Introduction
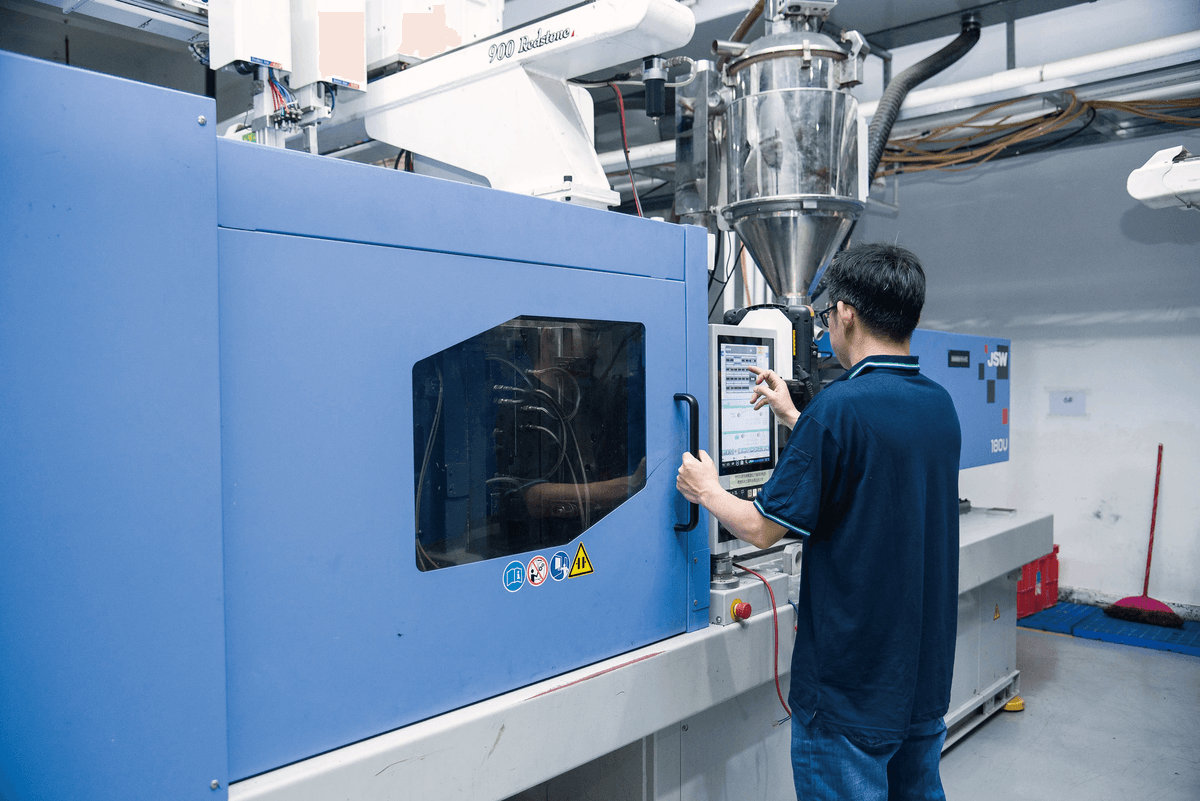
When it comes to plastic injection molding, choosing the right manufacturer is crucial for the success of your project. Many companies make common mistakes that can lead to costly errors and subpar results. From overlooking material quality to ignoring design for manufacturability, several key considerations should not be overlooked.
Common Mistakes When Choosing Plastic Injection Molding Companies
Selecting a cheap injection molding service can be a costly mistake. While it may seem like a way to save money upfront, it often leads to problems with durability and performance, resulting in higher expenses down the line.
To avoid these pitfalls, consider the following:
- Prioritize quality: Invest in a reputable service provider known for producing high-quality products.
- Factor in long-term costs: Evaluate the total cost of ownership, including potential repairs or replacements.
- Seek expert advice: Consult with industry professionals to understand the importance of quality injection molding.
By carefully selecting an injection molding service, you can ensure the longevity and performance of your products while protecting your bottom line.
Overlooking Material Quality
Using low-quality plastic pellets for injection molding can result in products prone to defects and breakage. Prioritizing material quality ensures the longevity and reliability of your final product.
Ignoring Design for Manufacturability
Design for manufacturability is often overlooked, leading to inefficient production and assembly processes. Considering manufacturability during the design phase, you can optimize your product for easier and more cost-effective manufacturing.
Remember, when choosing a plastic injection molder, it's essential to avoid these common pitfalls to achieve superior results and avoid costly mistakes in production.
Neglecting to Consider Production Volume
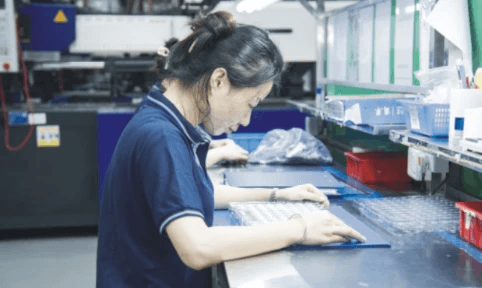
When working with plastic injection molders, it's crucial to consider production volume to ensure optimal efficiency. Failing to do so can result in unnecessary costs and delays. By overlooking production volume, companies may miss opportunities to streamline manufacturing processes and reduce lead times.
