Introduction
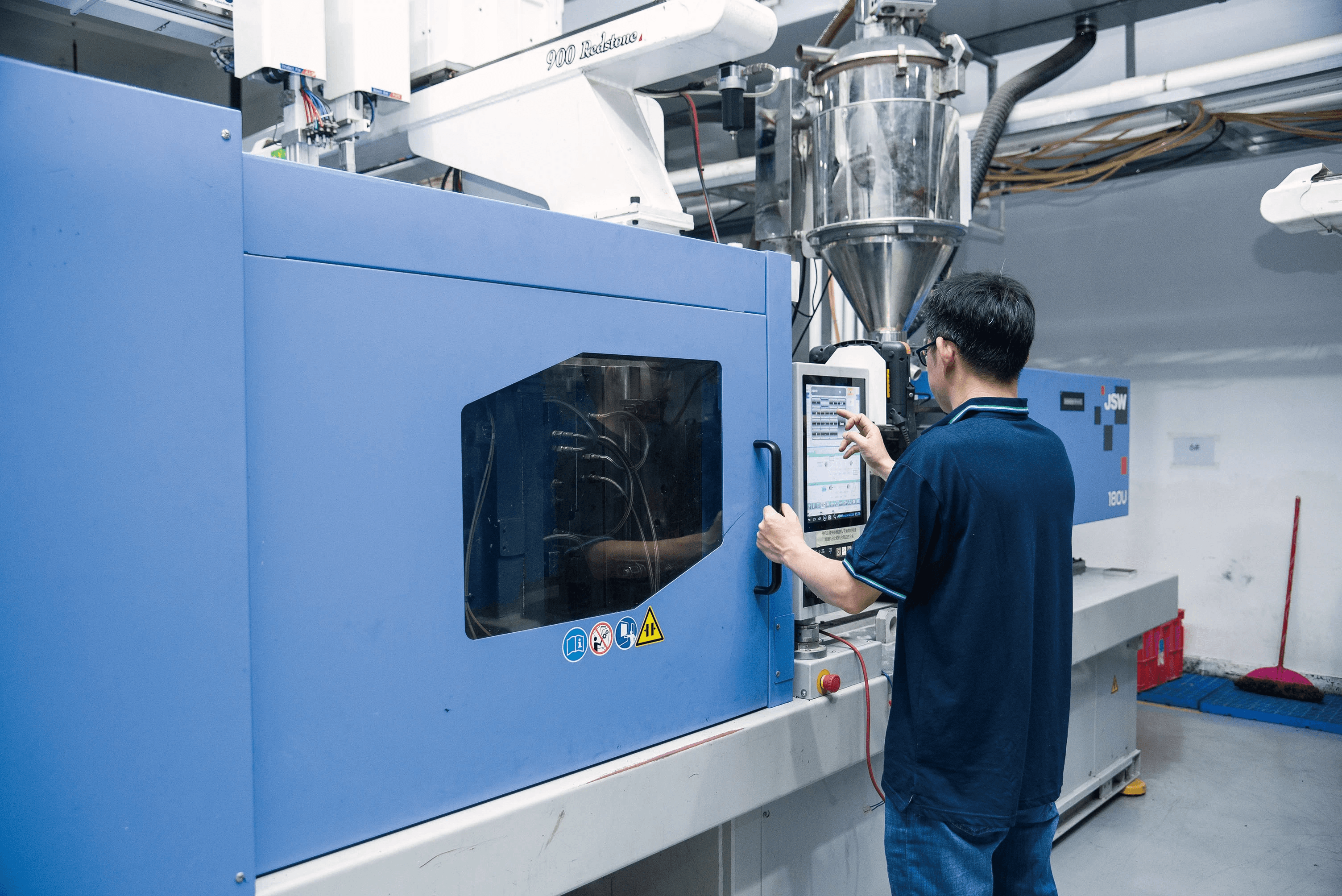
Acrylic injection molding is a fascinating process that has gained significant traction in the manufacturing sector. This technique utilizes polymethyl methacrylate (PMMA), a versatile thermoplastic known for its clarity and durability, making it an excellent choice for custom parts. As we delve into the world of acrylic injection molding, it's crucial to understand not only what it is but also why it stands out among other materials.
