Introduction
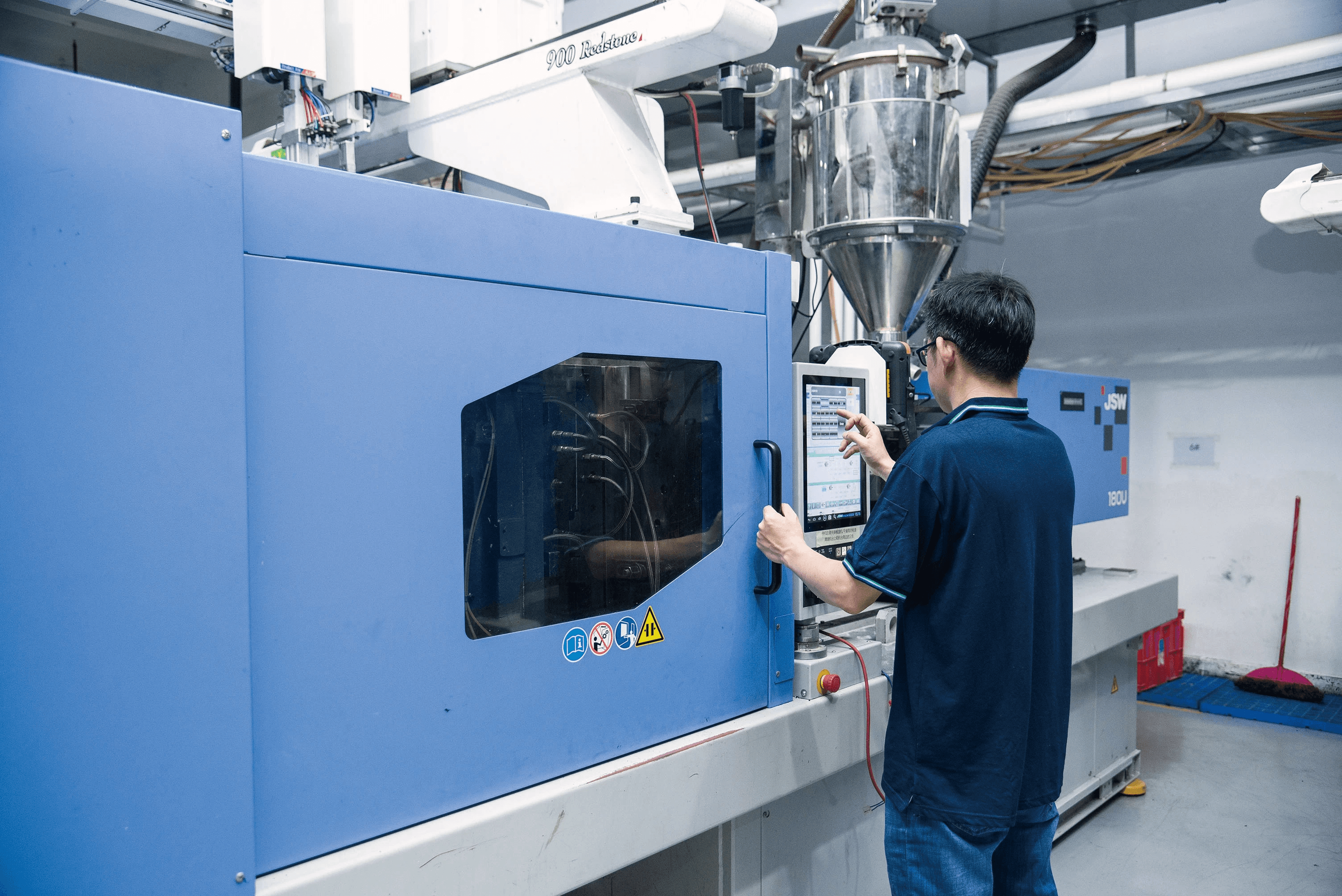
The world of injection plastique medical is a fascinating and complex arena that combines cutting-edge technology with stringent regulatory requirements. As the demand for high-quality medical devices and components continues to rise, understanding the nuances of Medical Plastic Injection Molding becomes increasingly essential. This introduction will guide you through the critical aspects of this industry, emphasizing the importance of precision in manufacturing and how selecting the right Medical Plastic Injection Molding companies can significantly impact success.
