Introduction
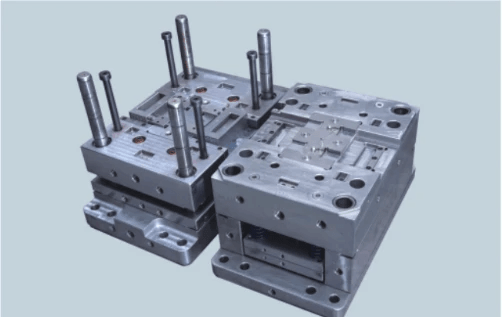
Injection molding is an essential process in manufacturing, allowing for the creation of intricate designs and components with high precision. One of the critical aspects that mold designers need to understand is injection molding undercuts, which can complicate the production process if not addressed properly. By mastering the intricacies of these undercuts, designers can enhance the functionality and aesthetic appeal of their injection molding products.
Understanding Injection Molding Undercuts
Injection molding undercuts refer to features that prevent a molded part from being easily ejected from its mold due to their geometry. These can include grooves, recesses, or other shapes that create a mechanical lock. Understanding how to design around these undercuts is crucial for optimizing both production efficiency and product quality in custom injection molding applications.
The Importance of Precision in Plastic Molding
Precision in plastic molding cannot be overstated; it directly affects product performance and customer satisfaction. In industries such as medical molding, where reliability is paramount, even minor deviations can lead to catastrophic failures or non-compliance with regulations. Therefore, ensuring precision during every phase—from selecting the right plastic molding material to final inspection—is vital for achieving high-quality results.
Techniques for Successful Mold Designs
Successful mold designs require a blend of creativity and technical know-how, particularly when dealing with complex shapes like injection molding undercuts. Techniques such as utilizing advanced simulation software can help visualize potential issues before production begins, saving time and resources later on. Additionally, collaborating with industry experts ensures that best practices are followed throughout the design process, leading to more effective use of injection molding machines and materials.
Mastering Design Planning

Evaluating Injection Molding Products
Evaluating injection molding products involves scrutinizing every aspect from functionality to aesthetics. Designers must consider how features like injection molding undercuts will influence the final product's performance and manufacturability. Additionally, understanding the specific requirements for medical molding applications or other specialized fields helps ensure that the selected plastic molding material meets necessary standards and specifications.
The evaluation process should also include an analysis of potential challenges related to mold design and production processes. Factors such as wall thickness, surface finish, and part geometry play significant roles in determining whether a product can be successfully molded without defects or delays. Ultimately, thorough evaluation leads to better-informed decisions that enhance product quality while minimizing costly revisions later in the process.
Utilizing Simulation Software
In today’s fast-paced manufacturing environment, utilizing simulation software is no longer optional—it's essential for effective design planning in injection molding projects. This software allows designers to visualize how their molds will perform under real-world conditions by simulating flow patterns and identifying potential issues like air traps or insufficient filling related to injection molding undercuts. With accurate simulations, teams can optimize their designs before committing resources to physical prototypes.
Moreover, simulation tools provide valuable insights into cycle times and material usage—crucial factors for any custom injection molding project aiming for efficiency without sacrificing quality. By modeling various scenarios with different plastic molding materials or machine settings, designers can pinpoint optimal strategies tailored specifically for their unique applications. This proactive approach not only saves time but also reduces costs associated with trial-and-error methods.
Collaborating with Experts like Baoyuan
Collaborating with industry experts like Baoyuan can elevate your design planning efforts significantly when tackling complex challenges in injection molding projects. Their extensive knowledge about advanced techniques and technologies ensures that your designs are not only innovative but also practical concerning manufacturing constraints such as clamping force requirements or multi-stage processes specific to medical molding applications. Having access to this level of expertise allows you to avoid common pitfalls associated with poorly planned designs.
Additionally, working closely with experts fosters an environment where knowledge sharing thrives—leading to enhanced creativity and problem-solving capabilities within your team. Whether it’s selecting the right plastic molding material or refining your approach toward managing intricate injection molding undercuts, expert guidance serves as an invaluable resource throughout the entire project lifecycle. Ultimately, collaboration paves the way for achieving high-quality results while maintaining efficiency in custom injection molding endeavors.