Failing to Optimize for Production Efficiency
Cheap injection molding may seem like a cost-effective solution, but failing to optimize for production efficiency can lead to higher long-term expenses. Plastic injection molding manufacturers should prioritize efficient production methods to minimize waste and maximize output. This can ultimately result in significant cost savings and improved overall productivity.
Not Understanding Tooling Costs
Understanding tooling costs is essential when it comes to plastic injection molding services. Ignoring the intricacies of tooling expenses can lead to budget overruns and project delays. By understanding tooling costs comprehensively, companies can make informed decisions that align with their budgetary requirements while ensuring high-quality results.
Overlooking the Importance of Mold Design
Mold design is a critical yet often overlooked, component of the injection molding process. Neglecting this crucial step can lead to subpar part quality and increased production time. To achieve optimal results, businesses must partner with experienced plastic injection mold experts who understand the importance of effective mold design.
By prioritizing the following key considerations when working with plastic injection molders, businesses can avoid costly mistakes and achieve superior outcomes in their manufacturing projects:
- Comprehensive Part Analysis: A thorough evaluation of part geometry, material selection, and functional requirements is essential for successful mold design.
- Optimized Gate and Runner Systems: Proper gate and runner placement significantly impacts part quality, cycle time, and material efficiency.
- Precise Molding Parameters: Collaborate with molders to establish optimal injection pressure, temperature, and cooling conditions for the specific resin and part design.
- Rigorous Testing and Refinement: Implement thorough mold testing and validation processes to identify and address potential issues before full-scale production.
By actively involving mold design experts in the early stages of a project, businesses can enhance product quality, reduce production costs, and gain a competitive edge in the marketplace.
Choosing the Wrong Material
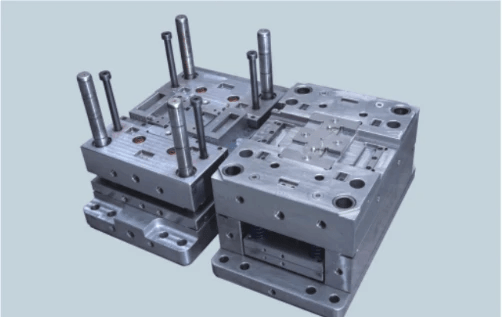
Plastic injection molders must be cautious when selecting materials for their projects. Not considering the environmental impact of the chosen material can lead to negative repercussions in the long run, such as increased waste and pollution. It's essential to prioritize eco-friendly options and ensure the material aligns with sustainable practices.
Not Considering Environmental Impact
Choosing a material without assessing its environmental impact can contribute to plastic pollution and harm ecosystems. Plastic injection molders should prioritize recyclable, biodegradable, or sustainable materials to minimize their ecological footprint and promote environmental responsibility.
Ignoring Material Compatibility
Neglecting material compatibility can lead to poor adhesion, warping, or even part failure during production or after deployment. Plastic injection molders must thoroughly assess the compatibility of different materials with their intended applications to ensure optimal performance and durability.
Underestimating Material Costs
Underestimating material costs can significantly impact project budgets and profitability for plastic injection molding manufacturers. To avoid cost overruns and maintain financial sustainability, it's important to carefully evaluate all associated expenses related to material procurement, processing, and waste management.
Choosing the right materials is crucial for successful plastic injection molding projects!
