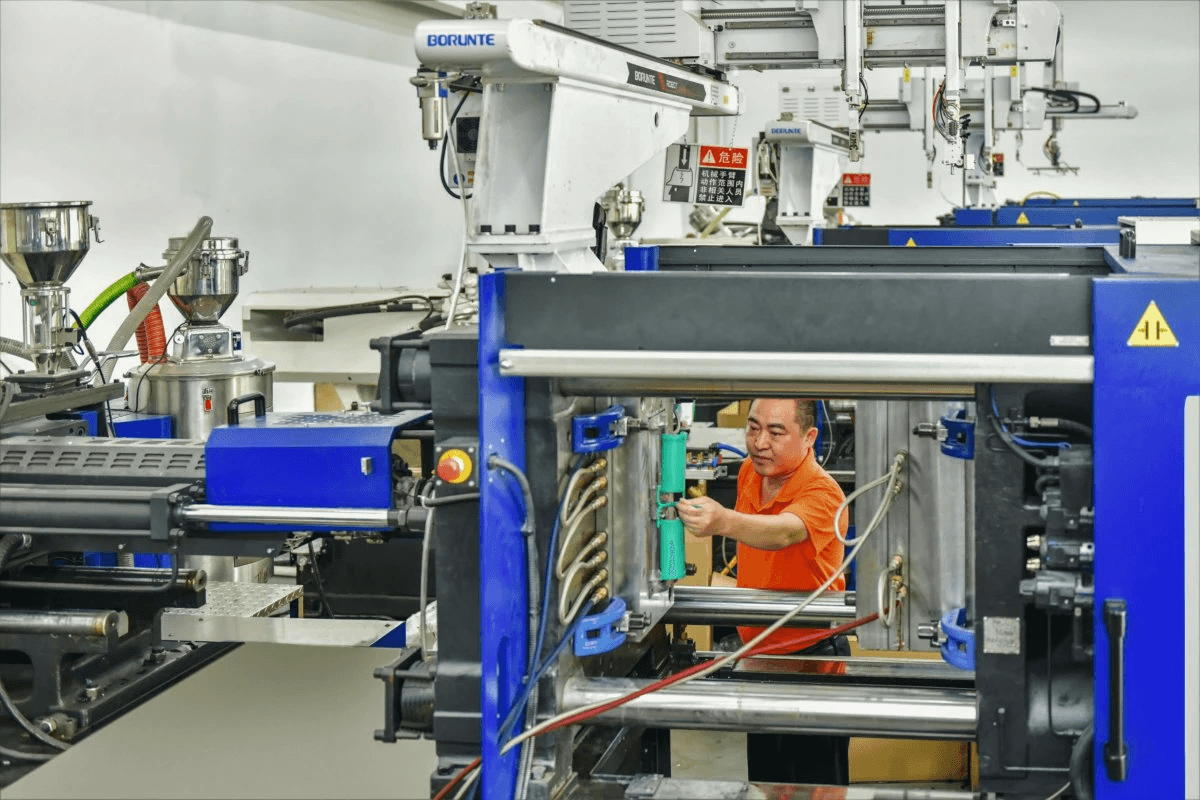
In the world of large-scale manufacturing, precision is not just a luxury; it's a necessity. Injection molding tolerances play a crucial role in determining the quality and functionality of the final product. If these tolerances are not met, manufacturers can face increased costs and reduced efficiency, which can be detrimental in a competitive market.
Injection Molding Tolerances Explained
Injection molding tolerances refer to the allowable variations in dimensions during the production process. These tolerances are essential because they ensure that parts fit together correctly, minimizing issues during assembly and enhancing overall product reliability. In large-scale manufacturing environments, maintaining tight injection molding tolerances can significantly impact production timelines and plastic injection molding prices.
Achieving precise tolerances requires meticulous planning and execution throughout the injection molding process. Manufacturers often invest in high-quality molds and advanced technologies to ensure that their products meet strict specifications. When companies overlook these tolerances, they risk incurring additional costs related to rework or even scrapping entire batches—ultimately affecting their bottom line.
Achieving Quality with the Right Injection Molding Hopper
The choice of an injection molding hopper is pivotal for achieving consistent quality in production runs. An optimal hopper design allows for uniform material flow, which directly influences the accuracy of molded parts and adherence to specified tolerances. In large-scale manufacturing settings, selecting an appropriate hopper can reduce variability and enhance efficiency across multiple production cycles.
Moreover, using high-quality hoppers can minimize issues such as material degradation or inconsistent feeding rates—both of which jeopardize precision during injection molding. By investing in the right equipment upfront, manufacturers can avoid potential pitfalls that lead to increased low volume injection molding costs later on due to defects or inefficiencies. Ultimately, ensuring quality through proper hopper selection is key to maintaining competitive plastic injection molding prices.