Selecting the Right Plastic Molding Material
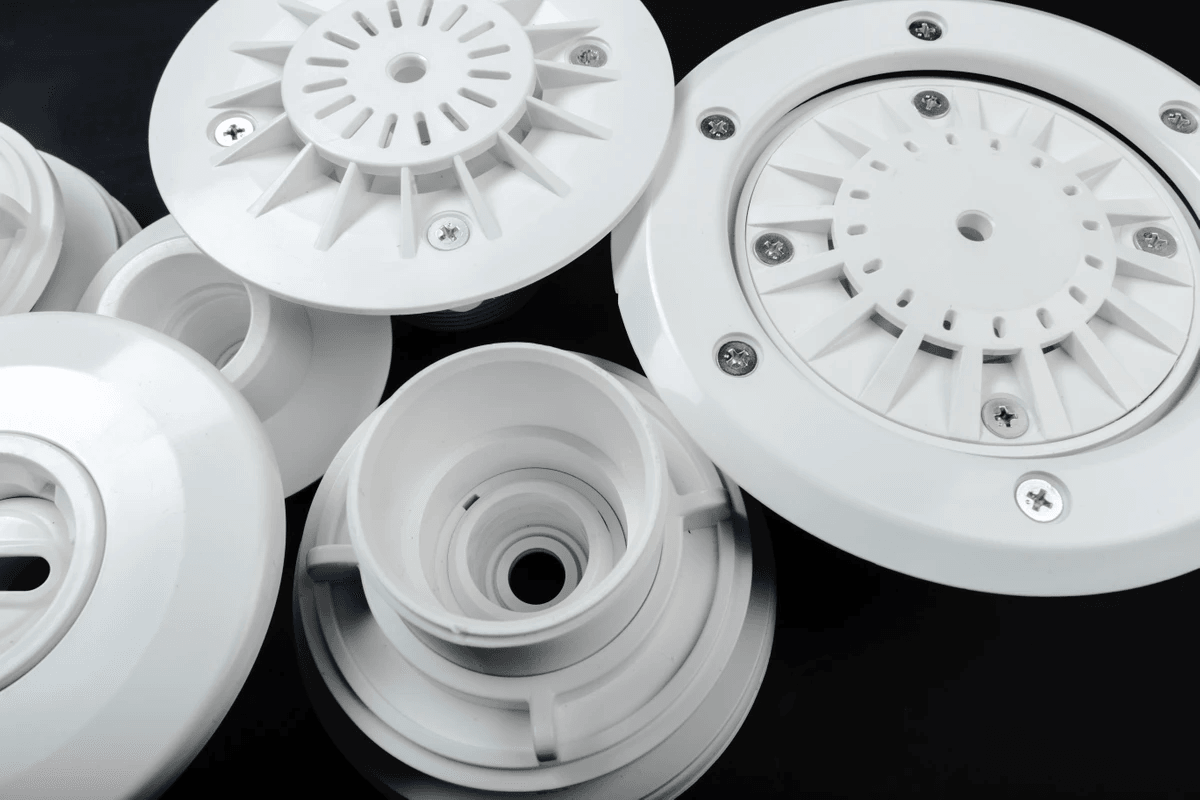
Choosing the right plastic molding material is crucial for achieving optimal results in injection molding, especially when dealing with complex designs that incorporate injection molding undercuts. The properties of different materials can significantly influence not only the performance of the final product but also the efficiency of the entire injection molding process. Understanding these properties helps mold designers make informed decisions that enhance product quality and reduce production costs.
Comparing Material Properties
When comparing material properties for injection molding products, it’s essential to consider factors such as strength, durability, flexibility, and temperature resistance. For instance, thermoplastics like ABS offer excellent impact resistance and are commonly used in a variety of applications, while polycarbonate is known for its high toughness and transparency—making it ideal for medical molding. Additionally, understanding how these materials behave during the injection casting process can help predict potential issues related to shrinkage or warping that might affect intricate features like undercuts.