Understanding Injection Plastique Medical
Injection plastique medical refers to the specialized process of creating plastic components specifically for medical applications through injection molding techniques. This method allows for high-volume production while ensuring consistency and quality in every piece manufactured. By leveraging advanced technologies and materials tailored for healthcare, injection plastique medical plays a crucial role in developing products such as syringes, surgical instruments, and implantable devices.
Importance of Precision in Manufacturing
Precision is paramount when it comes to manufacturing plastic injection moulded medical components; even minor variations can have significant consequences in patient safety and product efficacy. The intricacies involved in Medical Plastic Injection Molding require meticulous attention to detail throughout the design and production processes to ensure compliance with health regulations. Achieving this level of precision not only enhances product reliability but also builds trust between manufacturers and healthcare providers.
Selecting the Right Medical Plastic Injection Molding Partner
Choosing an appropriate partner among various Medical Plastic Injection Molding companies is vital for any organization looking to thrive in this competitive landscape. Factors such as experience, technological capabilities, and commitment to quality assurance should be at the forefront when making this decision. A reliable partner can help streamline production processes while ensuring that your plastic injection moulded medical components meet all necessary standards for safety and performance.
Key Trends in Medical Plastic Injection Molding
The landscape of medical plastic injection molding is evolving rapidly, driven by technological advancements and a growing emphasis on sustainability. As the demand for high-quality, reliable medical devices increases, innovations in injection plastique medical are at the forefront of this transformation. Understanding these key trends is essential for companies looking to thrive in the competitive field of Medical Plastic Injection Molding.
Innovations in Medical Plastic Injection Technology
Innovations in medical plastic injection technology are revolutionizing how we produce Plastic Injection Moulded Medical Components. Techniques such as multi-material molding and advanced 3D printing are enhancing design flexibility and functionality, enabling manufacturers to create complex components with precision. Additionally, new materials with improved biocompatibility and strength are becoming increasingly available, allowing Medical Plastic Injection Molding Companies to meet stringent industry standards while pushing the boundaries of what’s possible.
These advancements not only improve product performance but also streamline production processes, reducing waste and lead times significantly. The integration of smart manufacturing technologies, such as IoT (Internet of Things) sensors, is further optimizing operations by providing real-time data for better decision-making. As these innovations continue to evolve, they will play a crucial role in shaping the future of injection plastique medical.
Sustainability Practices in Plastic Injection Moulded Medical Components
Sustainability has emerged as a key priority within the realm of plastic injection molding in the medical industry. Manufacturers are increasingly adopting eco-friendly practices to minimize their environmental impact while producing high-quality Plastic Injection Moulded Medical Components. This includes using recyclable materials and implementing energy-efficient processes that reduce waste without compromising on quality or safety.
Moreover, many Medical Plastic Injection Molding Companies are investing in research to develop biodegradable plastics specifically designed for medical applications. Such efforts not only cater to growing consumer demand for sustainable products but also align with regulatory pressures aimed at reducing plastic waste globally. By embracing sustainability practices, companies can enhance their brand reputation while contributing positively to environmental conservation.
The Role of Compliance and Regulations
Medical Plastic Injection Molding Companies must stay updated on changing regulations and invest in quality assurance processes that align with industry standards like ISO certifications or Good Manufacturing Practices (GMP). This commitment helps mitigate risks associated with product recalls or liability claims while ensuring that all produced components maintain high levels of quality and safety throughout their lifecycle. Ultimately, navigating compliance effectively can be a significant competitive advantage within the highly regulated landscape of plastic injection molding in the medical industry.