Overlooking Quality Control
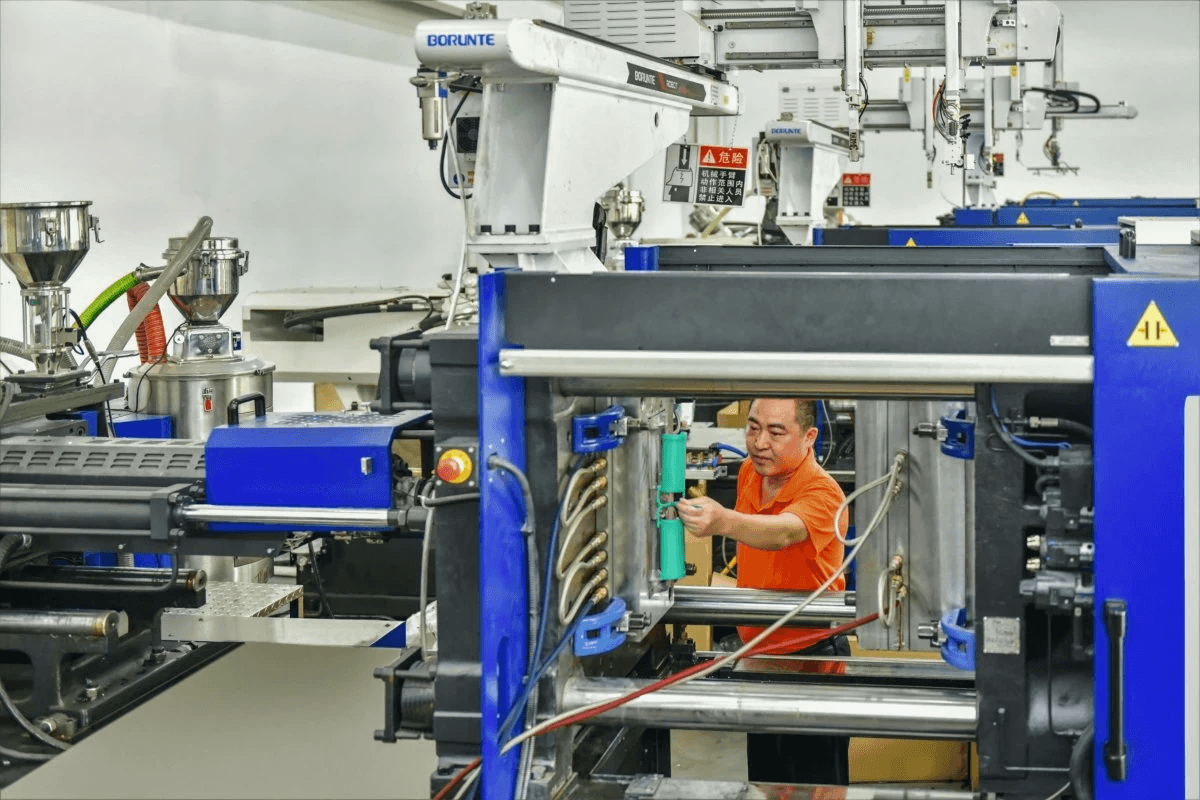
When working with plastic injection molding manufacturers, it's crucial to prioritize quality control throughout the production process. Ignoring part inspection can lead to costly defects and delays in production. By neglecting to address defects early on, you risk compromising the integrity of your final product and damaging your reputation. Failing to implement quality assurance processes can result in inconsistent output and dissatisfied customers.
Ignoring Part Inspection
Many cheap injection molding services may cut corners by skipping thorough part inspection, which can lead to disastrous consequences for your project. It's essential to ensure that every molded part undergoes rigorous inspection to identify potential issues early on in the production process. By overlooking this critical step, you risk delivering subpar products to your customers and damaging your brand reputation.
Neglecting to Address Defects
Addressing defects promptly is vital for maintaining high-quality standards in plastic injection molding. Failure to address defects as they arise can result in issues that impact the entire production run. This oversight can lead to increased costs, wasted materials, and delayed timelines, ultimately affecting your bottom line and customer satisfaction.
Failing to Implement Quality Assurance Processes
Plastic injection molders may struggle with consistency and reliability in their output without proper quality assurance processes. Manufacturers must establish robust quality control measures that encompass every stage of production, from material selection through final product inspection. Failing to implement these processes risks delivering substandard products that fail to meet customer expectations.
Disregarding Regulatory Compliance
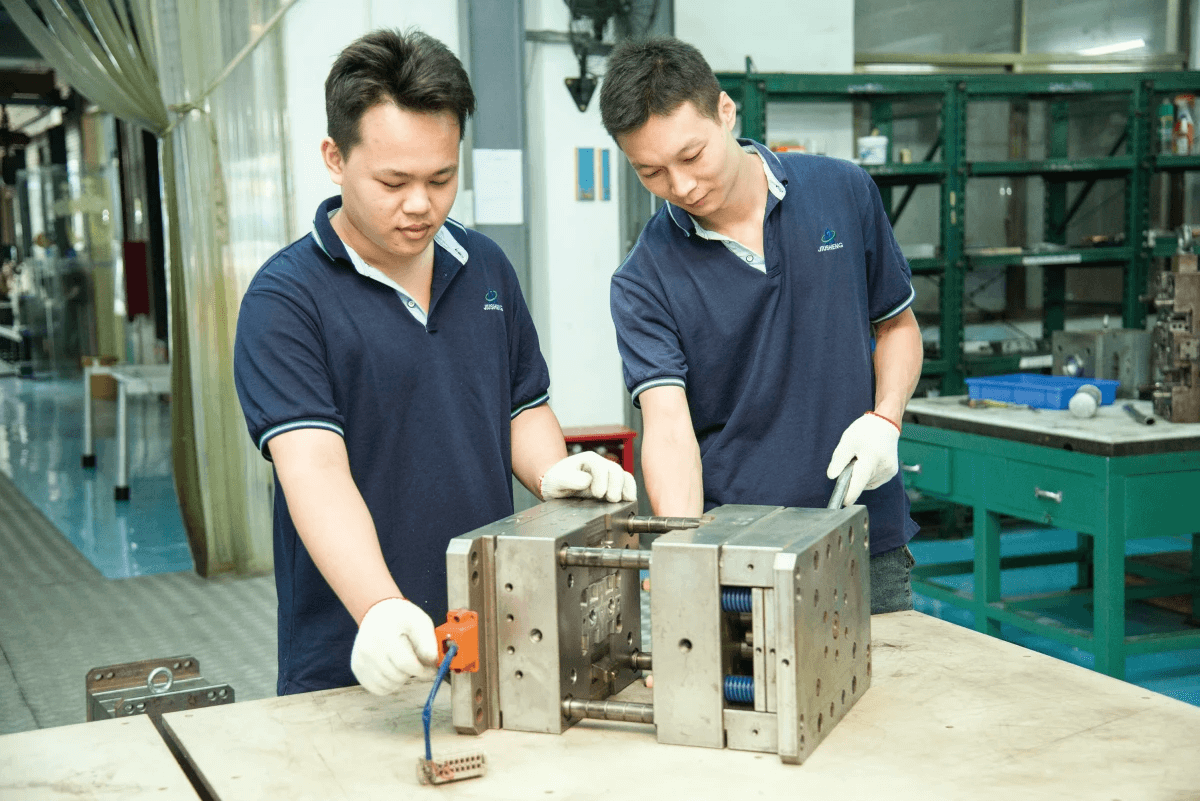
When choosing plastic injection molding manufacturers, it's crucial to ensure that they follow industry standards to guarantee the quality and safety of your products. Ignoring these standards can lead to subpar results and potential legal issues. Working with manufacturers who prioritize compliance with regulations to meet the highest quality and safety requirements for your plastic injection mold needs is essential.