Material selection also involves weighing cost against performance; some high-performance polymers may come with a premium price tag but could save money in the long run by reducing defects and improving cycle times. Furthermore, specific applications may require compliance with industry standards or regulations, particularly in sectors such as medical devices where safety is paramount. Therefore, a thorough comparison of material properties is essential to ensure that custom injection molding meets both functional and regulatory demands.
Custom Injection Molding Considerations
Custom injection molding often requires specialized materials tailored to unique specifications or end-use requirements. This customization can involve selecting specific additives or blends to enhance certain characteristics—such as flame retardancy for electrical components or biocompatibility for medical applications. When designing molds with complex geometries or undercuts, it’s critical to choose a plastic molding material that not only meets these specifications but also flows well during processing.
Moreover, designers should consider how various materials interact with different types of injection molding machines; some machines may be optimized for certain resins while others might struggle with them due to viscosity differences during melting and cooling phases. Collaborating closely with material suppliers can provide insights into which combinations yield optimal results while minimizing production challenges associated with custom designs. Ultimately, thoughtful consideration of material choices leads to better-performing products that stand out in competitive markets.
Impact on Injection Molding Undercuts
Injection molding undercuts present unique challenges during mold design and manufacturing processes; thus, selecting an appropriate plastic molding material can significantly impact their feasibility and execution. Materials with higher flow rates tend to fill intricate mold cavities more effectively, reducing instances where undercuts become trapped within molds—thereby enhancing overall production efficiency. However, overly rigid materials may complicate demolding processes if they grip onto undercut features too tightly.
Additionally, understanding how different materials respond to cooling rates is crucial when dealing with undercuts; slower-cooling resins might shrink unevenly around complex geometries leading to potential defects such as warping or misalignment post-mold release. This makes it vital for designers to balance performance attributes against processing characteristics when considering how various plastic types will handle intricacies inherent in their designs—especially those involving challenging features like undercuts found in many modern products today.
Advanced Injection Molding Machine Features
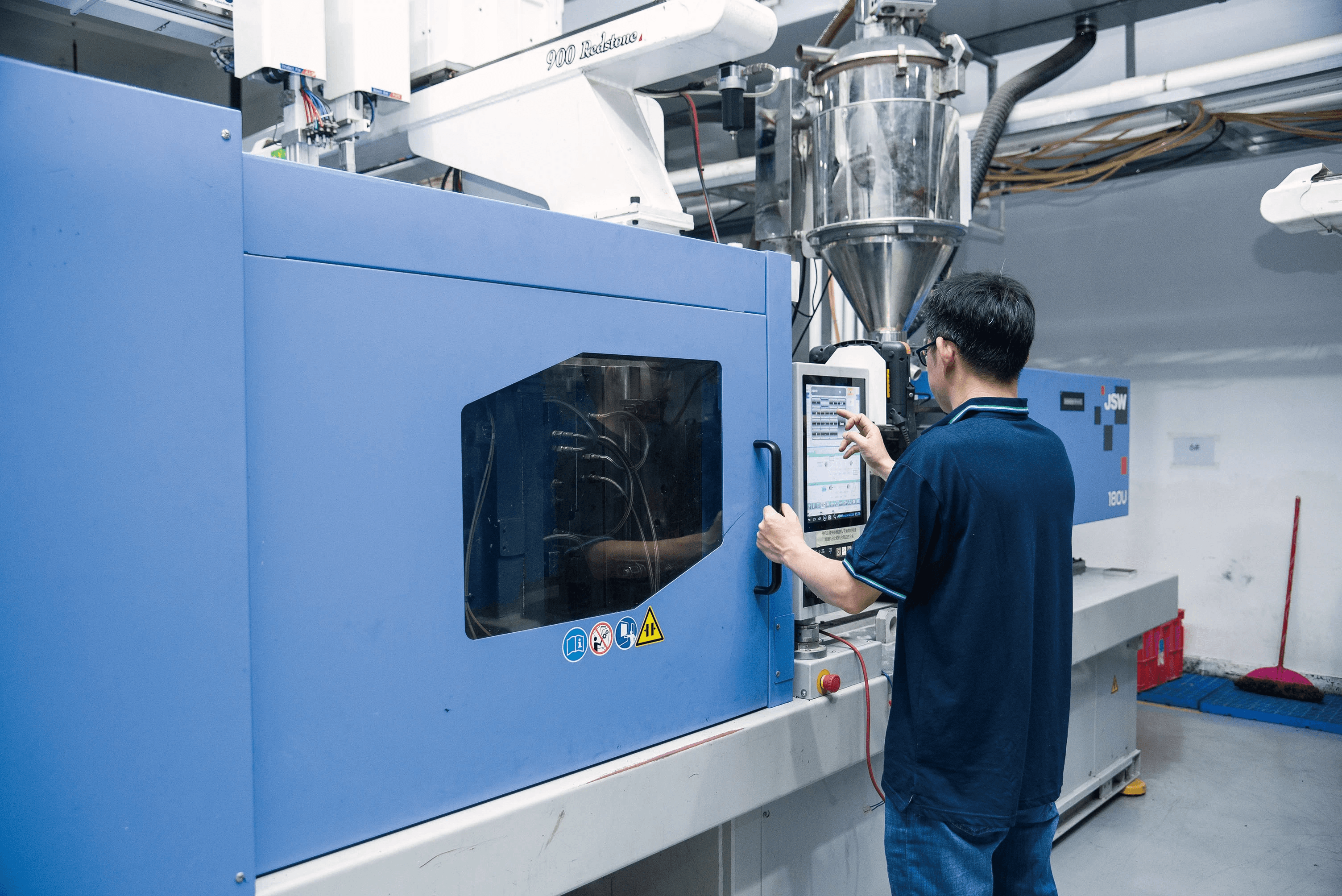