Choosing the Right Medical Plastic Injection Molding Companies
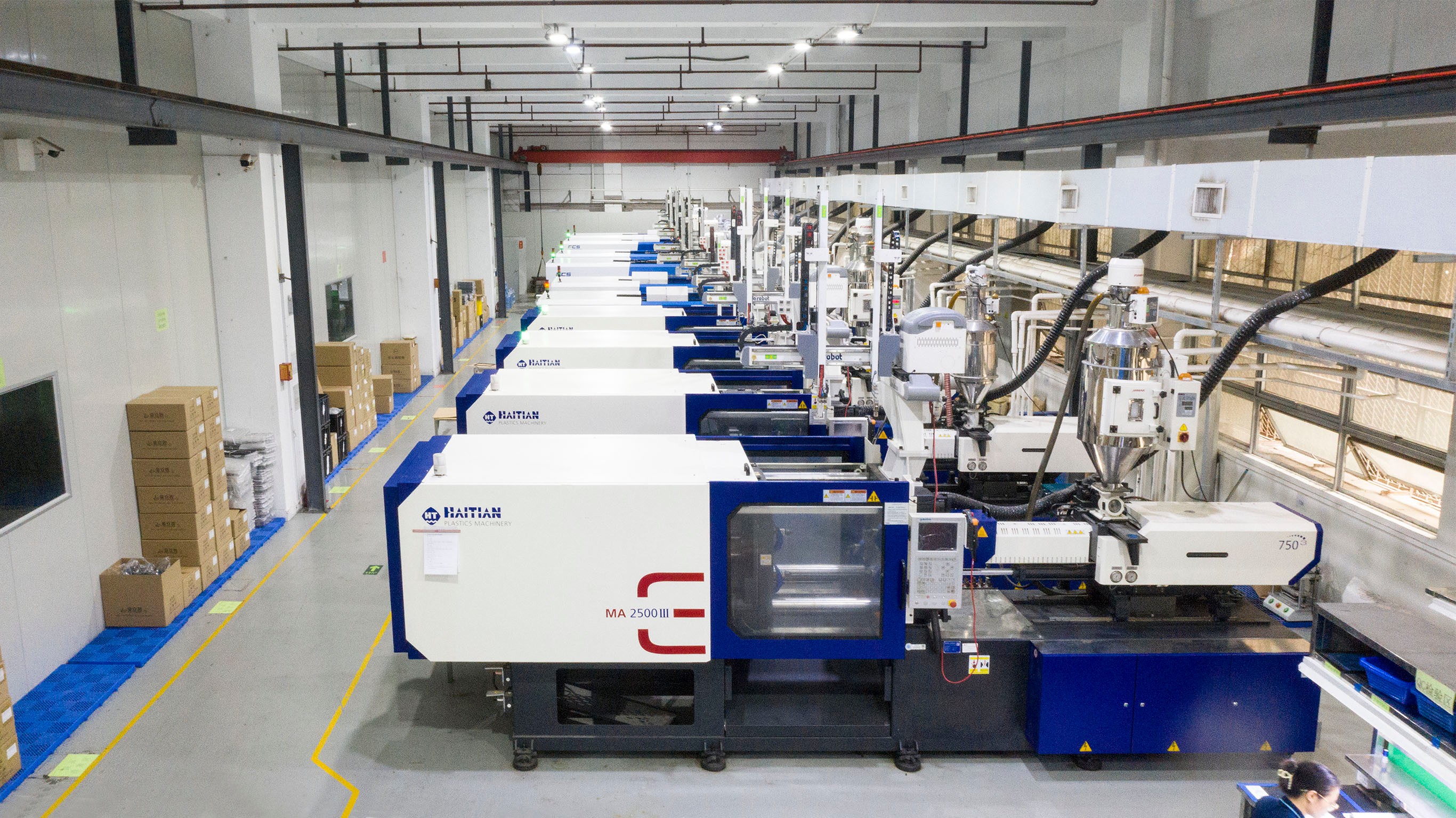
Selecting the right partner for your medical plastic injection molding needs is crucial for ensuring high-quality outcomes and compliance with industry standards. With a plethora of options available, it can be overwhelming to determine which medical plastic injection molding companies align best with your specific requirements. By focusing on experience, technology capabilities, and quality assurance processes, you can make an informed decision that will benefit your projects.
Evaluating Experience and Expertise
A company’s portfolio can provide a glimpse into their capabilities and past successes. If they’ve successfully handled similar projects or developed innovative solutions tailored to the medical industry, it's a good sign they understand your needs. Additionally, consider seeking testimonials or case studies from previous clients to gauge their satisfaction level—after all, word-of-mouth is still one of the best indicators of reliability.
Assessing Technology and Equipment Capabilities
In an era where technology is advancing at breakneck speed, assessing a company's equipment capabilities is essential when selecting medical plastic injection molding companies. The latest machinery not only enhances production efficiency but also ensures precision in creating complex designs for plastic injection moulded medical components. When evaluating potential partners, inquire about their investment in state-of-the-art technology—this could include advanced robotics, automated systems, or specialized software for design optimization.