Impact of Tolerances on Appliance Efficiency
The impact of injection molding tolerances on appliance efficiency cannot be overstated; it directly affects how well components function together within appliances. When parts are manufactured with precise dimensions, appliances operate more smoothly and reliably over time—leading to enhanced customer satisfaction and fewer warranty claims for manufacturers engaged in large-scale manufacturing operations.
Conversely, poor tolerance management can lead to misalignments or malfunctions within appliances that compromise their performance capabilities. This results not only in customer dissatisfaction but also increases operational costs due to returns or repairs needed for defective products—further driving up overall plastic injection molding prices for manufacturers trying to maintain profitability while addressing quality concerns.
In conclusion, precision through effective management of injection molding tolerances is vital for ensuring efficient appliance performance within large-scale manufacturing contexts; it’s an investment that pays dividends by enhancing product reliability while keeping costs manageable across all stages—from design through production.
Cost Analysis of Injection Molding
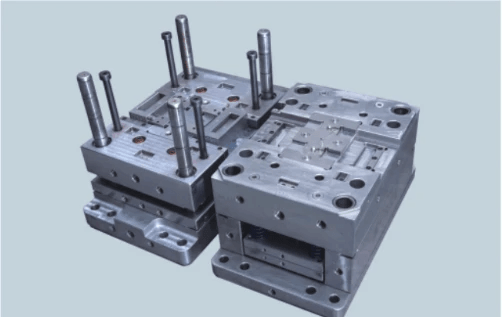
When considering the financial implications of injection molding, it's essential to understand how costs are structured within large-scale manufacturing. The price of plastic injection molding can vary widely based on factors such as material selection, complexity of the part, and production volume. By breaking down these costs into manageable components, manufacturers can make informed decisions that enhance their bottom line.
Evaluating Plastic Injection Molding Price
Evaluating plastic injection molding price requires a keen eye for detail and an understanding of various influencing factors. For instance, the choice of resin and additives can significantly impact overall expenses; high-performance materials typically come with a heftier price tag but may offer long-term savings through durability. Additionally, the intricacies involved in the design phase—such as optimizing injection molding tolerances—can also affect initial costs but lead to more efficient production runs down the line.
In large-scale manufacturing settings, it’s crucial to balance quality with cost-effectiveness when evaluating prices. Investing in an efficient injection molding hopper that ensures consistent material flow can help mitigate waste and reduce overall expenses. Ultimately, a thorough evaluation not only considers immediate costs but also anticipates future savings through improved processes and product longevity.
Breakdown of Injection Mold Price
Understanding the breakdown of injection mold price is vital for manufacturers aiming to optimize their budgets effectively. The mold itself is often one of the largest upfront investments in any injection molding project; it comprises design fees, machining costs, and ongoing maintenance expenses. Each element contributes to the total cost, making it essential for companies engaged in large-scale manufacturing to consider both short-term expenditures and long-term benefits.
Moreover, factors like mold complexity and required precision levels directly influence pricing structures; intricate designs may necessitate higher-quality materials or advanced machining techniques which drive up costs further. In this context, understanding injection molding tolerances becomes paramount—tight tolerances might demand more sophisticated molds that ensure parts fit together perfectly but could also increase initial investment requirements significantly.
By dissecting these components carefully, manufacturers can better strategize their investment in molds while ensuring they remain competitive within their industry.
Understanding Low Volume Injection Molding Cost
Low volume injection molding cost presents a unique challenge for businesses looking to produce smaller quantities without sacrificing quality or efficiency. Unlike traditional large-scale manufacturing processes that benefit from economies of scale, low-volume projects often incur higher per-unit costs due to setup times and mold preparation expenses being spread across fewer items produced. However, this doesn’t mean companies should shy away from low-volume runs; instead, they should approach them with strategic foresight.
Utilizing specialized equipment like an optimized injection molding hopper designed for smaller batches can help mitigate some cost issues associated with lower volumes while maintaining quality standards throughout production runs. Additionally, understanding how different materials impact overall pricing is critical; certain plastics may be more economical than others when produced in smaller quantities due to reduced waste during processing stages.
Ultimately, businesses must weigh these factors carefully against their specific needs—whether they prioritize flexibility or are committed to larger production runs—to find a balance that maximizes profitability while meeting market demands efficiently.