Not Following Industry Standards
Choosing cheap injection molding services without considering whether they adhere to industry standards can result in poor-quality products that don't meet the required specifications. It's important to partner with plastic injection molders with a proven track record of following industry best practices and regulations, ensuring your products are produced to the highest standard.
Ignoring Safety Regulations
Neglecting safety regulations when working with plastic injection molding manufacturers can lead to hazardous products that pose consumer risks. By prioritizing safety compliance, you can avoid potential liabilities and ensure your products are safe for use in various applications. Partnering with reputable plastic injection molders who prioritize safety is essential for a successful production process.
Failing to Meet Customer Requirements
Disregarding customer requirements regarding regulatory compliance can result in dissatisfaction and loss of business opportunities. Plastic injection molders must understand and fulfill customer-specific regulatory needs, ensuring that the final products align with industry standards and meet customer expectations. You can build trust and long-term partnerships with clients who value regulatory compliance by prioritizing customer requirements.
Partnering with Baoyuan ensures regulatory compliance throughout the plastic injection molding process, safeguarding the quality and safety of your products while meeting customer requirements.
Lack of Communication with Manufacturer
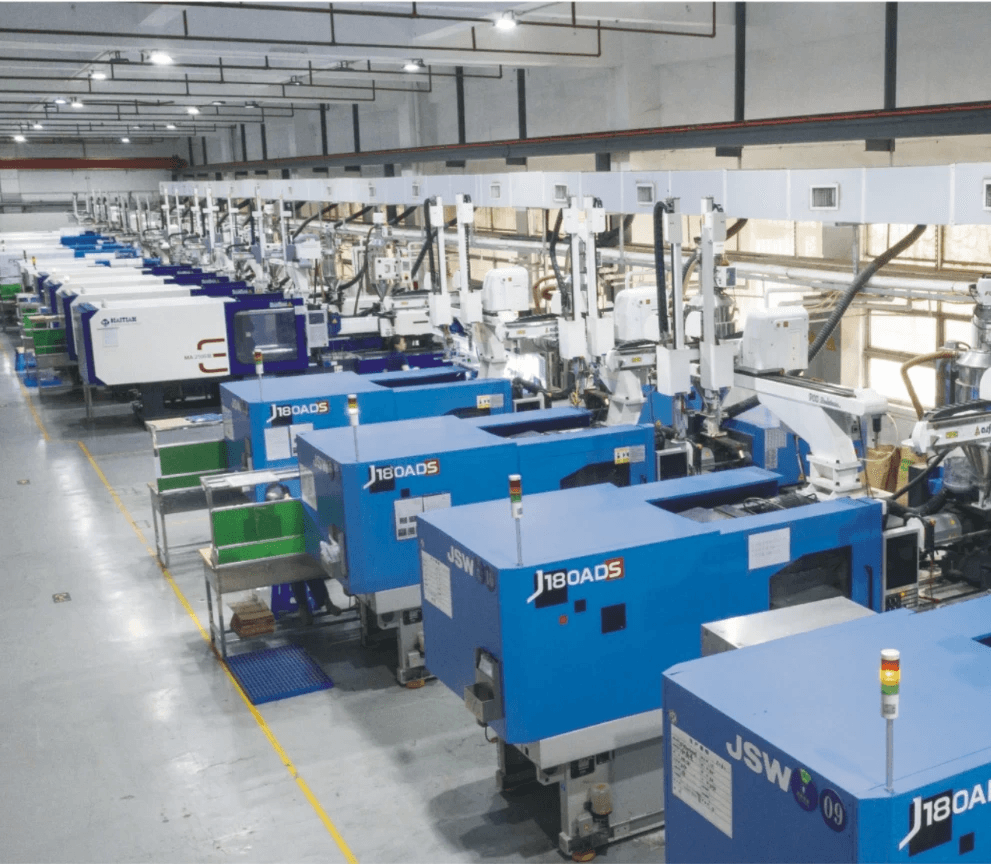
Clear communication is key to a successful partnership with plastic injection molding manufacturers. Not providing detailed specifications for your project can lead to misunderstandings and costly mistakes. It's crucial to clearly outline your requirements, including material type, part dimensions, and any specific finishing or assembly needs.
