Introduction
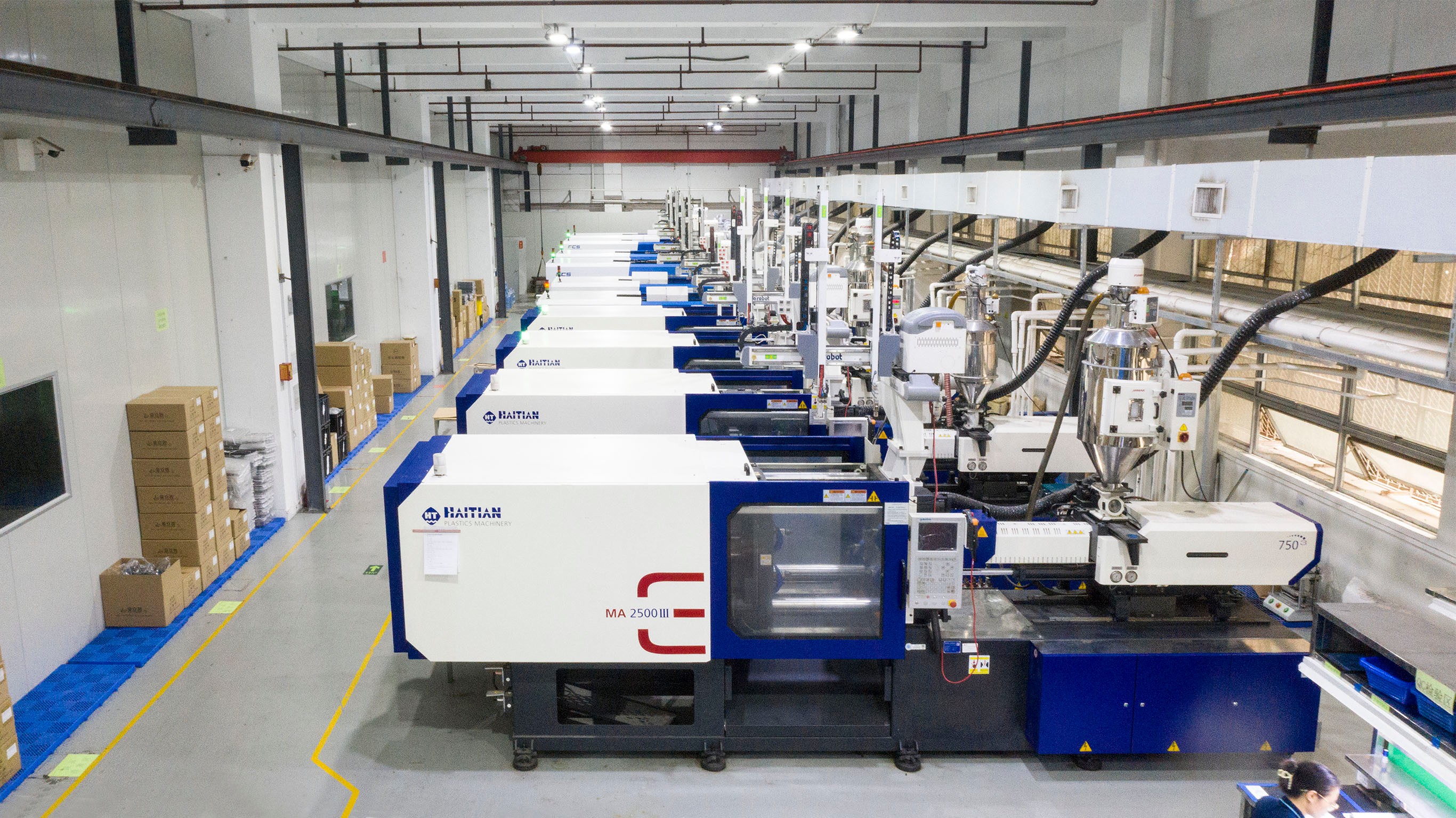
Are you curious about the intricate process of plastic part manufacturing? From injection moldable plastics to plastic extrusion, there's a world of innovation behind the scenes. In today's modern manufacturing landscape, plastics play a pivotal role in shaping our everyday lives. And when it comes to expertise in plastic manufacturing, Baoyuan leads the way with unrivaled precision and proficiency.