In the world of injection molding, advanced machine features can significantly enhance the production of complex designs, particularly when dealing with injection molding undercuts. These features not only improve efficiency but also ensure precision in the final product. By understanding and utilizing these capabilities, manufacturers can optimize their custom injection molding processes to meet diverse market demands.
Incorporating Multi-Stage Processes
Multi-stage processes in injection molding machines allow for greater flexibility and complexity in design execution, especially when creating intricate injection molding products with undercuts. By integrating multiple stages of material introduction or varying pressures, manufacturers can achieve superior surface finishes and reduce the risk of defects that often plague simpler methods. This approach is particularly beneficial in medical molding applications where precision is paramount and any deviation could compromise product integrity.
Moreover, multi-stage processes enable the use of different plastic molding materials within a single part, facilitating unique color combinations or varying material properties that enhance functionality. For instance, a product could feature a rigid outer layer combined with a softer inner core—ideal for ergonomic designs. By mastering these multi-stage techniques, companies can stand out in a competitive landscape while effectively addressing customer needs.
Importance of Clamping Force
Clamping force is another crucial aspect to consider when optimizing an injection molding machine for undercuts and complex geometries. Proper clamping ensures that the mold remains securely closed during the injection process, preventing leaks and ensuring uniform filling of the cavity with plastic molding material. Insufficient clamping force may lead to defects such as flash or incomplete parts—issues that are particularly concerning in high-stakes industries like medical manufacturing.
Understanding how to calculate and adjust clamping force based on part size and geometry is essential for successful custom injection molding projects. Manufacturers should also consider the relationship between clamping force and cycle time; too much force may slow down production while too little could compromise quality. Thus, finding the right balance is key to maximizing efficiency without sacrificing precision.
Optimizing Cycle Times for Undercuts
Optimizing cycle times is critical when working with injection molding undercuts since these features often complicate traditional processing methods. Efficient cycle times not only enhance productivity but also reduce operational costs—an essential consideration for any manufacturer aiming to remain competitive in today’s fast-paced market environment. Implementing advanced technologies such as real-time monitoring systems can provide insights into bottlenecks within production cycles.
