Introduction
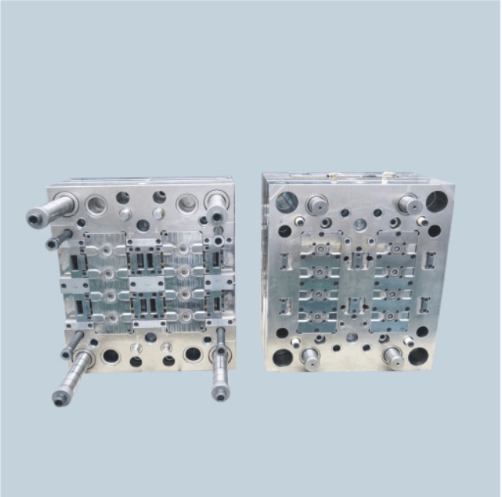
Injection molding is a fascinating process that transforms raw plastic into intricate parts and components, but what often goes unnoticed are the various injection molding gate types that play a crucial role in this transformation. Understanding these gate types can significantly enhance the efficiency and quality of the molded products. From sprue gates to pin gates, each type has its own unique functionalities, advantages, and applications that can influence the final outcome of your project.
Understanding Injection Molding Gate Types
So, what are the types of gates used in injection molds? The answer lies in an array of choices including sprue gates, edge gates, fan gates, pin gates, and submarine gates. Each injection molding gate type serves a specific purpose during the molding process, affecting how the material flows into the mold cavity and ultimately determining product characteristics such as surface finish and structural integrity.
Key Functions of Gates in Molding
Gates serve several key functions in injection molding beyond merely allowing molten plastic to enter the mold. They control material flow rates, influence cooling times, and help manage pressure within the mold cavity during production. A well-designed gate can minimize defects such as warping or uneven filling while maximizing efficiency—qualities that every designer aims for when selecting their injection molding gate design.
Importance of Gate Design Choices
Choosing the right gate is not just a matter of preference; it’s integral to achieving high-quality results in your molded parts. For instance, understanding what is the difference between fan gate and edge gate can help you decide which option best suits your specific application needs. The importance of making informed decisions on injection molding gate types cannot be overstated—getting it right at this stage can save time and resources down the line.
Sprue Gate
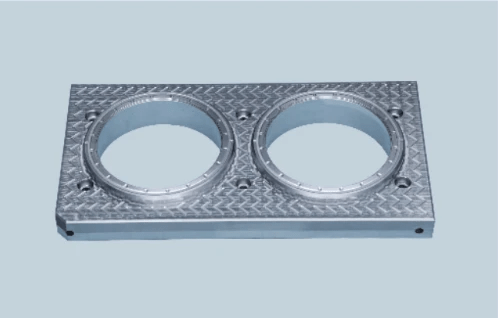
Injection molding gate types are crucial in determining how plastic flows into a mold, with the sprue gate being one of the most fundamental designs. This type of gate allows molten material to enter the cavity through a single, vertical channel known as the sprue. Understanding what a sprue gate is and how it functions helps designers make better choices in their projects.
Definition and Functionality
A sprue gate is essentially a direct channel that connects the injection molding machine nozzle to the mold cavity. It serves as an entry point for molten plastic, which then fills up the mold before cooling and solidifying into the desired shape. The functionality of a sprue gate is straightforward; it enables efficient filling while minimizing potential defects in the final product.
Advantages and Disadvantages
When comparing injection molding gate types, sprue gates come with their own set of advantages and disadvantages. One significant advantage is that they can handle high flow rates, making them suitable for large parts or complex geometries. However, they also have downsides; for instance, they can leave behind larger scars on parts where they connect to the molded item, which may not be ideal for aesthetic applications.
Common Applications in Molding
Sprue gates are commonly used in various applications across different industries due to their simplicity and effectiveness. They are particularly prevalent in molding larger components like automotive parts or industrial equipment where speed is essential. Additionally, when considering what are the types of gates used in injection molds?, it's clear that sprue gates play a vital role due to their ability to efficiently fill molds without excessive complexity.
Edge Gate
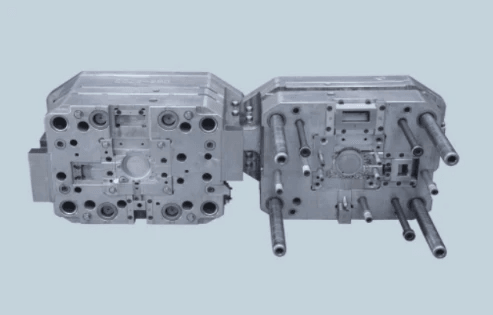
Edge gates are a popular choice in the realm of injection molding gate types, serving as a crucial component in the production process. They are positioned along the edge of a mold cavity, allowing for efficient material flow while minimizing issues like warping and sink marks. This design not only enhances the aesthetic quality of molded parts but also optimizes production efficiency.