Not Providing Clear Specifications
Failing to provide clear specifications for your plastic injection molding project can result in miscommunication and errors. Ensure you detail the exact dimensions, material requirements, and specific finishing or assembly instructions. This will help the manufacturer understand your needs and deliver the desired end product without delays or revisions.
Overlooking Feedback from Manufacturer
Ignoring feedback from your plastic injection molders is a missed opportunity for improvement. Manufacturers have valuable insights based on their expertise and experience in injection molding services. You may miss valuable suggestions that could enhance the design, improve manufacturability, or reduce production costs by overlooking their input.
Ignoring the Importance of Collaboration
Collaboration with your plastic injection molders is essential for achieving optimal results. Open communication and a collaborative approach foster a better understanding of each other's capabilities and limitations. By working together closely, you can address potential issues early in the process and ensure that the final product meets your expectations.
Remember that successful communication with your plastic injection molding manufacturer relies on clear specifications, consideration of feedback, and collaboration throughout the production process!
Ignoring Potential for Cost Reduction
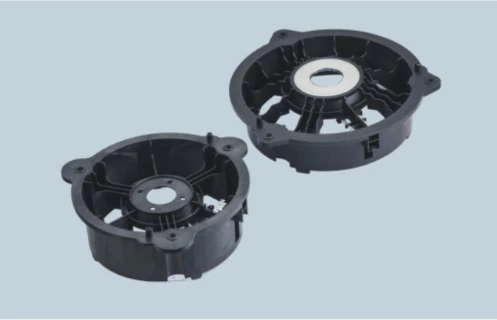
When selecting plastic injection molding manufacturers, exploring alternative manufacturing methods is crucial to finding the most cost-effective solution for your project. By considering different techniques, such as 3D printing or rotational molding, you can reduce production costs without compromising quality or performance.
Not Exploring Alternative Manufacturing Methods
Many companies overlook the benefits of alternative manufacturing methods when searching for plastic injection molders, often sticking to traditional injection molding processes. However, exploring options like 3D printing or rotational molding can uncover more affordable and efficient ways to bring your product to life.
Overlooking the Benefits of Automation
Automation is a powerful tool for reducing costs in plastic injection molding. Incorporating automation into your production process can significantly streamline operations and lower expenses.
Consider the following benefits of automation:
- Increased efficiency: Automate repetitive tasks like material handling and quality control to boost productivity.
- Reduced labor costs: Rely on machines to handle time-consuming processes, freeing up your workforce for higher-value activities.
- Improved product quality: Automation ensures consistent results and minimizes human error.
Partnering with a manufacturer specializing in automation can help you unlock these advantages and achieve substantial cost savings.
Failing to Negotiate Pricing Effectively
Negotiating pricing with plastic injection molders is a critical aspect of cost reduction that is often overlooked. You can secure favorable pricing that aligns with your financial goals by effectively communicating your budget constraints and seeking competitive quotes from multiple manufacturers.