Understanding Acrylic Injection Molding
When we talk about acrylic injection molding, we're referring to a specialized method where PMMA is heated until it becomes pliable and then injected into a mold to create various shapes and designs. This process allows manufacturers to produce high-quality components with intricate details and smooth finishes that are difficult to achieve with other materials. So, can acrylic be used for injection molding? Absolutely! Its properties make it an ideal candidate for this technique.
Why Choose PMMA for Custom Parts
One of the primary reasons to choose PMMA for custom parts lies in its exceptional optical clarity, which rivals glass but offers greater impact resistance. Additionally, PMMA can be molded into complex shapes that meet specific design requirements without compromising strength or quality—answering the question: can PMMA be injection moulded? When you choose acrylic injection molding, you're investing in a material that not only looks great but also performs exceptionally well under various conditions.
The Benefits of Acrylic in Manufacturing
Acrylic boasts numerous benefits that make it a preferred choice in manufacturing environments. For starters, it's lightweight yet robust, making products easier to handle while maintaining structural integrity. Furthermore, the versatility of acrylic means that manufacturers often ask themselves: can you inject acrylic? The answer is yes! With its ability to adapt to different applications—from automotive components to consumer products—acrylic continues to revolutionize how we think about custom plastic parts.
What is Acrylic Injection Molding?
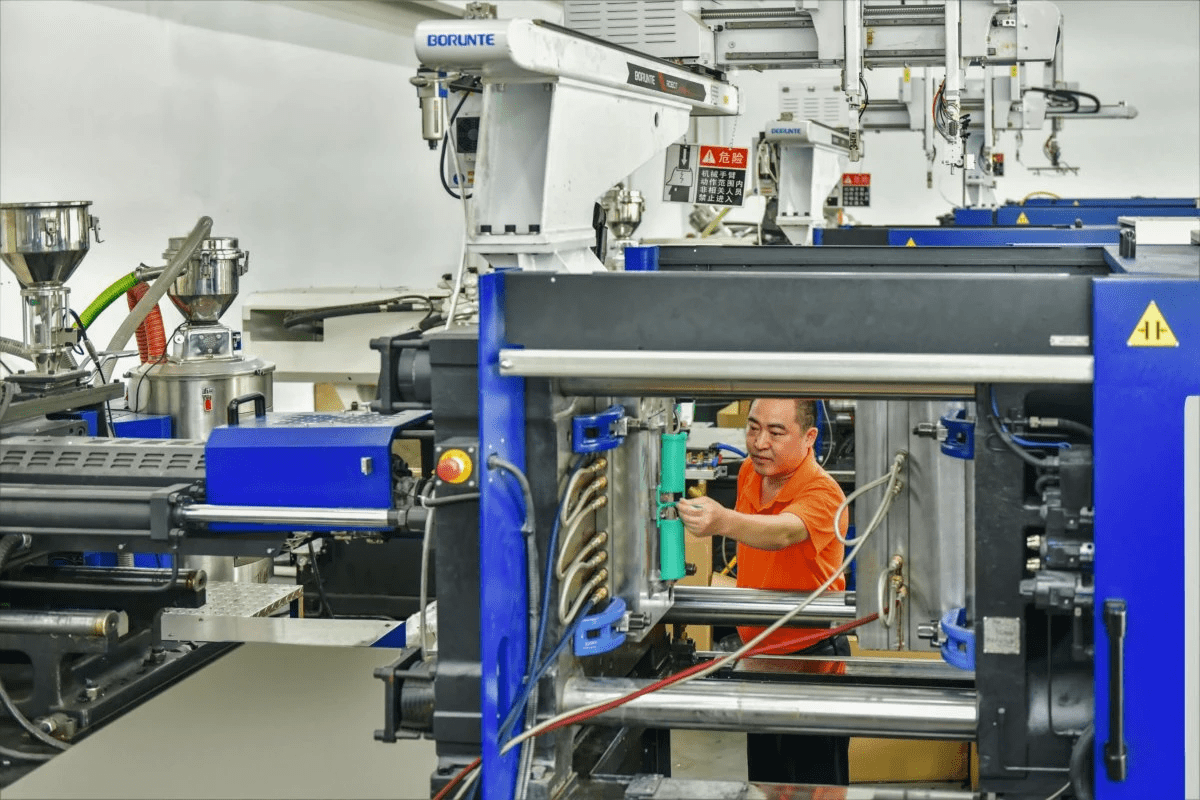
Acrylic injection molding is a manufacturing process that utilizes polymethyl methacrylate (PMMA), commonly known as acrylic, to create custom plastic parts. This technique involves melting acrylic pellets and injecting them into a mold to form various shapes and products. The versatility of acrylic makes it a popular choice for many applications, leading to the question: can acrylic be used for injection molding? The answer is a resounding yes!