What is an Edge Gate?
An edge gate is a specific type of injection molding gate that connects the runner system to the part cavity at its edge. This design facilitates a more controlled fill of the mold, reducing potential defects caused by uneven material distribution. By strategically placing these gates, manufacturers can ensure better surface finish and dimensional accuracy in their final products.
Comparing Edge Gate with Fan Gate
When comparing edge gate with fan gate, several differences come to light that can influence your choice for specific projects. The fan gate typically spreads out material flow over a wider area, which can be beneficial for certain shapes but may lead to issues like excessive flash or increased cycle times. In contrast, edge gates offer more precision and control over filling dynamics, making them ideal for applications where detail is paramount.
What are the types of gates used in injection molds? While both edge and fan gates have their merits, understanding their unique characteristics allows designers to make informed decisions based on project requirements.
Use Cases in Product Design
Edge gates find application across various industries due to their versatility and effectiveness in injection molding gate design. They are particularly suited for thin-walled parts or components requiring high cosmetic standards since they help maintain part integrity during cooling. Industries such as automotive, consumer goods, and electronics frequently utilize edge gates to achieve optimal performance while keeping manufacturing costs manageable.
In summary, if you're exploring different injection molding gate types for your next project—whether it be sprue gates or pin gate injection molding—consider how an edge gate might fit into your overall design strategy. Their strategic placement can significantly enhance product quality while ensuring efficient production processes that meet industry standards.
Fan Gate
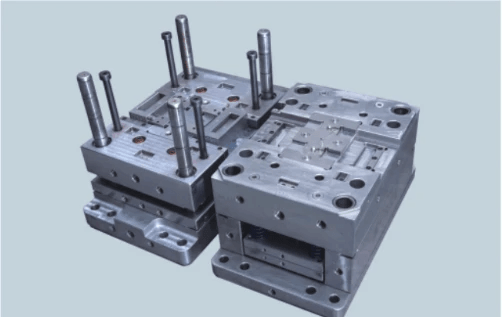
Fan gates are a popular choice among injection molding gate types due to their unique design and functionality. They allow for a wide and uniform flow of molten plastic, which helps minimize issues like weld lines and air traps in the final product. Understanding fan gates is crucial for anyone looking to optimize their injection molding process.
Exploring the Fan Gate Design
The fan gate design resembles a fan blade, spreading the molten material across a wider area before it enters the mold cavity. This shape enables better filling of complex geometries while reducing internal stresses that could lead to defects in molded parts. When considering what are the types of gates used in injection molds, the fan gate stands out for its ability to improve flow characteristics significantly.
One of the key features of fan gates is their ability to accommodate varying wall thicknesses, making them ideal for intricate designs. The wider entry point facilitates quicker filling times, which can enhance overall production efficiency. In essence, this design not only optimizes material flow but also contributes to more consistent part quality.
Differences from Sprue and Edge Gates
When comparing fan gates with sprue and edge gates, several differences emerge that can influence your choice depending on application needs. A sprue gate feeds directly into the mold through a single channel, whereas an edge gate typically runs along the edge of the part’s surface but may not distribute material as evenly as a fan gate does. What is the difference between fan gate and edge gate? The primary distinction lies in how each distributes material; while edge gates may create localized stress points, fan gates promote even distribution across larger areas.
Moreover, sprue gates can sometimes lead to excess material being wasted due to their direct feed method; this is less pronounced with fan gates since they utilize a broader entry point for improved efficiency. Edge gates often require additional trimming or finishing work post-molding due to their placement on part edges—something that isn’t typically necessary with well-designed fan gates. Ultimately, these differences make understanding various injection molding gate types essential for selecting the right one based on specific project requirements.
Ideal Scenarios for Use
Fan gates shine in scenarios where mold filling speed and uniformity are paramount—think large parts or components with complex geometries that need consistent quality throughout. Industries such as automotive or consumer electronics frequently leverage this type of gate design because it allows them to produce high-quality products efficiently without compromising structural integrity or aesthetics. Where are the gates for injection molding? Fan gates are often strategically placed at locations on molds where optimal flow paths can be achieved.
In addition to automotive applications, these versatile gateways find utility in producing thin-walled components or items requiring precise detail without sacrificing strength—like medical devices or intricate housings for electronics. Their ability to mitigate issues related to air entrapment makes them particularly suitable when working with materials prone to such defects during cooling phases as well. Thus, understanding when and how best to employ a fan gate can significantly enhance your overall production outcomes.