Understanding Plastic Part Manufacturing
The art of plastic part manufacturing involves various processes such as injection molding, blow molding, compression molding, and extrusion molding. Each method requires specialized knowledge and skill to create high-quality plastic parts that meet industry standards.
The Role of Plastics in Modern Manufacturing
Plastics have revolutionized modern manufacturing by offering versatility, durability, and cost-effectiveness. From automotive components to medical devices, plastics are indispensable in creating a wide range of products that enhance our daily lives.
Baoyuan: Leading the Way in Plastic Manufacturing Expertise
As one of the top molding companies in the industry, Baoyuan stands out for its cutting-edge technology and unwavering commitment to excellence. With a focus on injection moldable plastics and state-of-the-art equipment, Baoyuan is at the forefront of delivering top-notch solutions for all your plastic manufacturing needs.
Injection Molding Process
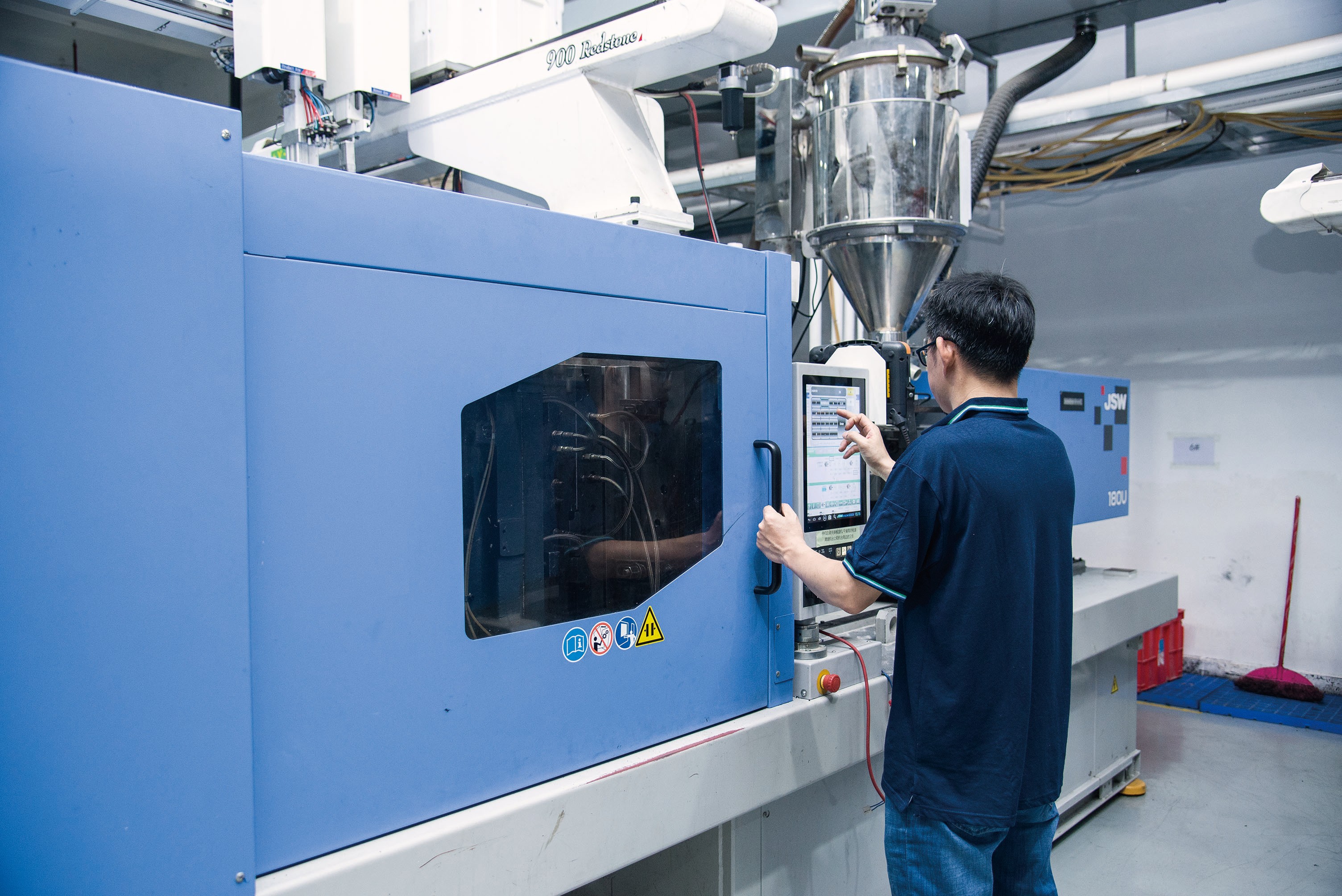
When it comes to plastic part manufacturing, injection molding is a game-changer. Baoyuan is at the forefront of this technology, with expertise in handling a wide range of injection moldable plastics. Their state-of-the-art facilities and skilled workforce ensure that your plastic parts are manufactured with precision and efficiency.