Moreover, consider whether they use simulation software during the design phase to predict potential issues before production begins. This proactive approach helps mitigate risks associated with defects or delays down the line—a vital factor in maintaining quality standards within the highly regulated medical industry. Ultimately, aligning yourself with a company that prioritizes technological advancement will set you up for success.
Importance of Quality Assurance Processes
Quality assurance processes are non-negotiable when it comes to injection plastique medical; after all, lives often depend on these products being safe and effective! A robust quality management system ensures that every step—from material selection through final inspection—is meticulously monitored to meet regulatory requirements and client specifications alike. Look for companies that adhere to ISO standards or other relevant certifications as these indicate a commitment to maintaining high-quality production practices.
Additionally, ask about their testing protocols: Are they conducting thorough inspections at various stages of production? Do they utilize third-party testing facilities to validate results? The answers will reveal how seriously they take quality assurance—and this should weigh heavily on your decision-making process when selecting partners in this critical field.
Designing Effective Plastic Injection Moulded Medical Components
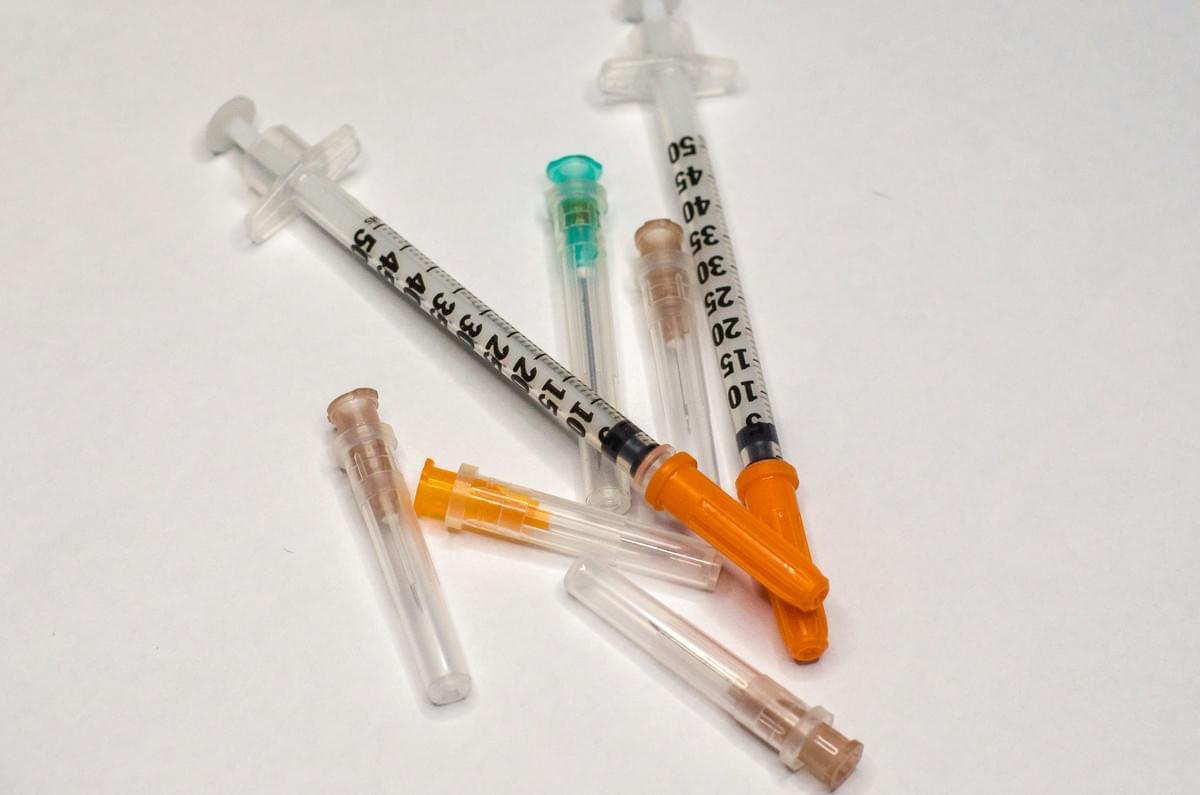
Creating effective plastic injection moulded medical components is not just about meeting specifications; it’s about ensuring safety, functionality, and compliance with stringent medical standards. The design phase is critical in the Medical Plastic Injection Molding process, as it directly influences the performance and reliability of the final product. This section will delve into essential design considerations, the benefits of collaborating with experts like Baoyuan, and the importance of prototypes and testing.