Underestimating the Importance of Prototyping
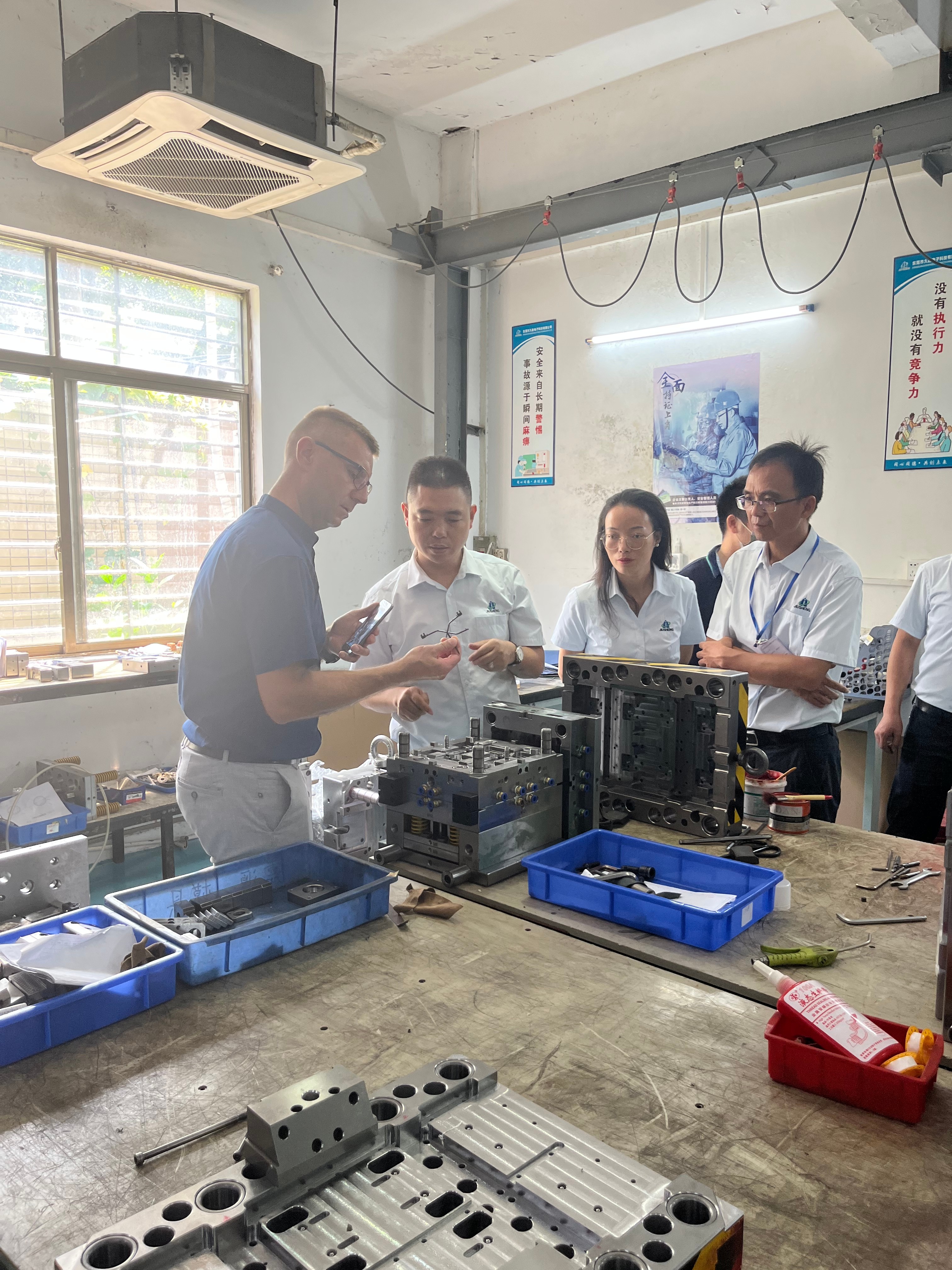
Prototyping is a crucial step in plastic injection molding that should never be overlooked. Not testing designs before production can lead to costly errors and setbacks. Thoroughly testing prototypes ensures that the final product meets all requirements and specifications.
Not Testing Designs Before Production
Many companies skip the prototyping phase in an attempt to save time and money. However, not testing designs before production can result in defective parts, wasted resources, and delayed timelines. Thoroughly testing prototypes can identify potential issues and address them early on, saving both time and money in the long run.
Neglecting the Feedback Loop
Another common mistake is neglecting the feedback loop during prototyping. It's important to gather feedback from all stakeholders involved in the project, including designers, engineers, and end-users. This feedback provides valuable insights that can help improve the design and functionality of the final product.
Ignoring the Value of Iterative Development
Iterative development is a key component of successful prototyping in plastic injection molding. Companies can ensure that their final product meets all quality standards and requirements by continuously refining and improving designs based on feedback and testing results.
Remember that taking shortcuts during prototyping can lead to costly mistakes later. Thorough testing and iterative development are essential to ensuring a successful plastic injection molding project!