Definition and Basics
At its core, acrylic injection molding involves the use of PMMA as a thermoplastic material that can be heated and molded into desired shapes. When heated, PMMA becomes pliable, allowing it to fill intricate molds before cooling and solidifying into durable parts. This process not only ensures high precision but also allows manufacturers to produce complex designs with ease—making it an attractive option in the world of custom manufacturing.
Differences Between Acrylic and Other Plastics
One of the standout features of acrylic compared to other plastics is its exceptional clarity and light transmission properties; in fact, PMMA can transmit up to 92% of visible light! Additionally, unlike some other plastics that may yellow or degrade over time, acrylic maintains its transparency even when exposed to UV light. Furthermore, while many plastics are prone to warping or cracking under stress, can you inject acrylic? Yes! Its inherent strength and resilience make it suitable for demanding applications where durability is crucial.
Applications of Acrylic Injection Molding
Acrylic injection molding finds its way into numerous industries due to its versatility and aesthetic appeal. From automotive components like lenses and dashboards to consumer goods such as display cases or lighting fixtures, the possibilities are virtually endless! Moreover, can PMMA be injection moulded for medical devices? Absolutely! Its biocompatibility allows it to be used in healthcare applications without compromising safety or performance.
Can Acrylic Be Used for Injection Molding?
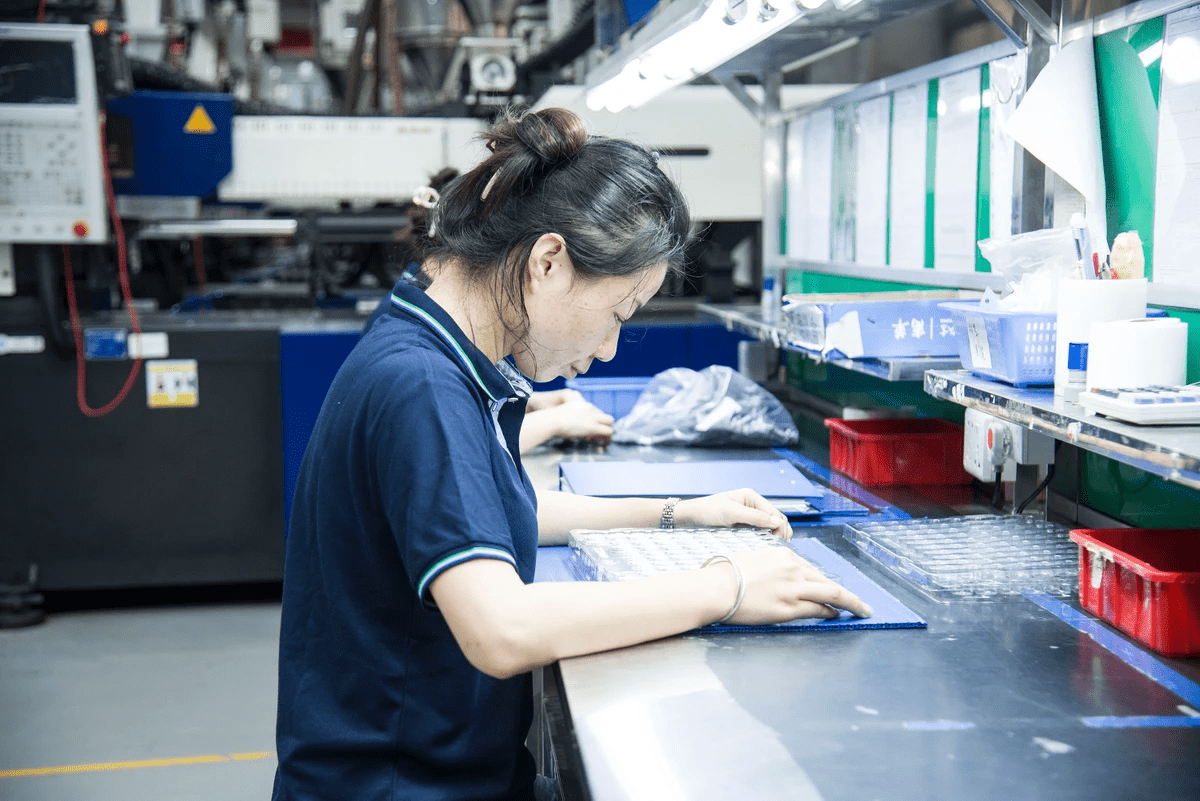
Acrylic, or PMMA (polymethyl methacrylate), is a versatile material that has captured the attention of manufacturers across various industries. The question Can acrylic be used for injection molding? often arises, and the answer is a resounding yes! With its unique properties and adaptability, acrylic injection molding has become a popular choice for producing high-quality custom parts.
Exploring the Versatility of Acrylic
When considering whether can acrylic be molded?, it's important to recognize its versatility in design and application. Acrylic can be shaped into intricate designs that are both functional and aesthetically pleasing, making it an ideal candidate for various products. From automotive components to consumer goods, the ability to inject acrylic into molds allows for endless possibilities in manufacturing.