Essential Design Considerations for Medical Applications
When designing components for injection plastique medical applications, several key factors must be taken into account to ensure their efficacy and safety. First and foremost, biocompatibility is crucial; materials used in Medical Plastic Injection Molding must not cause adverse reactions when in contact with biological tissues. Additionally, designers need to consider manufacturability—components should be designed for efficient production while maintaining high quality standards to meet the rigorous demands of the medical industry.
Another consideration is the component's functionality under various conditions such as temperature fluctuations or exposure to chemicals. This requires a thorough understanding of material properties and how they interact with different environments over time. Furthermore, ease of assembly plays a pivotal role; parts should fit together seamlessly without requiring excessive force or complex processes that could lead to errors during production.
Lastly, regulatory compliance cannot be overlooked; designs must adhere to industry regulations such as ISO 13485 or FDA guidelines. By integrating these essential considerations into the design process from the outset, manufacturers can significantly reduce risks associated with product failures in real-world applications.
Collaboration with Experts like Baoyuan for Optimal Results
Partnering with experienced professionals like Baoyuan can make a world of difference when designing plastic injection moulded medical components. Their expertise in Medical Plastic Injection Molding ensures that every aspect—from material selection to final production—is handled meticulously. Collaborating closely allows for innovative solutions tailored specifically to meet unique project requirements while adhering to industry standards.
Moreover, experts bring invaluable insights into current trends and technologies within Plastic Injection Molding in the medical industry which can enhance product performance significantly. They can suggest advanced materials or manufacturing techniques that may not have been considered initially but could improve durability or reduce costs effectively. This collaborative approach fosters creativity while minimizing potential pitfalls that may arise during development.
Furthermore, working alongside seasoned professionals streamlines communication channels between teams involved—designers, engineers, and manufacturers—ensuring everyone is aligned on project goals from inception through completion. Ultimately, this synergy leads to high-quality outcomes that meet both client expectations and regulatory requirements efficiently.
Prototypes and Testing: Why They Matter
Prototyping serves as a vital step in developing effective plastic injection moulded medical components because it allows designers to validate their concepts before full-scale production begins. Creating prototypes enables teams to assess design feasibility while identifying any potential issues early on—saving time and resources down the line during Medical Plastic Injection Molding processes. Additionally, these early models provide an opportunity for hands-on testing which is crucial for ensuring functionality meets specified requirements.
Testing prototypes under various conditions helps identify weaknesses that could compromise safety or performance once deployed in real-world scenarios like hospitals or clinics where reliability is paramount. Through rigorous evaluation methods such as stress tests or biocompatibility assessments, developers can refine designs based on empirical data rather than assumptions alone—a practice that ultimately enhances quality assurance across all stages of production.
In conclusion, investing time into prototyping and testing lays a strong foundation for successful outcomes within plastic injection molding projects targeting medical applications specifically tailored toward patient care needs effectively while complying with necessary regulations throughout every step involved from concept through execution.