Baoyuan's Expertise in Injection Molding
Baoyuan stands out among other molding companies as a leader in plastic injection molding. Their team of experts has extensive experience in mold plastic injection, allowing them to deliver high-quality products that meet the most stringent industry standards. From concept to production, Baoyuan is your trusted partner for all your plastic manufacturing needs.
Key Steps in Injection Molding
The injection molding process involves several key steps, including clamping, injection, cooling, and ejection. Baoyuan's streamlined approach ensures that each step is meticulously executed to produce flawless plastic parts. With their cutting-edge technology and attention to detail, they can handle complex designs and tight tolerances with ease.
Advantages and Limitations of Injection Molding
One of the main advantages of injection molding is its ability to produce large volumes of identical parts with high precision at a low cost per unit. However, it may not be suitable for small-scale production or prototyping due to the initial investment required for tooling and setup. Despite these limitations, Baoyuan's expertise in injection molding allows them to optimize the process for maximum efficiency.
Baoyuan's commitment to excellence sets them apart from other injection molding companies in the industry. With their unparalleled expertise and dedication to customer satisfaction, they are the ideal choice for all your plastic manufacturing needs.
Blow Molding Process
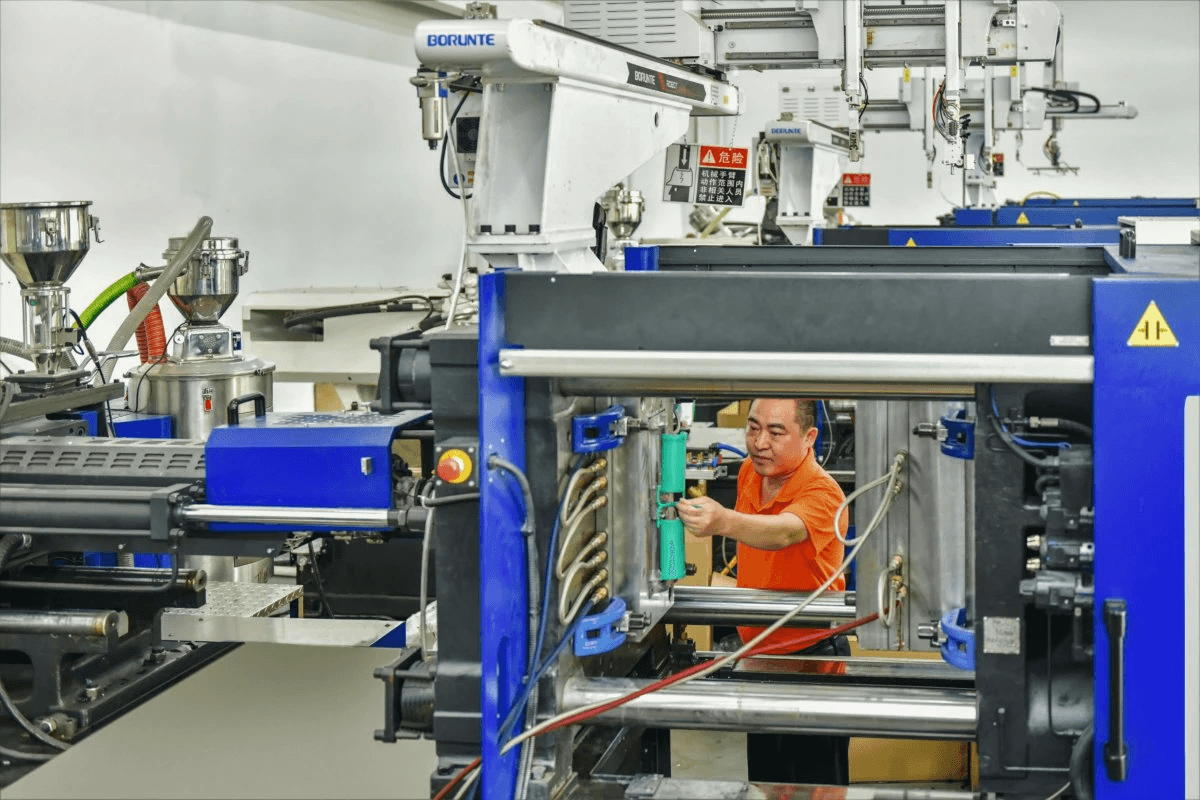
Baoyuan's Specialization in Blow Molding
When it comes to plastic part manufacturing, Baoyuan stands out for its specialization in blow molding. With state-of-the-art equipment and a team of experienced professionals, Baoyuan is able to produce high-quality plastic parts through the blow molding process.