Moreover, the adaptability of PMMA means it can easily accommodate different colors and finishes, enhancing its appeal in design-centric industries. Whether you're crafting transparent enclosures or colored components, acrylic injection molding provides flexibility that many other materials simply cannot match. This versatility makes it a go-to option for engineers and designers alike.
Material Properties that Make Acrylic Ideal
So what makes PMMA such an attractive option? First off, its excellent clarity rivals glass while remaining significantly lighter—a major plus when weight matters in product design. Additionally, acrylic boasts impressive weather resistance and durability against UV light exposure, making it suitable for both indoor and outdoor applications.
Another key property is its ease of processing; this is where can you inject acrylic? comes into play again! The thermal stability of PMMA allows it to flow smoothly during the injection molding process without losing integrity or quality. This ensures that manufacturers can produce consistent parts with minimal defects—an essential requirement in today’s fast-paced production environments.
Real-World Examples of Acrylic Applications
Real-world applications of acrylic injection molding are as diverse as they are innovative! For instance, many automotive manufacturers utilize PMMA for headlight lenses due to its lightweight nature and superior optical clarity—proving once again that can PMMA be injection moulded? certainly holds true in practical scenarios.
In the world of consumer products, everything from kitchenware to electronic housings often features components made from injected acrylic due to their aesthetic appeal and resilience against wear-and-tear over time. Even medical devices benefit from this adaptable material; clear casings allow visibility while protecting sensitive equipment inside.
As we delve deeper into how can acrylic be used for injection molding?, it's clear that this remarkable material not only meets but exceeds industry expectations across multiple sectors!