Streamlining Production Processes in the Medical Industry
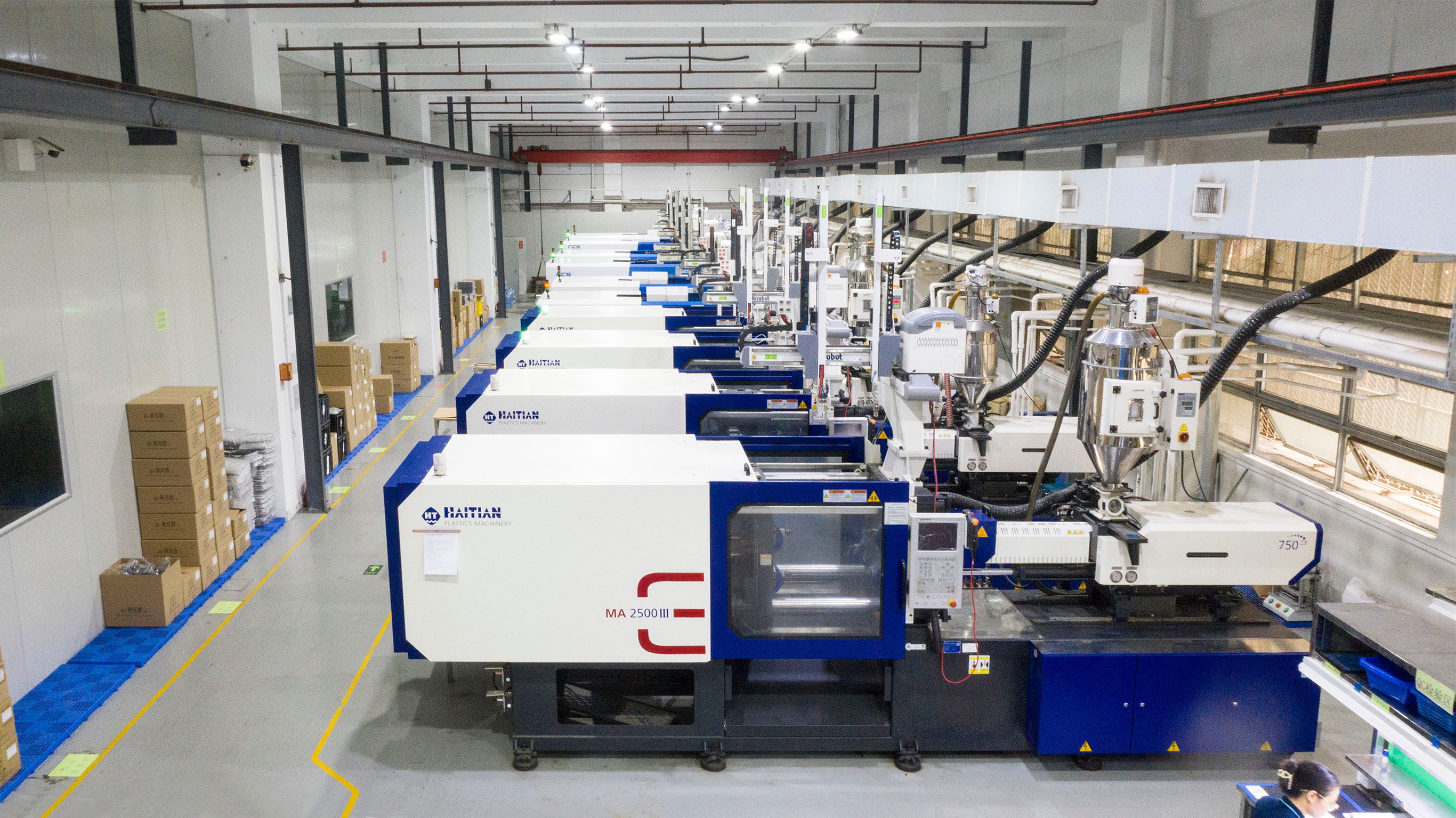
In the fast-paced world of medical manufacturing, efficiency is key. Streamlining production processes not only reduces costs but also enhances the quality of medical plastic injection molding products. By adopting innovative strategies, companies can ensure that their plastic injection moulded medical components are produced with precision and speed.
Lean Manufacturing Techniques for Injection Plastique Medical
Lean manufacturing techniques have emerged as a game-changer in the realm of injection plastique medical. These methodologies focus on minimizing waste while maximizing productivity, allowing manufacturers to deliver high-quality products without unnecessary delays or excess costs. By implementing practices such as value stream mapping and continuous improvement, medical plastic injection molding companies can refine their processes to meet stringent industry standards.
Moreover, lean principles encourage cross-functional collaboration among teams, fostering an environment where everyone is focused on enhancing efficiency and quality. This collective effort leads to better resource allocation and a more responsive production line for plastic injection moulded medical components. Ultimately, embracing lean techniques paves the way for sustainable growth in the competitive landscape of the medical industry.
Role of Automation in Enhancing Efficiency
Automation has become an indispensable ally in streamlining production processes within the medical industry. The integration of advanced robotics and machine learning technologies into medical plastic injection molding operations allows for greater consistency and precision in manufacturing practices. Automated systems can handle repetitive tasks with speed and accuracy, freeing up skilled workers to focus on more complex issues that require human insight.