Advantages of Large-Scale Manufacturing
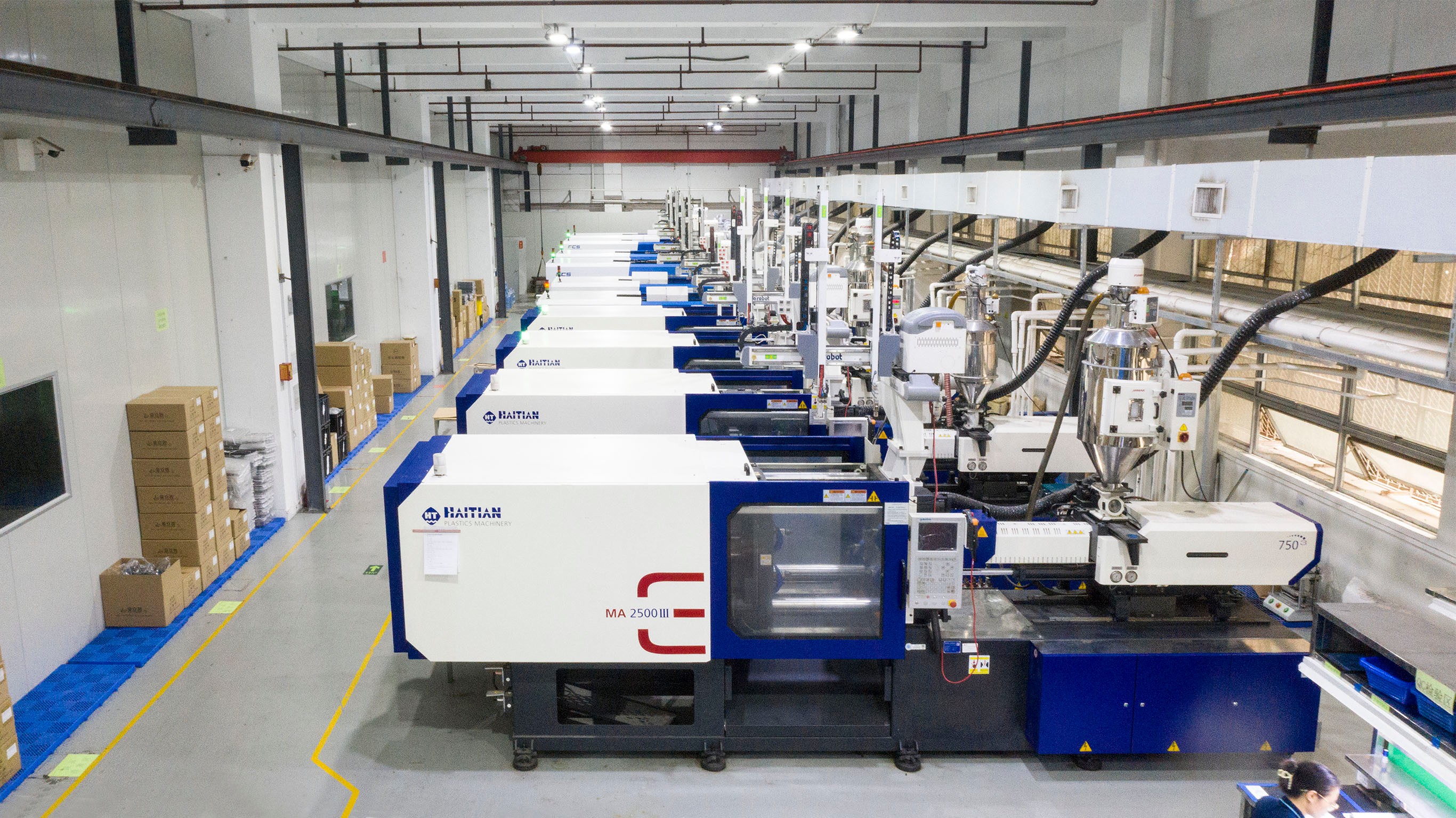
Large-scale manufacturing has revolutionized the way industries produce goods, particularly in the realm of appliances. By leveraging advanced techniques like injection molding, manufacturers can achieve remarkable scalability and efficiency that smaller operations simply cannot match. This not only enhances productivity but also significantly lowers costs, making it a win-win for companies and consumers alike.
Scalability and Efficiency in Production
One of the most compelling advantages of large-scale manufacturing is its inherent scalability. When production ramps up, systems like the injection molding hopper can handle increased output without compromising quality or speed. This efficiency means that as demand grows, manufacturers can quickly adapt their processes to meet consumer needs while maintaining tight injection molding tolerances.
In a large-scale setting, every component is designed for maximum performance. The integration of automation further streamlines operations, allowing businesses to produce more units without sacrificing precision or increasing labor costs significantly. As a result, companies benefit from reduced plastic injection molding prices over time due to economies of scale.