The Process Behind Acrylic Injection Molding
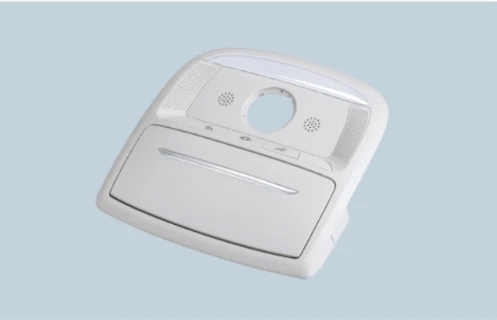
Acrylic injection molding is a fascinating blend of artistry and engineering, resulting in stunning custom parts that meet diverse needs. Understanding the process behind this technique can illuminate why it’s a preferred choice for many manufacturers. Let’s dive into the step-by-step journey of creating high-quality acrylic products.
Step-by-Step Overview of the Process
The journey of acrylic injection molding begins with material preparation, where PMMA (polymethyl methacrylate) granules are dried to remove moisture. This crucial first step ensures that the final product boasts clarity and strength, answering the question: Can PMMA be injection moulded? Next, these granules are heated until they melt into a viscous liquid, ready to be injected into molds under high pressure.
Once injected, the molten acrylic fills every nook and cranny of the mold before cooling and solidifying into its final shape. After cooling, the mold opens to reveal beautifully formed parts—this is where we often ask ourselves: Can acrylic be molded? Finally, any excess material is trimmed away, ensuring precision in every piece produced.
The Role of the Baoyuan Team in Manufacturing
At Baoyuan, our team plays a pivotal role in mastering acrylic injection molding techniques. With years of experience under their belts, they ensure each step—from material selection to final inspection—is executed flawlessly. When clients wonder if they can inject acrylic for their specific applications, our dedicated professionals provide tailored solutions based on industry standards.
Collaboration among engineers and technicians fosters an environment where innovation thrives; we continuously explore new methodologies that enhance efficiency without compromising quality. This teamwork not only addresses common concerns but also reassures clients about our capability to deliver top-notch products consistently.
Importance of Precision in Mold Design
Precision in mold design cannot be overstated when discussing acrylic injection molding; it’s truly at the heart of quality production. A well-crafted mold ensures uniformity across all produced parts while minimizing waste—a crucial factor for any manufacturing process aiming for sustainability. When addressing questions like “Can you inject acrylic?” or “Can acrylic be used for injection molding?”, it's essential to recognize how critical accurate molds are in achieving desired outcomes.