Additionally, automation minimizes human error, ensuring that each batch of plastic injection moulded medical components meets rigorous quality standards consistently. With real-time monitoring capabilities, manufacturers can swiftly identify potential bottlenecks or inefficiencies in their production lines—allowing for immediate corrective actions to be taken. As a result, companies can reduce lead times significantly while maintaining high levels of product integrity.
Reducing Lead Times and Maintaining Quality
In today's competitive marketplace, reducing lead times is critical for success in the field of injection plastique medical manufacturing. By optimizing production schedules through effective planning and leveraging technology like automation, companies can expedite their output without compromising on quality or safety standards associated with medical plastic injection molding processes.
Maintaining quality during this acceleration is paramount; therefore, rigorous testing protocols must be integrated into every stage of production—from design through to final assembly—to ensure that every component adheres strictly to regulatory requirements and customer expectations alike. This balanced approach not only enhances customer satisfaction but also establishes a solid reputation for reliability among leading players in the sector—an essential factor when selecting from various Medical Plastic Injection Molding Companies.
In conclusion, by focusing on lean manufacturing techniques alongside automation strategies while keeping an eye on lead times and quality assurance practices, stakeholders within the plastic injection molding in the medical industry can position themselves favorably for future challenges.
Future Outlook for Plastic Injection Molding in the Medical Industry
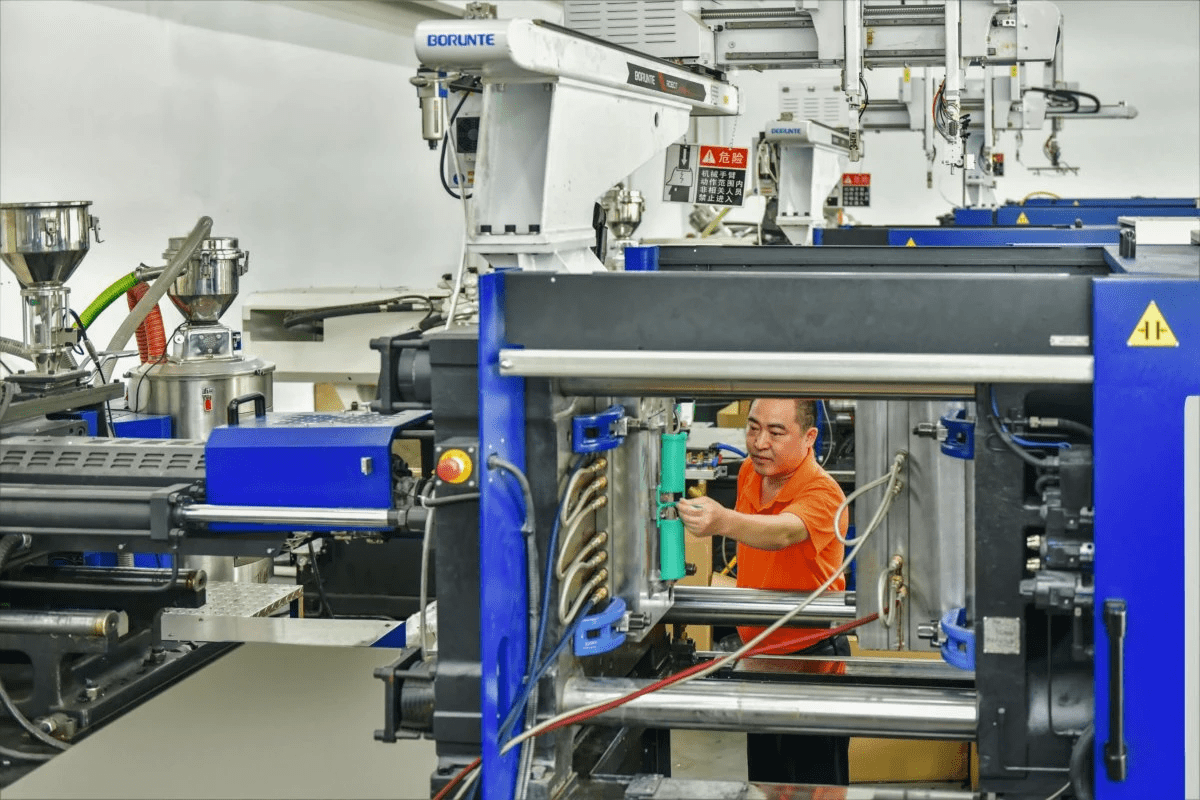
The future of plastic injection molding in the medical industry is poised for significant transformation, driven by technological advancements and evolving market demands. With the rise of innovative materials and manufacturing techniques, companies specializing in injection plastique medical are better equipped to meet stringent healthcare requirements. As these trends unfold, understanding their implications will be crucial for stakeholders aiming to stay competitive.