Key Steps in Blow Molding
The blow molding process involves melting down injection moldable plastics and then shaping them into a hollow form using compressed air. The key steps include parison extrusion, mold closing, blowing and cooling, and part ejection. This process allows for the creation of seamless and lightweight plastic parts.
In addition to creating seamless and lightweight plastic parts, blow molding also offers the advantage of producing complex shapes and designs that may be difficult or impossible to achieve with other manufacturing processes. This makes it a versatile option for a wide range of industries, from automotive to packaging. Furthermore, blow molding allows for cost-effective production of large quantities of identical parts, making it an efficient choice for mass production. With its ability to create high-quality, durable products at a low cost, blow molding is a popular choice in the manufacturing world.
Advantages and Limitations of Blow Molding
One advantage of blow molding is its ability to produce complex shapes with ease, making it ideal for manufacturing items such as bottles, containers, and automotive components. However, limitations include the need for uniform wall thickness and limited material options compared to other plastic manufacturing processes.
Additionally, blow molding is a cost-effective manufacturing process, as it requires minimal tooling and setup compared to other methods. This makes it an attractive option for businesses looking to produce large quantities of plastic parts without breaking the bank. The ability to quickly and efficiently create complex shapes also contributes to the overall cost savings, as less time and labor are required for production.
By specializing in blow molding, Baoyuan ensures that clients receive top-notch plastic parts that meet their specific requirements while benefiting from the advantages this process offers.
Compression Molding Process
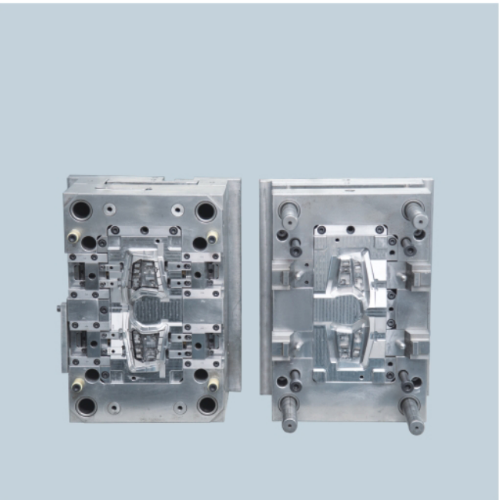
Baoyuan's Proficiency in Compression Molding
When it comes to plastic part manufacturing, Baoyuan stands out for its proficiency in compression molding. With years of experience and cutting-edge technology, Baoyuan has mastered the art of creating high-quality plastic parts through compression molding. Their expertise in this process ensures that they can meet the diverse needs of their clients with precision and efficiency.
With a state-of-the-art facility equipped with advanced machinery and technology, Baoyuan is able to produce plastic parts of various sizes and complexities through compression molding. Their ability to handle a wide range of materials and produce intricate designs sets them apart from their competitors. This ensures that clients can rely on Baoyuan for all their compression molding needs, no matter how challenging.