Moreover, precise molds contribute significantly to reducing cycle times and enhancing overall productivity during manufacturing processes at Baoyuan. By investing time and resources into meticulous mold design, we ensure that each custom part meets client specifications while maintaining durability and aesthetic appeal.
Quality Assurance in Acrylic Injection Molding
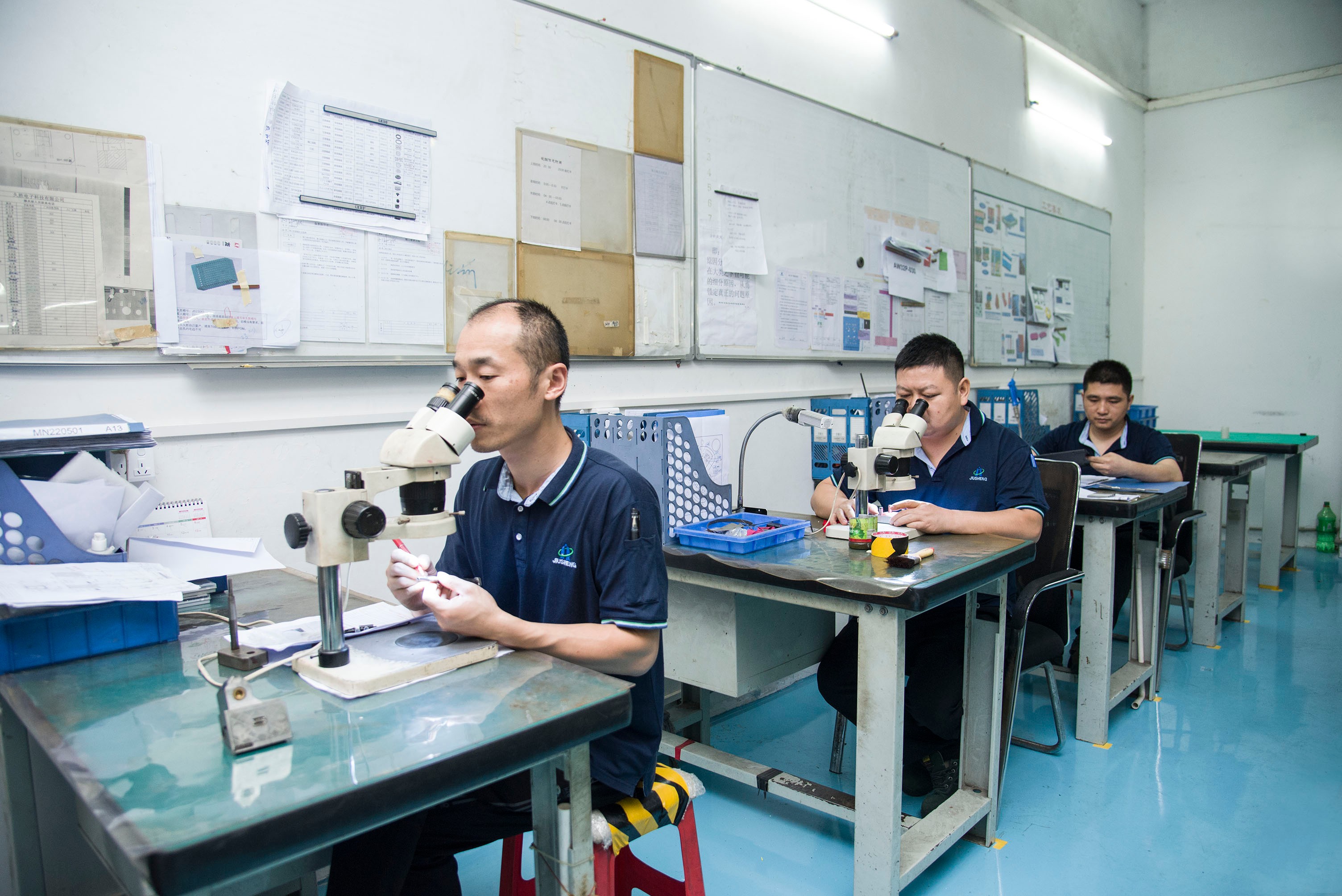
Quality assurance is a cornerstone of the acrylic injection molding process, ensuring that every part produced meets stringent standards for performance and aesthetics. With the unique properties of PMMA (Polymethyl Methacrylate), or acrylic, manufacturers must implement effective techniques to guarantee high-quality outcomes. This section delves into how these techniques are applied and why they matter.
Techniques for Ensuring High-Quality Parts
To ensure high-quality parts in acrylic injection molding, several techniques can be employed throughout the manufacturing process. First, precise temperature control during the injection phase is crucial; it prevents issues like warping or incomplete filling that can arise when the material cools too quickly. Additionally, using advanced mold designs that allow for optimal flow and cooling can significantly enhance the quality of molded parts.
Regular maintenance of machinery used in acrylic injection molding also plays a pivotal role in quality assurance. Well-maintained machines reduce defects caused by wear and tear, ensuring consistent output quality. Furthermore, incorporating real-time monitoring systems allows manufacturers to catch potential issues early on—because nobody wants a surprise when it comes to “Can acrylic be molded?”!
The Role of Quality Control in Manufacturing
Quality control is an integral part of the manufacturing process for acrylic injection molding, acting as a safety net to catch defects before products reach customers. By implementing rigorous inspection protocols at various stages—such as pre-production material checks and post-production evaluations—manufacturers can address concerns like Can PMMA be injection moulded? with confidence.