Pin Gate
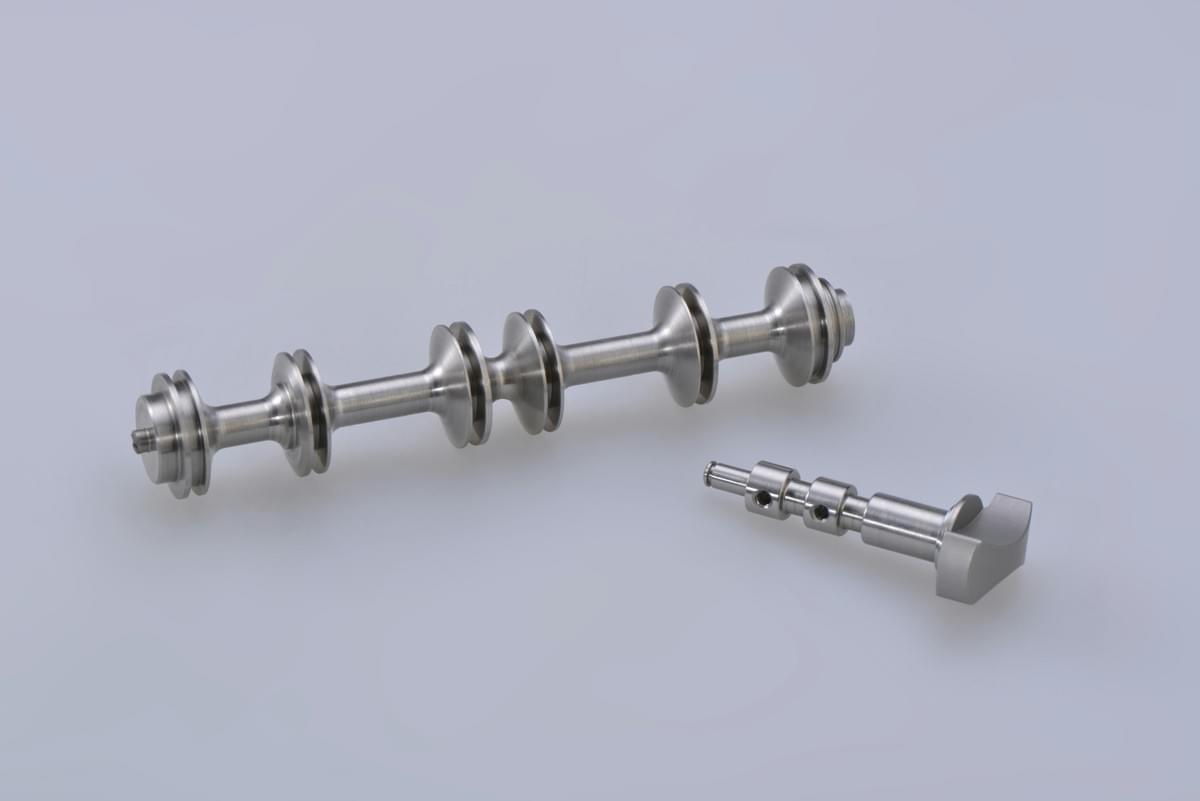
Pin gates are a unique and highly effective option among various injection molding gate types. They serve as a crucial entry point for molten plastic into the mold cavity, ensuring precise filling while minimizing imperfections. Understanding pin gate injection molding can significantly enhance the quality of molded products, making it an essential topic for designers and engineers alike.
Introduction to Pin Gate Injection Molding
The pin gate is a specific type of injection molding gate that utilizes a small pin to control the flow of molten material into the mold cavity. This design allows for efficient filling and is particularly useful in applications requiring high precision and minimal surface blemishes. When considering what are the types of gates used in injection molds, pin gates stand out due to their ability to create clean parting lines and reduce post-processing work.
In essence, the pin gate serves as both an entry point and a means of regulating flow dynamics within the mold. The design allows for better control over material distribution, which is vital in achieving uniform thickness across parts. This level of control makes pin gates an attractive choice for manufacturers looking to optimize their production processes.
Benefits of Using Pin Gates
One major advantage of using pin gates lies in their ability to minimize gate marks on finished products, resulting in aesthetically pleasing parts with smooth surfaces. Compared to other injection molding gate types like sprue or edge gates, pin gates leave less visible evidence of where the material entered the mold. This characteristic often saves time during finishing processes, allowing companies to deliver high-quality products more efficiently.
Another benefit is that pin gates can accommodate varying wall thicknesses without compromising structural integrity or appearance. They facilitate better packing during cooling cycles, which helps prevent defects such as warping or sink marks that can occur with other types of gates. Additionally, this efficiency translates into reduced cycle times and improved overall production rates.