Neglecting Post-Processing Considerations
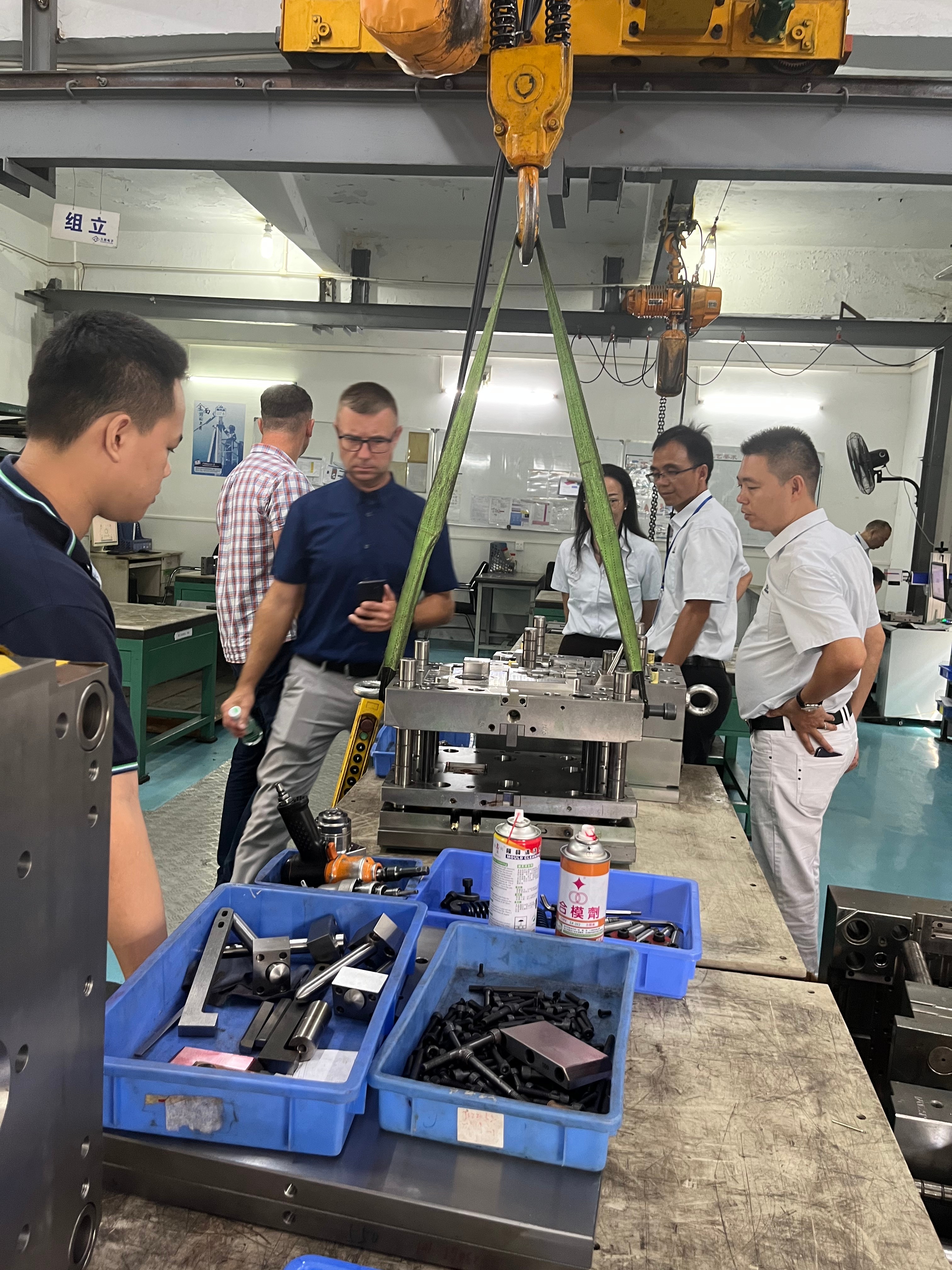
In plastic injection molding, overlooking post-processing considerations can lead to subpar results. One common mistake is overlooking finishing options, which can greatly impact the final appearance and functionality of the product. Ignoring surface treatment requirements can also result in parts that do not meet the necessary specifications for use. Failing to plan for assembly and packaging can lead to delays and added costs in the production process.
Overlooking Finishing Options
Many plastic injection molders neglect finishing options when it comes to their products. Whether it's painting, plating, or polishing, the right finishing touch can greatly enhance a part's appearance and performance. By considering various finishing options early in the design process, manufacturers can ensure that their products meet aesthetic and functional requirements.
Ignoring Surface Treatment Requirements
Plastic injection molding manufacturers often overlook surface treatment requirements, leading to parts that do not meet the necessary specifications for use. Whether it's corrosion resistance or improved adhesion properties, surface treatments ensure that parts perform as intended. By ignoring these requirements, manufacturers risk producing unfit parts for their intended application.
Failing to Plan for Assembly and Packaging
Failing to plan for assembly and packaging is another common oversight in plastic injection molding production. Proper planning is essential to ensure efficient assembly processes and secure packaging solutions for transportation and storage. Neglecting these considerations can result in costly delays and logistical issues.
Remember: Neglecting post-processing considerations can produce subpar results in plastic injection molding!