Moreover, employing statistical process control (SPC) techniques helps maintain consistency across production runs by analyzing data trends over time. This proactive approach not only improves product reliability but also boosts customer satisfaction—a win-win situation! Ultimately, robust quality control measures ensure that every piece produced meets industry standards while addressing common questions like “Can you inject acrylic?” effectively.
How Baoyuan Maintains Industry Standards
At Baoyuan, maintaining industry standards is not just a checkbox; it's embedded in our company culture and operational practices regarding acrylic injection molding. Our team employs state-of-the-art technology combined with experienced personnel who understand the nuances of working with PMMA materials—after all, knowledge is power when answering “Can acrylic be used for injection molding?”
We conduct regular training sessions to keep our staff updated on best practices and innovations within the field of plastic manufacturing. Additionally, Baoyuan adheres strictly to international quality certifications which provide an extra layer of reassurance regarding our processes and products’ integrity. By prioritizing these standards, we ensure that our clients receive nothing less than exceptional results from their custom projects.
Frequently Asked Questions About PMMA
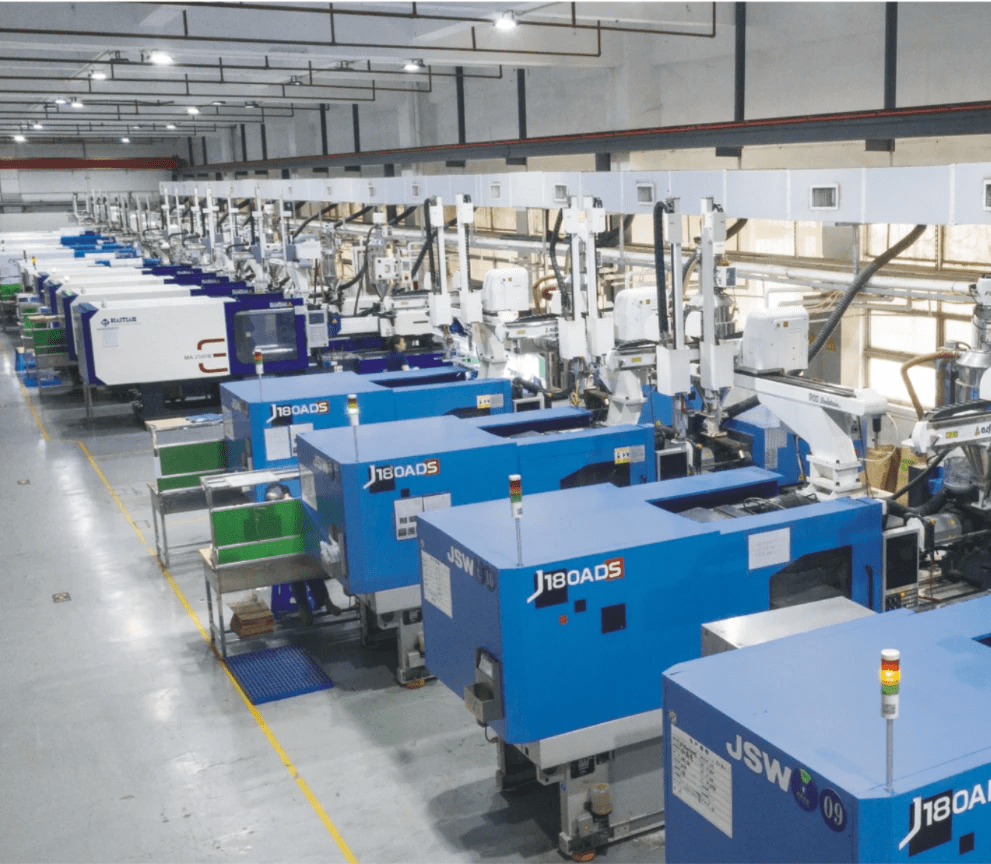
When it comes to acrylic injection molding, questions abound. This section aims to clarify some of the most common inquiries regarding PMMA (polymethyl methacrylate), a popular choice for custom parts. Let's dive into the specifics of using acrylic in injection molding and address any lingering doubts.