Reducing Production Time with Injection Molding
Injection molding is known for its ability to reduce production time dramatically compared to traditional manufacturing methods. The process allows for rapid cycle times; once the molds are created—often at a competitive injection mold price—manufacturers can churn out thousands of identical parts in mere hours. This speed not only satisfies market demands but also minimizes lead times for new products.
Moreover, with advancements in technology and machinery, even low volume injection molding has become increasingly efficient. Manufacturers can produce smaller batches economically while still benefiting from the precision that comes with high-quality molds. Consequently, this flexibility allows businesses to respond swiftly to market trends without incurring prohibitive costs.
Case Studies in Appliance Manufacturing
To illustrate these advantages effectively, consider several case studies within appliance manufacturing that showcase large-scale production benefits through injection molding techniques. For instance, a leading refrigerator manufacturer implemented an advanced injection molding system that reduced their overall production time by 30%. By optimizing their use of an injection molding hopper and refining their processes around stringent tolerances, they were able to meet rising consumer demands while keeping costs manageable.
Another example involves a company specializing in kitchen appliances that adopted low volume injection molding strategies for new product lines. They found that by investing wisely in high-quality molds at reasonable prices—often lower than expected—they could launch innovative products quickly without incurring excessive overheads associated with traditional methods. These success stories highlight how embracing large-scale manufacturing not only enhances operational efficiency but also positions companies favorably within competitive markets.
The Role of Technology in Injection Molding
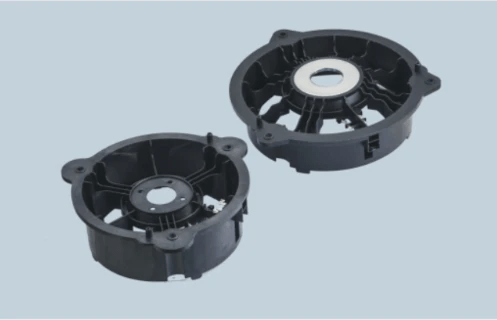
In the fast-paced world of large-scale manufacturing, technology plays a pivotal role in enhancing the efficiency and quality of injection molding processes. The integration of advanced software and expert teams ensures that every component is designed with precision, meeting the stringent injection molding tolerances required for high-performance appliances. By leveraging innovative approaches, manufacturers can significantly reduce costs while maintaining exceptional quality.
Advanced Software in Mold Design
Advanced software solutions have revolutionized mold design in injection molding, allowing for intricate designs that were previously unimaginable. These tools enable engineers to simulate the entire molding process, optimizing parameters such as flow rates and cooling times before any physical mold is created. This not only shortens development timelines but also minimizes potential errors that could lead to increased plastic injection molding prices due to redesigns or modifications.
Moreover, by utilizing sophisticated modeling techniques, manufacturers can better predict how materials will behave during the injection process. This predictive capability helps ensure that the final product meets all specified tolerances and performance standards while also reducing waste—an essential factor in large-scale manufacturing where efficiency is key. With these advancements, companies can confidently invest in new projects knowing they have a reliable design foundation.
The Baoyuan Team's Expertise in Quality Assurance
The Baoyuan team exemplifies how skilled professionals contribute to quality assurance within the injection molding industry. Their extensive experience allows them to implement rigorous testing protocols that ensure each product meets industry standards and customer expectations regarding durability and functionality. By focusing on maintaining tight injection molding tolerances throughout production, they help clients avoid costly recalls or repairs down the line.
Additionally, Baoyuan’s commitment to continuous improvement means they are always on the lookout for ways to enhance their processes further. They utilize feedback from previous projects to refine their approach continually, ensuring that both low volume injection molding cost and large-scale production remain competitive without sacrificing quality. Their expertise not only solidifies their reputation but also provides clients with peace of mind regarding their investments.
Innovations Driving Cost-Effective Production
Innovations in technology are paving new pathways toward cost-effective production methods within large-scale manufacturing environments. From automated systems that streamline workflows to smart sensors monitoring machine performance in real time, these advancements significantly reduce downtime and operational costs associated with traditional practices. As a result, businesses can achieve lower plastic injection molding prices while still delivering top-notch products.
Moreover, emerging technologies such as 3D printing are beginning to play a role alongside conventional methods like injection molding by enabling rapid prototyping at reduced low volume injection molding costs. This flexibility allows manufacturers to test designs quickly without committing extensive resources upfront—perfect for staying agile in an ever-evolving market landscape where consumer preferences shift rapidly. Ultimately, these innovations empower companies not just to keep pace but thrive amid competition.