Key Steps in Compression Molding
The key steps in compression molding involve placing a heated plastic material into an open, heated mold cavity. The mold is then closed with a top force or plug member, causing the plastic to compress and fill the mold cavity. The pressure and heat are maintained until the plastic has cured, ensuring that the final product is formed with accuracy and durability.
Advantages and Limitations of Compression Molding
Compression molding offers several advantages, including the ability to create complex shapes with excellent surface finish and dimensional stability. However, it may not be suitable for high-volume production due to its slower cycle times compared to other molding processes such as injection molding.
While compression molding offers the advantage of creating complex shapes with excellent surface finish and dimensional stability, it may not be the best choice for high-volume production. The slower cycle times of compression molding can lead to longer lead times and increased production costs, making it less suitable for mass production compared to other molding processes like injection molding. This limitation should be carefully considered when deciding on the most appropriate manufacturing method for a specific product.
Extrusion Molding Process
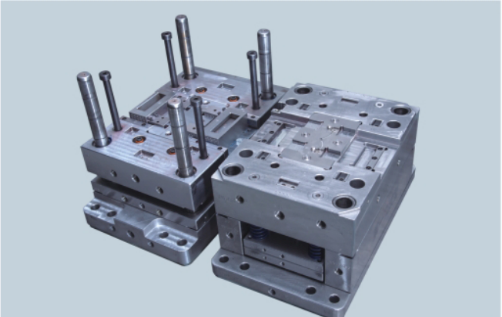
Baoyuan's Excellence in Extrusion Molding
At Baoyuan, we take pride in our excellence in plastic extrusion molding. With state-of-the-art equipment and a team of skilled technicians, we ensure that every plastic part manufactured through extrusion molding meets the highest quality standards. Our meticulous attention to detail and rigorous quality control processes guarantee that each product meets the exact specifications and requirements of our clients. In addition, our commitment to continuous improvement means that we are always exploring new technologies and techniques to further enhance the precision and efficiency of our extrusion molding processes.
Key Steps in Extrusion Molding
The key steps in plastic extrusion molding involve heating the raw material to a molten state, forcing it through a die to create the desired shape, and then cooling and cutting the formed part to the required length. This process allows for the creation of continuous shapes with consistent cross-sections.
After the plastic material is heated to a molten state, it is forced through the die, which can be customized to produce a wide variety of shapes and sizes. This flexibility makes extrusion molding suitable for a range of applications, from simple plastic tubes to more complex profiles and components. Additionally, the continuous nature of the process means that large volumes of parts can be produced with high efficiency, making it a cost-effective manufacturing method for many industries.