Moreover, understanding how different factors like cooling time and mold design impact overall cycle time allows manufacturers to make informed adjustments tailored to specific projects involving custom injection molding or medical applications. For example, using advanced cooling channels can drastically reduce cooling time without compromising part quality—especially important when producing large volumes of intricate parts with undercuts. Ultimately, optimizing cycle times leads to improved throughput while maintaining high standards for quality assurance across all products.
Implementing Effective Mold Making Techniques
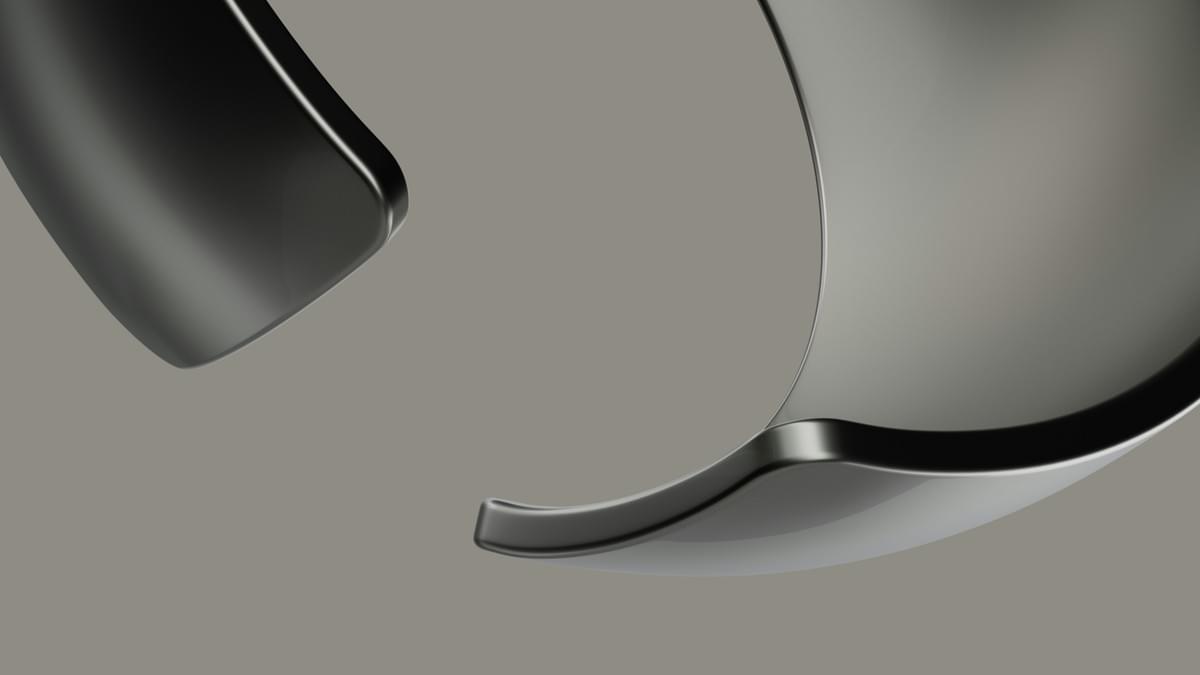
In the realm of injection molding, mastering mold making techniques is crucial for producing high-quality products, especially when dealing with intricate designs. Effective strategies not only enhance the functionality of injection molding undercuts but also improve overall production efficiency. By focusing on innovative mold-making methods, manufacturers can ensure that their injection molding products meet rigorous industry standards.
Strategies for Complex Geometries
When it comes to complex geometries in injection molding, a well-thought-out design strategy is essential. Utilizing advanced CAD software allows designers to visualize and refine their molds before production begins, minimizing errors associated with injection casting. Additionally, incorporating features like collapsible cores or lifters can effectively manage undercuts while maintaining the integrity of the mold structure.
Moreover, understanding the flow properties of different plastic molding materials helps in selecting the right material for intricate designs. Designers must consider how each material behaves during the injection process and how it influences cooling times and shrinkage rates. Ultimately, a strategic approach to complex geometries can lead to more efficient manufacturing processes and superior end products.