Emerging Technologies Impacting Medical Plastic Injection
Technological innovations are reshaping the landscape of medical plastic injection molding, with advancements like 3D printing and smart manufacturing leading the charge. These emerging technologies enable manufacturers to create more complex designs for plastic injection moulded medical components while reducing waste and enhancing precision. Moreover, integrating Internet of Things (IoT) devices into production processes allows for real-time monitoring and data analytics, further improving efficiency in medical plastic injection molding.
Additionally, the development of biocompatible materials is paving the way for safer and more effective products in healthcare applications. This trend not only enhances patient safety but also broadens the scope of what can be achieved through injection plastique medical processes. As these technologies continue to evolve, they will play a pivotal role in shaping future practices within medical plastic injection molding companies.
Predictions for Market Growth and Challenges
The market for plastic injection molding in the medical industry is expected to experience robust growth over the coming years due to increasing demand for advanced healthcare solutions. Factors such as an aging population and a rise in chronic diseases are driving this demand, creating opportunities for innovative plastic injection moulded medical components that cater to specific needs. However, challenges such as regulatory compliance and material shortages may pose obstacles that companies must navigate carefully.
Furthermore, competition among medical plastic injection molding companies is likely to intensify as new players enter the market with unique offerings. To maintain a competitive edge, established firms will need to invest in research and development while also focusing on sustainability practices that resonate with environmentally conscious consumers. Balancing innovation with compliance will be key as businesses strive to capitalize on market growth opportunities.
Long-term Strategies for Success
To thrive in an ever-evolving landscape of plastic injection molding in the medical industry, companies must adopt long-term strategies that prioritize adaptability and collaboration. Embracing lean manufacturing principles can streamline production processes while minimizing waste—a crucial factor when dealing with high-volume orders typical of healthcare applications like surgical instruments or diagnostic devices made from injection plastique medical techniques.
Strategic partnerships with technology providers can also enhance capabilities by integrating cutting-edge solutions into existing workflows, thereby improving overall efficiency and product quality. Additionally, investing in workforce training ensures that employees remain skilled in new technologies essential for maintaining competitiveness among leading medical plastic injection molding companies.
In conclusion, staying ahead requires a proactive approach focused on innovation, quality assurance processes, and sustainable practices tailored specifically towards meeting growing demands within this sector.
Conclusion
In wrapping up our exploration of injection plastique medical, it's clear that the landscape of Medical Plastic Injection Molding is both dynamic and essential. The focus on precision, compliance, and innovation underscores the importance of choosing the right partners in this intricate field. As we look to the future, understanding the trends and technologies shaping Plastic Injection Moulded Medical Components will be crucial for success.
Recap of Injection Plastique Medical Essentials
Throughout this discussion, we've highlighted that injection plastique medical is not just about creating components but ensuring they meet rigorous standards for safety and efficacy. The process involves a blend of advanced technology and stringent quality assurance practices to produce reliable Medical Plastic Injection Molding solutions. By prioritizing design considerations and collaboration with experienced manufacturers, stakeholders can ensure that their Plastic Injection Moulded Medical Components are optimized for performance.
Final Thoughts on Choosing Partners and Technologies
Selecting the right Medical Plastic Injection Molding Companies is paramount in achieving high-quality outcomes in the medical sector. It's essential to evaluate not only their experience but also their technological capabilities and commitment to sustainability practices. In a field where precision matters greatly, aligning with partners who share your vision for quality can make all the difference in delivering superior products.
Preparing for the Future in Medical Plastic Injection Molding
Looking ahead, the future of plastic injection molding in the medical industry appears promising yet challenging due to rapid technological advancements and evolving regulations. Staying informed about emerging technologies will be key for companies aiming to maintain a competitive edge while adhering to compliance standards. By adopting proactive strategies now, businesses can better prepare themselves for changes ahead, ensuring they remain leaders in producing top-notch injection plastique medical components.