Advantages and Limitations of Extrusion Molding
One of the main advantages of extrusion molding is its ability to produce complex shapes with high precision and consistency. However, it may not be suitable for producing intricate designs or parts with varying wall thicknesses due to limitations in die design.
Remember that at Baoyuan, we are dedicated to providing top-notch plastic manufacturing services using various processes such as injection moldable plastics, mold plastic injection, and plastic extrusion molding to meet your specific needs.
Rotational Molding Process
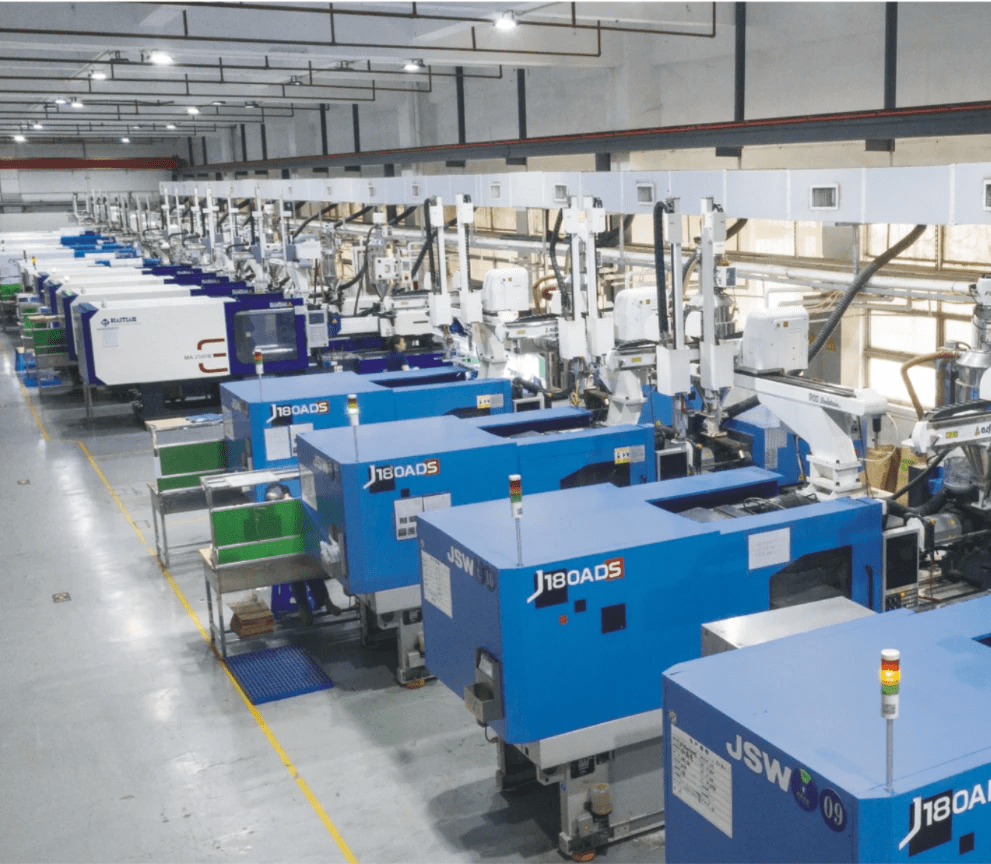
Baoyuan's Precision in Rotational Molding
At Baoyuan, we take pride in our precision in rotational molding, offering top-notch expertise in creating high-quality plastic parts. Our team of skilled professionals ensures that every step of the rotational molding process is executed with utmost accuracy and attention to detail, resulting in flawless end products. Our state-of-the-art equipment and advanced technology enable us to achieve consistent wall thickness and intricate designs, giving our clients the assurance of top-quality products every time. Additionally, our commitment to sustainability means we prioritize eco-friendly materials and processes, ensuring that our precision in rotational molding is not only high-quality but also environmentally responsible.
Key Steps in Rotational Molding
The rotational molding process involves several key steps, including loading the mold with the raw material, heating it until it melts and coats the mold's interior, cooling the mold to solidify the material, and finally removing the finished product. Baoyuan's state-of-the-art equipment and advanced techniques enable us to carry out each step seamlessly, guaranteeing superior results.
In addition to the key steps mentioned above, it's important to highlight the versatility of rotational molding. This manufacturing process allows for the production of complex shapes and designs that may be difficult or impossible to achieve with other methods. This flexibility opens up a world of possibilities for product designers and engineers, enabling them to create innovative and unique products that stand out in the market.
Advantages and Limitations of Rotational Molding
When it comes to plastic part manufacturing, rotational molding offers numerous advantages such as design flexibility, cost-effectiveness for large parts, and excellent impact resistance. However, it also has limitations including longer cycle times and limited material options compared to other molding processes. Our expertise at Baoyuan ensures that we maximize the benefits while mitigating any drawbacks of rotational molding.