Lastly, using pin gates can lead to lower scrap rates since they allow for more consistent flow characteristics during injection molding processes. By providing controlled filling conditions, manufacturers can reduce waste caused by imperfectly molded parts or excessive trimming required after production. This not only enhances profitability but also contributes positively to sustainability efforts by minimizing material usage.
Applications in Diverse Industries
Pin gate injection molding finds applications across various industries due to its versatility and effectiveness in producing high-quality components. One prominent area includes consumer electronics where precision is paramount; components such as casings or connectors often utilize this type of gating system to ensure flawless finishes and tight tolerances are met consistently.
Additionally, automotive manufacturing benefits from using pin gates when creating intricate parts like dashboard components or interior fittings that require both durability and visual appeal. The ability to achieve smooth surfaces without extensive post-processing aligns well with industry standards focused on efficiency and quality assurance.
Medical device manufacturing also leverages the advantages offered by pin gate designs; devices often have strict regulatory requirements regarding dimensional accuracy and surface quality—attributes that are easily achieved through careful application of this gating method. With its broad applicability across sectors ranging from electronics to healthcare, understanding how different injection molding gate types function—including the specific benefits provided by pin gates—is essential for successful product development.
Submarine Gate
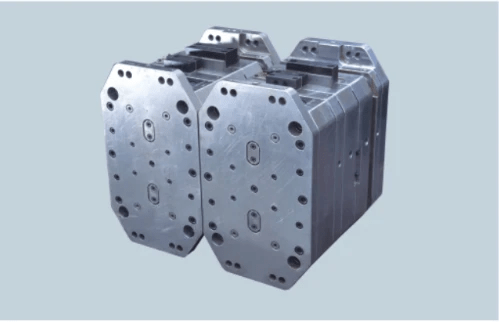
Submarine gates are a unique injection molding gate type that offers both versatility and efficiency in product design. These gates are typically located below the parting line, allowing for a more seamless integration into the molded product. Understanding the submarine gate concept is essential for optimizing your injection molding process.
Understanding the Submarine Gate Concept
A submarine gate is designed to be submerged beneath the surface of the molded part, which means it’s less visible once production is complete. This feature allows designers to maintain aesthetic integrity while still benefiting from effective material flow during the injection molding process. By utilizing this gate type, manufacturers can achieve better surface quality and minimize post-molding finishing work.
How It Affects Injection Molding Efficiency
The submarine gate significantly impacts injection molding efficiency by reducing cycle times and enhancing material distribution within molds. Since these gates are positioned strategically, they allow for better control over how molten plastic flows into cavities, leading to fewer defects in final products. Additionally, this design can help mitigate issues like warping or sink marks that may occur with other injection molding gate types.
Situations Best Suited for Submarine Gates
Submarine gates shine in applications where aesthetics are paramount, such as consumer electronics or automotive parts that require a clean finish without visible gating marks. They're also ideal for complex geometries where traditional gates might struggle with material flow or lead to uneven filling of mold cavities. In scenarios demanding high-quality surface finishes and minimal post-processing, submarine gates prove to be an excellent choice.
Conclusion
In the realm of injection molding, understanding the various injection molding gate types is essential for achieving optimal results. Each gate type—whether it's the sprue gate, edge gate, fan gate, pin gate, or submarine gate—has its unique characteristics that cater to different applications and design requirements. By grasping these differences, manufacturers can make informed decisions that enhance product quality and production efficiency.
Summary of Injection Molding Gate Types
To recap, what are the types of gates used in injection molds? We explored the sprue gate, which is a straightforward entry point for molten plastic; the edge gate that offers versatility in design; and the fan gate known for its wide distribution of material flow. Additionally, we discussed pin gates that provide precision and submarine gates that effectively minimize visible marks on finished products. Each of these injection molding gate types plays a critical role in determining how well a part fills and cools during the molding process.
The Role of Gate Design in Quality
The importance of injection molding gate design cannot be overstated—it significantly impacts not only production efficiency but also the quality of the final product. Properly designed gates ensure uniform material distribution and reduce issues like warping or incomplete filling. For instance, what is the difference between fan gate and edge gate? While both serve similar functions, their designs influence flow patterns differently; thus affecting surface finish and dimensional accuracy.
Choosing the Right Gate for Your Project
When it comes to choosing the right gate for your project, several factors must be considered: part geometry, material properties, and desired aesthetics all play a role in this decision-making process. Understanding where are the gates for injection molding located can help you visualize how they affect overall mold performance. Whether you opt for a pin gate injection molding method or prefer another style like a sprue or submarine gate will depend on your specific needs—so weigh your options carefully!