Can PMMA Be Injection Moulded?
Absolutely! PMMA is not just a pretty face; it’s a robust material that can be effectively used in acrylic injection molding. The process involves melting the acrylic granules and injecting them into molds, creating precise shapes and designs that are both durable and visually appealing. So, when you ask, “Can PMMA be injection moulded?” rest assured that it’s not only possible but also widely practiced in the industry.
Can You Inject Acrylic?
Yes, you can inject acrylic! The versatility of acrylic makes it an excellent candidate for various manufacturing processes, including injection molding. If you’re wondering whether “can acrylic be molded,” the answer is a resounding yes—this material adapts well to different designs and applications while maintaining its strength and clarity.
Addressing Common Concerns and Misconceptions
There are many misconceptions surrounding acrylic injection molding that can lead to confusion. For instance, some people believe that using PMMA limits design options or compromises quality; however, this couldn’t be further from the truth! In reality, when executed correctly, “can you inject acrylic?” opens up a world of possibilities for creating intricate designs with high-quality finishes.
In summary, whether you're considering custom parts or exploring new manufacturing techniques, understanding these FAQs about PMMA can help ease your concerns about using acrylic in your projects.
Conclusion
In wrapping up our exploration of acrylic injection molding, it’s clear that this process offers unique advantages for creating custom plastic parts. With its versatility and aesthetic appeal, acrylic, or PMMA, stands out as a material that can be molded into various shapes and sizes. Whether you're asking Can acrylic be used for injection molding? or Can PMMA be injection moulded?, the answer is a resounding yes—this method is not only feasible but highly effective.
Key Takeaways on Acrylic Injection Molding
Acrylic injection molding is a powerful technique that brings together the best properties of PMMA to produce high-quality parts with clarity and strength. It’s essential to note that many manufacturers question, “Can you inject acrylic?” The answer is affirmative; not only can you inject it, but doing so allows for intricate designs and functional components tailored to specific applications.
Additionally, one of the standout features of this process is its ability to produce items with excellent optical clarity and durability. As we’ve discussed throughout this guide, understanding whether “can acrylic be molded?” leads us to appreciate the myriad applications across industries—from automotive components to consumer goods. The key takeaway? Acrylic injection molding provides an effective solution for those seeking quality and precision in their custom parts.
The Future of Custom Plastic Parts
Looking ahead, the future of custom plastic parts seems bright, particularly for materials like PMMA in injection molding applications. With advancements in technology and manufacturing processes, we can expect even more innovative uses for acrylic materials in various sectors. As industries strive toward sustainability and efficiency, the question “Can PMMA be injection moulded?” will continue to gain traction as businesses seek eco-friendly solutions without compromising on quality.
Moreover, as designers push boundaries with their creative visions, acrylic's adaptability makes it an ideal candidate for new product development. This evolution paves the way for enhanced functionality while maintaining aesthetic appeal—an essential combination in today’s market landscape. Embracing these trends will allow manufacturers to meet growing consumer demands while exploring novel applications of acrylic injection molding.
Why Partnering with Experts Like Baoyuan Matters
When navigating the world of acrylic injection molding, partnering with experts like Baoyuan can make all the difference in achieving your project goals effectively and efficiently. Their deep knowledge ensures that questions such as “Can you inject acrylic?” are addressed comprehensively while maintaining high standards throughout the manufacturing process. By collaborating with seasoned professionals who understand both material properties and advanced techniques, businesses can confidently move forward knowing they have support every step of the way.
Baoyuan's commitment to quality assurance reinforces its position as a leader in custom plastic part manufacturing—ensuring that each piece meets stringent industry standards without compromise on performance or aesthetics. Ultimately, choosing a knowledgeable partner allows companies to focus on innovation while leaving technical challenges behind them—making success not just possible but inevitable.