Conclusion
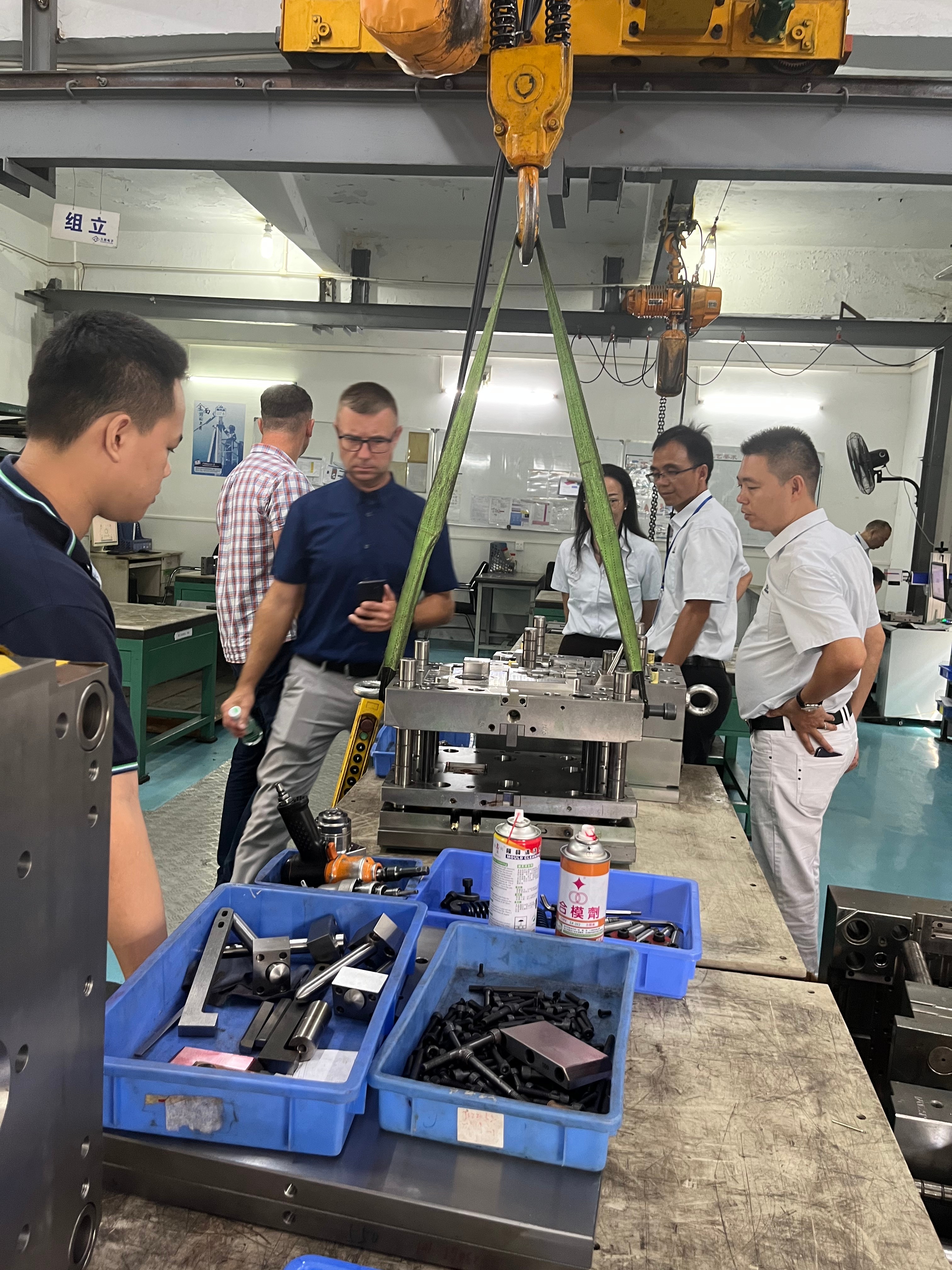
Choosing the Right Manufacturing Process for Your Plastic Part
When it comes to plastic part manufacturing, it's crucial to choose the right process for your specific needs. Whether you require injection moldable plastics or plastic extrusion, finding a reliable partner with expertise in various molding processes is key to ensuring the success of your project. Additionally, it's important to consider factors such as production volume, material selection, and cost-effectiveness when deciding on the manufacturing process. Working with a knowledgeable partner like Baoyuan can help you navigate these considerations and make informed decisions for your plastic part production.
Baoyuan: Your Trusted Partner in Plastic Manufacturing
Look no further than Baoyuan for all your plastic manufacturing needs. As one of the leading molding companies, Baoyuan specializes in injection molding, plastic extrusion, and more. With a proven track record of delivering high-quality products, you can trust Baoyuan to bring your vision to life.
Mastering the Art of Plastic Part Manufacturing
Mastering the art of plastic part manufacturing requires a deep understanding of various molding processes and their advantages and limitations. With Baoyuan's expertise in mold plastic injection and other techniques, you can rest assured that your project is in capable hands.
Mastering the art of plastic part manufacturing also involves staying updated on the latest industry trends and technological advancements. Baoyuan prides itself on keeping abreast of these developments, ensuring that your project benefits from the most cutting-edge techniques and materials available. By choosing a manufacturer with a finger on the pulse of innovation, you can be confident that your plastic parts will meet and exceed industry standards.