Conclusion
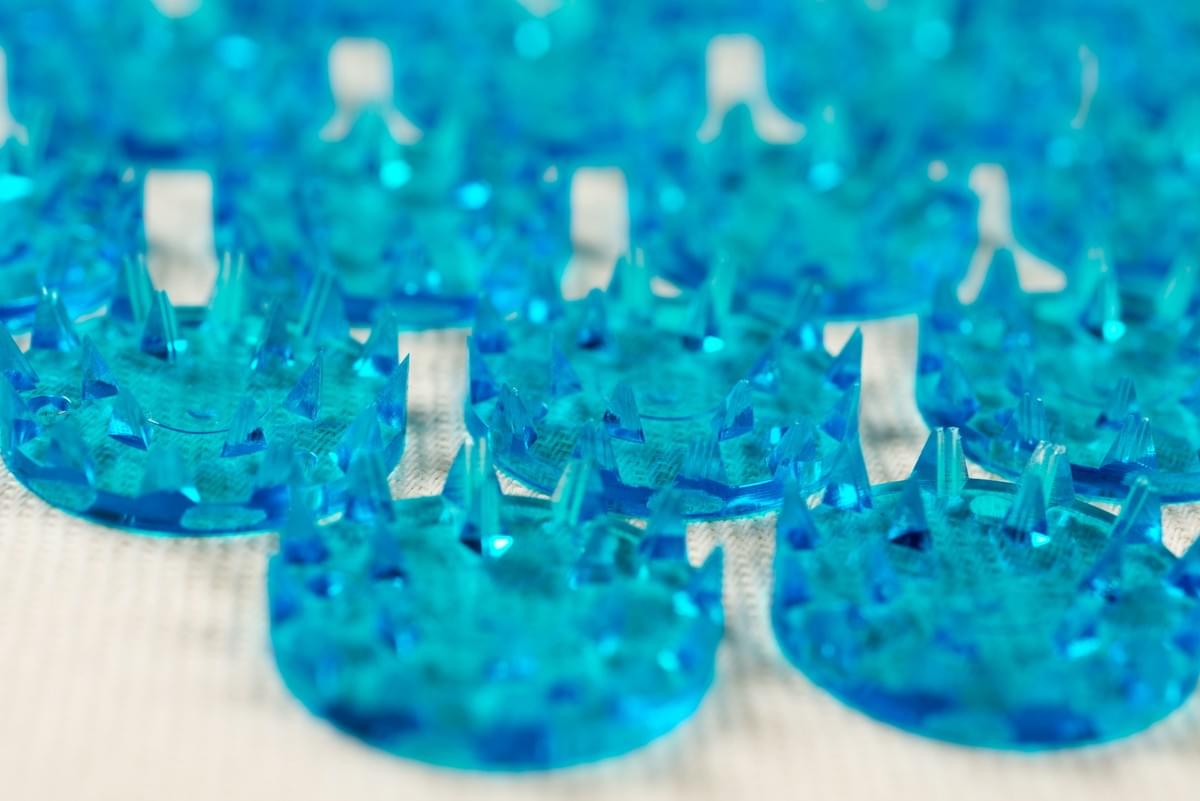
In the rapidly evolving world of large-scale manufacturing, injection molding stands out as a cornerstone of efficiency and precision. By leveraging advanced techniques and technologies, manufacturers can enhance production capabilities while maintaining stringent quality standards. The integration of injection molding not only streamlines processes but also significantly reduces costs associated with appliance production.
Enhancing Production with Injection Molding
Injection molding is revolutionizing the way appliances are produced, ensuring high-volume output without compromising on quality. With the right injection molding hopper, manufacturers can achieve consistent results while adhering to tight injection molding tolerances that are crucial for appliance functionality. This technology allows for rapid prototyping and mass production, making it an indispensable tool in modern manufacturing.
Future Trends in Appliance Manufacturing
Looking ahead, the future of appliance manufacturing is poised for exciting advancements driven by innovation in injection molding techniques. Emerging trends include sustainable materials and smart manufacturing processes that will reshape how products are designed and produced. As manufacturers adapt to these changes, understanding plastic injection molding price structures will become increasingly important to maintain competitiveness.
The Competitive Edge of Large-Scale Manufacturing
Large-scale manufacturing offers distinct advantages that set it apart from traditional methods, particularly in terms of scalability and cost-effectiveness. By analyzing factors such as injection mold price and low volume injection molding cost, companies can identify opportunities for optimizing their production lines. Ultimately, embracing these strategies not only enhances operational efficiency but also solidifies a competitive edge in the marketplace.