Benefits of Double-Color Molding
Double-color molding offers a unique advantage in custom injection molding by allowing manufacturers to produce parts with multiple colors or materials in a single cycle. This technique not only enhances aesthetic appeal but also improves functionality by combining different material properties within one product—perfect for applications like medical molding where specific characteristics are required. By streamlining production processes, double-color molding reduces waste and lowers costs associated with secondary operations.
Furthermore, this method can help simplify assembly processes by creating parts that fit together seamlessly without additional fastening elements. The ability to incorporate various textures or finishes adds another layer of customization that can set products apart in competitive markets. Ultimately, embracing double-color molding can lead to innovative solutions that cater to diverse consumer needs while optimizing manufacturing efficiency.
Quality Assurance Practices
Quality assurance practices are paramount in ensuring that every aspect of the injection molding process meets stringent quality standards—especially when dealing with critical applications like medical devices or components requiring precise dimensions due to injection molding undercuts. Regular inspections throughout the production cycle help identify potential issues early on, allowing for timely adjustments before mass production begins. Employing statistical process control (SPC) techniques further enhances quality management by monitoring key variables in real-time.
Implementing thorough testing protocols on finished products ensures they meet all specifications and regulatory requirements prior to market release. This includes evaluating mechanical properties and conducting stress tests on various plastic molding materials used during production. A commitment to rigorous quality assurance not only safeguards product integrity but also reinforces customer trust in your brand's reliability.
Leveraging Industry Innovations
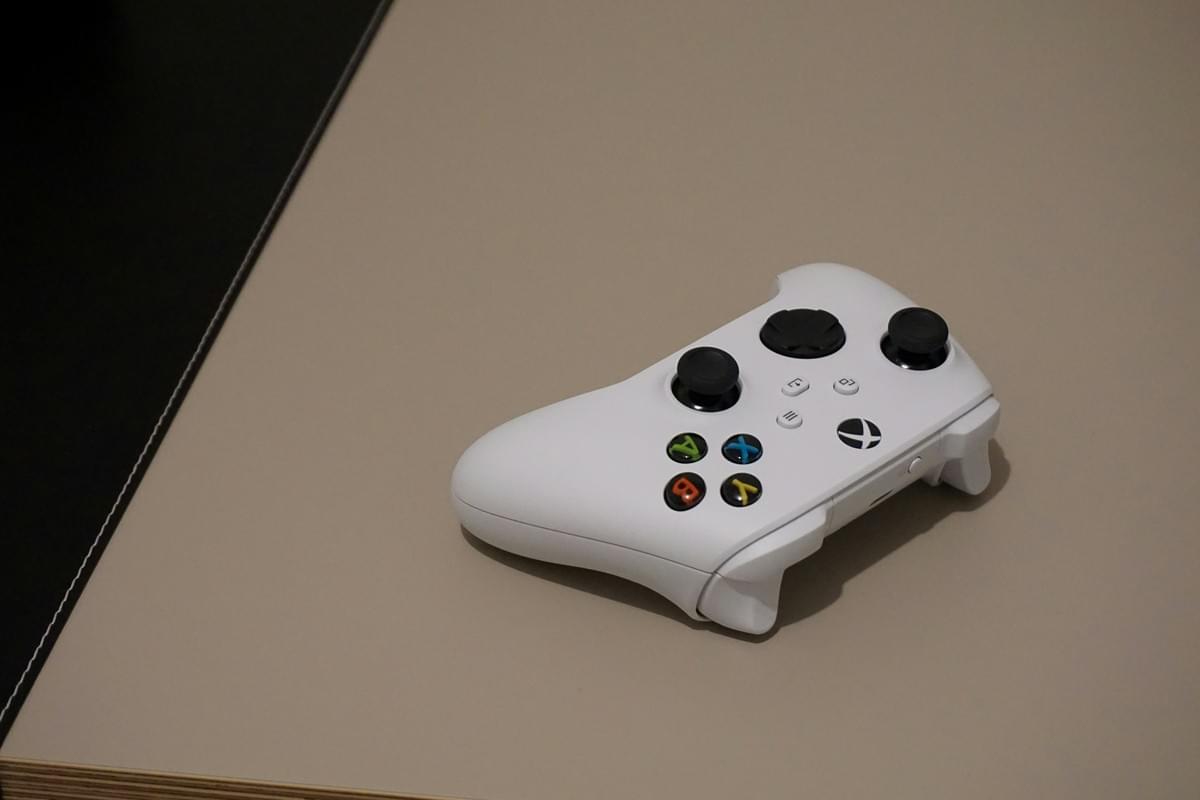
In the ever-evolving world of injection molding, innovation is key to staying ahead. As the demand for precision and efficiency grows, particularly in sectors like medical molding, companies must adapt by embracing new technologies. From advanced machinery to novel materials, leveraging these innovations can significantly enhance the production of injection molding products.