Disregarding Environmental Impact
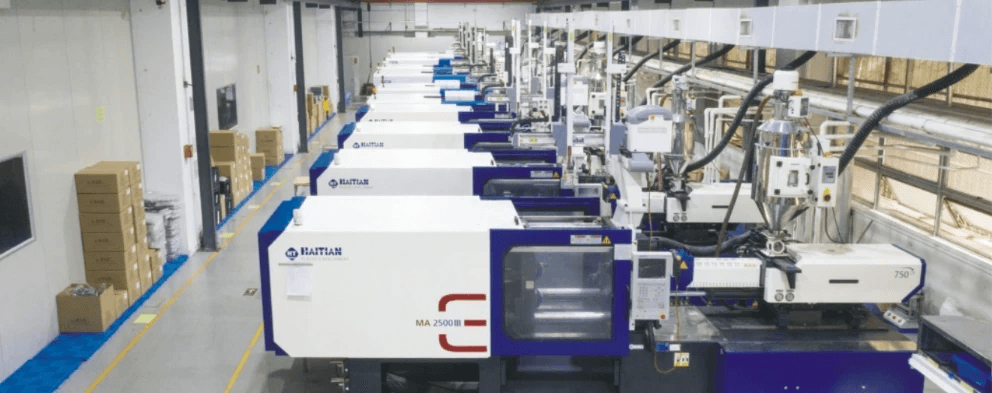
Plastic injection molders must prioritize sustainability by using recycled materials and ensuring their manufacturing processes are environmentally friendly. By utilizing plastic pellets made from recycled materials for injection molding, companies can reduce their carbon footprint and contribute to a more sustainable future.
Not Considering Recycling and Sustainability
Plastic injection molding manufacturers should explore the use of recycled plastic pellets for injection molding to minimize environmental impact. By incorporating sustainable practices into their production processes, such as using biodegradable or recyclable materials, companies can demonstrate their commitment to environmental responsibility while reducing costs.
Ignoring Energy Efficiency
Cheap injection molding may seem cost-effective in the short term, but it often comes at the expense of energy efficiency. Plastic injection molders must invest in energy-efficient equipment and optimize their manufacturing processes to minimize energy consumption. This not only benefits the environment but also leads to long-term cost savings.
Failing to Minimize Waste
Injection molding instant quote may be appealing, but companies should not overlook the importance of waste reduction in their production processes. Implementing lean manufacturing principles and efficient material usage can significantly reduce waste generation and contribute to a more sustainable operation. Plastic injection molders can enhance their environmental performance while improving overall efficiency by minimizing waste.
Overlooking Long-Term Partnerships
When choosing plastic injection molding manufacturers, evaluating the manufacturer's reputation is crucial. Look for companies with a proven track record of delivering high-quality products and exceptional customer service. By partnering with reputable plastic injection molders, you can ensure that your projects are in good hands and avoid costly production delays or quality issues.
Not Evaluating Manufacturer's Reputation
Many businesses make the mistake of prioritizing cheap injection molding over the manufacturer's reputation. This can lead to subpar results and ultimately cost more in the long run. Before making a decision, take the time to research and evaluate plastic injection molders' reputations. Look for reviews, testimonials, and case studies to understand their capabilities and reliability.
Ignoring Baoyuan's Expertise and Experience
Baoyuan is a leading provider of plastic injection molding services with extensive expertise and experience in delivering superior-quality products. With state-of-the-art facilities and a team of skilled professionals, Baoyuan offers innovative solutions for all your plastic injection molding needs. By partnering with Baoyuan, you can benefit from their industry knowledge and commitment to excellence.
Failing to Establish a Long-Term Relationship for Future Projects
Building a long-term relationship with your chosen plastic injection molder is essential for future projects. Establishing trust and open communication can streamline the production process, reduce lead times, and achieve cost savings on future orders. Don't overlook the value of forging a strong partnership with your manufacturer for ongoing success.
Remember that choosing the right plastic injection molder is crucial for the success of your projects. Don't underestimate the importance of evaluating their reputation, recognizing Baoyuan's expertise, and establishing long-term partnerships for future endeavors.
Avoid Costly Mistakes in Injection Molding Production
When it comes to successful plastic injection molding, factors like material quality, production volume, and environmental impact must be considered. Partnering with Baoyuan, a leading plastic injection molding manufacturer, ensures superior results and cost-effective solutions. You can achieve high-quality parts at competitive prices by avoiding costly mistakes in injection molding production.
Key Considerations for Successful Plastic Injection Molding
Selecting the optimal plastic pellets for injection molding is crucial in achieving high-quality product outcomes. To ensure success, consider the following key factors:
- Design for Manufacturability: Optimize the part design for efficient injection molding.
- Production Efficiency: Streamline processes to maximize output and minimize waste.
- Quality Control: Implement robust testing and inspection procedures.
- Regulatory Compliance: Adhere to industry standards and safety regulations.
By carefully addressing these elements, you can enhance overall production performance and deliver exceptional products.
Partnering with Baoyuan for Superior Results
Baoyuan offers top-notch injection molding services with an instant quote option for your convenience. With their expertise and experience, you can trust that your project will be in good hands from start to finish. Don't settle for cheap injection molding when you can have superior results with Baoyuan.
By partnering with Baoyuan, you can avoid common mistakes that lead to subpar results and increased costs. Their attention to detail and commitment to excellence sets them apart from other plastic injection molders. With their instant quote feature, you can start your project without delays.
Remember, when it comes to plastic injection mold production, choosing the right manufacturer is crucial for the success of your project. Don't settle for anything less than superior results - partner with Baoyuan today!