New Technologies in Medical Molding
The medical industry has seen remarkable advancements in injection molding technologies that cater specifically to its stringent requirements. New techniques such as micro-injection molding enable the creation of intricate components with exceptional precision, ideal for devices like syringes and implants that require tight tolerances. Furthermore, advancements in plastic molding material allow for biocompatible options that ensure safety and efficacy in medical applications, which is crucial when designing products with injection molding undercuts.
With the integration of automation and robotics into medical molding processes, manufacturers can achieve higher production rates while maintaining quality standards. Automated inspection systems are also being implemented to monitor each stage of production closely, ensuring that any defects are caught early on. This combination of technology not only streamlines workflows but also elevates the overall reliability and performance of custom injection molding solutions.
Cost-Effective Solutions for Custom Injection Molding
Cost management is a significant concern for manufacturers looking to optimize their custom injection molding operations without sacrificing quality. One effective approach involves using simulation software during the design phase to predict how different designs will perform before committing to production. This proactive strategy helps identify potential issues related to injection molding undercuts or complex geometries early on, ultimately saving time and resources.
Additionally, adopting lean manufacturing principles can lead to substantial cost reductions by minimizing waste throughout the production process. By focusing on efficient use of materials and energy within an injection molding machine's operation, companies can significantly cut down on expenses while increasing output quality. The result? More competitive pricing for clients seeking high-quality injection casting services without breaking the bank.
Future Trends in Injection Molding
Looking ahead, several trends are shaping the future landscape of injection molding that manufacturers should keep an eye on. One promising development is the rise of sustainable practices within plastic manufacturing; eco-friendly materials are gaining traction as consumers demand greener products without compromising performance or durability in their favorite injection molded items. This shift towards sustainability may influence choices regarding plastic molding material used in various industries.
Moreover, advancements in digital manufacturing technologies—such as 3D printing—are beginning to complement traditional methods like custom injection molding rather than replace them entirely. These innovations offer flexibility in prototyping and small-scale production runs while maintaining cost-effectiveness and efficiency over time. Ultimately, staying informed about these trends will empower mold designers and manufacturers alike to adapt their strategies effectively.
Conclusion
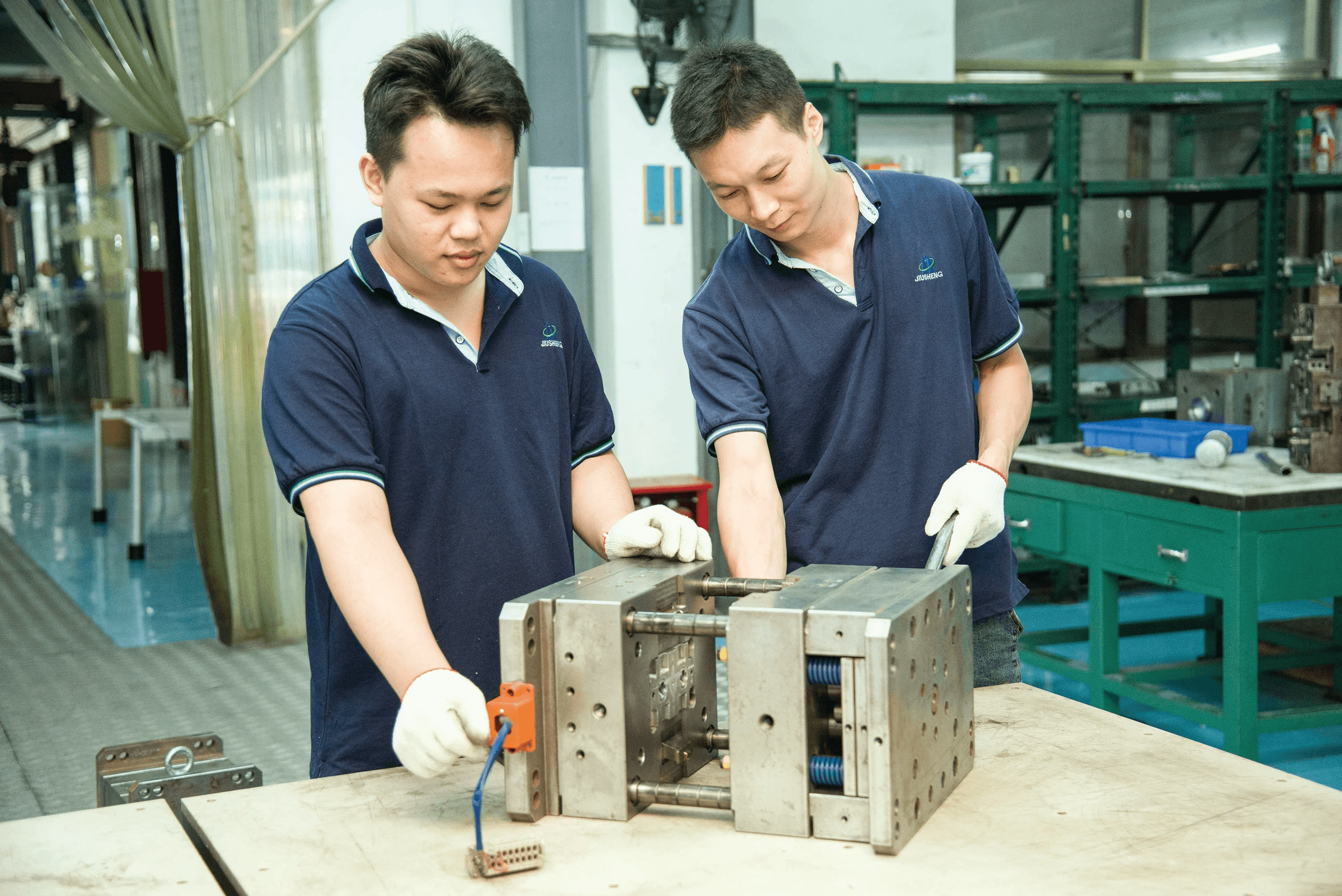
In the intricate world of injection molding, understanding the nuances of injection molding undercuts is paramount for mold designers. The journey from conception to production hinges on a blend of creativity, technical knowledge, and precision. By mastering these elements, designers can create superior injection molding products that meet industry standards and client expectations.
Key Takeaways for Mold Designers
Mold designers should prioritize a thorough evaluation of injection molding products to ensure they align with project specifications. Understanding the properties of various plastic molding materials is crucial; different materials can significantly impact the final product's performance and manufacturability. Additionally, employing advanced techniques such as simulation software can help visualize potential challenges with injection molding undercuts early in the design process.
Emphasizing the Role of Precision
Precision in custom injection molding cannot be overstated—it's the difference between success and costly errors. Even minor deviations can lead to significant issues during production, especially when dealing with complex geometries or medical molding applications where accuracy is critical for functionality and safety. Therefore, investing time in perfecting designs ensures that every detail aligns perfectly with specifications, thereby enhancing overall product quality.
Continuous Learning in Injection Molding
The landscape of injection casting continues to evolve rapidly, making continuous learning essential for professionals in this field. Staying updated on new technologies and methodologies not only improves individual skills but also benefits entire teams by fostering innovation within projects involving injection molding undercuts or other complexities. As trends shift towards more sustainable practices and advanced machinery features, embracing lifelong learning will empower mold designers to remain competitive and effective in their craft.